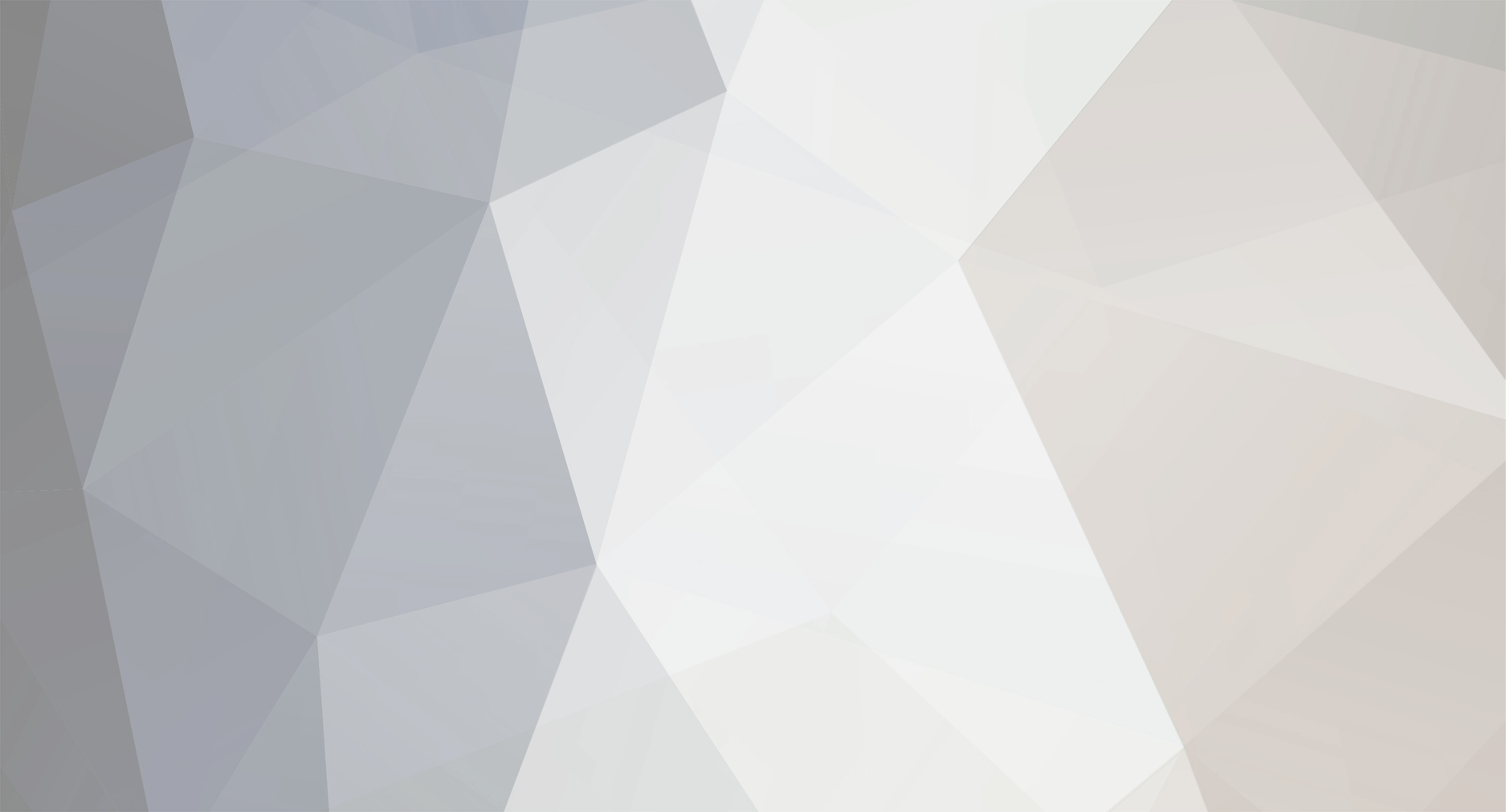
fonzoooroo
Member-
Posts
156 -
Joined
-
Last visited
Content Type
Profiles
Forums
Events
Shop
Articles
Everything posted by fonzoooroo
-
Short, practical answer about the styrofoam cases: No. Longer answer: Perhaps they're ok for home/car or van/gig, but nothing more...(the kind of thing where you could get away with a bag, but would rather something thicker just in case!) The foam'd have to be much thicker to withstand any significant impact/bending load. A friend of mine received a styrofoam violin case (new) which was flown in a single wrap of bubble wrap from Belgium. Something had clearly been put down/landed on it, and it was caved in. Luckily, that was just an empty case, but if it had contained an instrument, it wouldn't have looked too healthy! A few years ago, when the styro cases were just getting popular for cello, a shop I was doing some work for had a load of them in. The fittings (hinges and catches) were attached using 1/2" screws into the foam. They were tumbling apart on the shop floor! Of course, they may be better now...
