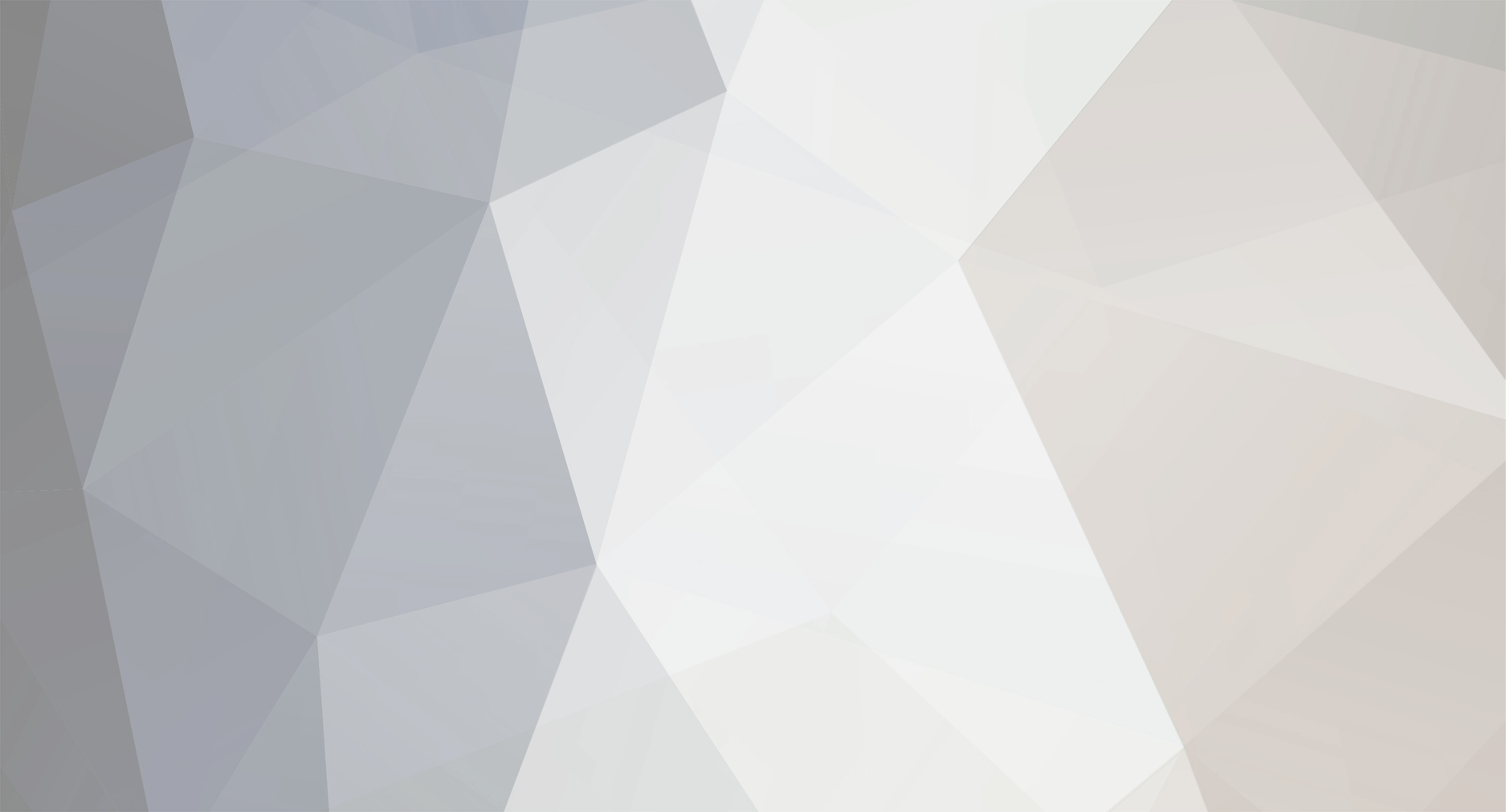
rmorris
Member-
Posts
1,302 -
Joined
-
Last visited
Content Type
Profiles
Forums
Events
Shop
Articles
Everything posted by rmorris
-
I'm looking at this plugin now. tbh it shouldn't be necessary to trawl through all the FAQ to find out something like this.
