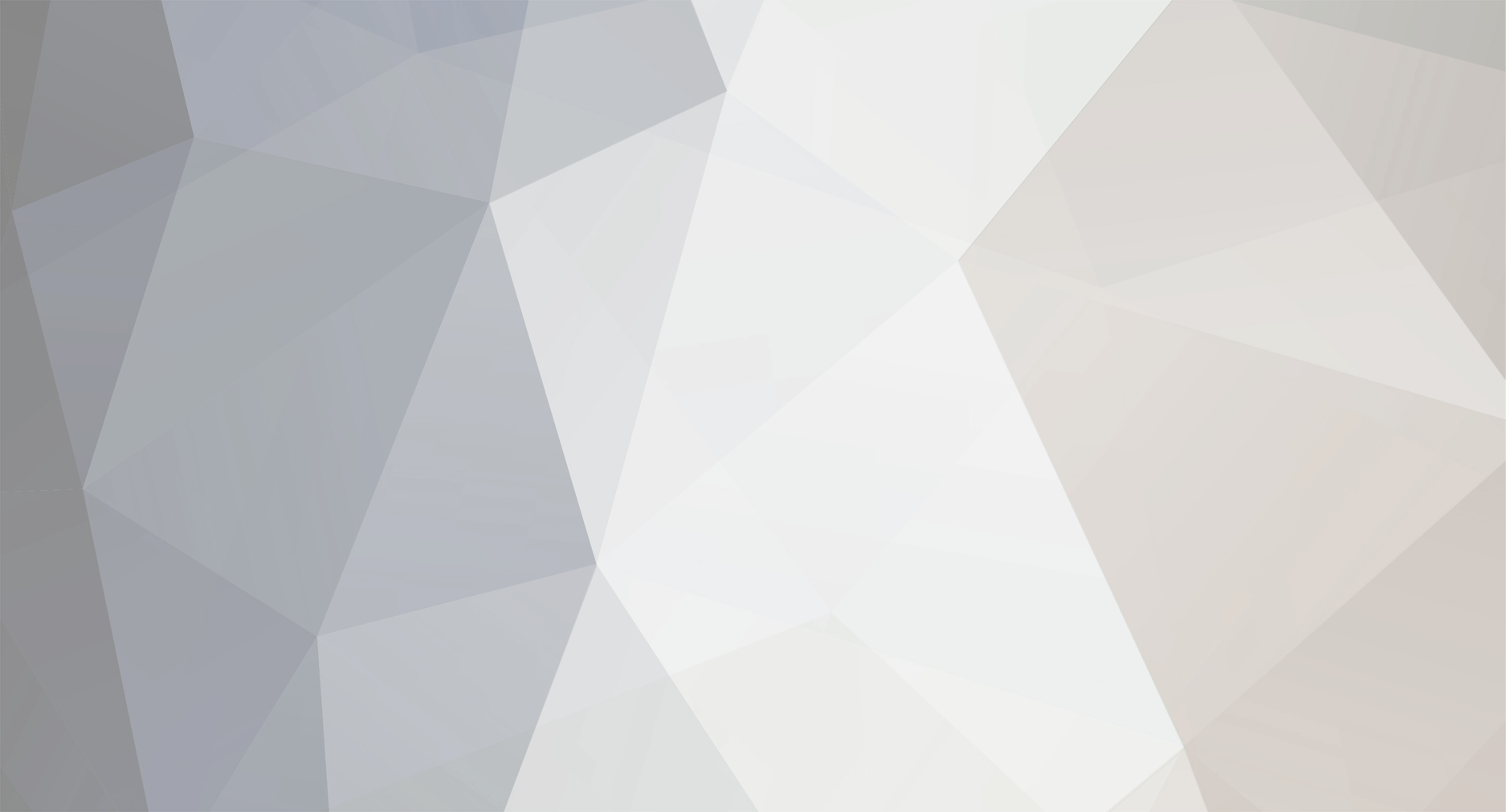
kodiakblair
⭐Supporting Member⭐-
Posts
3,372 -
Joined
-
Last visited
-
Days Won
1
Content Type
Profiles
Forums
Events
Shop
Articles
Everything posted by kodiakblair
-
There's a whole industry supporting it. I've done all sorts of mods and wholeheartedly agree 🙂 As @Cato said, it's not uncommon to see posts on US sites where folks have a shopping list of aftermarket parts before they buy the actual bass. There's little thought given, just a bunch of buzzword brand names they hope will gain them 'likes'. As an example of how little thought is given there's light weight tuning pegs, Hipshot Ultralites are popular. Now we've all heard of or experienced 'dead spots'. One cause is the mass of the peghead yet nobody seems to give a monkey's, it's shave 200g off and damn the results.
