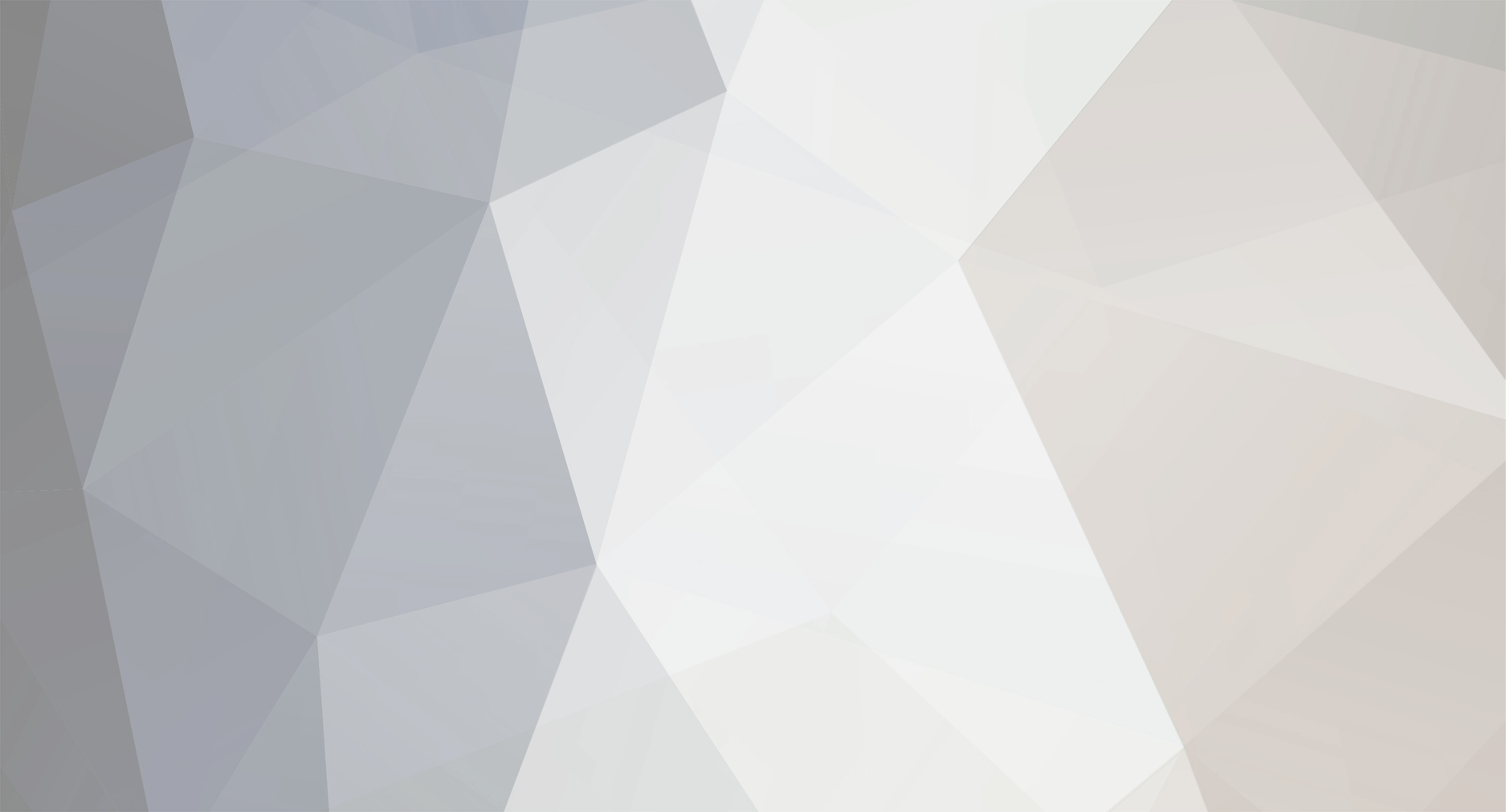
PlungerModerno
Member-
Posts
1,449 -
Joined
-
Last visited
Content Type
Profiles
Forums
Events
Shop
Articles
Everything posted by PlungerModerno
-
The tone of the Reverse P: when is it a Good Thing? when is it not?
PlungerModerno replied to a topic in Bass Guitars
Looks groovy. Tasteful timber. I think the single coil P bass was always about mass production, keeping it simple. The split P was a cheaper way to get a hum-cancelling pickup than two four string sized coils. I suspect the prototypes ('51 and '57 styles) were trying to get a more upright thumb plucked tone, judging by the "tug bar". I can get a decent variety of tone with my hands by plucking at various locations along the string, as mentioned by @Doctor J. Floating thumb technique (or moving anchor) gives you more freedom than any fixed anchored position. Having a bridge pickup opens up the possibilities hugely, no doubt PJ or PM PMM or any dual pickup bass (except a dual neck pickup setup like a 'cavern' Höfner lol) is much easier to get those tones that are mostly or exclusively 'bridge pickup' tones. -
The tone of the Reverse P: when is it a Good Thing? when is it not?