-
A lot of old ply basses have painted fingerboards. (not translucent, thick, often nastily applied - often with runs!) that wears/chips and generally feels nasty. When I get these in to work on, I tend to scrape them back to bare wood and oil the 'board. A close-up pic of the issue would help suggest the most appropriate course of action.
-
Arco sound: Silly question, but[i] why[/i] is the sound poor? Is it the acoustic sound that's poor, or just off the pickup? If it's an acoustic issue, are you getting good grip from the bow on the string? If not, what state is your bow hair in? What rosin are you using? Is it sticky enough for your strings/setup? That's where I'd look first... If the bow hair is old, the rosin often won't "take" on it, in which case, only a re-hair (or new bow) will fix it. If the issue is only with the sound from the pickup, don't worry, as you'll presumably be mic'd in the studio, meaning only the acoustic sound matters.
-
Now the funny thing here is that I've got a choice of cellos (Been playing since I was a kid, still got my old instruments, then I trained as a luthier, so have 2 that I've made too.) (all are used, so consider the deal "private" rather than "trade") I'm just not in a position to add cash, so it'd have to be a straight swap. Any of the cellos can be just the instrument, or an outfit... Pics available... just need to point the camera at them... which I will if there's any interest! As you'll gather from the various values of the cellos, I'm not picky about the bass - could be ply or solid, old or new, playing or damaged. Try me. Only thing I'll say is that it needs to be 3/4 or 4/4. I want it to play, (I have a couple of EUBs, but now I've finally got a music room and an estate car, I've got the space to have a "proper" bass!) not as a commercial deal. So... The cellos: 1: I've got a 3/4 laminate effort. Playing, but unremarkable. Can come with hard case. Cello worth approx £150. Good, solid instrument for beginner. (got me up to grade 5) 2: 4/4 solid wood. Korean made, with French label (Debourde) made 1990 or 1992 - can't remember which without looking! Took me up to grade 8. Nicely set up with good action and Dominants. Value approx £500. Can come in practically new Hiscox wheeled hard case (worth £200 as it stands... Much dearer new) 3: 4/4 Strad pattern. One I've made, and got little use out of, as I mainly play on my 5 string... BIG sound. Larsen/D'addario/Supersensitive strings. Proper "advanced" cello. Amber varnish. Value approx £3000. As above, can come in the wheeled Hiscox. 4: 4/4 modified Strad pattern 5 string. (CGDAE) This is the instrument I'd happily NEVER sell.... It's my "daily" cello. One I made, even designed and carved the tailpiece myself from solid ebony. Not quite such a "big" sound as #3, but balanced, smooth, lovely to play. Properly designed as a 5 string - standard string spacing, standard peg spacing, beefed up bassbar and front. Amber varnish, showing a little wear round the edges. Always said I'd only sell to fund wood to build a 6 string! Value approx £5000. As above, can come in the wheeled Hiscox. Cheers. John.