-
Two totally different things. Ed is well known and respected as a player, author and bass guru. He does straight up honest reviews. Lobster fella is selling folk on mods. He does his initial video then does another after he's had someone swap the pickups, whether they actually need swapping or not. He's looking for YT checks for video, kickbacks from his embedded links and lastly cash in his back pocket when he punts the bass on the QT.
-
Own several at 12lb and up. I'm much the same as @Reggaebass and @neepheid in preferring a heavier bass, also agree it's not a competition. Countless hours were spent as a laddie trudging to the hut with 50Kg cement bags on my left shoulder. That really messed up some folk but I was one of the lucky ones. Knees are shot these days, back and shoulders still in tip top condition.
-
No problem under the strings, dropped right in. If memory is correct David used 25mm slugs, that's the same as Entwistle machine screw poles. Plenty of firms aim for 19mm deep with pickup cavities, foam or springs do the lifting. I copied "plenty of" when making the pine slab body so sunk to the floor; 6mm proud. Still had to use foam to lift it as you've generally got 12mm from the body to the underside of strings. "Difference" was more lesson learned. I'd hoped the massive overwind would get me a 'mudbucker' but pickup placement is king there 🙂
-
I've never used Toltec but had David at Bloodstone build me a few. One was a massively overwound (29.9k ohm) split coil in a 51 single footprint, price was so reasonable I'll never consider buying pickups from outside the UK again. This is it next to his normal 51 single. More 51 singles and 51 hum cancelling have come from Martin Herrick in Wales. Recently I have pickups from another Martin, surname Harmer. He's involved with the Durham folk runningguitar building/luthier courses along with his White Label Pickups brand. Had ALNICO 2 split coil and 51 single from this Martin. He also made me a pair of 51 singles for a jazz bass arrangement. Needed a wider pole spacing for that so Martin cut me custom flatwork and the bridge went RWRP. Again very reasonable, about 60% the price of Fralins.
-
Which bass do you want, even though you shouldn't?
kodiakblair replied to BassAgent's topic in Bass Guitars
I'd like one of those Italia basses with the 4 lipstick pickups. Boy in Stirling has one for sale, been asking £600 for it most of last year. That's twice what I'm prepared to pay 😀 -
Where are we going to get scratchplates made these days?
kodiakblair replied to franzbassist's topic in Repairs and Technical
Brian has those, listed in his "Pickguards for various bass models" section. Size is 'cat 3', £40 for most colour options, £42 for carbon fibre, £50 for transparent or mirror finish. https://www.ebay.co.uk/itm/114490584526?hash=item1aa82badce:g:bt8AAOSwloxfnA5O -
I went the opposite way last time Stew. Felt the bridge on was too close to the pickup on this build. 30" scale length 24 frets. For my take on the Mosrite, I still used a 30" scale 24 fret neck but chopped it down to 20 frets. Forced me to move the bridge to a better position.
-
Where are we going to get scratchplates made these days?
kodiakblair replied to franzbassist's topic in Repairs and Technical
I second @neepheid's suggestion. -
Any chance the neck has a 21st fret overhang ? Sticking a block arse end of the pocket would shift the nut further from the bridge. Course you'd need to plug and re-drill the neck screws but the bridge can remain in place and the overhang will hide the eyesore.