PlungerModerno replied to a topic in Bass Guitars
Life is full of such delights. I think you need near identical pickups, scale length, and strings to do a fair comparison. I can hear (or think I can anyway) the difference between neck position and bridge position on basses even with OD etc. so I guess it should be fairly apparent P vs. reverse P of the same or near identical pickups. I was reminded of this. a fairly subtle move seems to cause a massive shift in tone. -
Maurszczyk Paddock 5a truss rod snapped!
PlungerModerno replied to radcliff43123's topic in Repairs and Technical
Just imagine if it had gone down over a densely populated area. Not to minimize the horrific loss of life (almost half the souls aboard), but a real example of heroic piloting. -
To be fair we don't know what it started out as. With that finish on the back of the neck I suspect it may be a refin, who knows what kind of whittling was done prior to the spraying. I agree it has nothing that indicates it ever was a Warwick, even if it has been renecked or extensively modded. I am no expert though!
-
Maurszczyk Paddock 5a truss rod snapped!
PlungerModerno replied to radcliff43123's topic in Repairs and Technical
I'd forgotten about that one. Tragic but not half as tragic as it might have been. Here's a good article on it: popularmechanics.com the-final-flight-of-united-232 -
Maurszczyk Paddock 5a truss rod snapped!
PlungerModerno replied to radcliff43123's topic in Repairs and Technical
Good to know you should have a smoothly operating truss rod for the foreseeable future. I wonder if you can grease a two way truss rod nut once it's installed? I know the single action ones just come off like any other nut. I'd say you're probably right. I hope your right about Maurszczyk, that they'll make it right. That link does lead to a very damning impression of the work done on that one neck at least. I'm not confident that is representative of their work, given you would expect QC oversights to show up for major repairs much more often than the average example from the manufacturers. If the truss rods are thick enough and made carefully, and installed in a carefully engineered neck, a good steel ought to be more than strong enough. Even titanium alloy or the best steel for the job will occasionally be the victim of a manufacturing error, which will in rare occasions be missed by even the best QC. I think the brutal stress tests you'd need on each neck to guarantee the neck up to a certain tension would cause more issues than they'd solve. -
Maurszczyk Paddock 5a truss rod snapped!
PlungerModerno replied to radcliff43123's topic in Repairs and Technical
While I don't think the maker can predict the outcome of every neck perfectly, they can stack the deck heavily in favour of strength. I think Ibanez making reinforcement universal on the higher end models is a smart move, having it as an option may be more profitable, but I can see it creating issues, especially if you don't go for the removable style of truss rod (like Warwick used to use). -
Maurszczyk Paddock 5a truss rod snapped!
PlungerModerno replied to radcliff43123's topic in Repairs and Technical
That's an interesting question... I may be wrong but I always understood it that a stiffer neck would reduce the amount of turns and hence the pressure on the steel of the truss rod. It would reduce the amount of deflection due to the strings and thus mean less work for the truss rod. But if that work is straightening a much stiffer neck is it the same or perhaps more work in a smaller range of motion i.e. fewer turns with more force needed in each turn? What about dual action truss rods? It's an interesting question. Maybe my theory about always adding stiffening rods to thin necks might create additional problems. Ibanez have been mentioned by @Woodinblack and I would take their descisions seriously given their vast experience with thinner necks and their reputation, especially the higher end stuff. -
Maurszczyk Paddock 5a truss rod snapped!
PlungerModerno replied to radcliff43123's topic in Repairs and Technical
I think the cheaper end of the market where margins are super tight it's probably cheaper to just give a free replacement instrument or neck for the one in a few thousand that fails than to spend extra in making them reinforced. I would say it's building to a price rather than an oversight. For custom instruments I can't see the logic in not adding the re-enforcement. Even if the customer explicitly asks for it to be left out... will they X-ray the neck? Saw it up during the warrentee period? I can see why an individual luthier or company builder might be tempted to lie and just put them in anyway to build a stiffer neck they'll hopefully never have to work on again. -
Maurszczyk Paddock 5a truss rod snapped!
PlungerModerno replied to radcliff43123's topic in Repairs and Technical
Do we know for certain that the truss rod would still be intact if you had got the stiffening rods? I think any manufacturer, no matter how good the QC will produce lemons or defective parts or goods/services. Even the best truss rods have a failure rate in normal usage, wood being wood it's not possible to achieve perfect consistency. I can see the difficulty a maker faces, since there's no way a manufacturer can prevent a person from tightening a truss rod to breaking point (not saying that's what happened in this case), they can just use very tough truss rods and make very stiff necks that need minimal interaction with the truss rod within the warrantee period to keep the failure rate as low as possible. I hope they will support and stand behind their work. I doubt they need to offer a free replacement neck or repair, in UK or EU consumer law, but should consider this opportunity to offer a reduced cost repair or better yet, only have the owner pay shipping! I would like to see every manufacturer go down the road of insisting on overbuilding necks for stiffness and strength, only allowing normal/thin necks without reinforcement as aftermarket sales (bolt on only) or as second necks in addition to a super stiff stock neck. Those necks should be sold as decorations and explicitly excluded from any warrantee to free the maker from the consequences. EDIT: Obviously a manufacturer can just decide to keep making necks traditionally, and just hope for the best, replacing more of them for free than if they had gone with a stiffer design, or charge the customer at the cost of reputation and reduced sales. -
Maurszczyk Paddock 5a truss rod snapped!
