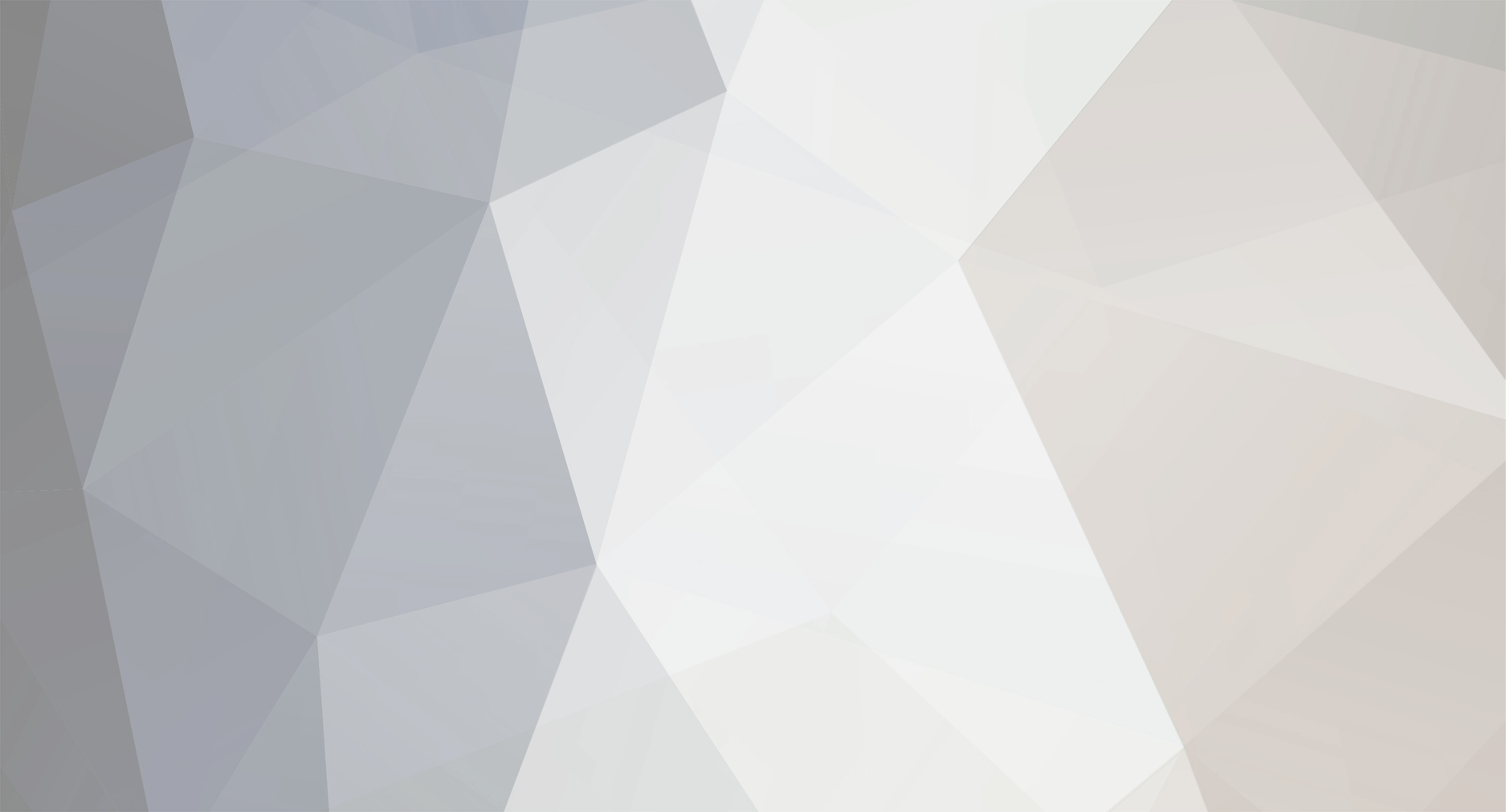
3below
Member-
Posts
2,670 -
Joined
-
Last visited
Content Type
Profiles
Forums
Events
Shop
Articles
Everything posted by 3below
-
NBD: Warwick Corvette 5 string: Refin in progress
3below replied to Grangur's topic in Repairs and Technical
If you have any big lift outs / chips it might be worth exploring the PTFE sheet, CA & sawdust method. It has worked really well on my refret and the ebony bridge I constructed recently. Body looks super -
The filter circuit appears not to be a 'notch' but is a [b][low pass] WRONG[/b] . The idea that it is a 'notch' filter is stated elsewhere on websites/forums. Using this website [url="http://sim.okawa-denshi.jp/en/RLClowkeisan.htm"]http://sim.okawa-den...LClowkeisan.htm[/url] [b][edit for correct link] [/b]and the following values: R = 220 Ohms, C = 0.02 uF and L = 1.5 H gives a low pass filter result. I used 30Hz to 12000 Hz as the frequency limits. I would like to model it in some other simulations before drawing firm conclusions. Quite why you would want to low pass the 'mudbucker' is debatable (and counterintuitive). More research to follow. [b]Edit for sense and correctness: [/b]After thinking and exploring the correct simulation I have realised that it is a low pass filter. The digram on the website takes the output voltage across RC. The Gibson EB3 circuit modelled takes the output voltage across the inductor L. This 'inverts' the filter to a high pass filter. My rhetorical question at the end of post was right.
