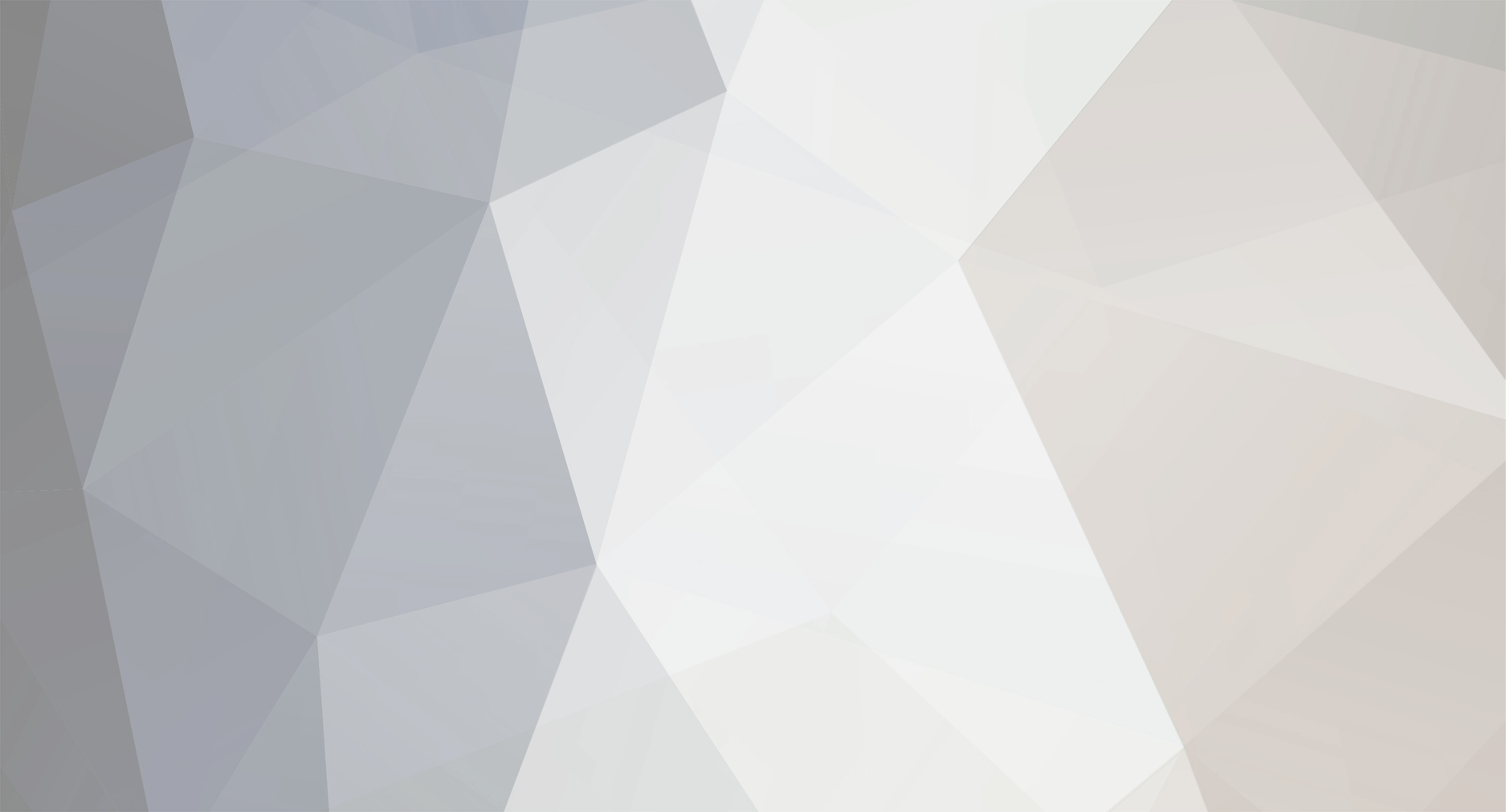
alexclaber
Member-
Posts
5,091 -
Joined
-
Last visited
-
Days Won
1
Content Type
Profiles
Forums
Events
Shop
Articles
Everything posted by alexclaber
-
Happy Barefaced Retro Two10 Christmas to me
alexclaber replied to Jenny_Innie's topic in Amps and Cabs
[quote name='Conan' timestamp='1423471372' post='2685030'] Or speak to Alex and see if you can get some of the silver cloth to put on your existing Compact? [/quote] Sadly it's impossible to change the grill type once they're built, as the mount for the steel grill takes up the space where the frame for the cloth grill needs to go. [quote name='Jenny_Innie' timestamp='1423484443' post='2685255'] Although I read Alex saying somewhere that they can be used that way, but are designed to be horizontal. [/quote] I'm glad someone's listening to me! -
[quote name='Musky' timestamp='1423327698' post='2683614']Why do many of these top flight luthiers who are carefully selecting their wood for its tone then go and lacquer with tone killing finishes?[/quote] They don't - they do polyester finishes right! But there's a big difference between a carefully applied thin layer of poly and the thick coat put on many lower budget mass produced basses. I only took the finish off the neck of my first bass (Hohner Jack) because I preferred how the raw wood neck felt on my second bass (Warwick Streamer), and it came off so easily with a hot air stripper I thought I'd do the body as well because it would look cool. Unfortunately the body was finished in a different way and it was a nightmare to strip - I ended up using a big drill with a wire brush on it! Never got around to getting it to a luthier quality finish but I could not believe how much it improved the tone - this was the late '90s and I hadn't been in the world of bass for all that long, so there was no placebo effect going on. The whole band noticed it, even the drummer!
-
[quote name='xgsjx' timestamp='1423228365' post='2682479'] I know it's been a commonly debated subject. I know that in an acoustic instrument there is a noticeable difference, but for electric, the debates have mostly said it's minimal. The string rests on the bridge & nut (another 2 parts that are contested to whether they affect tone) & the sound is picked up from the electrics. From my understanding, the density could impact how the vibrations travel, leading to < or > sustain, but not play that big a part on the actual tone, hence different body materials still sounding similar to ones made of wood. Is it more to do with the density of the material & not whether it is wood? Meaning that if a bass is made from a hard alloy, it would have similar characteristics as a hard wood of similar density? I've not got the means to test & it's hard to trust a manufacturer, as they're gonna say what is going to sell more.[/quote] I'm trying to remember if I've written a column on this - no, I haven't... So this is how I see how tone happens, step by step: 1. Finger/thumb/pick strikes the string. This determines the initial balance of harmonics and percussives. 2. This stimulation excites the whole string. 3. The excited string loses energy to four places - the pickup(s), the air, the bridge saddle and the nut/fret/fretting finger. 4. The energy lost into the pickups and air is gone for good. 5. The energy lost into the bridge saddle travels through the bridge and set the body resonating. 6. The energy lost into the fretting finger is gone for good, whilst that going into the nut/fret travels down the neck and sets the body resonating. 7. Depending on the frequency of the energy entering the body/neck it is either damped and lost (turned into minuscule amounts of heat), resonates and emits into the air and is lost, continues resonating within the body/neck or resonates within the body/neck and is returned into the string via the bridge/fret/nut. The tone you hear from the bass is what the pickup 'hears' at its specific location - with a wide-range pickup like an Alembic or Q-Tuner it's very similar to what you'd get from close micing at that point. The tone at that point depends hugely on how the body/neck of the instrument is taking energy from and returning energy to the strings. I noticed a HUGE change in tone after removing a very thick layer of gloss paint off the neck and body of my first bass - it was absolutely transformed, it suddenly sounded alive! Instead of sounding dead and always wanting new strings it had much more midrange character and growl and more brightness up top. Why? Because the body/neck were no longer damping so many of the good frequencies. Before the bass cab thing I spent ages on designing a custom bass and put a lot of effort into finding out everything I could about how the parts of a bass affect how it sounds. Another example from that custom bass thing is I ended up with an ebony nut. Why? Because when you fret a note your finger provides damping despite being behind the fret. My first bass had a zero fret and I always noticed that the open strings on that sounded much more different from fretted notes than when playing basses with normal nuts - despite some luthiers claiming a zero fret sounds more consistent (a classic case of a brain's ideas over-riding the truth from the ears). But open strings with bone nuts still sounded different to fretted notes - with an ebony nut the softness of the wood (compared to metal anyway) adds that bit of damping which the finger would - voila, more consistent tone! I always say that when bass shopping, play it unplugged. A bass that sounds great unplugged can always be made to sound great plugged in with the right pickups. A bass that sounds mediocre unplugged will never sound better than mediocre plugged in, whatever you do. It is an acoustic instrument first - just a very quiet one!
-
Happy Barefaced Retro Two10 Christmas to me
alexclaber replied to Jenny_Innie's topic in Amps and Cabs
[quote name='LukeFRC' timestamp='1420503107' post='2650186'] can I just interject here and say sorry. I'm a fussy designer - and I made a comment about a logo that isn't great in my opinion - but it's also not awful and far worse design horrors have been unleashed on us bass players... warwick up to a few years ago used comic sans as the main typeface on their amps and so on. Please don't turn this thread into a barefaced slagging one - we've had enough of them. I'm interested in Jenny's new cab, and the new designs generally - I think I've played through about 5 or 6 different barefaced models - 1 I didn't like, 1 was very impressive, 2 were brilliant but not my taste and 1 was one of the best bass cabs I've ever played through. I'ld buy one tomorrow if I had the money. Please don't start the slagging again. (I was actually thinking - what other UK based, UK build amplification/cab companies do we have? Barefaced, Purple Chilli, Matamp and [i]some [/i]ashdown stuff are all I could think of, does anyone make speakers in the UK still Celestion I guess... and volt which Glockenklang use?) [/quote] Luke, if you'd been on basschat back in 2008 you could have designed the logo! I can't find the old thread about it but it was a collaborative affair with deksawyer providing the bulk of the final look. So blame him if you don't like it! -
Barefaced Cab Problem (and I can't get hold of them!)
alexclaber replied to misterook's topic in Amps and Cabs
This is our landline: +44 (0)1273 945959. Our previous mobile number is no longer in use, so don't call or text it if you want a response! If you don't receive a timely response from [email protected] then email again and cc [email protected] Emails are constantly monitored during weekday working hours and responded to in order of urgency. Occasionally (usually when sent out of hours) they don't get labelled and marked correctly and thus don't get dealt with when they should. We also have Facebook: http://www.facebook.com/pages/Barefaced-Bass-speaker-cabs/130257677703 We prefer email to Facebook messages but if you haven't heard back then feel free to try it. -
Barefaced Cab Problem (and I can't get hold of them!)
alexclaber replied to misterook's topic in Amps and Cabs
Sorry, I failed to mark your email down to reply to, so it got forgotten. You can't text us, we no longer have a mobile number. We have a landline which usually gets answered during working hours but not always if we don't hear it! If you don't get a response within a reasonable time frame, please email us again. Email is by far the best way to get hold of us. Apologies again for missing your email. -
NCD - Barefaced Retro 210 4 ohm - Story so Far....
alexclaber replied to Huge Hands's topic in Amps and Cabs
[quote name='Huge Hands' timestamp='1422441021' post='2672574']Duly noted Alex, but I have to say that when only using one cab stood on the floor, it feels a bit too low down to sit horizontally (have to bend down to adjust my head!), so it feels like the natural thing to do to put it on its side. I was using it again last night in this way and was absolutely loving it - sounds really good across the range. If you're saying it's even better horizontally, then all the better I say - will try this next time![/quote] It basically sounds fatter when horizontal because both speakers couple with the floor up to a higher frequency - I guess it's less 'hi-fi' but nothing about this cab was designed to be hi-fi. And that coupling makes it louder through the lower half of the frequency range. It also sounds deeper when horizontal because of what happens to part of the tuning of the hybrid resonator when the port is coupled with ground (as in the vertical position). -
NCD - Barefaced Retro 210 4 ohm - Story so Far....
alexclaber replied to Huge Hands's topic in Amps and Cabs
The Retro Two10 is designed to be predominantly used horizontally - that's why it has a crossover inside to give it good dispersion that way around. We've put feet on the side so customers can use it vertically if that helps in a difficult acoustic situation (it can help in boomy/muddy rooms) but it's not how the cab is designed to look best or sound best. -
[quote name='artisan' timestamp='1422093244' post='2668552'] last year i enquired about buying a new bass cab mainly for use with my upright bass,all of my emails were promptly replied to & Alex recommended the Big Baby 2 for me. last November i again made enquiries & once again my emails were replied to promptly. so i placed my order & paid my deposit,no confirmation email,receipt or anything which i was a little worried about,i ended up emailing to ask if they had recieved my order,after a day or so i got a reply but this was several days after i placed my order. since then some emails i sent were not replied to at all & i felt i had to chase Barefaced for a reply. i recieved my cab in January,which i was pleased with but had to push for a delivery date,now i wasn't in a massive rush but had heard nothing at all & was concerned my cab wouldn't arrive before my first gig of the year. since my cab arrived i sent another email thanking Alex for sorting my order out & saying how pleased i am with the cab,so far, & guess what,yes no reply. Barefaced need to sort out their customer service as if they wish to operate as a top flight company then they need the level of customer service that goes with that,as it is i just spent £699.00 with them & feel pretty much ignored,like i am an inconvenience to them. i work in retail & no matter how busy i am i look after my customers properly,if i didn't i'd be out of work pretty damn quick. having said that my cab is awesome,first gig next saturday,but i'd think carefully before i ordered anything else from here. rant over,as you were. Edit: I just remembered I also emailed Alex asking for a receipt/invoice for my cab & he's ignored that email too. totally craps,if my cab doesn't really impress me next Saturday he can have the sodding thing back ! [/quote] Hi Neil, I'm so sorry to hear that you feel like this. I know when you placed your order I said the current queue was "a month or so, though that depends on how smoothly things run here". You should have received a confirmation email from PayPal as soon as your order went through - I just made a purchase from our site via my personal email address and it worked but I know emails like that can vanish into spam folders. As you said, two days later I did send a confirmation email confirming your cab had been allocated into the production queue. When you got in touch on the 22nd Dec warning us of your next gig on the 31st Jan I replied that day to say you should have the cab before then (I don't think I ever say 'definitely' nowadays because knowing my luck the bloody building will then go and burn down or something...) As you'll recall you emailed on on the 13th Jan because your band were hassling you about not having a cab to rehearse with, so we jumped you a week up the queue and sent you a cab that day. I was very happy to read your overwhelmingly positive comments about the appearance and build quality of the cab and about the tone from your low volume tests when you received it and noted down that you'd asked for a receipt "but no rush whatsoever for that", so I was looking forwards to emailing you with that receipt and asking how your first gig (next weekend) had gone with the cab. I saw your email earlier today asking for your receipt again so I'd made a note to email it to you next week, as it must have been more urgent than I realised. I'm sorry you didn't get the cab before Xmas as you'd hoped (and obviously the Xmas break delayed it by another fortnight). I'm really sorry that you feel like you've been "pretty much ignored" and an "inconvenience" and I assure you that's not the case. Based on your email on the 16th Jan I'd assumed you were very happy with the cab and I was looking forward to finding out how it performed on your gig at the end of the month. The only unreplied email from you I can find on any of our accounts is the one you sent saying that the cab looks fantastic and asking for a receipt, which I was going to respond to the first week of Feb after your first gig - I will check nothing has vanished into the spam filters on our non-gmail accounts in case you sent one to the customer services address and it disappeared into the ether. I hope you understand that we didn't mean to disappoint you in the way your post describes and I wrongly thought we'd done a decent job of looking after you. ----- To anyone else who has been frustrated by our customer service, since we started in late 2008 right up to now, I can only apologise. Starting and growing a business which does all its design and manufacturing here in the UK has not been an easy ride and the challenge of simply surviving has sometimes caused us to drop far too many of the 'non-essential' plates that you have to keep spinning if you want to be a great company. With the investment we've put in over the last 6+ years I think we're finally at that point where we have products which are world class in all aspects, manufacturing processes which work efficiently (we're still sorting out some of our stock control and accounting processes) and we should be able to make sure that 99.99% of our customers have a great purchasing experience once we've tidied up some more of the details of how we deal with all our pre-sales, pre-shipping and post-purchases communication. I do have a list of things I want to address to improve the customer experience, the first being finally having cabs in stock or with very short lead times (at the current production rate this should happen in February) and the second being a nice printed quick-start guide to go with each model and a more comprehensive manual, so customers can get the most out of their new purchase. There's lots more but they're the first two. For a long time I've dreamed of the day when anyone emails and I can say you can have it tomorrow (or at least this week if you're overseas) and that's close to being a reality. If you did buy a Barefaced cab in the past and either returned it or sold it on fairly quickly because you were disappointed with our service or the cab itself, if you'd consider giving us a second chance then I'd be happy to consider loaning out some demo cabs. It's less of a gamble buying our stuff now we're better established but we really do particularly appreciate those of you who were brave enough to buy an oddball cab from a funny little British company run by an argumentative sod, especially when you fell foul of us being spread too thin to provide consistently good service... Best regards, Alex Managing Director Barefaced Ltd www.barefacedbass.com
-
I can't say that much because I don't want other manufacturers to catch on to some of what we're doing (I'm sure Stevie is rolling his eyes at this and thinking that it's just more 'hyperbole' and smoke and mirrors...) but we doing things with the new drivers that some of these posts suggest is impossible. The reason the new drivers took so long was because we were trying quite a lot of different methods to achieve key aspects of performance and some worked and some didn't and some of the things that partially worked had aspects that did work so then we took the good bit and tried another approach and so on and so forth. It was quite a journey of discovery but bloody stressful because time spent on R&D is time not spent on building cabs, doing marketing and generally making money to pay the wages, rates, rent and my own living cost! The 12HP1020 certainly wouldn't achieve our goals. I know what if you went to John Meyer or Doug Button or someone with that level of transducer understanding, that once they understood the unique challenge of amplifying bass guitar (note that everyone posting in this thread is an expert user and we sell our cabs to everyone - including mechanically unsympathetic players in very loud bands who use very powerful amps) that they'd probably end up developing something similar to our new driver. I live in hope that it might take a while to understand the unique challenges of bass guitar because it certainly took a while for me and I think I now have a better grasp of it than anyone I know of. But nobody in the pro sound industry has tried to make something like this because they make mid-bass drivers and they make subwoofer drivers and they both have very different uses. An 'ideal' bass guitar driver needs some aspects of both plus some other aspects which are unique to it. I've just had a look through the technical pages on our site to see if any of them can be read between the lines to get a feel for what we're doing but having scanned through them I see that I have been quite circumspect about what we're doing. Much as part of me wants to go, "ta da! How clever is that?" I shall instead say that post 39 and 40 are on the right track, post 42 doesn't address that unless bandpassed that midrange drivers all tend to have quite unique 'sounds' due to their break-up modes, 10"s and 12"s can have pretty decent dispersion from 1-2kHz with the right soft parts, and post 44's first paragraph states the 'impossible' problem that we've solved, yes of course we've measured dispersion (!), and I agree about passive crossovers. Hope that's not too annoying a post, I would love to say more but I don't think that doing so would be a sensible business decision! (I have noticed that the big PA players are being more and more cagey about what they're up to too, to my great disappointment because I've learnt a lot from their writings).
-
This is a really great document - I want a big paper copy to stick on our factory wall! http://www.klippel.de/fileadmin/klippel/Files/Know_How/Literature/Papers/KLIPPEL_Cone_Vibration_Poster.pdf
-
[quote name='Jus Lukin' timestamp='1387365732' post='2311070']The reason I don't lust after one is that by all accounts they are very crisp, HiFi sounding cabs...[/quote] But they're not. If they all sounded the same there would be no point making so many different models!
-
[quote name='The Dark Lord' timestamp='1387374474' post='2311216']I think the lightness, good as it is, has had an impact on their quality. For example, the grill is very flimsy. I think that is a deliberate weight-saving measure. But there are other, non weight related things that I don't like about the quality. I mean, if you look at the way that the Barefaced logo has been attached, with clumsy glue, it's a bit "man-in-a-shed".[/quote] I feel like I'm in Groundhog Day. Your cab was built by by a "man-in-a-shed" five years ago. I see it was up for sale for £315. It cost £375 new FIVE YEARS AGO. Is that bad value? If you want to talk about the build quality with respect to current prices, look at a current model! The current models which are far from being built by "a-man-in-a-shed". Look at the current grills, the finish, the corners, the handles, everything. However, we still attach the badges with silicone - unless yours is one of the very first which went out without badges and a badge and epoxy kit followed for those first customers to attach. We don't use silicone because it's cheap or easy, in fact it's a pain to work with - double-sided tape, as used by many manufacturers, would be cheaper and easier. We use silicone because it sticks really well, stops rattles and helps to damp any grill movement and will keep the badge on there for a very long time.
