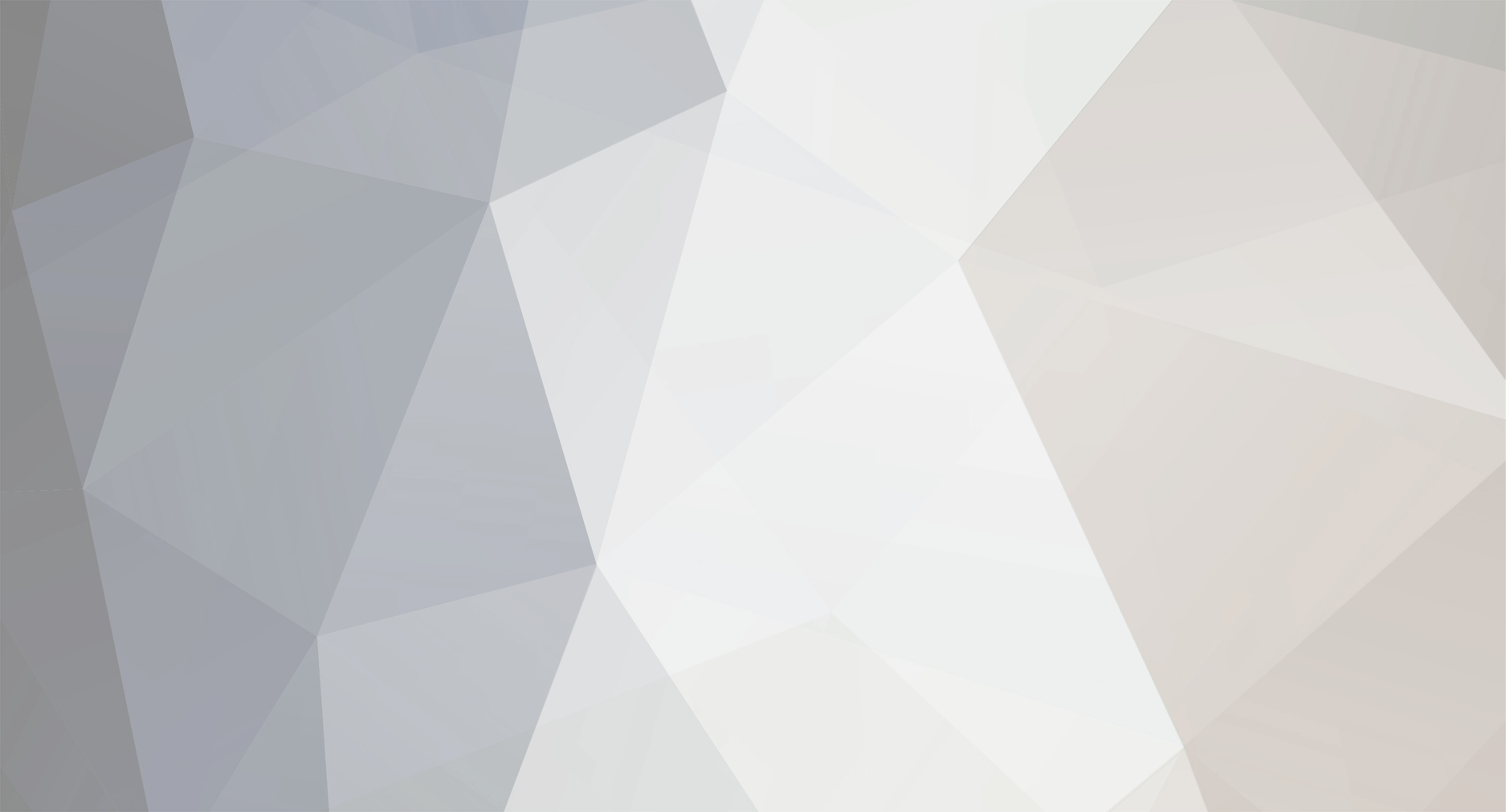
SubsonicSimpleton
Member-
Posts
945 -
Joined
-
Last visited
Content Type
Profiles
Forums
Events
Shop
Articles
Everything posted by SubsonicSimpleton
-
Gotta love Doug's attitude to his own custom spector bass which he has played the cr*p out of http://youtu.be/aPekZmNeuDs?t=18m6s Doug and Vernon have the most insanely complicated signal processing I've ever seen, probably not a good idea to watch this if you have bad FX GAS.
-
Gordon Bennett... I've bought basses for less!