-
If the finish was to be relic'd, why not.
-
I just made one from scrap timber, took about 10 minutes all in 👍
-
Bought a set of TruBass for £5 in a closing down sale. Loved them, they were on my P-bass from 1984 to when I sold the bass late 1989 🙂
-
I'd rather buy an Alpine. Made in France so cost about the same. https://www.alpineguitar.fr/work/50s-cat/ No "world-leading pickups", instead you get Hepcats which I'm familiar with 🙂
-
Nope, they can weigh more than some T-40s 😮 Good shout putting tapes on it, I always kept one strung with tapes myself 👍
-
Fact that the back of an axe head can be seen in the photo is just pure coincidence 😄
- 7 replies
-
- 1
-
-
- harley benton
- mosrite
-
(and 1 more)
Tagged with:
-
Could this have something to do with "Sorry, no photos." ? Warehouse could be miles away, not to mention the folks working there are likely way too busy shipping out orders.
-
If that's the case, expect to see one build diary a month throughout 2024 😁
-
This abstinence thing, does it cover building basses from parts you already own ?
-
Still to do. Matching black peghead veneer. Swap the W/B/W scratchplate for tort. Hide the TOM threaded inserts with a sticker, probably this one 😀 I'll likely have some 4 pole P-90s made but things are pretty good as is👍
- 7 replies
-
- harley benton
- mosrite
-
(and 1 more)
Tagged with:
-
Not a bad afternoon's work 🙂
- 7 replies
-
- 7
-
-
- harley benton
- mosrite
-
(and 1 more)
Tagged with:
-
Early Mosrite basses had 20 frets and the baritone had 24. Solution, remove the excess neck. You'll note, removing this much from the heel exposed the TR channel. Had scrap maple from the peghead reshape, handy material for a plug 🙂 Next thing was that massive bridge. Spotting a Guyker copy of the Gretsch Space bridge gave me hope 🙂 Only issue with that bridge is position, mess that up and you're stuffed 🙁 One way round this would be use a floating bridge so I made a cradle from scrap rosewood. Sorry, no photos; I was on a roll this afternoon 😁 Tail piece or string anchor was up next. Grabbed an old base plate and cut it down to size. Part 2 was shaping a block. The 4 screws hold it in position while drilling the mounting screw holes.
- 7 replies
-
- 2
-
-
- harley benton
- mosrite
-
(and 1 more)
Tagged with:
-
Set up was OK, intonation easy to do, balance was fine. Major problem. It didn't look very Mosrite 🤣
- 7 replies
-
- harley benton
- mosrite
-
(and 1 more)
Tagged with:
-
Had some teething problems with it. Heel was wider than the pocket, not a huge problem. Finding a bridge as tall as the TOM and with narrow spacing , that was a bigger problem. Bought this big chunky Sung Il, it was tall enough and I could shave the sides of the saddles for a tighter spacing. Wound up with this.
- 7 replies
-
- 4
-
-
- harley benton
- mosrite
-
(and 1 more)
Tagged with:
-
Continuing my trend for slightly off-kilter basses 🙂 No idea why Mosrites appeal to me but that appeal does not run to £1100+ for an original, £600 for an Eastwood copy nor £400 for the Aria 😄 Was very disappointed with Thomann last year when they launched the MR-60 but ignored us bass players 👎 To spite them I started a build though never got passed the rough cut 😔 Rough cut taunted me for months then I thought about the Retrovibe short scales David Konig was doing, guitar bodies/bass necks 👍 Trial run using a cheap Fazley with a baritone paddle neck went OK so Thomann got cash from me after all 😁 MR-60 guitar. Baritone neck from eBay.
- 7 replies
-
- harley benton
- mosrite
-
(and 1 more)
Tagged with: