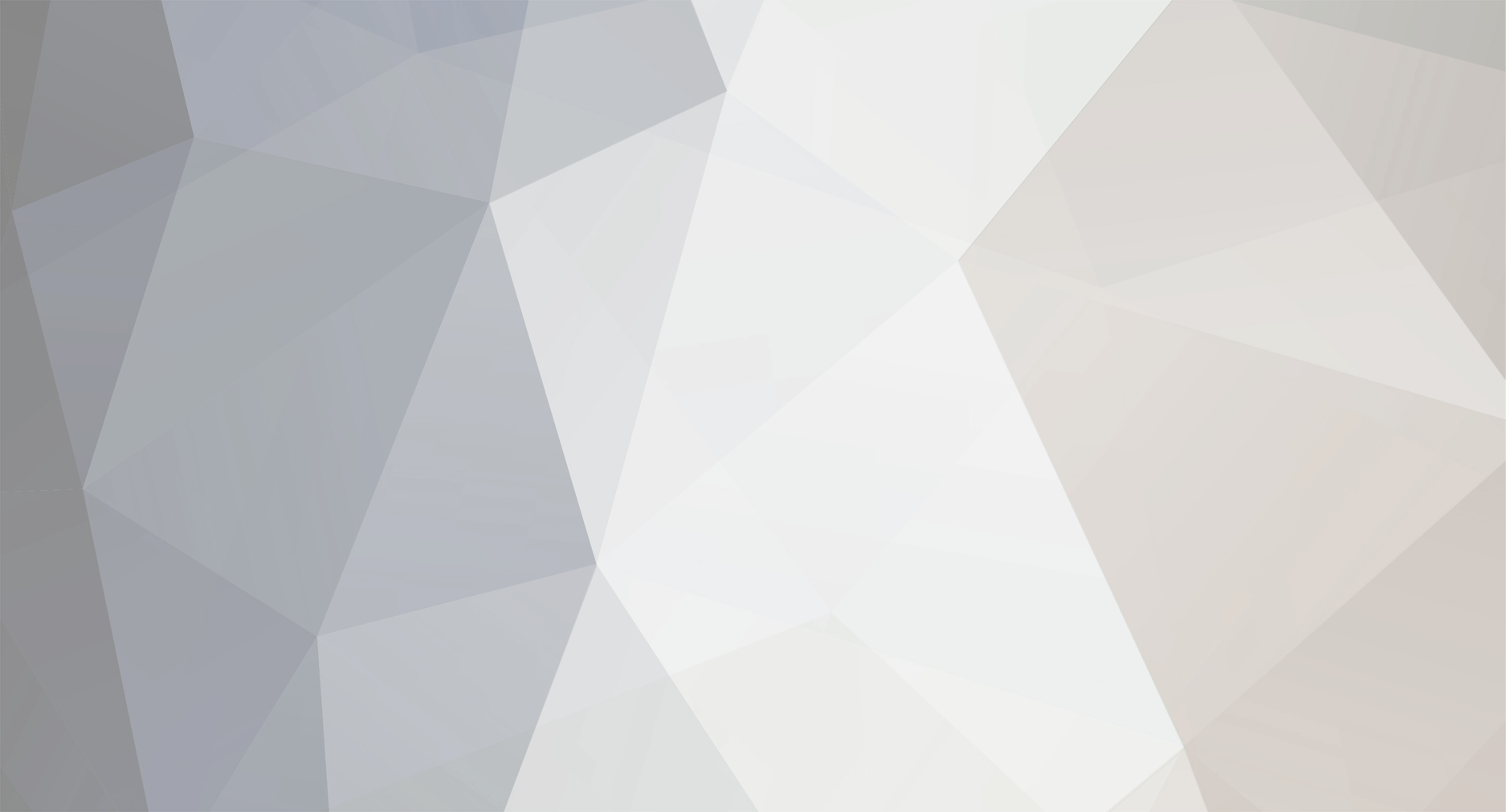
rwillett
⭐Supporting Member⭐-
Posts
1,625 -
Joined
-
Last visited
-
Days Won
6
Content Type
Profiles
Forums
Events
Shop
Articles
Everything posted by rwillett
-
I also am looking for exactly what the OP wanted. Something small and not headphone based, I have a NUX headphone amp which is OK but sometimes I don't want to wear headphones. I won't derail this thread though and will lurk. Interested in what @Phil Starr recommends for an amp for his self build as well. Thanks Rob
-
Just to let you know I tried the Positive Grid Spark with bass and then send the unit back. I brought it on pre-order and it was pointless for bass. Not so bad for guitar but useless for bass. I even made a video for Positive Grid as they were being difficult even though their website said it could be returned. No bass, no power at all. Just my 2c Rob
-
@SamIAm You're going through the same process I did for my headless bass. My thoughts are/were: 1. Taking the head off and the tuners will dramatically change the balance back to the body. My headless bass has zero dive. Your balance point will move back a fair way when the head and machine heads are gone. One way to check is to use a thin piece of picture framing wire between the two strap points and a tiny skateboard bearing to see where the balance is and how it changes. I have a <ahem> larger body mass due to good living, plenty of fresh air, lots of rugby and significant amounts of alcohol and chocolate, so that helps me stop neck dive. You may not be so lucky as me 2. The Nova kit is very good, and the bridge is quite light. So that won't adversely change your balance point. 3. You need to think carefully about how the Nova string clamp is going to fit. @JohnH89 modified the neck he kindly gave to me. He put a backplate on the neck where the Nova string clamp which is a very good idea. You need to think about filling the large holes left by the tuners, the backplate and front plate hide a lot. Cleverer people than myself (a disjoint union of 1 person and everybody but one person on Basschat) advise people to fill the holes with cross grain plugs which I struggled to find anyway and is one of the reasons my Aria Pro II neck is still in one piece. 4. My headless bass is slightly longer than standard to accommodate the bass tuners. I decided to make the body the right length so they didn't stick out. However other people did suggest that they did stick out and add some design features to protect them. Horses for courses and both ideas are in production by proper guitar makers. I decided to keep them inboard as I'm clumsy and would break anything not significantly protected. I just sketched out the scale and bridge positions in Fusion 360 to see what it looked like. 5. Your new body and choice of material will make the biggest difference. Fusion 360 is supposed to be able to make the calculations for balance points or centre of gravity. I don't have that version though My headless bass is now 3.99Kg, the neck is circa 1.8Kg (https://shop.rall-online.net/Fender-Standard-Series-Jazz-Bass-Neck-Maple) so this means the body is around 2.2Kg with everything connected up. The aluminium backbone is probably 1.3 to 1.4Kg from memory. The printed body paret is very light. Don't know how you want to do the body, but if its small, it may need to be dense. At the end of the day, you have a long lever attached to a smallish body so "you canna change the laws of physics cap'n" whatever you do. I'd test, test and test again. Duct tape may be your friend here. I'll happily weigh and measure things for you, but I'm in Italy on holiday with family until Weds. Rob
-
Pictures please.... I can imagine something like Grizzly Adams with a bass that Lurch would play in the Adams family
-
But the very slight upside for you is that if I ever have the cash for a good bass, I’ll know exactly where to come to for a sensible deal.
