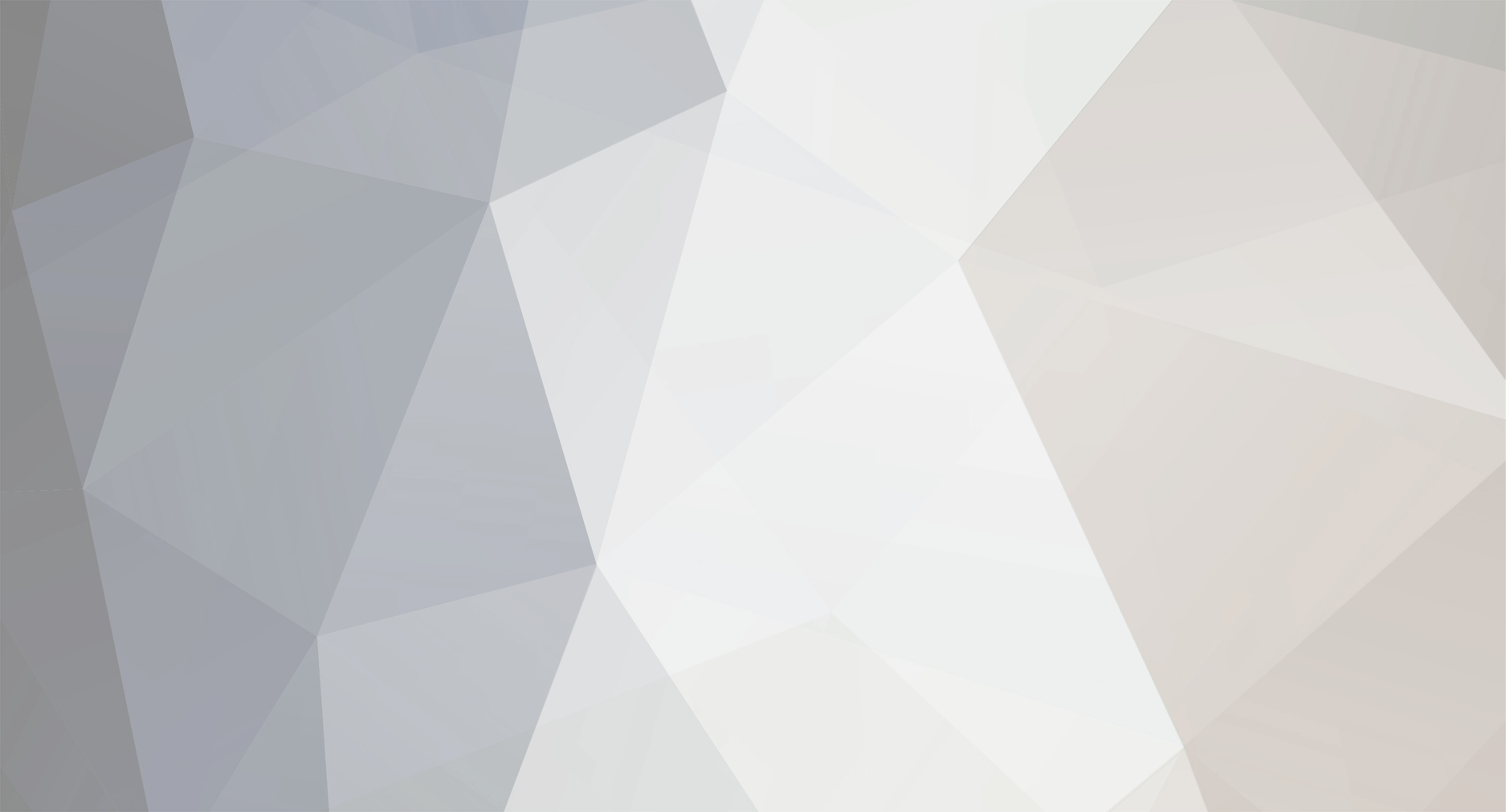
BOD2
Member-
Posts
1,112 -
Joined
-
Last visited
Content Type
Profiles
Forums
Events
Shop
Articles
Everything posted by BOD2
-
This should probably be in the technical forum, maybe someone will move it. Anyway....technically it should not be necessary if both pots and the jack socket are elctrically connected to the metal foil. In fact earthing these items separately will actuall create a mini "ground loop", but in the scheme of things its effect is negligible. In practical terms, however, it usual to earth everything together with a separate wire (pot to pot and pot to jack socket) because there is a chance that, over time, the contact to the earthing foil may deteriorate and break the circuit (or the foil could tear if a component twisted at a later date). I'd be inclined to earth them all with a wire - this is what everyone else does.
-
It's possible, but these things are usually quite robust. The jack socket controls the power to the preamp, so if there is anything wrong there then no power will get to the preamp. The jack socket will have three wires going to the tip, ring, and sleeve connectors on the socket. The tip is the "hot" output from the preamp. The ring and sleeve connectors and joined together when a mono jack plug is inserted so one wire should go to the battery and the other should go into the preamp. Double check this wiring first and make sure the jack socket itself isn't damaged in any way.