-
Velcro can be used too. (sticky back) and the plate the pickups are mounted to could be a piece of aluminium sheet - that way it'll bend to the fingerboard contour and effectively allow you to adjust the pickup height by bending... Might save you a lot of sanding/planing bits of ply!
-
The problem is often that the screws are cast, so the "grip" and the threads are in 1 piece. In something like this, the plating is MUCH harder than the structural bit. (if you see what I mean) so when the plating begins to wear, it'll strip quickly. The collars are also often made of a "metal" that may as well be cheese. There are a couple of threads in use on "modern" insrtuments - M6 & M8. Some drum hardwear is also M8... so if yours happens to be M6, drilling and tapping M8 could give you potential for a screw upgrade. (did this very job myself this morning on a cello for a customer!) As for the size of the tapered plug; they're not standardised. The reamer to make the hole in the bass bigger is hugely expensive. Effective solution is to reduce the diameter of the endpin plug itself - spinning it in an electric drill/pillar drill whilst filing/sanding the taper face is the way to go. Just be sure to maintain the taper, and not go too far! ... If it's already too small when supplied, a wrap of paper/card is the usual solution unless it's massively too small.
-
[quote name='mart' post='1221972' date='May 6 2011, 09:58 AM']That sounds intriguing. Can you explain this leverage issue a bit more? Most of my basses have barrel sockets, so I'm very interested in anything that makes them work better.[/quote] Same with most sockets to be honest... The only types you should really be using a straight jack plug with are 1: strat style socket plates. 2: recessed sockets where you can't use a right angle plug. The issue is simply how far the plug sticks out of the socket before the cable emerges. Pull on the cable, and you're straining the socket. With a right angle plug, the height of the plug is reduced, hence the leverage is reduced. That's all.
-
If the socket itself is dodgy, replace it, and on the new one, pop a bit of threadlock on the retaining nuts. The tap washer isn't a bad idea. You could also run some thin superglue into the crack from the unpainted side. it'll soak in and help strengthen. The alternative is to go for an "open" type socket (stereo if you're staying active!) on one of this type of jack plate: [url="http://cgi.ebay.co.uk/OVAL-GUITAR-JACK-PLATE-SOCKET-GOLD-BLACK-CHROME-/190406419586"]http://cgi.ebay.co.uk/OVAL-GUITAR-JACK-PLA...E-/190406419586[/url] You'll need to have a good measure up first, and see how it'll sit before you start... The width of the "flat" face of the edge is often too thin for that type of plate on instruments that had a barrel as standard. The hole in the body'll need opening up quite a bit to get an open socket in too. So consider what drilling tools you have access to. Using a "flat bit" will result in disaster unless you fill the hole 1st. (piece of dowel could be the easiest.) The socket is a more reliable design though. Don't mind me saying this, but you do use rigt angle jack plugs? Yes? Failure of barrel sockets is often down to straight jacks and their huge leverage being used.
-
Cleaning double bass strings - advice needed
fonzoooroo replied to jbn4001's topic in EUB and Double Bass
meths is good too. any of the above ideas are fine as long as your fingerboard isn't stained with spirit based dye! If you only play pizz, you can use fret mate or similar. but avoid the bowing area if you use a bow. There are also dedicated string cleaners available (royal oak do one, and i'm prety sure there's a Hill one.) As for rosin, just don't let it build up. if you keep on top of it with a dry duster (removing as soon as it starts to build up) (if you use soft rosin, this could be every 1/2 hour of playing!) it'll never be a problem. Again, if you've a rosin build up on the strings/undyed fingerboard to clear, Meths is yur friend! -
[quote name='Mat Heighway' post='1210888' date='Apr 25 2011, 02:13 PM']This is an interesting answer, as I've never known of an endpin screw going at all. I suspect this is only the case with an all-wooden ferrule on the block. If your spike-hole has a metal collar then this shouldn't be an issue, as the screw binds into this rather than the wood. I've had a couple of basses with a simple bar as a spike and found that this is what causes the spike to slip into the instrument - a proper endpin should have reamed 'notches' in it to stop it slipping - if it has, then the screw shouldn't have to be done up tight anyway. My current bass had a 7mm diameter spike when I got it, and now has a 10mm Manson superspike. The screw hasn't slipped once. I suspect fonzoooroo was rather unlucky to have this happen. Incidentally, a properly nothced spike not only reduces the amount of work that the screw threads have to do, but also tends to eliminate any possibility of endpin-rattle.[/quote] In truth my comment was based more on cello experience than bass, but the design's the same. And you'd be surprised what horrible grades of metal, and poorly toleranced threads are out there on endpins! I've replaced a few for friends and customers over the years... +1 on the notched spike comment though. It reduces the need to excessively tighten the threads by putting the thumb screw into shear.
