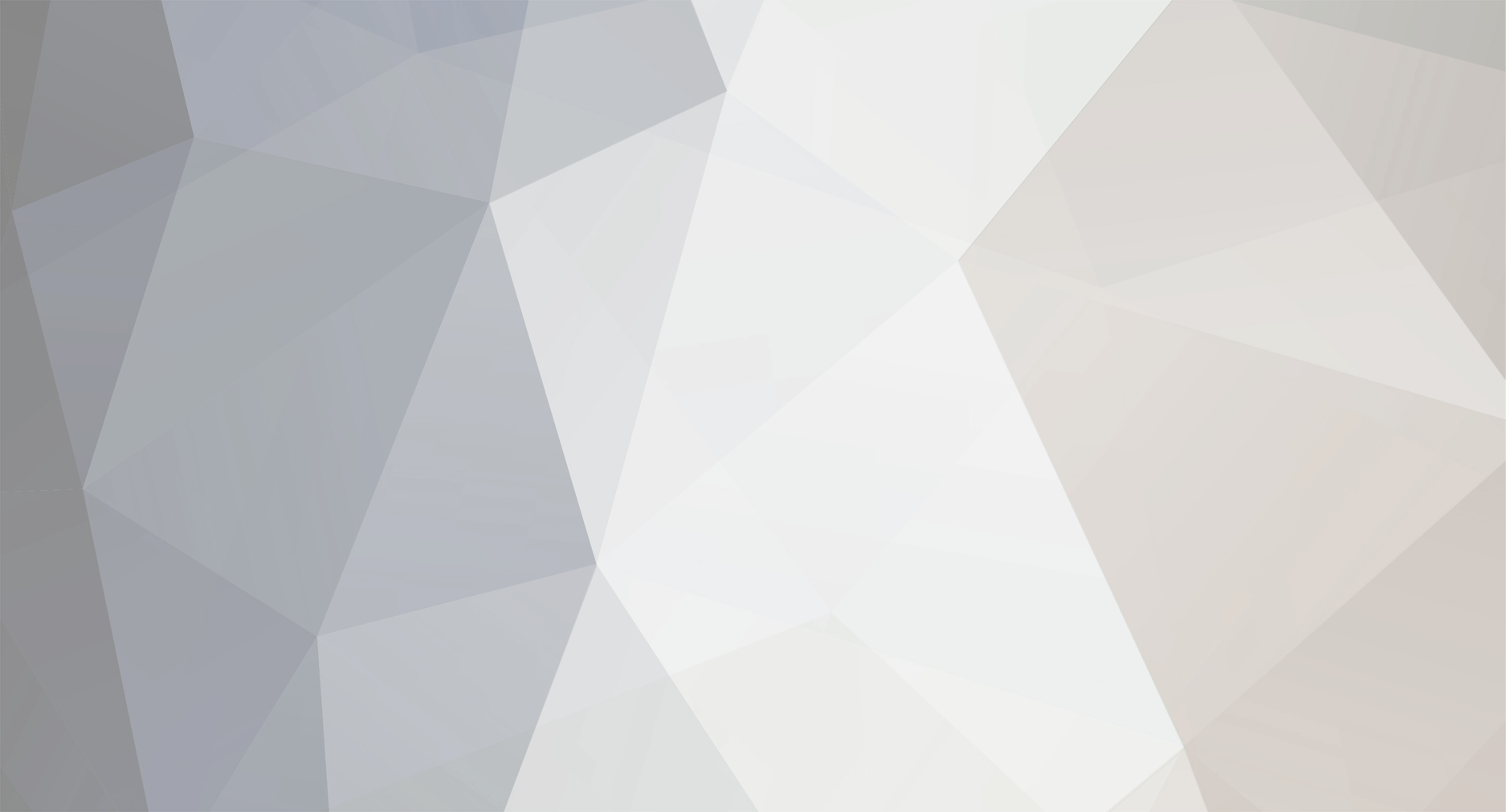
3below
Member-
Posts
2,670 -
Joined
-
Last visited
Content Type
Profiles
Forums
Events
Shop
Articles
Everything posted by 3below
-
Done some sums No guarantees that they are correct though. The slew times are well below the half period times at 50 Hz and 5KHz for 'normal'operation. It is only in the edge case of 1uA bias current that slew times might start having an effect at f >= 556 Hz. (The simplifications: the slew time needed is for a linear rise from a trough to a peak i.e. T/2 and op amp operating at 18V rail to rail).
