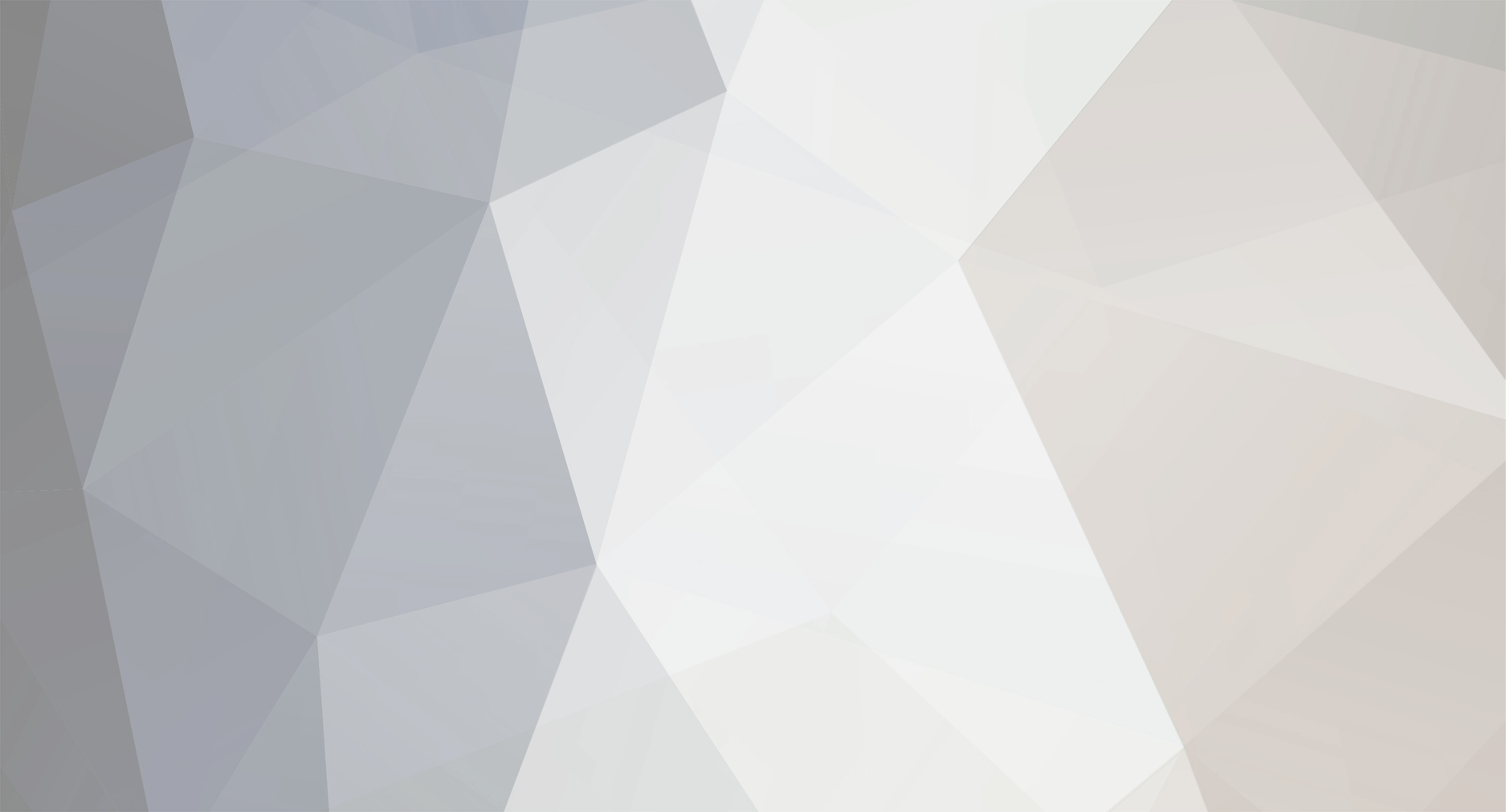
rmorris
Member-
Posts
1,302 -
Joined
-
Last visited
Content Type
Profiles
Forums
Events
Shop
Articles
Everything posted by rmorris
-
[quote name='garry warrington' timestamp='1501002755' post='3341723'] The Tropical fish cap was meant to be 0.047 ,(perhaps it didnt get on with the SX pots. The tone sounded harsher and less defined, Sx basses are half decent for the money, and usually give a passable p bass tone. Would it be worth my while getting some CTS pots with a orange drop cap. [/quote] 0.047 ie 47nF or 0.47 ie 470nF. 0.047 as stated seems rather tiny for a passive bass tone circuit ?