-
If you enlarge the hole to tae a larger diameter spike, you reduce the number of threads for the retaining screw to engage in. The screw threads are usually more of a weak pont than the spike - so I'd tend to leave well alone.... I'd tend to replace the spike with solid stainless steel bar.
-
You CAN afford a pickup - just perhaps not the one you ultimately hope for! A piezo transducer like this: [url="http://cgi.ebay.co.uk/5x-New-FT-20T-6A1-MINIATURE-UNCASED-PIEZO-TRANSDUCER-/250445825335?pt=UK_BOI_Electrical_Components_Supplies_ET&hash=item3a4fbc0537"]http://cgi.ebay.co.uk/5x-New-FT-20T-6A1-MI...=item3a4fbc0537[/url] (note that's a price for 5 of them!!!) can be used. ... just needs a bit of work to get it fitting quite tightly under the "wing" of the bridge, then (ideally) the shortest cable you can get away with before the preamp. Use a good quality cable to attach toe transducer to an inline type jack socket, attach that to the tailpiece (or tailgut with cable ties if you're feeling fancy) amd off you go... You can use a 2nd one in a similar way as a fingerboard pickup, then you MAY get away with wiring them together, or run them to either a stereo socket/cable and preamp seperately, or run 2 cables to the bass. You wouldn't be the 1st to do it like that! I'd get the playability sorted first, so you can sort the technique, and accept the acoustic volume that you get. If you're using a decent amp, you'll be surprised how good a sound you can get using the gear i've just outlined.
-
The sound of the slap is in the technique. Most modern "cheap" basses are supplied with steel strings. This is not necessarily a bad thing. (I play slap on steels - a lot of psychobilly players do, and those that want to use magnetic pickups) To slap on steels either requires fingers of iron, or a relatively low action. If the action is high, and you like the action high, the only option is to use softer strings (nylon core, "bumped" strings [using an A as an E, D as an A etc],guts or weedwhackers) Clarky is not alone: MANY players dislike whacker E&A strings. I'm a classically trained luthier, and can assure you there's a lot of knowledge involved in bridges/setup on basses. I often find that once the bridge is adjusted to height that the fingerboard then requires work. Whilst you [i]can[/i] DIY it, you're likely to get a much better result from a luthier who isn't doing their first bridge. Pickups: As you're aware, K&K rockabilly is one of the preferred few, though there are other ways depending on the sound you're after, and how loud you want to go.
-
Just did a swap of some pickups with him. Pleasure to deal with. What more can I say?!?
-
-
Clicky pickup: [url="http://cgi.ebay.co.uk/GT537-Acoustic-Guitar-Piezo-Transducer-Pickup-Kit-/300527402849?pt=UK_Guitar_Accessories&hash=item45f8d43f61"]http://cgi.ebay.co.uk/GT537-Acoustic-Guita...=item45f8d43f61[/url] They're self adhesive, but if you can apply pressure to them, the output increases MASSIVELY - so screw a plate down tightly over the top. Then either a bridge piezo or mag pickup, wire toa stereo socket on the bass, then split out to seperate preamps. I'm running exactly this setup with Gotoh P bass pickups on my EUB, and though I make no pretence about a natural DB sound, it's a sound I like, and it's certainly happy going LOUD! Just a thought.