-
From the data sheet the re-assuring statement ".. will perform in a manner similar to four amplifiers of the 741 type, but with improved frequency response and input characteristics". Good at the time but things have moved on a long way. The datasheet is quaintly retro compared to modern datasheets. Buried at the end of the datasheet are the very helpful (not) absolute maximum ratings "common mode input voltage - not greater than supplies", supply voltages ± 15V and Differential input voltage ± 25V. It would be interesting to find out just how much the 'deficiencies' contribute to the sound
-
@luthifer as per @funkle, great work. Apologies if you know these aspects already. The backbone of the circuit is a 2nd order low pass filter, an explanation and the maths is here https://www.electronics-tutorials.ws/filter/second-order-filters.html. or here https://www.ti.com/lit/an/sboa093a/sboa093a.pdf (p30). C26/C28 and C19 / C23 are coupling capacitors, preventing d.c moving through the circuit and not part of the filtering. Not being an EE I can't (yet) figure out what is happening with the 1 MOhm resisitor e.g. using the bridge circuit - if R46 is at 0 Ohms (Lo) then the feedback loop is the '2nd order low pass' version (ignoring the coupling capacitor). If R46 is 2.7 K Ohms then C29, R46 & R47 appear to be acting as some form of high pass filter https://www.electronics-tutorials.ws/filter/filter_3.html. Misquoting a great song I ain't no EE, I ain't no EE's son But I'll be your circuit man Till the real engineer comes
-
Not for this specific job but I have learned through experience that they can remove material very quickly. All too easy to remove more than you wanted to. This looks useful, though not UK based. Now found them in the UK, ToneTech. http://www.luthiersfriend.com/robosander/robosander.html#robo3
-
Not that long ago I wrote a page turner Blue Tooth app for ESP32 to drive my tablet with music tabs etc. This involved short and long button detection, debounce etc. I tried several libraries and eventually reached a simple approach adapted from somewhere that I can not now remember / find. I have pmd you some code that is straightforward and seemed effective. HTH.
-
I have also experienced unexpected font size problems with OLEDs. From memory (it was a while ago) my kludge solution was to keep the text messages short and use println(), not ideal but it sufficied. Good luck with tracking your issue down.
-
At the less exotic budget range (especially used examples on BC), Chowny SWB-1 short scale.
-
I owned a Kimbara strat copy sometime around 1977. Maple neck, natural body with nice grain, a well made guitar very playable.
-
Another big plus about older Peavey amps is that in the (unlikely in my experience) eventuality of a fault they are repairable on a DIY basis (or good local repairshop). I used a MKiii bass combo from 1980? until about 2010. Replaced with BF Big One and a Peavey Tour 700 (another bargain now when they appear).
-
Spot on, Firebass 700, built like a tank (personal experience) and from memory needed 2 Ohms to deliver the full 700W. I gave mine away as a bonus gift with the VBA 400 I sold.
-
-
Making a neck from Oak ? OK or No Chance ?
3below replied to Waddo Soqable's topic in Repairs and Technical
Depends on what you are doing with the headstock and which end the adjuster is going to be at. I feel this approach will be much easier than chiselling / plough planing a channel -
Making a neck from Oak ? OK or No Chance ?
3below replied to Waddo Soqable's topic in Repairs and Technical
With some careful thought and measurement a thin strip of a suitable thickness down the middle can have the truss rod slot cut into it before gluing. This is something I intend to try - one day when I get around to it. Decisions, decisions. Following earlier comments, the G&L bi-cut neck was not a symmetrical split, the channel was routed on one side only. The joins are so well done they are very hard to detect on my two G&Ls. -
Making a neck from Oak ? OK or No Chance ?
3below replied to Waddo Soqable's topic in Repairs and Technical
G&L used to do a curved channel in the two neck halves and then glue it up with the rod inside. I only know this as I have a G&L from that era. https://glguitars.com/non-compression-truss-rod/ . I am led to believe that some Peavey and Hamer basses used the same method. The (very, very beaten) Peavey Patriot bass I have has a two part neck that suggests this is the case. -
Making a neck from Oak ? OK or No Chance ?
3below replied to Waddo Soqable's topic in Repairs and Technical
If you are going to make the truss rod channel by hand (plough plane, chisel, drill) then your rebate idea would help (to my way of thinking). As @Andyjr1515says there will still be tidying up. -
Making a neck from Oak ? OK or No Chance ?
3below replied to Waddo Soqable's topic in Repairs and Technical
Life intervened, in 2017 I started getting divorced after 37.5 years of marriage. Six years later it is only just getting finished despite going to court. Anyway, the bass still exists, the blunders were rectified and the neck has been perfectly stable. I would happily use oak again in some laminated form. -
Owning a Kramer DMZ4001, I will echo @Shaggy's comment - seriously good basses. Since there is no (simple diy) neck relief adjustment a definite try before buying bass.
-
Very cool looking bass and great wood chops
-
50 year old Acoustic 136 combo 1x15 - *SOLD*
3below replied to funkgod's topic in Amps and Cabs For Sale
-
50 year old Acoustic 136 combo 1x15 - *SOLD*
3below replied to funkgod's topic in Amps and Cabs For Sale
-
50 year old Acoustic 136 combo 1x15 - *SOLD*
3below replied to funkgod's topic in Amps and Cabs For Sale
-
A really good summary. Does the bass sing unplugged is an important one for me. I have been heavily using my Corvette fretless on a daily basis for the last 4 months and it has really opened up in this respect in the last few weeks. No idea why this would be with a solid body bass, if you had asked me that several months ago I would have not believed it possible. Stating the obvious, really unlikely random parts can produce staggeringly good results. One of the best P basses I have ever played was put together by a teaching assistant for a special school music room. It had been hammered in the time I I knew it. Made with a Peavey neck, unknown body, BBOT bridge and a cheap Chinese pickup. It was seriously good, it had the 'sings unplugged' factor in spades. An absolute banger of a bass, as good as anything USA I own.
-
IIRC there was also a similar 1970s Carlsbro mixer amp - no backlighting or nifty handles though. Can't find any images, however Carlsbro have certainly made a vast range of kit over the years. I had a job offer with HH circa 1979 but in the end chose to work for British Gas as a research engineer. Interesting video on their website https://www.hhelectronics.com/history