-
[attachment=249903:41RCoJ-uLnL._SX258_BO1,204,203,200_.jpg]For Sale: My copy of Small Signal Audio Design by Douglas Self. Published by Focal Press ISBN 978-0-240-52177-0 Note: This is the first edition (2010). There is now a second edition - I've bought it hence my first edition is now for sale. Very Good Condition - It's been read but not bashed about Superb text from Douglas Self (ex Soundcraft etc and significant audio bod) for anyone even semi interested in designing / understanding pro level audio circuitry. No need to get too 'maths' if you don't want to. Brings a lot of sense and experience to small signal audio design which can seem a bit of a mysterious art sometimes :-) If in douby give it a Google. £28 posted UK mainland or £24 face to face Brighton / Crawley / A23 corridor between Photo is not the actual copy - just a web picture to identify. [attachment=249903:41RCoJ-uLnL._SX258_BO1,204,203,200_.jpg] Thanks for reading
-
[quote name='Rubbersoul' timestamp='1501001743' post='3341708'] Update: The ferrite clip made zero difference. [/quote] Yeah - Ferrites work up in the rf range - tens to hundreds of Megahertz - and won't really effect hum.
-
Paul Stevens Guitars - Lutherie/repairs/setups in East Sussex
rmorris replied to philw's topic in Repairs and Technical
[quote name='TheGreek' timestamp='1500841847' post='3340575'] Hey Phil I know it's the not the most unusual name in the world but is this the Paul Stevens who was CEO at Trace Elliot and now Blackstar? [/quote] Seems not: [color=#605E5E][font=din-next-w01-light, din-next-w02-light, din-next-w10-light, sans-serif][size=4]Paul learned guitar-making at Guildhall University, London back in the 90's. He now has his own workshop on Pevensey Rd, Eastbourne where he spends most of his time making bespoke electric and acoustic guitars. Pauls custom guitars are made from top quality materials, premium hardware and the best electronic components. Most are based on classic designs but he does have plans for some more original rock machines.[/size][/font][/color] [color=#605E5E][font=din-next-w01-light, din-next-w02-light, din-next-w10-light, sans-serif][size=4]For the last 15 years He has worked as a guitar repairer, in the Gibson Artist Relations Office London, Hanks Denmark Street, Wembley Guitar Centre, Bonners Music Shop and his own clients include Stereophonics, Idlewild and Tokyo Dragons. He has also worked as a guitar tech for the likes of Daniel Bedingfield, One Hundred Hours, and the West End show We Will Rock You. He now does repairs from his workshop in Eastbourne.[/size][/font][/color] -
Check ground connections to any meta pickup cover / body of pots etc. Is the pickup cavity / control cavity screened - Aluminium or Copper or 'Black' conductive paint ? If so then check continuity from screening to output jack connection ( can be difficult with the paint so check visually too.
-
[quote name='ahpook' timestamp='1500471646' post='3338062'] Cool They're MMBF-J201s [/quote] Okay. Just checking that if there were something wrong they'd be easy enough to replace without having to get another kit of parts. That series of jfet not so common in UK (to avoid shipping charges out of scale with the cost of a few small components) but Farnell have stock atm so should should be okay. And your build is probably okay anyway. Good Luck...
-
[quote name='ahpook' timestamp='1500463880' post='3337958'] OK, after shorting the G-S the voltage drop is still about the same. Right then, I reckon that means things aren't as bad as I first thought. [/quote] Yep - I don't think there's a problem. As Bobbass said failure usually open or short circuit - not intermediate value. What is the jfet model number ?
-
[quote name='bobbass4k' timestamp='1500461154' post='3337920'] How are you measuring the D-S voltage drop? It isn't as simple as it is for the, G-D/S, internal capacitance can skew the readings. Try shorting source and gate and check the reading again, 1.3 sounds about right to me, as long as it's not fully short or open its probably fine. Like static, it's actually pretty hard to kill a part with heat. I'm not sure where this perception of smt parts as delicate faberge eggs comes from, but it's really not true. [/quote] +1 Sounds about right to me too. And semiconductors - SMT or Thru Hole - are fairly robust when it comes to soldering. Of course, it helps if you use a temp controlled iron and nice and hot so that iron only needs a short contact time with the component leg - especially if using Lead Free solder.