-
It was going well then. Bin strike not really relevant. fwiw the corner door in view there wasn't used as an entrance. The immediate area is quite lively as it happens. Street bric a brave etc market on the street to the left today with a street band entertaining the customers outside the Dorset bar opposite. And Kensington Gardens predictably busy on a Saturday especially during the festival
-
G4M have bought GAK stock / website / data from the administrators. Not planning to trade under the GAK brand identity.
-
Studiospares went into liquidation. Gear4Music have subsequently picked up the brand, IP , assets etc. Offering a range of products from Studio spares own / proprietary brands. Maybe more to follow. But at present a far cry from the previous 'full range" offering of music / studio kit. Seems they picked it up for around £150k. Nearest outfit to the old Studiospares is Canford Audio. But they operate only on a B2B basis.
-
I see what you did there 🤣 Naughty 😳
-
Yes. But beyond our bass centric world - GAK went beyond the bass / guitar / amp area. More full range with drums / studio / keys etc. Nearest thing now for UK may be Gear4Music. Thomann in Germany obvs. Not a new thing though - on the studio side anyone remember Thatched Cottage Audio ? And more recently the demise of Studiospares?
-
Back to GAK - just been past. Stock shifted and Shop to Let signs up.
-
The context seemed clear to me but since that comment was going against my recognition of the risk aspect then you'd need to ask the poster about what exactly was meant. As for "encompassing all of the factors..." - how would you propose to approach that ? (outside of the tax regime )
-
Very much so. Malfeasance is another level as I see it. What I more often see is a business that is maybe going along okay but not stellar being acquired with the aim of pushing / expanding it hugely. It's risky, it fails. Employees lose their jobs and the future opportunities along with them. The company owners can afford the loss and that loss is minimised by use of company structures and (legal) accounting practices. Yes. Though a not insignificant number of "bad apples' eh "Phoenix companies". Maybe I've spent too long in / around small scale businesses where the "bosses" have been more interested in their next car 🤔 That's interesting. I've also found HMRC okay (fingers crossed as I'm waiting to hear back from them on something atm) But I know someone where it has been awful trying to get something personal resolved. I believe there has been a significant degree of loss of experienced senior staff over time. Pay restraint and high offers from financial businesses drawing them away. Although many then not happy with the pressure piled on them.
-
No. Whilst there may be numerous risks in business, the relevant risk wrt taxation status (which is the area under discussion here wrt difference in tax / NI rates PAYE vs Dividend Income) IS the investment risk and whether it justified being taxed at a different rate. In many cases it's not a problem tbh but it can be subject to abuse.
-
The benefits thing is tired tbh. Of course owners / self employed don't get company paid benefits as they would simply be paying themselves. There is an argument around state paid benefits, esp SSP but it's fairly marginal. Holiday / Sickness Pay considerations etc need to be rolled into renumeration taken. It's why you pay a trade a multiple of the "?wage" itself. Paid Directors are subject to PAYE and any contractual terms between them and the limited company. Of course, depending on the circumstances, this may be a zero sum gain. Where it gets "interesting" is with multiple directors who are also shareholders and where there is disagreement on finance / policy / direction etc. Cause of many a company break up and bad feeling. Like being in a band 🤣 As for GAK specifically - I'd say - picked up by a notorious businessman for a punt. Aim to push further into online. Focus on high margin items judging from emails. When all incomes are under increasing cost pressure. Large physical shop in high retail value area. High staff costs. Accountants inform them it was no longer a viable operation so immediate lock up and nonsensical "Refurbishment" notice slapped on a door ?