-
[quote name='Phil Starr' timestamp='1387279120' post='2310074']It seems as if Alex Claber is having some input into the design of his drive units, that's a luxury I'd love to have.[/quote] There's a bit about it over here: http://barefacedbass.com/technical-information/generation-three-development.htm It was a very long process but on the plus side we learnt a lot on the way which changed our goals, so it worked out best in the end. Didn't feel it at the time though, R&D is expensive and I just wanted to get on and get the new designs happening! Here's something else to consider - what's the surround doing? And if you haven't thought about it already, what's the dustcap doing? And what happens at the joints of dustcap to cone and cone to surround?
-
Doug Button of JBL wrote a very good paper about some of this stuff: https://secure.aes.org/forum/pubs/conventions/?elib=5524
-
[quote name='Musicman20' timestamp='1387204862' post='2309286']It's worth noting that I am MORE than happy to be proved wrong or that things have changed with the new Gen 3 compact, If that small 12" cab can perform like the original but with more high end, then that is only a good thing.[/quote] Could you stop going on and on and on and on about the aesthetics of our cabs until you've seen one of the generation three examples then?
-
The old Compact's 15" runs to about 4kHz on-axis but that's pretty irrelevant unless you, your band, and the audience all stick their ears in the direct line of fire - which is impossible! Once you move off-axis it rolls off much lower and therefore doesn't work that great for a lot of players. If it works for you then that's excellent but it's not bright enough for everyone. The 15" in the Orange cab isn't as clean (being a ferrite magnet and different cone/suspension and voice coil), so it synthesises extra brightness and has a really strong sharp treble peak from the dustcap - but you'd need almost two of them to produce as much bottom at full tilt. Our new 12" runs to about the same point as the Compact's 15" on-axis but sounds far brighter in the real world because it disperses that treble around the room. This is not because it's a 12" rather than a 15" (though that helps a bit) but because the non-pistonic behaviour hugely improves the dispersion. Anyone claiming that a driver of a certain diameter will only work to a certain frequency because of its size limiting dispersion doesn't know what they're talking about because no musical instrument loudspeakers manage to behave pistonically beyond a few hundred Hz at best. I see people insisting that a woofer of diameter X must be crossed to a midrange driver at frequency Y and just roll my eyes at the massive oversimplification of the problem and the lack of understanding of non-linear behaviour from some self-appointed experts... I can totally see why Musicman20 didn't like the sound of the Compact! I know our Compact owners mean well but sometimes reading these well-meaning posts is a little like reading someone insisting that a Bedford Rascal is ideal for removal men in a van forum because a whole load of florists love them... Horses for courses! Nothing is perfect and engineering is all about getting the least bad combination of compromises for a specific goal.
-
At a guess fewer than twenty Barefaced cabs used foam for damping. Very early on we switched to a different material which worked better, was easier to handle and cost less. The foam was the same material used for mattress toppers - I'm surprised it's crumbling already but maybe it's been exposed to quite high heat if the cab has played long loud gigs and that's caused premature degradation? Anyway, it's only in the very earliest Compacts and Big Ones, with plastic corners (and only in a minority of the plastic cornered cabs) - cabs that seem to sell secondhand now for little less than they were originally bought five years ago. We're hoping to take on an admin person early next year so any issues with feet and handles on the old models will be addressed more promptly. If your handle has worn out you can have a free replacement. If you want to upgrade to the new handles we've worked out a way to do that despite them being different sizes - we'll put an upgrade kit on our site which will be priced at the cost of us to assemble and post it. I can't see the new handles wearing out in a very very long time.
-
Run the S12 on one channel, run the Compact on the other channel. You can't use the GK biamp because that would require a tweeter and a specially wired cab. Normal biamping is rarely a good idea with bass cab - much much better to share the load of producing the lows between as much cone area and excursion as possible - the S12 can produce more bottom than the Compact but an S12+Compact working in unison can produce yet more. The earliest Compacts and Big Ones had open-cell foam damping rather than batting - I guess it could degrade over time and go crumbly like some foam can do. It's easy enough to replace if it bothers you. Any cabs built after spring 2009 won't have that problem. On the other hand, some crumbling foam still works better acoustically than the complete absence of damping in many cabs!