-
Method of soldering earths in a bass
rmorris replied to tommorichards's topic in Repairs and Technical
[quote name='Meddle' timestamp='1500413241' post='3337640'] The popping is actually your body being earthed to the bass, rather than the bass itself. As far as I understand it, the human body, being all water and fat, is an effective receiver for AC. The hum when you take your hands off the strings of an unshielded bass is actually the hum of the AC your body is attracting. When you touch the bridge, strings or other grounded part of the bass you're creating an effective pathway for this AC interference. Shielding your Rickenbacker's cavities might be a good start, and if the pop is bad then I would maybe check the electrical sockets you are using as a precaution. [/quote] [quote name='tommorichards' timestamp='1500416708' post='3337675'] @ikay, yeah, thats going straight to the bridge earth. And @meddle, thats also been suggested to me too. But ive had basses without shielding that have been popping free, so this confounds the matter for me. [/quote] Not sure about the water/fat thing (any ElectroAnatomists in the room ?) - but yes the mass of your body acts as an antennae for electrical interference and there's mains frequency 'noise' all around. So grounding yourself via the bass gets rid of this. BUT there can be a transient noise ie a pop when you touch the bridge / strings / whatever where the skin/metal contact isn't 100% as you first make contact. Especially as the interference is generally at maximum when you are near the metalwork but not touching it. If you're already 'grounded'by touching strings or another piece of earthed kit then it shouldn't happpen. It's likely to be different on different basses depending on Pickup sensitivity and the finish / plating on the metalwork etc. -
[quote name='ahpook' timestamp='1500369590' post='3337207'] Need a bit of advice folks ! I've started building the GUMA Vinatge kit ans have, with as much care as my shaky hands and bad eyes will allow, soldered the SMT JFETs in. I've quickly checked the Gate - Source and Gate - Drain resistances and although I was expecting an open circuit, both chips are reading ~250K ohm. Any idea if I've trashed the chips ? [/quote] Are the 250K readings with the JFets in the circuit ?
-
[quote name='tony_m' timestamp='1499964712' post='3334885'] FWIW, I also run a couple of Trace Elliot pedals (SMX Dual Comp and SM7EQ), but as these require an 18v supply (with a 2.5mm connector) I'm using separate wall-warts for each of them. I've been looking at the Fame / Vitoos DC8 type of thing as these have the requisite number of outputs at different voltages required, but then again the current setup seems to work OK so I'll probably stick to what I've got for now. [/quote] fwiw I run a TE SMX Dual Comp from a Thomann (HB) Powerplant Junior. Two outputs wired in series to give the voltage (DIY cable). It uses two of the five outputs but it's' a working solution without going to other supplies.
-
Depending on the tone you need the a BDI21 might be just the thing. But you don't get 'comprehensive' EQ. Are you going just to FOH / Monitors or using an amp setup too ?
-
[quote name='bobbass4k' timestamp='1499769337' post='3333425'] I work with smt pretty much every day, I've never actually seen an smt part (or any part actually) killed by static. ESD precautions are generally overzealous, and with good reason, but handling them with esd tweezers and just not licking them or rubbing them on the dog will usually be more than adequate. [/quote] +1 Same here. Not saying it can't happen - and it may be more likely that an ESD hit could cause damage that causes a failure further down the line - 6 months ? 6 years ? But unless you are experiency static shocks it's pretty safe for a DIY effort. Guess I'll wandr back to the lab area now and Zap! some CMOS logic
-
Can you use Microphone cable as instrument cable?