-
The risk taking argument really only applies to what in realistic terms can be judged to be real investment risk. Where it is being used as a vehicle to subsidise unrealistically low PAYE income then, yes, it's avoidance ( unless HMRC / Courts find it to be evasion).
-
Depends on the specific circumstances. There is an element of encouraging risk taking. But it can be abused in terms of trading realistic salary income for dividend income to artificially reduce income tax. It can, of course, backfire. Remember the outcry when people who paid themselves largely through dividends were not eligible for furlough support etc during COVID-19 restrictions.
-
There will be creditors. To withdraw assets / reserves from a company in such circumstances would be illegal.
-
In general yes. But there is no statutory requirement for a director to be a shareholder or vice-versa. Although it might be a requirement set by the company itself. I'm very aware that "dodgy accounting" is a thing. But legally dividends must be paid only from available profits which limits scope. OTOH there are Directors Loans as a financial vehicle...
-
Not understanding that remark. Dividends are paid to shareholders in a company. Who may, or may not be, Directors (as in Officers of the Company).
-
Get what you are saying. But that retail model seems to not be working out well atm ? wrt GAK specifically I sensed a significant bias towards pushing the expensive kit. In the current general economic climate and the difficulties of semi/pro musicians earning significant money then I can't say I'm shocked that the shutters have gone up.
-
Interesting shop and some interesting stock. Different game to GAK obvs. Although does carry Revelation on the new side and they are always worth a look. But prices seem on the high side and very much so on some vintage but "cheap" guitars - eg Kay etc. The fun about such guitars is the "funky and cheap" aspect. They aren't good quality physically. Once you start asking £200+ then that fun dissipates. Brighton Guitars around the corner in Sydney Street is also worth a look. Some interesting stick esp on SOR.
-
Yes. But it's not always so straightforward. Where stock has been obtained on credit terms (usual practice) then ownership may contractually remain with the supplier until payment is made. I know there may be examples of stock being shifted out of the jurisdiction to avoid seizure of goods. But this may well put officers of a company in legal peril. The store looks to be full of stock atm - I walked past about an hour ago - so to move that stuff now would be blatant. Of course there is also "warehouse stock" where the situation is less clear. Apart from that it would be usual for suppliers to arrange Credit Insurance before supplying goods. The inability to do so was a major factor in the downfall of eg Woolworths (UK) and IIRC Debenhams. At the end you would go to the store and there would be sparse non-franchise stock.
-
He owns the (remaining) pier in Brighton as well as some other bits (including some now failed businesses) and was complaining around people not visiting due to industrial action by ASLEF on Thameslink trains from London.
-
To round this out in context - I do, of course, have much sympathy with staff who may lose their jobs. Been there. Done that. Particularly for those who qualify for only the legally minimum compensation.
-
Indeed - and IIRC he was the guy calling for the sacking of train drivers during a Thameslink dispute. Also investor in the failed "Dirty Blonde" bar in East Street ? How he ever headed up C4 is a disgrace tbh.
-
fwiw wrt Brighton music shops - I'd recommend giving Badlands Guitars in Preston Road (and Online) a look. Nice stock and Graham and Suzy are very god at looking after their customers. (No personal involvement - just bought the odd small item there but mainly used for guitar fret levels / setups)
-
For clarity on what I mean by looking to the current ownership / investors: not my words but... "There may be other investors, but one appears to be Risk capital partners , aka Luke Johnson. He owns the Pier, invests in Gails and Revolution bars, and previously Laine Pub Co, Small batch coffee, and various others. Bit of a weird guy, extremely right wing and lost a lot of credibility while chair of Patisserie Valerie when it collapsed with a £100m black hole, and a fraud investigation"
-
seems to be the case. Notice on door simply states "Closed for maintenance" or similar and website / online is unavailable. Now if you know the buildings this seems implausible. Large two floor store. Seems unlikely you would need to completely close the premises for maintenace unless it were about to fall down or explode ! The adjacent buildings and businesses seem fine. And the website down so ... Suggest look to the ownership since changing hands a few years back.