-
The Short Scale Bass Appreciation Society!
rwillett replied to Baloney Balderdash's topic in Bass Guitars
The current exchange rate £:$ is around 1.25 (ish). So £349 is approx $436. Take off VAT at 20% and we're back to $363. That's approx a 75% uplift. A bit more than a little extra profit. There are other costs as well but not a bad increase (for the seller) Rob -
Relatively speaking
-
Now that is a great picture, small, medium and large (relatively speaking) I like the way each Musicman has its own stack.
-
I can also assure you that Microsoft will still dump your email even when you have SPF/CNAME/DMARC setup correctly, have checked every sodding blacklist under the sun, have jumped through every known hoop to please them and still have no idea why they reject my emails to hotmail.co.uk. I’m old enough to have configured sendmail by hand so i figured i knew what i was doing. Anyway unless your business is IT or you get a kick out of reading large amounts of online manuals, find an onsite presence and buy it in. The only system I'd avoid is WordPress unless you like living on the edge about what the next exciting critical vulnerability will be and how quick you can patch the system. Friends don't let friends use WordPress. Rob
-
How the hell do you lose something that big and heavy? Given the weight of it, perhaps it just collapsed into a black hole and is now orbiting Jupiter...
-
Tremblap donated a rather nice EMG active pickup for my 3d printed bass guitar. Very nice and generous. Thanks Rob
-
Wow that's a great rabbit hole to go down. Be back in about six months 😊 Thanks. I'll dig down in there and learn. All the best Rob
-
Ah! The symbol for registered trademark. That's the sort of detail that really helps Thank you for the informative response. Rob
-
Could you expand on this for the uninitiated please?
-
This is what I like about Basschat. Never heard of Sunn before. I'm no expert now but I know a lot more than I did about Sunn guitars (which isn't difficult TBH). Will keep an eye out as I'm looking for parts and guitars. Thanks. Rob
-
Malicious Compliance
-
In that case just give the stuff to me and save a fortune on buying post-it notes. Always happy to help Rob
-
As I've more or less finished the headless bass, I thought I'd go back and look at the very first guitar I printed up. Just looked at it again and I'm going to apply all the lessons I learnt from the headed and headless basses back to the six string. Here's rough sketch of the new version. A lot more open, a lot more rounded, a lot thinner (31mm vs 45mm), probably a little lighter. The colours are there to identify components and are not being printed. It's also not a three string. That's there to check the neck vs bridge height.
-
EMG-P4 pickup, from the 90s, very used - GONE!
rwillett replied to tremblap's topic in Completed Items
Thats funny, I drove past Huddersfield this morning coming back to North Yorkshire. I live near Settle. Pm me and I'll find a method of payment that works. Thanks very much Rob -
EMG-P4 pickup, from the 90s, very used - GONE!
rwillett replied to tremblap's topic in Completed Items
The condition is not the slightest problem. If the case was too bad, I'd simply design and 3d print a new one, Here's a Wilkinson case I redesigned. The main reason for this one was to change the way it mounted so I could fit it into my 3d printed headless bass. The Wilkinson pickups are on rails rather than mounted to the body. -
EMG-P4 pickup, from the 90s, very used - GONE!
rwillett replied to tremblap's topic in Completed Items
Happy to take this off you if you wish. Thanks Rob -
One of the auctions is at Milnthorpe which is very close to me.
-
I didn't know that site exists, wish I still didn't Perhaps I need to check my bank balance...
-
@BigRedX It doesn't work on an old Macbook Pro 2013. It will on a new one, but all that method will do, will get you back to a version of OS X that's as old as Noah and the Ark, reliable but ancient. I think it was Snow Leopard or similar. You cannot get to whatever the latest version that is supported on an eleven year old laptop without going through a number of OS X upgrades. You cannot do it from the recovery partition. Apple has made it more difficult to do this, but it's not impossible. I did a similar chain of work when I donated an old Macbook Air to a gent here, so I knew more or less what to do. I had forgotten some of the details but thats just my old age. At the end of the day, I was trying to make it easy for Paul and his son. It's now done, Paul has the laptop, he can do with it whatever he sees fit. Rob