-
[quote name='Dropzone' timestamp='1386693048' post='2303165']plus will be a bi amp with the compact expected to take the lows.[/quote] Please don't do that.
-
And I wouldn't describe the Compact as 'very transparent'. It is a pretty honest sounding cab but only within its usable bandwidth and that bandwidth certainly doesn't go high enough for everyone, especially once you're out in the room.
-
If the Compact was the be all and end all of our cabs: 1. We wouldn't have sold a whole load of alternate models, from pretty much the start. 2. We'd still be making it. It seems that most people who say they don't like the sound of Barefaced cabs have tried a Compact and didn't like it. Funnily enough I used to get lots of emails saying "I want to buy a Compact", I'd ask some questions about their tone and have to tell them that they wouldn't like how it sounded. Fortunately we'd usually have an alternate model that would suit their sound, but not always.
-
There seems to be a lot of confusion on this thread, so let me try to help! [quote name='basswesty' timestamp='1385186747' post='2285401']I had a G1 and a G3. Both great but I preferred the sound of the G1, I remember it being warmer.[/quote] You didn't have a G3. The G3 is a completely different model, the Super Compact, which only came out in Sept 2013. If you preferred the sound of your first Compact to your second Compact then you preferred the amp you were using with the first one or your memory is failing you. Some Barefaced history: Generation One models: Compact (1x15HO), Big One (15LF+6.5), Vintage (2x15HO), Big One T (15LF+6.5+tweeter) Generation Two models: Midget (1x12HO), Midget T (1x12HO+tweeter) Super Twelve (2x12HO), Super Twelve T (2x12+tweeter), Big Baby (12LF+6.5), Big Baby T (12LF+6.5+tweeter), Big Twin (2x12LF+6.5), Big Twin T (2x12LF+6.5+tweeter), Super Fifteen (2x15HO), Dubster (2x15LF) Generation 2.5: Original '69er (6x10") Generation Three models: Super Midget (12XN550+tweeter), Super Compact (1x12XN550), Super Twin (2x12XN550), Big Baby 2 (12XN550+HF driver), Big Twin 2 (2x12XN550+HF driver), updated Retro '69er (6x10), Retro 215 (2x15 - not launched yet!) There have been various versions of each model - the earliest G1 models had plastic corners and heavier ply, then metal corners and lighter dual-density ply. The G2 models all had metal corners, but the earlier ones were made by carpenters, the later ones cut by CNC and made in-house. The later G1 Compacts were also made by CNC in-house, the other G1 models had been discontinued by this point. There have been various other tweaks over time, bracing, damping, cosmetics etc. The Generation Three cabs are all new, based around a new 12" driver which we spent over two years developing, and in my opinion are quantifiably the best bass cabs ever made. They are clean sheet designs, from the ground up, building on the knowledge, expertise, experience and feedback gleaned over the last five years since Barefaced began. I believe they represent as large a leap forwards vs our previous models as our previous models were vs other bass cabs of their era. The only problem right now is we're so busy building them that we don't have enough time to tell everyone about how incredible they are!
-
[quote name='Deedee' timestamp='1384275576' post='2274732']I think the key is the depth of the cab. Years ago I could slide my old TE 2x10 combo into a saloon boot no problem. Now the cabs seem to be far deeper, although the Barefaced cabs don't seem to be as deep.[/quote] I don't quite get why so many modern cabs are deep but short and wide - I suppose it makes them look smaller in photos which is persuasive from a downsizing marketing thing! However it makes them less impressive looking and harder to hear on stage and harder to fit through doors and into cars. Weird... One (30cm deep!) Super Compact could handle pubs and small clubs easily unless your band is very loud or amp rather weedy.
-
It doesn't make a difference if the cabs are designed right. If you cut corners when designing the alternate impedance version of the drivers and the related crossover then it's perfectly possible for a 4 ohm and 8 ohm version of a cab to sound different. And if one has a sound which you prefer then you might declare that your amp sounds better into that impedance - but the difference wouldn't be because of the load or the power output but because the drivers sound different!