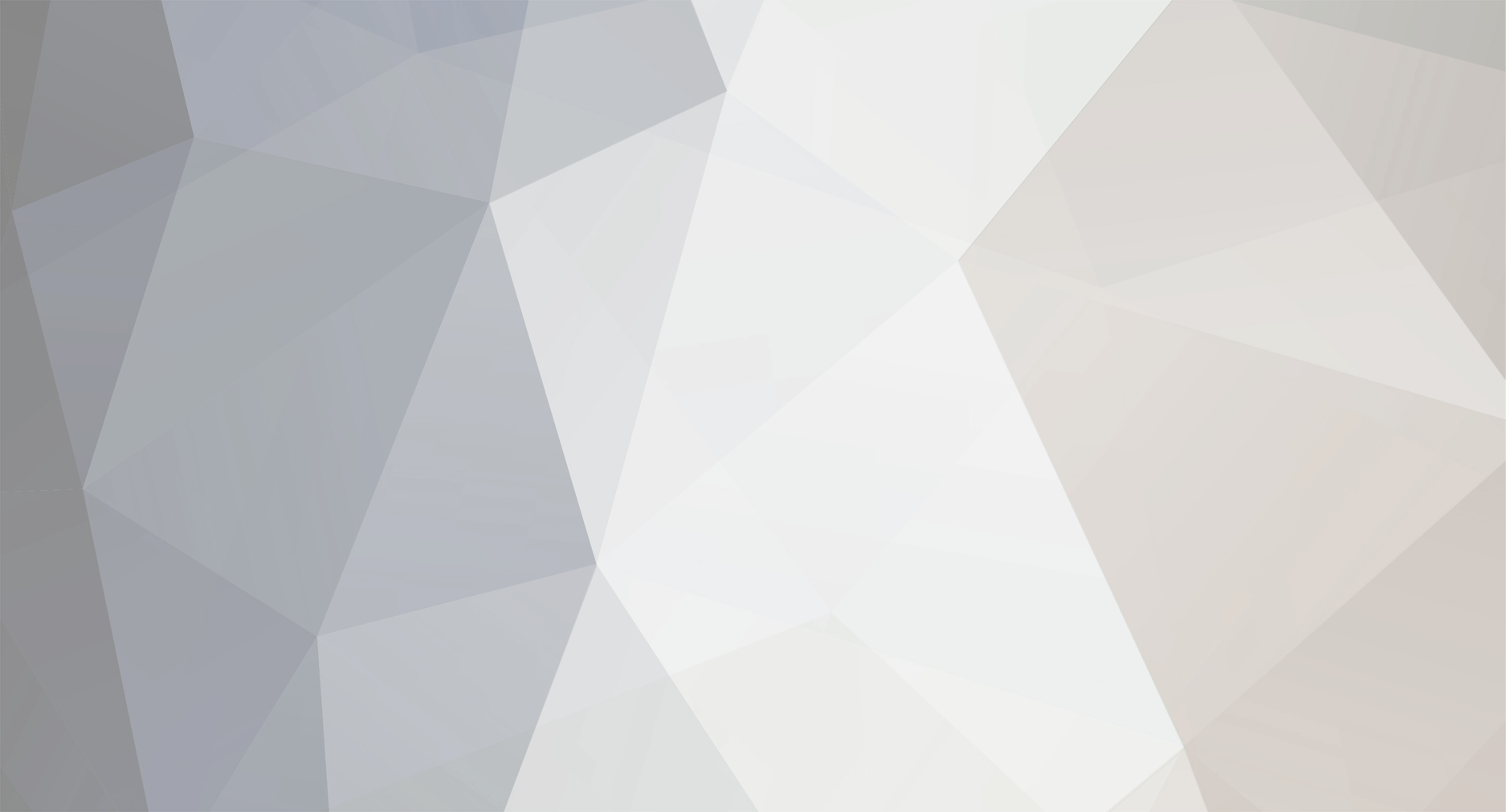
honza992
Member-
Posts
520 -
Joined
-
Last visited
-
Days Won
2
Content Type
Profiles
Forums
Events
Shop
Articles
Everything posted by honza992
-
Nope, cant post images. Something's changed in the last 4 years. i used to just cut & paste the BBCode from ibb. Any pointers anyone? EDIT: ok, I've cut and pasted the photos themselves rather than the links, like I used to. Is that how it's done these days? I'm feeling old.....