SubsonicSimpleton replied to alyctes's topic in eBay - Weird and Wonderful
I think it's a typo and he meant £1.75 -
de afwerking mk4-7 - blablas next build project
SubsonicSimpleton replied to blablas's topic in Build Diaries
The nut slot looks quite narrow, what material are you going to use for the nut? -
Look in the yellow pages for engineers merchant, engineers supplies, fixings and fasteners. Engineers merchants supply the engineering trade, so they don't really devote much space for typical retail browsing, usually just a few things on display at the trade counter - as they warehouse a lot of stock they are usually located on industrial estates. Probably worth giving a quick phone call first to check that they will be able to help before travelling - some suppliers are quite specialist, but they should be able to point you in the direction of someone who can help you out.
-
[quote name='Conan' timestamp='1398873485' post='2438537'] I can live with the rust, I would just prefer not to! I don't mind a bit of mojo on the bass body (the wooden bits!) but I hate to see tarnished and rusty metal. I'll get it sorted somehow! However, I have very little technical or engineering knowledge, so things like identifying threads and getting machine screws (whatever they are!) is a bit beyond me I'm afraid! I'm fairly handy with a screwdriver - but that's about my limit! [/quote] The best way to identify them is to go to an engineers merchant, they should have the proper thread gauges and measuring tools to correctly identify the machine screws - they may even have suitable replacements in stock.
-
Maybe replacing them with stainless steel machine screws is worth considering, or at least identifying the thread etc while you have them out of the bass, just in case you want to do it at a later date without taking the bass out of service.
-
Are the screws seized into the bridge saddles? If they are, then personally I would avoid resorting to caustic chemicals, and instead apply a little thin oil (such as 3 in 1) to all threaded parts, giving the oil opportunity to soak in by capillary action which may require several applications over several days(and care to make sure you keep the oil off the finish). Use an old toothbrush to get any loose crud out of the threads that you can reach during this process, wire brush might damage the plating. Most importantly be patient, and don't force anything - machine screws tend to be made from cheese, and are easy to shear/strip threads/heads.
-
More hilarious relic shenanigans
SubsonicSimpleton replied to lemmywinks's topic in eBay - Weird and Wonderful
Just seen this horror on gumtree http://www.gumtree.com/p/for-sale/fender-jazz-bass-relic/1059170060 nice custom scratchplate is the road wear meant to replicate what happens if you keep your bass out of it's case in a small caravan full of woodpeckers? -
The Rean jack is identical as near as dammit to the switchcraft item in all aspects except the shape of the solder tags, and much more readily available, I replaced the same part on my Yamaha RBX775 recently which uses the stereo socket to switch the active circuit on/off, and my initial search for replacements turned up blank at the various suppliers who all were listing the switchcraft item as out of stock - might explain why the previous owner opted to fit an acoustic endpin jack instead.
-
I would suggest that you should look at creatively reusing something like fibre opic based christmas decorations/novelty lamps or solar powered LED garden lighting, with LEDs as your main lightsource if you want to maximise robustness and minimise electrical noise. There is an abundance of shonky tat waiting to be turned into something decent, and available very cheaply.
-
Preamp recommendations for a Jazz bass
SubsonicSimpleton replied to Old Horse Murphy's topic in Repairs and Technical
If you found one pre-amp led to too much fiddling, what has changed? Maybe it is worth considering using an outboard solution instead - EQ is EQ whether you mount it in the bass, a pedal or a rack unit. And re:behringer BDI, have you seen this vid conan? http://www.youtube.com/watch?v=l8MbcoSsc14 -
[quote name='LukeFRC' timestamp='1398614305' post='2435733'] for the stupid amongst us.... what's tension bracing? I've seen a few types of cab bracing around. I don't know the proper names! Fearful seem to favour using wood on the panels to stiffen it - a bit like a acoustic guitar top. Bill Fitzmaurice seems to advise a grid of dowels pushing out, I think Andy at ACME does similar. And Barefaced seem to (possibly) use some simple matrix type bracing. [/quote] I was referring to the BFM/ACME ram in a bit of wood that is a little longer than the inside dimension of the cab method - no idea if it is actually correct terminology, but it made sense to me. It looks a little crude at first, but makes a lot of sense as all materials become stiffer as you shorten their vibrating length.
-
Any plans to experiment with thinner panels and tension bracing them? I was kinda suprised that there were no braces in evidence on the test cabs(that i could see from the pics anyway), but if you can get acceptable results with 12mm and no bracing, are you not interested to find out if you can push the envelope and make a thinner panel work?
-
If he made such a bodge in the first place, better to check the wiring yourself - it isn't complicated.
