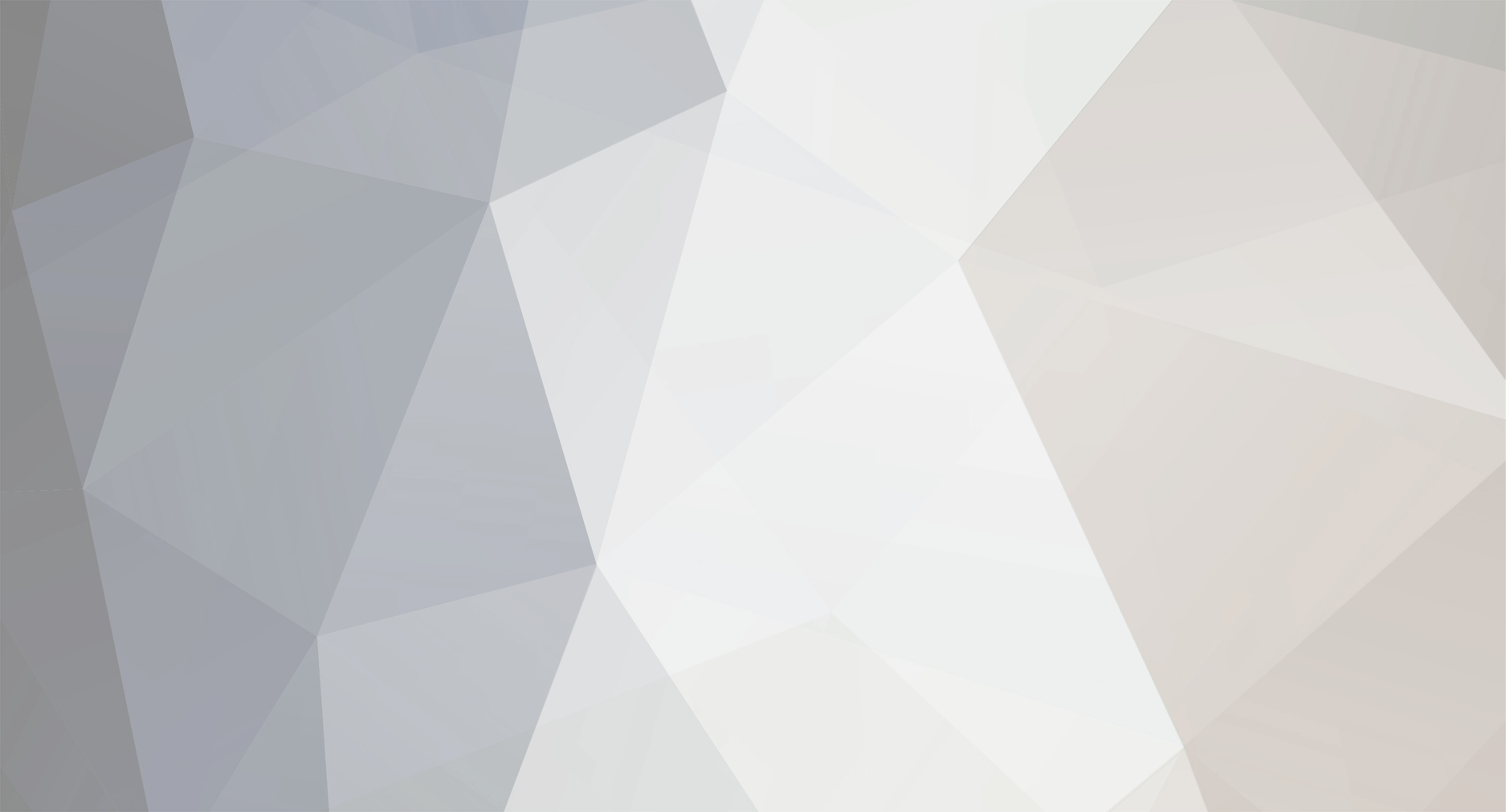
fonzoooroo
Member-
Posts
156 -
Joined
-
Last visited
Content Type
Profiles
Forums
Events
Shop
Articles
Everything posted by fonzoooroo
-
press next to it with reasonable pressure using your thumb. if the 2 sides of the crack move relative to each other, it needs gluing, and a couple of studs fitting inside. it'll cost a bit to get done (less than £50 though - the cost is the bench time while the glue goes off - the job's only a 10 minuter!) if this is the case, get a local quote, add that to the £50 (for the unsightly blemish on your new bass) and push the supplier for that. the repair mentioned will repair and stablilise - it'll be good for 100s of years! if there's no movement, there's nothing to worry about. take the 50 quid.
