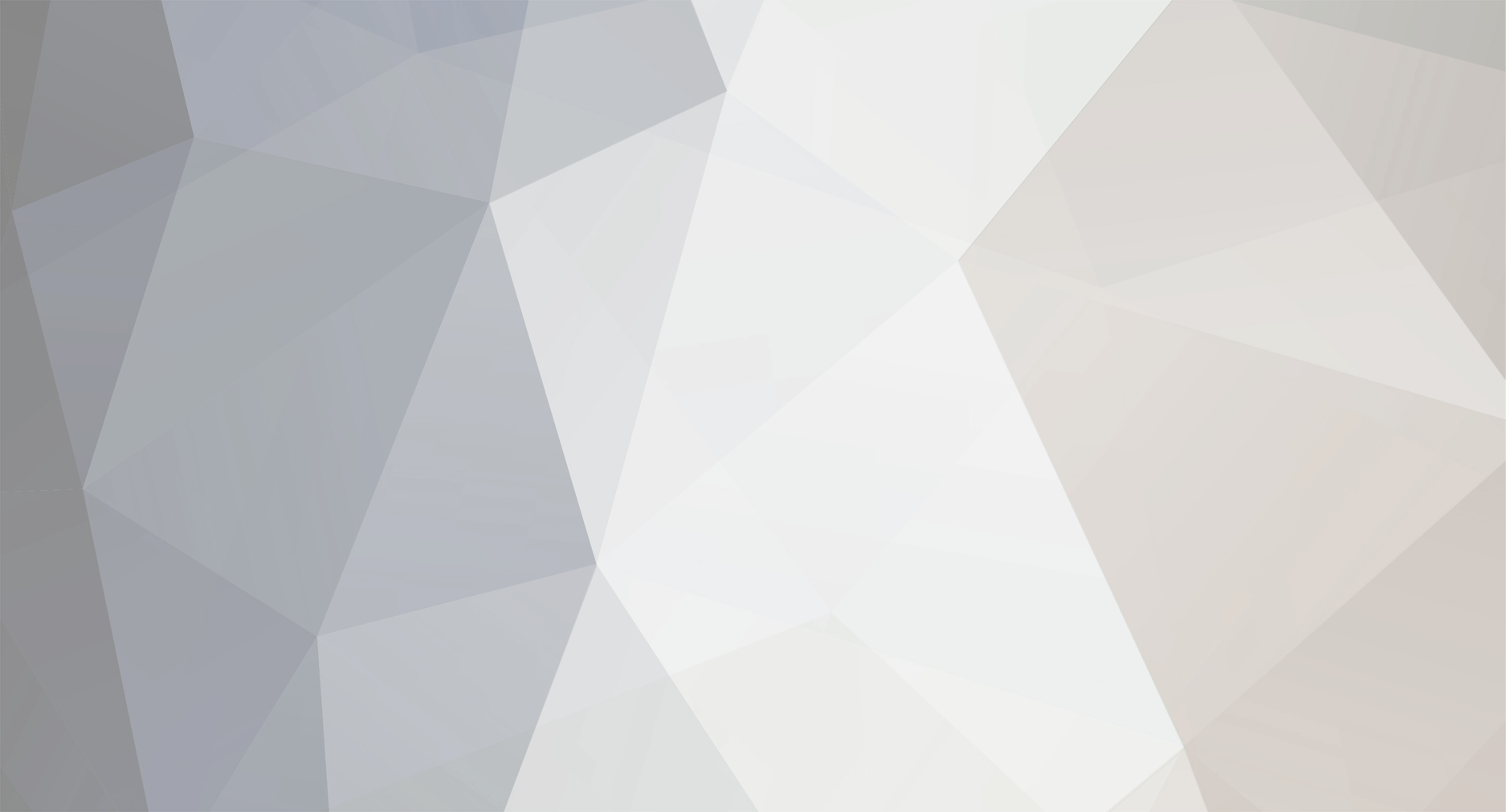
nilebodgers
⭐Supporting Member⭐-
Posts
707 -
Joined
-
Last visited
Content Type
Profiles
Forums
Events
Shop
Articles
Everything posted by nilebodgers
-
After Eighty - Small Ashdown Combo On Steroids
nilebodgers replied to Chienmortbb's topic in Build Diaries
The NC500MP OEM and NC502 MP OEM look interesting as integrated modules (having a separate psu like the others is a step backward IMO). A quick google didn't reveal any street prices though. -
After Eighty - Small Ashdown Combo On Steroids
nilebodgers replied to Chienmortbb's topic in Build Diaries
That's an unmissable warning! The Icepower modules are a fantastic thing that solve all the issues with SMPS and Class D in one hit for an amateur designer. The only snag is the difficulty of getting ones with known provenance at a sensible price given how much fakery goes on. -
After Eighty - Small Ashdown Combo On Steroids
nilebodgers replied to Chienmortbb's topic in Build Diaries
Yes, I was.a pro elec engineer and there is no way I’d go anywhere near an amateur designed SMPS, there are an large number of failure modes and non-obvious design considerations that can be traps for the unwary. Ditto with amateur class-d power amps. -
Attached pic is a simulation of the freq curves for the high mid control of a Little Mark II. Total range is +/-15dB at approx 800Hz and the different colours correspond to control rotation in 11 equal steps (flat centre is 12 o'clock). You can see the effect at other frequencies either side of the centre freq. Q is about 1.2 for the 2 mid controls.
-
I have seen marks like that on the steel pole pieces from a ceramic magnet pickup. I have a pair of Mim jazz ceramic pickups circa 2008 in my shed, I’ll have a look. None of the Alnico pickups I have seen look like that.
-
Little b*tch by the specials is hard right??
nilebodgers replied to alexa3020's topic in Theory and Technique
LOL - I've never tried to play that and I thought it didn't sound hard so had a go.....then my picking hand exploded. That will take some practice to get up to 161bpm without strain for a whole song. -
I'd 2nd getting a headphone amp - if you are a beginner you are unlikely to develop good muting technique unless you are amplified.
-
Taking a PayPal payment for an item to be collected...
nilebodgers replied to binky_bass's topic in General Discussion
Isn't there a loophole if the buyer has funded paypal via a credit card and then claims that the credit card was stolen/compromised? I thought the transaction could be reversed in that case. -
Interesting. I have a Taiwan one just like that. I read up on the history via the Facebook Yam BB group and as far as anyone knows the Japan and Taiwan models are identical in every respect apart from the pickup covers/surrounds.
-
I use AKG K92s with my B1-4. I bought them for the light weight and wearing comfort while still sounding good and not being expensive. I also have Beyer DT150s which are great headphones, but they are also heavy and very close fitting. They have great isolation if you are working in a loud environment, but not so comfortable for home use.
-
Nice bass playing, but the overall vibe is so hipster that it is a bit of a send-up.
-
Isn't she just. There's some killer little fills in her line too.
-
There is no bottom end on anything I can hear and the cymbals have that low bit-rate phasey thing going on, sounds like a poor encoding that has been high-passed for playing on mobile phones...
-
That's crazy, never seen anything like that before. I wonder how quickly it clogs up and if it can it be cleared while hot? I usually have to clean a manual sucker every few goes, when I used to to do electronics professionally I used the braid mostly as it was cleaner and more precise and didn't suffer from jamming (and the mechanical twang making everything jump around).
-
Funny - I always fancied a Stingray, but they have always been a bit more money than I can justify. I have been looking since the mid 80s 🙄
-
Rebecca Johnson band - bass-led Aussie covers trio
nilebodgers replied to bornagainbass65's topic in General Discussion
I know what you mean about BVs. Someone posted a video on here of their own band doing an original song a while back and it was pretty good, but the simple absence of BVs made it sound a bit lacking. -
After Eighty - Small Ashdown Combo On Steroids
nilebodgers replied to Chienmortbb's topic in Build Diaries
You could pinch the thermostatic fan control circuit from something like the GK MB200 that uses the same ICE module. See: U1 is a LM35 attached to the main heatsink on the ice module (at least on the MB500 - I haven't seen where it is attached on a MB200) and the fan is one of the tiny 25mm x 25mm 12V ones that run at 60mA-ish. -
After Eighty - Small Ashdown Combo On Steroids
nilebodgers replied to Chienmortbb's topic in Build Diaries
A common technique is to use back-to-back 12V zeners with a resistor in the 1k - 3k3 range (plus a 50V min blocking capacitor). GK do that on a lot of their later models. -
After slapping what about tapping?
nilebodgers replied to Barking Spiders's topic in General Discussion
It's all very clever and that, but I can't imagine ever being in a situation where I could use it (and be welcome 😉) so I haven't bothered even experimenting with it. -
Fun. I recognised 9/10 even if I couldn’t name the artist on a couple without prompting. On ‘89 I’m pretty sure I’ve never heard that pixies track and the bass line is so generic it wouldn’t have caught my ear anyway.
-
It sounds great and is easy to use for someone that doesn't really know what they are doing (i.e. me). The only minor downside is that if you don't donate you have to open the plugin and dismiss the splash screen every time you load a project using it otherwise no sound comes out.
-
Well, the D.C. resistance of a typical nominal 8 ohm driver is somewhere around 5.5 ohms so 2 in series and a bit of a handwave for cable resistance would be 12 ohms? (although that would normally be called 16 ohms)
-
I was thinking "I'll never be able to read that well" ... but then I remembered how the intro goes - hardeharhar
-
The tweeter is/was the weak point on these cabs. I bought a 210 and the tweeter was dead on arrival. The shop ended up sending the cab back to Ashdown and rather than replace the stock part Ashdown fitted an Eminence APT instead.