-
Some interesting information about valve/tranny amps here [url="http://www.award-session.com/pdfs/GEAR_TALK_1.pdf"]award-session.com[/url]
-
Resistance is futile ...I'll get me coat
-
[quote name='Jean-Luc Pickguard' post='117077' date='Jan 9 2008, 03:51 PM']Smoky pubs - I remember them. [/quote] Hey, does this mean that white scratchplates are no longer going to turn yellow after 10 years playing pub gigs ? The "distressing" and "vintaging" experts will have to learn some new trciks !
-
Anyone heard of a bass player called Nigel Clutterbuck?
BOD2 replied to Thunderthumbs's topic in General Discussion
Come on guys, lets take it for what it is. It's a guy in a music shop having a bit a fun showing what he can do. It's not a piece of music. It's not a performance. It's a bit a fun. Great technique, and I wish I could do that too. What do you play when trying a bass out in a music shop ? Root notes might be what we all play in a band but they're not very interesting played on their own in a music shop ! Is he a great bass player ? I don't know. I can't tell from that clip. I suspect that he is. It still just looks like great fun to me. Well done mate. -
Yes, it could be the string itself. Unfortunately the only way to rule it out is to change the string. Try playing the same "A" note on the other strings (and at octaves above). Do you hear the sound at all (even faintly) or does it only happen with the open A string ? Try damping anything you can touch in the string path (from bridge to tuner) while playing the note to see if anything is resonating. Try tuning the A-string up/down a semitone. Do you still hear the ring ? If you don't then it's something resonating somewhere to that particular note. If you do hear it when tuned differently then it could be the string itself. Do you have an old A-string lying around to swap temporarily ? Process of elimination is all you can try.
-
Something loose on one of the tuners ? Sometimes a resonant note will make something ring out in sympathy. It probably isn't anything to worry about.
-
And, of course, "Antoria" made those lovely Strat-style double neck copies as 6/12 or 6/4 string models. [url="http://www.ibanezcollectors.com/forum/index.php?topic=9478.0"]ibanezcollectors.com[/url] ....sigh...takes me back
-
Static build up on scratch plate / pickguard
BOD2 replied to EBS_freak's topic in Repairs and Technical
I've seen on may guitars/basses there is often some "tin foil" stuck to the back of the scratchplate around the area of the control cavity. The control pots (which are earthed) should touch this foil when they're installed. The foil is probably there for rudimentary screening purposes but it may also drain any static to earth. Do you have any foil on the inside of your scratchplate ? -
couple of questions about badass III bridges
BOD2 replied to ahpook's topic in Repairs and Technical
There's not much about Badass III in the sticky but it does say... "The BadAss III is similar to the BadAss II but is designed for Fender American Deluxe basses with through-body stringing and only 3 mounting screws. It features pre-slotted bridge pieces and extra holes in the bridge plate giving the option of either standard stringing or through-body stringing" As far as I can tell the dimensions are the same as for th Badass II and you may have the same potential problem with the action (which can be fairly easily rectified by shimming the neck). -
It could be glued in, or it might just be a tight fit. First protect the fretboard and neck around the nut with cardboard and masking tape. I would then suggest cutting down around the front and back edges with a razor blade (to ensure that it is detached from the fretboard) and then tapping lightly from the sides with a suitably sized wood block to push it out sideways. Some people suggest using a heat gun to heat and melt any glue. This might help if you have one. If it's really stuck you can cut the nut sideways across the direction of the fretboard until you almost reach the bottom, then collapse the nut in on itself. Check this link [url="http://www.stewmac.com/freeinfo/A-NUTS.html"]Stewmac.com[/url]
-
I have a real soft spot for 70's Japanese guitars/basses (although preferrably the better ones). That's what was widley available when I first got interested in playing so it must stem from that. I started off on guitar with a "Sumbro" (imported by Summerfield Brothers) then a "CSL" before treating myself to a late 70s Fender that was probably no better than the CSL. I can recall the Cimar brand, among many others, and that looks like a nice example. That surely is a DiMarzio P-Bass pickup with the adjustable hex-key polepieces and the cream coloured pickup covers ? Nice find.
-
[quote name='Buzz' post='111575' date='Dec 31 2007, 05:41 PM']Could you not just go shopping at your nearest PC outlet, buy a quiet fan and replace it? I am assuming here that it's a bog standard 12v fan, and of standard 60, 80, 120mm sizes.[/quote] In an ideal world, yes, you'd be right. However, there's no guarantee that the Hartke fan is "off the shelf". You'd need to check the obvious voltage and physical dimensions. Also important is the capacity of the fan (i.e. how much air it can shift per minute). You need to be sure that any replacement fan is powerful enough to do teh same job as the original.