-
Andy, I am just back from visiting various teachers I work with ('touring' Wales, very scenic 4hrs in car plus meetings). I will see if I can model the notch filter tomorrow and see what it should do.
-
Left arm or right arm? Whichever, it is probably due to a slightly changed playing position. I have done the same, right arm, changing from 34" to 30" bass. Do you want the bad news? You need to be really careful with the arm and elbow now. I got to the point where I could not lift pans, cases, mow lawn etc. Take real care now otherwise the injury can take forever (months or even a year) to fix.
-
NBD: Warwick Corvette 5 string: Refin in progress
3below replied to Grangur's topic in Repairs and Technical
How well is the BLO taking to the existing finish? How much existing finish did you take off? I also have a bubinga corvette and it would benefit from a 'light' refresh. Refrets with the right tools (Hosco cutters, tang nibblers etc) are not that difficult, I did my first this year on a 'project bass' with bound fingerboard. Am pleased with the results (though I could improve). -
Anybody here bought this? John Birch 8-string doer-upper!!!
3below replied to tony_m's topic in eBay - Weird and Wonderful
[quote name='spectoremg' timestamp='1476737199' post='3156883'] That's a hell of a 'saved from the bonfire' story. Could you find out a bit more about it? Might be interesting. What's that screw on backplate all about? nb. saw a JB Rick 4-string in dark blue at the NEC guitar show around '02/03 - looked lovely. [/quote] The screw on backplate was a JB feature to prevent buckle rash. As a young man (The Who) in the late 1970s and early 80s I was wearing Levis and Wranglers complete with large buckled belt. Fashionable at the time I am told, great for guitar backs. My JB EB/SG bass (in my hands circa 1980/81) had the same feature, the complete back 'scratchplate, it seemed to work well. Whatever JB used as finish was 'interesting', my bass (black) had lost a fair amount of neck finish, leaving some white coloured undercoat showing. JB did an excellent job of refinishing neck (and electrics) for not much money. This was when they were based in Bromsgrove. -
Anybody here bought this? John Birch 8-string doer-upper!!!
3below replied to tony_m's topic in eBay - Weird and Wonderful
Owned a JB SG / EB3 bass somewhere around 1980. Even had the man himself rewire the electrics (they were way to complex). It was a really 'solid' bass, had a feel of quality build and last a lifetime. Downer was the neck dive, really bad. Hope the restoration goes well. -
[quote name='BigRedX' timestamp='1476725506' post='3156696'] What value choke are you using? IIRC the Gibson circuit diagrams only give a Gibson part number rather than the actual value of the choke. [/quote] A further element of subterfuge / chicanery was alleged on the part of Gibson: The inductance values were stated incorrectly on the circuit diagrams to mislead other manufacturers. I have picked up this statement from internet research so it may have no credence whatsoever. Do you have a multimeter that will measure inductance?
-
I suspect the 0.02uF is a consequence of the Gibson notch filter design intention rather than a 'standard' tone capacitor. Do you know what the inductance of your choke is?. I would be interested in modelling what the circuit is intended to do.
-
Choke capacitor 0.02 uF which translates to 20nF. I wonder if a 20pF would have any audible effect (it is too late in the evening to do the maths out and work it out ). Soundclips awaited
-
Alternate zero fret / nut thought. You could widen the zero fret slot to (3mm? 1/8" ?) and fit a Fender type nut at the zero fret. Not in keeping with the EB3 vibe but probably a simpler solution. If you used black acetal (aka Delrin) it would not stand out much and could be followed by whatever nut you were originally planning. Other alternatives to acetal could be nickel silver or brass plate. If this was slotted (and probably glued) in it could be levelled and crowned. Apart from the side view in the fingerboard it would present as a higher fret, same frontal profile and appearance.
-
Hard to tell from the pictures, Is the extender bar pulling firm against the metal of the bridge and not indirectly into the body? I found I had to be careful with my home made one, it seemed very easy to ding the body with the bar and the ball ends (mine were not significantly countersunk). It was a wise move not attempting the recessed bridge approach, in that route (pun intended) lay potential disaster.
-
I have owned an EKO BA4 since 1981 ish (still using original strings). Used in small scale acoustic operations I have always felt it was not bad (nor great), it is big which helps. With a J bass pickup in the soundhole it was great for trad folk bands. A solid instrument but not the most finessed build quality (if thin finishes allow an instrument to breathe, this bass was suffocated at birth, it never got anywhere near oxygen).