rmorris replied to Osiris's topic in Repairs and Technical
In short - Yes - you can use Mic cable. Just wire the 'spare' inner conductor to either tip or shield. Either is fine but just make sure to do same at both ends It's quite usual to use two core cable for unbalanced connections just because it's more usual to have mic cable readily available in pro audio. Is there a catch ? Well, yes there can be, Proper 'Instrument' cable isn't simply a shielded single core cable. It should also have a ' semiconducting' carbon based sheath between the insulation of the core and the screen. This is the bit that you are normally advised must be cut back when terminating to a connector so that it doesn't touch the signal. What's it for ? Moving a cable generates a signal due to small changes in the cable geometry / capacitance / static electricity etc (Wikipedia is your friend to read more...) The magnitude of the signal for a given disturbance depends on the electronics at either end of the cable. Basically higher impedance circuits end up with more noise. And, of course, 'standard' Bass/Guitar pickups are pretty High Impedance and so are Amplifier / Pedal inputs. So the signals can be a problem - think 'swishing' and 'crackling' noises. So how much of a problem you get with a given cable depends on your bass/amp setup and how much the cable moves. On a bass it's inevitably going to move. Between fx and Amp etc it'll likely not be moving much. Plus Impedances are lower so probably okay. It doesn't affect mic signals ? The same thing happens but impedances are much lower (typ Mic Z is around 150 Ohm) so less noise. But it's also helped by the typical 'cotton' fillers you see inside a mic cable. These help maintain the relative geometry of the cable to an extent ( as well as affecting the way a cable 'handles') so you do get some help there. As it happens I think I've recently seen some Mic cable available that has a semiconducting screen (don't quote me) but in general they don't. -
[quote name='MGBrown' timestamp='1499171362' post='3329652'] I have a 2u power amp in a 2u flightcase. Do I need to bother with the rear supports? The manufacturer's blurb recommends fitting them but they are pricey. Not likely to be on any tours any time soon - car transportation only. Amp weighs about 9kg and is a QSC PLX 1202. Any experiences would be welcome. Thanks. [/quote] They're a good idea with that size / weight. But, as you say, these sort of accessories tend to carry a large price premium when they are the gear manufacturer's 'official' part. Depending on the mechanical construction of the amplifier and the rack it's worthwhile to see if you can fashion something to do the job from metal brackets / timber etc. Helps if handy with drill / saw etc :-) As it'll be out of site it doesn't need to be particularly elegant.
-
Wouldn't it be easier and more flexible to use EQ to take the edge off the tone. Or is there a particular issue with the speaker ?
-
[quote name='dannybuoy' timestamp='1497708889' post='3320177'] Yup, the only other cables that had the same issue were the Warwick Rockbass clones of the EBS flat ones and a cheap plastic Bespeco one. Planet Waves plastic jacks were fine though, as were anything metal, from cheapos to pancake jacks, to George L's. [/quote] Yes - I haven't cut one open but I assume that the problem cables don't have screening at the plug end whereas if there's effective screening beneath the overmoulded PVC then that's all good.
-
[quote name='Cuzzie' timestamp='1496786717' post='3313901'] Honestly you won't go wrong with a proper isolated power supply. Is your smart phone in your pocket? Active or hot pick ups on your bass, the phone can create some noise. [/quote] +1 esp the mobile phone - easy to overlook. Even a simple quartz watch can be an issue. On a single coil Strat type guitar I had this - a 'tick' coming through at - ooh about once a second. Took me an embarrasingly long time to work out it was synchronised with the second hand on my watch :-)
-
[quote name='dood' timestamp='1497541674' post='3318992'] The guy was 'partly right', but it's knowing where that common ground is. I can understand where he is coming from when looking at a basic schematic diagram. The ones in some of my old books always have a single line at the bottom for 0v and thus it's easy to assume that it is the only and common ground path. For DC, fine. However, it doesn't take in to account the path the AC (audio and noise) signal goes on when using patch cables and other leads. So, you have a 'ground' going down the cables and then, when you start using a daisy chain power supply, well, that's another ground path. Two paths, which is where the problems can appear. I'll quickly insert that some pedals really aren't bothered and you might not ever have any noticeable noise problems from them when daisy chained together, but certainly some, like a pair of mine that both use a fair amount of DSP do seem to dump (AC) noise on to the daisy chained power supply output. This is where isolated power supplies come in. A daisy chain power supply only has one '+' and one '-' for supplying all pedals. The isolated supply 'decouples' so each pedal sees a completely independent power source, breaking the 'common shared' '+' and '-' connections - which would be the equivalent of using multiple adaptors plugged in to a long trailing socket blah blah, nobody likes that. A singe box that can mimic separate power supplies is tidier and far less hassle. After a long day working, I hope this makes sense! [/quote] It makes sense :-) I'd just add in that regarding picking up external interference ( as opposed to noise from digital pedals ) then the pedals themselves make little / no difference. It's the cable layout an the area of the 'ground loop that matters. The external interference induces a voltage into the loop. Minimising the loop area will reduce the effect. As will increasing distance from interference source.