-
I play a 5-string version of the one in your first photo. I've found the construction and feel to be excellent and the hardware all seems to be of a very reasonable quality. They used to use EMG Hz pickups and preamps but the more recent models don't seem to advertise this (although I wouldn't be at all surprised if they pups they use turned out to be the same minus the EMG badge). It won't sound like a P-bass or J-bass (the construction and electrics are too different) but if you try it out and like the sound then go for it. Some models have a relatively narrow width fretboard (which I like) so check you're comfortable with this first.
-
Have you tried wearing different shoes ? Some materials are better electrical insulators than others and will prevent static from leaking away to the floor noiselessly. Also man-made "fleece" fabrics will tend to generate static more than other materials so if you wear these a lot then they might be the source of the problem (much better to wear a brown 70's "Bri-Nylon" shirt ) I've had occasional problems with static shocks when getting out of cars - usually only happens when I'm wearing a paricular pair of shoes !
-
[quote name='MB1' post='105503' date='Dec 17 2007, 07:14 PM']MB1. Does this mean due to a change in management Badass could become Goodass? [/quote] Or maybe they'll make an extra chunky heavy duty one and call it "PhatAss" ? They're missing all these commercial opportunities here.
-
All good advice above. For screwdrivers make sure you have several different cross-head sizes and choose one that fits the screws best without slipping. If it's an old Fender then it will not have "Pozidriv" screws as these are a more modern invention. The older "Philips" screwdriver size will probably fit better. As long as the driver doesn't slip and damage the screws it doesn't really matter. Make sure you have a small box to keep all screws so that you don't lose any. Put a nice soft towel or something on the work surface first to protect the finish. If you're worried about the finish then protect it with cloth/towel/cardboard or anything around the screws as you work.
-
Bear in mind the two options will have different potential effects (although how audible the difference will be is open to question). With the bass plugged into the compressor and then into the amp the compression is occurring BEFORE the preamp stage of the amp. The peramp is processing a compressed signal. The compressor might be set to avoid any possible peaks reaching the preamp. With the compressor in the FX loop it's working on the signal from the preamp before it is sent to the power amp. If the FX loop is "post-EQ" then the signal received by the compressor comes after all the EQ on your amp. It's a different effect. No right or wrong here - just different.
-
Not sure if I can help here but I'll give it a try. Firstly I'm assuming you've got a good wiring diagram. There's one [url="http://www.aguilaramp.com/pdf/support_wiring_obp3.pdf"]here[/url] if you don't. The OBP-3 is quite tricky to wire up as there are so many wires involved. Also, when I did mine, at least one of the wires was a different colour to that suggested in the diagram. Process of elimination eventually sorted that out. Yes all of the earths go to the barrel of the jack socket. That's the part that protrudes out of the jack socket - the shell (sleeve) of the socket if you like. There should be two sprung contacts inside the socket. One (the ring) takes the black wire from the battery connector and the other (the tip) takes a green wire from the preamp. I found I couldn't physically connect all of the earths to that point so I soldered a metal washer onto a short piece of wire, connected the end of the wire to the earth point of the socket, then connected all the earths to the washer. Then - very importantly, wrapped insulating tape around the finished washer so that no bare wires could touch anything else. Note that the earths from the pickups should also come to this earthing point - they're not shown on the wiring diagram. Check and double-check the wiring of the blend pot. The "hot" wires from the pickups connect one each to the centre pins of the blend pot. Then there are two short "jumper wires" connecting the diagonally opposite pins from each layer in the pot. Finally, one wire goes to the master volume pot. The pots are shown from the rear in the diagram (the shafts pointing away from you). Make sure there are no short "whiskers" of wire touching anything they shouldn't as this would short out the circuit and change its behaviour. If you can see nothing wrong, try sending an email to Aguilar and describe the problem. They might be able to help. As for the bridge. Hold the old bridge above the new one so that the mounting holes line up. Does the back edge of the new bridge fall roughly in the same place as the old one ? Have the bridge pieces got the same amount of travel ? If they don't then it might be necessary to remount the bridge using different holes. Hope this helps.
-
If there's definitle no screw holding them on then they could just be very tight. Protect the body with some thick card (maybe make a bit of card with a hole cut out and pout this over the pot). Then get two flat bladed screwdrivers and place them opposite each other under the knob. Now gently and evenly lever off the knob by twisting the screwdrivers, always making sure the body is protected by the card. Once the knobs are off you should see a nut the holds the pot against the body. Tighten this up to stop the pots from moving around then put the knobs back on.
-
Can't help feeling that this thread would not look out of place on a medical self-help forum...
-
Are they push-fit knobs or do they have a small grub screw to keep them on (this would be a samll screw inset at the side of the knob). If there's a grub screw then you'd have to undo the screw enough to get the knonb on then tigthen it up afterwards.
-
Yes that should work ok. Just make sure you turn evrything DOWN (epsecially the volume on the Tascam) before you attach it and then bring up the volume gradually. If anything distorts then turn it down. I think the Tascam has a setting for Mono sound so that would resolve the stereo/mono problem.