-
[quote name='Manton Customs' timestamp='1476305215' post='3153269'] What angle did you go for? Gibsons tend to be excessive (usually 14 or even 17) and there's really no need for such a steep angle. [/quote] An interesting question, I have some extremely capable Physics students at the moment. They should be able to derive the maths and calculate what angle will prevent the string moving in the nut / zero fret view of the applied (plucking) force. Interesting to see how theory will compare to tradition. Should occupy them for a while
-
Hipshot supertone 3 point bridge fitted to SG bass: Baseplate is 7.95mm E & G string, 8.65mm A & D string. Saddles are 7.7mm deep (base to bottom of saddle notch). Approx 15 mm will be the lowest string height above the body (body to underside of string at saddle). Hope this is of some use.
-
Side angle on strings prevents rattling / spurious vibration in nut slots ☺ Measurements to follow on return to Mid Wales. Are you contemplating a routed recess for the whole bridge to lower into 📥? That would be very skilled and brave 🚫 The zero fret is an interesting issue. Logically (unless I am missing something) the zero fret is no different to any other fret in the near vicinity. Why does the zero fret need to be higher but the first fret does not? Is the amplitude difference between zero and first fret that great?
-
Looking good, commiserations about the blunder. I keep hoping I will not drop a serious one in my build. I could measure the lowest and highest string height available on my supertone 3 pointer if that would help. Am away from bass until Weds.
-
[quote name='Manton Customs' timestamp='1476010812' post='3150373'] Tightening the truss rod nut removes relief, so don't do that! To induce some relief you have a few options. Heavier gauge strings would work fine and after being on for a few weeks you could most likely go back down to regular gauge and the relief will hold. Alternatively you could tune up a note or two and leave it for a few weeks. Or remove the neck, loosen truss nut fully (if it isn't already) clamp into a slight forward bow and tighten the nut. All three should work, but as you're selling it I'd probably just put some heavier gauge strings on it and sell it like that. [/quote] Or the more 'direct' method, loosen truss rod, hold neck in left and right hand with middle of fretboard resting on or against knee. Give the neck [b]slight gentle pressure [/b] to aid the forward bow, no need to remove the neck. If this terrifies you (no reason why, I have used this method on many basses with no ill effect) you can achieve the same by placing the bass strings down on a flat surface (table) and putting a thin paperback book in the middle of the neck. Apply [b]gentle[/b] downwards pressure at both ends of neck.
-
-
On the home straight to the first non neck diving EB3 Time someone formulated an effortless finish that you can brush on, one coat and as if by magic it emerges as a perfect smooth high gloss finish, no further work needed. Not likely to happen though.
-
What I have found strange in this build is my obvious mistakes. All have been foreseeable but have still happened. I am working on getting it right 2nd time as I regain long lost skills.
-
Pictures show various divots infilled with mahogany and epoxy. Somehow very satisfying about shaping them to fit nicely. The small yellow blemish shown in earlier pictures developed into a substantial sized lump of well dried resin when it was exposed in a further router pass. Jack socket hole and wiring channel also sorted. Body is now ready to have the oak top glued on. The bridge, hmmm, I am not impressed with my workmanship here (as presented it is a long way from finished). The string holes do not align, I should have bolted a stop on the pillar drill table (and worn my reading glasses). The 3mm bridge saddle channel has a couple of router divots (the lighter grey parts in photo). I will attempt to sort these with ebony dust and epoxy. I may well have another go at a bridge, the ebony works out at about £2.50 for the bridge so no great loss. I now understand how I can make a better mk2 jig for this job.
-
Photos tomorrow, and agree on small steps forward. Am operating on the Zen principle, this is a thing of pleasure so have to be in the right frame of mind Hence slow progress at the moment.
-
Other than the headstock is the wrong way round, and it has a set neck it reminds me of some Peavey basses (of which I own a few) . Given that the Peavey basses are made with 'quality' wood and fetch as little as £100 used I think I will pass on this Gibson bass. In the interests of being non-partisan, I have owned two Gibson basses and currently my SG bass is my 'get to go' implement.
-
Slow progress, the day job uses time up. Tidied up the 'bad router day' issues. Sliced up various bits of mahogany into 2 / 3mm slices, bandsaw and file to fit the divots. Epoxied in and then routed flat. Started on the bridge, ebony slab planed and chamfered. String holes carefully measured and subsequently drilled. Today's lesson is - if you need reading glasses for close work, you should wear them. I got the measurements and hole locations spot on, not quite that good using the pillar drill making the holes. I should be able to 'lose' the slight misalignment issue. Next up, routing the 3mm bridge slot, have had several trials on this, still not really happy with the quality of what I can attain.