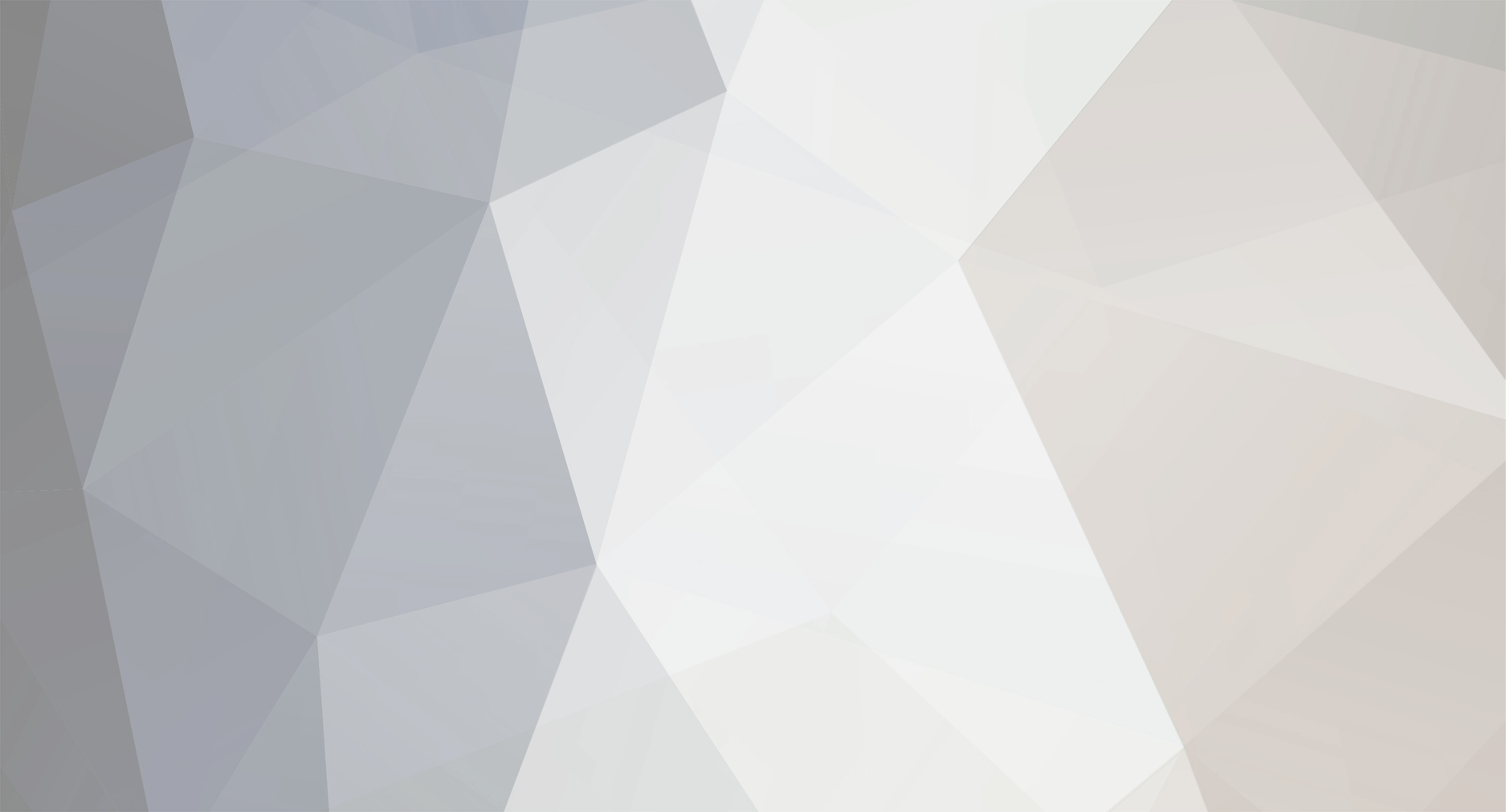
PlungerModerno
Member-
Posts
1,449 -
Joined
-
Last visited
Content Type
Profiles
Forums
Events
Shop
Articles
Everything posted by PlungerModerno
-
I guess a lot of luthiers could adapt an A4 into smaller A4 style bass, but I think you might be better off going fully custom if you're going to do major neck & body work / have a big body shave and a new neck made. I think the key is the body, since it's a pretty typical fender style neck, I can't think of a maker that does a mini A4 style or similar body.
-
would a shorter neck, custom or converted if you could find something suitable, be out of the question, if you really like the A4 as a long scale?
-
Now that is a suggestion I like the sound of... It's usually a butterscotch '57 style P, but it definately can work with a natural wood finish...
-
Did somebody say tort? I think a yellower tort might look nice.
-
Aren't the Status basses carbon fibre too? http://www.status-graphite.com/status/frames/index_home.html Looks like they use Machined brass... with the zero fret on a lot of their basses I think they have very little to gain by offering different nut materials to be fair.
-
I think, like everything on the neck, it can help or worsen dead spots, but since the nut is generally fairly light, even if brass, it will be a very subtle effect. I think the cut of the nut matters a lot more than material.
-
I think the handy solution if you intend on smoothly clear-coating the pickguard and polishing it to a mirror shine is to sandwidch a wood veneer of your choice beneath a clear plastic pickguard. It won't look exactly the same as a fully wooden guard but will look fairly close, and won't have the issues of screws splitting thinner wood if it gets tightened a little over enthusiastically. If you want a textured grain effect it will mean using wood just under a light finish, so it will probably wear fairly quickly if it's hit with a pick or fingernails or most things that would leave marks on that kind of finish on a body or neck. You might also want to look at using double sided tape or maybe a light adhesive to attach the pickguard as an alternative to screws, especially if you want it to be a very thin guard. Look at how the acoustics are generally held in place. If you go with a thicker wood (3mm or more I'd guess) you could go with mini-magnets in the top but they'd mean drilling larger than normal pilot holes. Look at those nifty screwless control cavity covers I'd suggest. https://www.talkbass.com/threads/screwless-removable-pickguard-solution.1184607/ a user a few years back on this thread suggested silicone as a finish safe adhesive. I've heard bad things about silicone and nitro, so please proceed with caution if you use an adhesive on finish!
-
A Lovely S1 Hamer Cruisebass.
PlungerModerno replied to NancyJohnson's topic in eBay - Weird and Wonderful
At current prices I'd say it's worth about 2 and a half packets, and a nearly empty lighter. -
Unusual Acoustic Bass from Italy
PlungerModerno replied to TheGreek's topic in eBay - Weird and Wonderful
I like it. Cool sound hole, not convinced by the chamfer/roundover on the lower bout, seems like it might be more welcome on the upper bought the way it's strung... -
A Squier, for £1,800 ????
PlungerModerno replied to WHUFC BASS's topic in eBay - Weird and Wonderful
My thought at first was it was just an extra 0 by mistake, he wanted £180. Then I took a look at the description... Clearly in no rush to sell it. Might be to get a person off their back, put it up for sale for x10 times the cost, either you make bank or get to keep what you like. -
Minimum width for 34 Inch neck?
PlungerModerno replied to SgtPepper02's topic in Repairs and Technical
Is the neck truly a write off? Is it breaking apart to fragile chunks or could it be glued back together, i.e. would it work again if the truss rod worked? I'm asking because if it held tune once, it may again. If you liked the way it was it may before it may be easier to repair this neck, than to modify another neck to feel like this one. I'm just wondering on the construction - would it need a new sunk stripe, would routing it out be an option, or would it be an opportunity to replace the fretboard if that's a concern? (if it's soft wood or badly damaged). Replacing it with a quality used or new neck will probably be the better option, as long as the neck pocket is stable and the neck is fitted well. -
Learn some Duck Dunn techniques from ‘Sweet Home Chicago’
PlungerModerno replied to greghagger's topic in Blues
Duck was the man. Fun stuff.- 16 replies
-
- 1
-
-
- duck dunn
- sweet home chicago
- (and 7 more)
-
stop oiling your fretboards
PlungerModerno replied to Killed_by_Death's topic in Repairs and Technical
That's a good point, I think most people believe it helps slow down the woods changing with the seasons, rather than stopping it. I could be wrong about that of course. I think the reality is the finish, unless it's some sort of metalized finish (kinda like the inside of a packet of crisps?) or made of glass it will tend to allow water vapour in and out very gradually even if the entire instrument is sealed. Given most basses have raw wood in the neck pocket, pickup routes, and elsewhere like the machine head holes which mean water can slowly get in and out, even if you have a ""sealed" fretboard under a hard finish. -
The fingerboard oil survey
PlungerModerno replied to Jean-Luc Pickguard's topic in Repairs and Technical
Do you believe in the "Big fingerboard oil" conspiracy theory where guitar manufacturers spread fake news to convince people to ruin their instruments by oiling their fingerboards? Yes, but more that a tiny number of people will pickle their unfinished fingerboard and cause issues with binding, finish, and frets, not that the manufacturer is trying to ruin anybodies instrument, just they want to sell more product and emphasize the selling points rather than potential issues. -
stop oiling your fretboards
PlungerModerno replied to Killed_by_Death's topic in Repairs and Technical
I found this: https://images.thomann.de/pics/atg/atgdata/document/specs/189610_safety_data_sheet.pdf Confirming that figure of it being mostly mineral oil. I think if 5 or 10% is not listed I wouldn't want whatever is in it being absorbed by my skin. If they don't list the ingredients they can switch them or alter the concentrations without letting you know, so those who had no reaction to it before may have a reaction to a slightly different blend. It doesn't appear at all dangerous, but I'll stick with known ingredients with their risks - a tiny bit of linseed oil as a cosmetic aid, it's a bit of fire hazard but you can deal with that by laying flat etc. https://www.bartoline.co.uk/wp-content/uploads/2018/11/BARTOLINE-Raw-Linseed-Oil-SDS4843.pdf I think the boiled stuff is a lot handier, but contains far less healthy ingredients, you'd want it to harden fully before touching it with bare skin. https://www.bartoline.co.uk/wp-content/uploads/2018/08/BARTOLINE-Boiled-Linseed-Oil-SDS4832.pdf Mentions the typical catalysts that are added you probably don't want to expose yourself to. Obviously breathing it might be substantially worse, depending on the amount of ventilation. -
Labella B string won't go through bridge hole
PlungerModerno replied to lobematt's topic in Repairs and Technical
If it's only ever so slightly too big, if there's a bulge in the wrap close to the ball end, you may be able to compress it enough to sneak it through. Just try to make sure it can spin freely as you get wraps around the post. -
stop oiling your fretboards
PlungerModerno replied to Killed_by_Death's topic in Repairs and Technical
Go to 1:40: https://www.youtube.com/watch?v=rGDZ_HyEBS4 -
stop oiling your fretboards
PlungerModerno replied to Killed_by_Death's topic in Repairs and Technical
Don't your fingers sweat a mix of oils and waxes? I know keyboards and touchscreens get pretty manky in use unless you clean them. If you haven't cleaned a fingerboard in a while you'll generally have a crop of what some call "mojo" built up. I think oil or wax may help protect a unfinished piece of wood from splitting or warping due to extreme changes in humidity, especially on endgrain, like they do to lumber the world over: I think people should know what's on their instrument, and care for it as they see fit. If it get's hot or will be in sunlight I'd say if it's painted, treat it like car paint, wax and polish it and keep it out of the sun as much as possible. If it's an oil finish I guess follow the directions for that finish. Not all oils get on with each other, or with all waxes is my understanding. -
BEWARE: Geeetar content - Ibanez X-ING midi
PlungerModerno replied to TheGreek's topic in eBay - Weird and Wonderful
Cool geeetar. Could work in a more avant-garde setting. -
Bridge and strings separate for easier transport.
PlungerModerno replied to Happy Jack's topic in eBay - Weird and Wonderful
"Minor seam repair needed at base of neck." It mightn't need to come completely apart but I suspect it'll need a fair bit of work. -
:Looks like it's gonna be a solid joint, all going well. I think 2 screws should be enough, 4 is good, 6 is better, I think Ritter might be overdoing it though:
-
My guesses (make yours before peeking!): Looks like it should be very unique, cool, and practical.
-
Washburn AB20 Acoustic Save (fingers crossed)
PlungerModerno replied to Andyjr1515's topic in Repairs and Technical
I think there maybe some woods out there sold as mahogany that are much much stiffer and tougher than the usual stuff, but I agree there is not enough there to be fully confident in any wood. Even the most consistent wood can hide a void or shake! Luthiers, especially those dealing with tricky and non traditional instruments like acoustic basses, should always err on the side of sturdiness when there is no issue with volume or tone, like the neck. Unless they like warrantee return work lol. -
Monster basses for the money, now the disadvantage of not being able to try them in many stores is suspended for now I'd recommend trying with confidence. Always check the return policy though, you may love it but want a slightly different spec, or maybe won't get on with it. Used they are a steal, if they go for their usual modest prices.