-
Bright ideas for removing stuff from inside a DB?
fonzoooroo replied to Clarky's topic in EUB and Double Bass
The download-free version... Lie the bass on it's back. Shake until the stuff is clearly visible opposite an f hole (bass side, preferably - avoids the possibility of knocking the soundpost. Fashion an extension for the crevice tool of your vaccuum cleaner (rolled paper, kitchen towel roll etc) Gaffer (or similar) it to the afore-mentioned crevice tool. Attach to 'cleaner hose. Apply suction. -
Welcome to the minefield! Fom my experience: Strings and technique dictate action height. Players using a soft string (weedwhackers/guts) use a very high action to get" underneath" as you describe... but if you go for a higher tension string, you won't be able to slap on a very high action. I currently have 2 electric uprights, one with spirocores (for the mag pickup) and a very low action (gives a psychobilly sound, for want of a better description! - perfect with a loud band though.), the other with some sort of innovation nylon cores on (peizo pickup - much more "natural" sound) ... Both have 4/4 strings on a 3/4 scale length and a correspondingly higher action for the one with nyons (even then, it's only regular "classical" action though!) and I play slap on both. I'd assume you're after more of a "thwack" slap sound rather than a "click" ? if so, that's going to be gut strings/whackers or nylon core (possibly bumped or solo set de-tuned) and a high action. There's lots of chat/reviews/rants on here about amps... have a read of those, and you'll quickly get a shortlist together! ...It all comes down to power (how loud your drummer is) in the end though! A customer of mine just bought a 700W GK beast for his DB and is very happy. ... I run a ridiculous mixer/POD XT/Behringer shark (just to pre-amp the clicky) /PA power amp/big peavey 2x12" PA cab... but that's far from normal! I'd offer lutherie, but I'm a bit of a hack down the country for you!
-
I run a full rack one (a Samson since you ask) on my bass rig, that way, you can see what you're doing on the meters - I run one channel compressing, and the other limiting, overkill, perhaps, but it suits me! I wouldn't recommend the Samson though... I've got a Alesis 3630 and a Behringer Composer Pro in the "studio" rack, and both seem better! (the Samson has had a few random issues that turning each pot up/back down seems to "fix" ... but doesn't inspire musch confidence long-term!)
-
Which corner of Derbyshire are you in? I've got a "power bank" (5 9V outputs overall max 450mA, on/off switch, and i've put a IEC socket on the mains lead so it plugs in on a kettle lead) I don't use you can have for a tenner in Coalville (or Woodville) PM if you're interested.
-
the vibration of the instrument could be making the screw "run" if the threads are cut slack. Threadlock will fix this. It wouldn't be the 1st newish mex fender i've seen with stripped screws in the bridge though. If so, it's either an engineering job (drilling/tapping the saddles a larger thread and replacing the grub screws to suit) or new saddles.
-
Glueing down a lifting bridge on an acoustic
fonzoooroo replied to Marky L's topic in Repairs and Technical
A lot of them have the bridge glued to the varnish... So wood glue's no good. I've done a few that've come off completely with 2 ton epoxy. I've never had a complaint. -
Knurled Saddles? Whats so great about them?