-
An interesting something (advice needed)
SubsonicSimpleton replied to Anthony Joseph Wiaczek III's topic in Build Diaries
This is going to sound a bit harsh, but from the pictures it looks like you have bought a bass shaped wall ornament that was made by someone who didn't understand or plan what they were doing. I'll elaborate - building a neck is a multi-step process, and although different manufacturers/custom builders use slightly different processes and construction methods, basically they all follow a very similar workflow, like this http://www.youtube.com/watch?v=loV2_sDuEo8 It would take an age to link every relevant video(but you can find them easily enough), but there is a basic common theme - they all plan their builds in a sensible order to enable accurate and efficient work and get the best result at the end of the process. Nowhere will you find a competant person applying finish before they have completed basic construction processes. Now take a really critical look at your new aquisition - does it look like it has really been executed by someone who knew and understood how to build a bass, or someone who knew how to make a nice bass shape out of wood? Is that truss rod channel cut accurately and straight, and has it been cut to fit a specific bit of hardware, or will the luthier need to make an oversize cut, back fill the cut with another piece of wood and then re-cut the slot to ensure the neck is sound? Is the neck to body angle and height relationship going to allow a playable setup once you have the fingerboard on? I would guess that the going rate for a refret is somewhere in the neighbourhood of £200(looking at a couple of luthiers website prices), due to the additional work involved in fitting the fingerboard, custom inlays etc and the difficulty of handling a fully built bass, I would guess that you would be lucky to see much change out of £600 for all the work you want doing (of course get some proper quotes, this is guesswork on my part) plus the additional cost of pickups and other hardware(which will add up if you want decent kit even if you buy S/H) - and really you need to look very carefully at what that money would buy you on the S/H market and decide whether you are just throwing good money after bad. I would guess that you would be lucky to spend less that £800, and this might stretch closer to £1000 if you start getting GASsy for preamps or needing a specific bridge or your inlays are particularly complicated etc - and it will have no residual value beyond parting it out. My advice is enjoy it as an ornament or flog it, minimise your loss and save your cash for something really worthwhile that you won't lose your shirt on if you want to sell it on at a later date rather than trying to fix someone else's flawed and abandoned project. -
If you are getting fed up with setting up/breaking down a complicated setup, at your next rehearsal, try just using bass->lead->amp and nothing else, which might make you feel a little exposed if you are used to using lots of widgets, but maybe rather than needing to build a rack system you just need to simplify, and if you do this a few times you'll soon work out what is really indispensible and what you can live without.
-
Thomann also do a 30" hofner violin bass copy http://www.thomann.de/gb/harley_benton_beatbass.htm Maybe also consider as another alternative refinishing/customising something like a used bronco as a project that you can do with your son to create something unique that he will really value as he has invested time and effort into and made with dad.
-
This just made me spray my monitor and keyboard with hot tea http://www.gumtree.com/p/community/musician-offering-spelling-lessons/1056958775
-
Odd Question Lakland bridge replaced with a badass??
SubsonicSimpleton replied to krispn's topic in Bass Guitars
[quote name='Sean' timestamp='1397835297' post='2427802'] The BBOT wasn't broken but until someone came along and made it better... [/quote] Define better. -
Odd Question Lakland bridge replaced with a badass??
SubsonicSimpleton replied to krispn's topic in Bass Guitars
If it isn't broken, then you need to ask yourself why are you trying to fix it? -
^^^ this pretty much, tone is for the most part down to the musician, but don't take my word for it, watch this video as mr Devine explains it pretty well. http://www.youtube.com/watch?v=-vUNUo3TbyI
-
Thoughts for a "different" pickup to pair with a P
SubsonicSimpleton replied to hamfist's topic in Accessories and Misc
What about piezo equipped saddles or a piezo strip under the bridgeplate instead of using a magnetic pickup. -
Reading through this thread I did notice that one aspect of this whole argument seems to have been overlooked, so I'll don my asbestos underpants and play devils advocate; Is lack of choice really a problem, or could it also be viewed as an advantage? Right handed bass and guitar players are overwhelmed with choices, which seems to lead quite easily to serious GAS which is basically an excuse to avoid practising because buying a new bit of kit believing it is the answer to your problems is easier. So if you viewed the situation from the POV of being a musician rather than a consumer/collector, being restricted in what is available to purchase shouldn't be a massive issue, as it is one less distraction from actually making music. The most talented musicians that I've had the good fortune and pleasure to play with all stuck to one instrument which they were intimately familiar with, and in the ocasional situations where I saw them pick up something else, they still sounded good and very much themselves. Conversely, I've also met plenty of bad/mediocre (mostly guitar) players with really extensive instrument/equipment collections, and if you can't play for toffee, a megabucks dragon inlay PRS and a boutique amp isn't magically going to endow you with talent. As a percentage, how many instruments actually get played on a daily basis as opposed to being ornaments, or sitting in their racks/cases unplayed for months or even years on end? Was Jaco Pastorius disadvantaged by using predominantly the same sunburst jazz his whole career? Undoubtably if you want to go on a massive GAS binge as a lefty and welcome the inherent financial issues that will arise, or are sufficiently rich to not care, then lack of choice is going to be frustrating, but is this really a barrier to making music, or just materialistic consumtion?