-
[quote name='dannybuoy' timestamp='1497524385' post='3318830'] I ran a daisy chain for years without an issue, apart from introducing chirping and whining noises into the signal with the odd (but not every) digital pedal. I started practicing through a headphone amp where I noticed the noise in my chain a lot more (my cabs don't have tweeters). Since I'd recently added 12V and 18V pedals to the collection, I bought a Cioks DC5 to power and isolate them all. Yet the noise remained. In the end after extensive testing, I found it was the recently added EBS flat patch cables that were adding a ton of noise if I had my dimmer switch on in the room. I now have silence after switching those out! [/quote] Yes - I've had a similar problem with those generic cheap moulded patch cables in the different colours. Noise picked up at the jack ends. Replacing with good metal jack patch cables cured it.
-
[quote name='cheddatom' timestamp='1497524259' post='3318829'] but in general, are there are plus-points to a daisy chain? Would it be possible to reduce noise in a particular chain by switching from isolated/separate supplies to one supply with a daisy chain? Obviously disregarding digital pedals there. Or is it best practise to always have isolated/separate supplies? I suppose the question is: If money were no object, would you want an isolated supply for each pedal? Or would there be occasions where a daisy chain is preferable? [/quote] Technically Isolated supplies are always better. Basically you have a 'Ground' connection via the patch cable screen. Ideally you don't want another common connection path to 'ground'.
-
[quote name='cheddatom' timestamp='1497514943' post='3318724'] Has anyone got a handy link to explain this to me? It's just that someone once told me daisy chaining would be "cleaner" but now everyone's going isolated... I haven't got a clue on the science of it [/quote] Don't have a link but my input: As with most things there's a few things going on at the same time - 'Digital Noise' - as lots of people find - a digital unit may put a lot of noise onto the Ground Power line which is then connected to other fx in the daisy chain - so an isolated psu helps here. Bear in mind that 'Ground' is never the same at any two points carrying a current since cables have resistance and inductance ( unless you had superconductors !) 'Ground Loops' - assuming all inputs / outputs are unbalanced then with any daisy chain you have 'ground loops' which are susceptible to external interference. Susceptibility depends on cable layout etc. It may cause you a problem or it may not but it's always there waiting to !
-
[quote name='paul_5' timestamp='1495810644' post='3306811'] Not really, just knowing that increasing Emitter resistors decreases the gain of the transistor. [/quote] True :-)
-
[quote name='Grangur' timestamp='1495798767' post='3306695'] ... The important thing is to get a quality one so it lasts well. [/quote] +1
-
[quote name='chris_b' timestamp='1495791172' post='3306584'] I doubt Fender are using the best parts they could source on this bass, so you could use this opportunity to replace the electrics with better components; new loom, pots (audio taper) and cap. IME this [i]will[/i] improve the sound of your bass. As far as I read things, changing the caps won't add or subtract bass. The cap is what turns the pot into a tone control, by creating a variable low pass filter that progressively removes the top and mids. Better caps will allow better control of the filtering of the top and mids but it's the quality of the pots that will increase the volume of the whole bass, which will probably unlock bass frequencies your current pots don't let through, but caps they don't add any frequencies. [/quote] It's never a bad idea to fit good quality components (not necessarily the most expensive). Especially with an electromechanical component like a potentiometer. With low quality the taper can be off - making accurate adjustment difficult , the wiper contact can be intermittent - causing crackling / drop out on a volume pot or varying tone on a tone pot, and the thing may eventually just 'fall apart'. But there are no "[i]bass frequencies your current pots don't let through[/i]". Think about it - they work at DC. If anything they can let high frequencies avoid going "through the pot" due to stray capacitance but that's a minor effect in this application. And a pot itself can only attenuate and not increase volume. The response of a passive tone circuit is governed by the complete network in the bass (pickup / vol pot value and setting / Tone pot value and setting ) as well as the cable capacitance and amplifier input impedance. But all else being equal a smaller cap value will shift the filter frequency higher = less loss of lower frequencies. Any reasonable capacitor just "sits there and does its thing". If you want to get 'audiophile' on it use a Polypropylene type.