fonzoooroo replied to son of frog's topic in Repairs and Technical
[quote name='Johnston' post='1161442' date='Mar 14 2011, 09:53 AM']they look to me like a bit of threaded bar. Tap and die set and make your own [/quote] yep - a bit of stainless studding, saw to length, some awkward cross drilling, tap the cross drillings and off you go. Knurling is a different animal altogether - it's the process of cutting a pattern by imprinting it under pressure. (part to be knurled is rotated, and the knurling tool is pressed up against it.) That's how the control knobs are done. -
Looking for a pair of monitor headphones
fonzoooroo replied to Mornats's topic in Accessories and Misc
For that sort of money, you're in the realms of Beyer DT100s... (or the variations thereof) perhaps not the most inspired choice, but a studio standard for a reason! (and you can get all the parts!) -
Fingerboards: Ebony is better. Agreed. However, an "ebonised" board can be fine, as long as the chosen hardwood isn't[i] too [/i]soft. Have a look at the fingerboard under the strings in 1st position and check for wear. If it's a '60s bass, it's had a fair bit of use, so as long as there isn't a massive amount of wear, (like it needs a re-shoot in the nextyear or 2) it'll be fine. I've re-shot lots of "ebonised" fingerboards, and the only snag is that it costs the customer a little more, as it needs re-finishing afterwards. If it looks generally OK, go for it. You'll have to excuse me saying this, but: I'm aware that for [i]you[/i], it's a lot of money, but... for a double bass, it isn't.... so you can't go too far wrong. Especially from a decent retailer.
-
[quote name='Bilbo' post='1161509' date='Mar 14 2011, 10:44 AM']And you can get an extension thingy for a double bass that takes it down to C and octave lower. [url="http://en.wikipedia.org/wiki/File%3a%44ouble_bass_C_extension.jpg"]C Extension - picture[/url][/quote] indeed you can. I think we've all skirted round the big fact here... The cello is a member of the violin family. (period in history, shape of upper bouts and tuning in 5ths) The double bass is effectively still a viol which stayed in use in a standardised (much more recently) version of its original form. (presumably due to ease of playing - imagine the stretch required in the left hand if it were tuned in 5ths!) A bass viol is cello sized, (give or take) - certainly cello pitch. Hence double bass sounds an octave lower than a bass viol. To get an octave lower than that just gets silly... [url="http://wn.com/octobass"]http://wn.com/octobass[/url]
-
[quote name='Blademan_98' post='1146352' date='Mar 1 2011, 08:21 PM']Does that mean an electric bass is more akin to a cello? (Serious question) Cheers.[/quote] They're same pitch as double bass. Bottom string on a cello is C wchih is C on the A string of a bass. (double bass or bass guitar)
-
There's quite a lot of factors involved in a proper setup (as mentioned) but If there's nothing wrong with (for example) the fingerboard, (or it's in shouting distance on a cheapie!) the luthier'll leave it alone - hence you won't get charged for it. If they re-use your existing bridge, you're only paying for an hour or so of labour to sort it. New bridges are dear though! Nut adjustment takes minutes. If the bass is ply, the soundpost adjustment won't make anything like the difference that it will on a good carved bass - as long as it's in (about) the right place at a reasonable tension, it's fine. Upshot is that if that £150 includes fingerbaord re-shoot, bridge re-cut, nut re-cut and soundpost adjustment, you may find the bill's lower than that. In practice, I never charge that sort of money on a cheapie bass. (I do on a good bass, as it simly takes longer) What forces the cost up on a cheapie is a stained hardwood fingerboard, as it needs re-finishing afterwards!
-
You won't notice the difference in tension - less than 2%. I've got an EUB with a 101 scale length and 4/4 nylon cores on, and even that doesn't feel particularly slack!
-
[quote name='Bill Fitzmaurice' post='1159350' date='Mar 12 2011, 02:42 PM']though he had no idea what a rear loaded folded horn actually looked like or how they worked.[/quote] Excellent. Thanks for that reply - It's cleared a lot up!
-
I assume taking the average WxH dimensions x overall length for the port dimensions?
-
[quote name='alexclaber' post='1159120' date='Mar 12 2011, 11:27 AM']That's a ported cab - funny shaped port but nevertheless it is. Use a sine wave generator to find the tuning frequency, calculate the internal volume, then you know where to go with drivers. It'll need a lot of bracing to handle high power drivers, it needs lining with damping throughout and it's not going to be terribly robust because of the chipboard...[/quote] I'll look into it...
-
[quote name='Mr. Foxen' post='1159102' date='Mar 12 2011, 11:14 AM']Also appears to be made of chipboard, which kind of makes it not especially worthy of driver investment, if the current one works.[/quote] Well that all depends on what driver, and what cost... Obviously, I'm not keen to whack a £150 driver in, but the cab is convenient, was REALLY cheap etc, so Icould justify chucking a bit of money at it...
-
Yes, "Folded horn" seemes the best way to describe it with no research... I've only ever mucked about with sealed and ported cabs before...
-
pic: dimensions: overall internal height: (incl. horn mouth)570mm overall internal width: 570mm overall internal depth: (measured from inside face of baffle) 300mm horn mouth: 570x150mm horn throat (correct term?) 570x40mm the driver: inside:
-
[quote name='ficelles' post='1157495' date='Mar 11 2011, 12:06 AM']with an expanding bolt holding the pickup paddles against the inside of the bridge legs -[/quote] If that's effectively a spreader clamp between the bridge legs, it's not the best idea tonally... especially if you add flat caces to butt up to the bridge legs. If you want to use any of the pickups that wedge under the wings of the bridge, you'd be better modifying the wing shape of the bridge. (which'll make much less impact on the acoustic sound)
-
I was asked to record a friends band
fonzoooroo replied to Blademan_98's topic in General Discussion
If the playing's poor, they need to know so they can sort it. Time pressures/stresses/unfamiliarity etc when recording can mean that players often mess up stuff they can play live easily. If the sound was off, that's your responsibility, but the musicianship's theirs. I'd let them hear it after you've put in the least work you can (properly rough/basic mix) If they want you to "Do the best you can with it" after hearing what it's like now, then that's what you should do, but otherwise, I'd organise another recording session! The last recording we did was 5 tracks in 1 evening (after work) in the upstairs room of a local pub. By the time the gear was all set up, we'd all had enough (tiredness - not ale), so the playing wasn't perfect... We just quickly listened back, and re-did any tracks (all live takes) that were ropey. The technical sound was hard work due to all the spill in the mics, but we ended up with well enough played takes for the purpose. As above - "no problem, and no harm done" -
I recenty got hold of a "COMPACT Sound MKII" 1x15" folded horn cab. It's labelled as 100W at 8 ohms. The logic was simple: At £12.50 I couldn't go wrong! I checked it worked. After an hour with the kitchen cleaner, rags, superglue and finally boot polish, it looked presentable. I then whipped the driver out, replaced the world's thinnest speaker cable with some that has copper in(!) and that's it. The size of the cab is fantastic. nice and easy to load into cars for practices etc... and it'll take HUGE power. (I'm running a bass POD/1000W InterM Power amp setup)... I've (just to try it - wouldn't fancy it long term!) run the amp bridged and kept turning it up - No distortion right up to the "clip" lights... So it's perfect? ... Well...... No... My gigging cab is a Peavey Hisys 3 (2x12" with mid and horn) with Eminence Delta 12 LFs (with port tuned to compensate) replacing the black widows (which were dead when I got it) and the smooth, effortless bottom end is fantastic... There's just loads of smooth, clean bass. (at the expense of efficiency, I might add... but that's OK!) I'd love to get more of this characteristic out of the little 15". Now, I know the folded horn 15" can't compete with this in the treble range, but I can't help but think that a modern driver with a stiffer cone would help get more bottom end out of it. (the outer suspension is barely softer than the cone itself - in fact I guess the cone's actually bending pretty significantly when it's playing) and hence get a lot closer to the sound of the Hisys. What do you think? Pics and dimensions to follow...
-
[quote name='ficelles' post='1151238' date='Mar 6 2011, 10:32 AM']Btw can anyone recommend a pickup system that fits a Bausch bridge? ficelles[/quote] There's a pickup that sits on top of the bridge, between the outermost pairs of strings. I've seen one in a catalogue, but have no experience of them... Snag is, I'm not sure what they are... My gut reaction was a Shadow... But I wouldn't swear to it! Do I get the "Most useless reply of the week" award for that?!?
-
D'addario half rounds don't have silk. Admittedly, they're not flat either, but I use them on a couple of fretlesses without issues. Just a thought.