PlungerModerno replied to radcliff43123's topic in Repairs and Technical
I think if the neck profile is very thick (front to back) and made with a suitable wood, or it's made with tough enough wood multi-laminate left thick It should be extremely stiff, even with 6 very high tension strings. The problem is those necks will only suit a minority of players, who feel those beefy necks are way too much. Many of the modern slim neck profiles make steel or carbon fibre re-enforcement rods required if you want a stable neck IMHO. Even if you have a multi-laminate neck made from the stiffest woods (ebony, wenge, paduk, purpleheart etc.) A super thin neck front to back is just too close to a veneer to be acceptably stable at bass scale lengths, at least with natural woods alone. To be fair maybe not in a conventional tuning, but shouldn't you want your 4 string neck to be so strong it can be converted to an 8, even if it's headless or fretless where that's very unlikely? I think skinny necks need to be overbuilt for stiffness if they want to avoid issues. It's more for the manufacturer than the player IMO, where a pattern of returns and repairs will damage the companies reputation. I think every maker ought to do some R&D and come up with a minimum neck thickness they'll make without reinforcement for each neck construction, or install them in everything, or just go full on composite lol. I don't think any manufacturer will be viable making only very thick profile necks, the market probably won't support that. EDIT: How Warmoth do re-enforcement makes sense to me. -
Sorry to hear you got kicked out of the band, 27" is gonna probably suit a baritone better than a bass, even a bass VI, unless you want the super-short kinda sound & feel. Why are you turning from the elegance of the 10 string to the awkward and messy 6 string arrangement? I think you should reconsider the understated simplicity of the BC Rich original: EDIT: I must add, there is no easier restringing than this, except possibly the patented "easy access" 12 string guitar headstocks from our dear friends at Rickenbacker.
-
If you aren't re-using the neck and body, is it truly a conversion? I would say it can be, especially if you're reusing a bunch of the electronics, hardware etc. If the only original thing is the body and the output jack, and maybe the neck screw plate and a few pickguard screws, then I'm not so sure at all. I'd say you should use the original scale length to keep the bridge and fret locations where they are, unless you find when testing bass strings at that scale length (presumably around 25") it's just useless in bass tunings, even with adequately chunky strings.
-
Which drummer you would like to have played with?
PlungerModerno replied to Bassman Sam's topic in General Discussion
I think Brian Downey could be a lot of fun to share a share a stage with. -
If there's no flex between those sections of of the body, it'll probably be perfectly fine, especially since the neck and the bridge are anchored to the same section of wood. I'd get some slightly diluted wood glue and some veneer and fill 'em up. If you don't have veneer handy you can use stout plane shavings or just use sawdust for convenience. Filler will work too but like sawdust it won't be the same long grain glued to long grain strength. If there is flex I'd open it up till you can thoroughly clean it, breaking it off if necessary, then glue it like you mean it!
-
Cool bass. The red position markers are a nice touch matching the logo. Definitely a more interesting alternative to the typical paddle bass!
-
Fitting a right hand ledge or holder to a pickguard?
PlungerModerno replied to TJ1's topic in General Discussion
Floating thumb is definitely worth trying if you have muting issues or pains in your plucking hand/wrist (or want to prevent them!). Or you just want another fun technique as a feather in your cap! check out: from about the 8 minute to 9 minute marks - he shows three complementary plucking hand muting options including floating thumb, all seem more ergonomic than a fixed anchor point. -
I thought this looked very nice: From the The Official MARUSZCZYK CLUB!
-
If you could choose only one bass guitar ...
PlungerModerno replied to Happy Jack's topic in Bass Guitars
I'd say the North Korean bass tends to be on the extreme left, but when you're that far out there it may as well be extreme right, it's meaningless after a certain point! -
Sweet! I think the smaller headstock looks very neat, a nice piece of maple too. Those bridges are pretty comfy too, kinda like the auld Ibanez bridges.
-
Sounds great. Yeah it's heartening to see a band giving it socks, in person and sharing a stage. Rock (& funk) on!
-
They all sound great, clearly lend themselves to a killer slap tone. My fav is the Kingbass Parametrix. Sweet as a nut!
-
http://www.acguitars.co.uk/project/0278krelletype5/ It's already been done, and done with style and taste. The subtle grain of the maple board... the carefully stained grain of the body & ramp/pup cover... the racy stripes in the headstock... Don't go to the "Finished Basses" section unless you want to drool...
-
Should be lovely. I think it's a nice fretboard, should come up lovely with a dash of oil or other finish/protectant. Recessed knobs? Nice. Just don't make the wood too thin or you'll risk a cracking outcome!