-
It might be possible to steam your bridge flat. I've done a few for customers, and it lasts a while. Better to fit new though. If you know how high you want the action, there's little point in having adjusters (unless the action varies wildly with humidity - but that's less likely if it's a ply bass!) A £40 to £60 blank and a "budget" fit (all important bits done, but only quick trimming up) from a luthier's the way to go. I often turn that kind of bridge-fit round in 60-90 mins on a bass and charge accordingly. Endpin: If you can get hold of a suitable thumbscrew with a larger thread, and drill/tap accordinly, go for it. Budget endpins start at about a tenner, but unless you're VERY lucky with the shank size, it'll need fitting to the taper (either by machining the taper on the pin, or by the use of a DEAR reamer in the endblock of the bass.
-
Power supply. 9V 450mA 5 outlets. Supplied with leads shown - 3 original leads and a tangle with a few re-usable plugs (it's been sat about for a while and cannibalised!) The inlet is fitted with about 18" of cable and a male IEC so the 'board could plug in on a standard IEC cable. £10 collected from LE67
-
Sorted thanks. PLEASE DELETE
fonzoooroo replied to fonzoooroo's topic in Accessories & Other Musically Related Items For Sale
-
Sorted thanks. PLEASE DELETE
fonzoooroo replied to fonzoooroo's topic in Accessories & Other Musically Related Items For Sale
-
Title says it all really... I have a used schaller bassbucker I don't need: [url="http://schaller-electronic.com/hp38916/Bassbucker.htm"]http://schaller-electronic.com/hp38916/Bassbucker.htm[/url] which I want to swap for something decent to fit in a '51 style P bass.... or perhaps something to fit in a "normal" P... Anything considered. Try me!
-
SOLD please remove
fonzoooroo replied to fonzoooroo's topic in Accessories & Other Musically Related Items For Sale
-
Others have hinted, but is the problem that your bass is too good? A good bass is a good, big resonating box. Thin, low-density fronts, good bass bar shaping, correctly placed/tensioned soundposts, good bridge fitting etc. all help acoustic sound significantly... and the better that acoustic sound is, the more it'll feed back, as it'll pick up vibrations from the amp/band/stage. That's an excuse to go cheap bass hunting, get a real shocker, and fit steels with a mag pickup. block the soundholes, use the tricks above to damp the tailpiece and string afterlength... and if you still get trouble, fill the whole thing with expanding foam! Never tried this, but logical thought and all that: You might get some milage from some acoustic damping between you and the drummer, you and your amp etc... Raise the amp up, (again, isolated from the stage, so a layer of foam/gramma pad/whatever) and fire the speaker away from the body of the bass (or at least, not directly at the back of it - aim for a corner in the upper bouts if you're really stuck for space) and a few stands supporting vertical carpet/foam/whatever on each side of you. Don't point a monitor directly at it either - again, aim at a corner, or could you even use a small speaker high up, rather than a conventional wedge? Another place that the vibration can get back "in" is through the endpin. A good layer of soft stuff underneath will help disconnect the bass from the stage. (A "wolf" ball or similar on the end of the pin, and foam with a piece of board glued to the top) Finally, once you've got it basically tamed acoustically, what about running a dedicated feedback eliminator in the FX loop of your amp? I use a little Behringer Shark to preamp the clicky on my EUBs, and tend to go for a high pitched click sound - that can feed back if I'm close up to a loud amp, and the Shark catches it.
-
SOLD please remove
fonzoooroo posted a topic in Accessories & Other Musically Related Items For Sale
Used condition. The inside's lovely - clean, fresh (no weird smells!) The outside's got a few scuffs/marks/tears, but nothing too bad. It'll look better than it does in the pics for the buyer, as I'll stick the tolex down where it's damaged and give it a clean. Got to be a bargain for £20 collected from LE67