-
Hi All It's been a while since I've posted anything here. We ended up moving to Italy in the middle of the first wave of COVID. We've been re-structuring a house and finally, 4 years later, I've got a workshop set up in the basement. Sooo..... I'm making a fully acoustic bass. I've been planning it for what seems like forever. The idea is to make an acoustic bass that is designed to be amplified. It's not designed for acoustic volume, for that the body needs to be much bigger. My thinking though is to make the top as flexible as possible, then amplify the movement of the top with a K&K piezo, stuck on the inside of the top, under the bridge. It's a 'flarchtop'....So the spruce top is pushed into a tight radius (15 foot) by the braces, it's not carved like a normal archtop would be. It will have an archtop style floating bridge and tailpiece. I strung it up for the first time yesterday and the top didn't immediately collapse. Which is a good thing..... I didn't take pictures along the way, never got round to it. It still needs sanding, and heel cap and a few other bits, but the end is definitely in sight. A couple of pics....
- 50 replies
-
- 22
-
-
Fender Custom Shop 2019 Precision Heavy Relic -SOLD
honza992 replied to Simonsbass's topic in Basses For Sale
-
-
SOLD, Duesenberg short scale star bass (trade status or AVRI P bass)
honza992 replied to roger's topic in Basses For Sale
-
SOLD! Fender Player Series Jazz bass - Black/Maple beauty!
honza992 replied to michele's topic in Basses For Sale
-
SOLD! Fender Player Series Jazz bass - Black/Maple beauty!
honza992 replied to michele's topic in Basses For Sale
-
Yes, smallest bottle is plenty. It's pointless buying more because it forms a skin and becomes unusable pretty quickly. I know some people recommend poking a small hole in the foil and storing it upside down, but my understanding is that tru oil hardens in contact with air, so I'd rather have guaranteed fresh oil every time.
-
I was hoping this one was going to be finished before our move to Italy. Unfortunately I got side tracked with a hundred other things. The neck is basically finished, and finished, and looks nice! I've also glued in the neck. I used West System Epoxy because it doesn't need a perfect joint. As my first set neck guitar I was happy enough with the joint, but better safe than sorry. Some builders (Bruce Johnson for example) always use epoxy and if it's good enough for him, it's certainly good enough for me. Here it is clamped... It seemed to glue really well. Feels competely solid and the alignment and elevation at the bridge is spot on. All in all I'm pleased. I started off doing a wipe on poly (Ronseal Hardglaze) for the body and the neck. The neck turned out nicely, the body less so. I think keeping the finish very thin like I did on the neck makes it a really nice finish, almost like oil. For the body though, the more layers I put on the less I liked it - it became more and more artificial feeling. So...(as I always seem to end up doing)....I sanded back to bare wood and my plan is to French Polish with shellac. However that will have to wait till we get to Italy because I have a flat and a workshop to pack up, and two weeks to do it in. TIme to get off my lazy derrière......
-
I think 38-40mm is my preferred thickness for a fender style body. It doesn't look weirdly thin, but is significantly thinner than a standard Fender body which can help with weight. The other limiting factor is what switches etc you want to use. That can limit how thin you can make the body. A solid mahogany P bass will come in pretty heavy though, even at 38mm. If you can weigh the block you have, I can give you a pretty accurate guess of what a final weight bass will be. I can usually get to within a couple of hundred grams!
-
I've got so much respect for Jon Shuker, he really does lovely work. And not a CNC in site. Old Skool craftsmanship.....
-
Fanned frets is on my list of challenges.....it looks like you've got the perpendicular fret at about 11 or 12? Can I ask how you decided to put it there?
-
Jig GAS!! Nice.......
-
Thanks for linking to that, I've never seen one like that before. If I ever get a table saw I shall definitely be making one. Simple and elegant. Without a table saw, the other option if you have two straightedges which are the same height is simply to tape those down onto the neck. Use a guided router bit to run along one of them, and the other is there just for support. Low tech, but routers naturally 'go left', so the guided bit pushes against the left hand straight edge. Perfect straight slots (as long as you remember only to rout pushing away from you, never pulling towards, otherwise the 'left' changes sides and you slot gets wider......) The perpendicular mini straight edge is just a 'stop'.....
-
Anyone heard from Jess Loureiro pickups recently?
honza992 replied to honza992's topic in Build Diaries
PayPal have just refunded my money. He didn't respond to them either. Obviously there may be personal reasons for all of this, but may be worth being cautious if considering a JL pickup. -
Where are you?
-
@Bassassin Is this Danish or Tru-oil? If Danish, exactly which one? If it is Danish Oil then I'm surprised you were able to get such an obvious build. Here's a mahogany tele with multiple coats of Liberon Superior Danish Oil. I found that after a few (may 5 or 6?) there was really no point in going much further, it wasn't building at all and it wasn't adding to the 'depth' of the finish, so I stopped. One problem is that most finishes give you little clue as to what is actually in them. Most of them that are called 'Oils', are in fact varnishes. Really all you can do is try out each individual finish on scrap to see whether it provides the finish you like. @Andyjr1515 uses a 'slurry sand' technique which is really designed to seep into the wood (albeit to only to a tiny extent), and harden the wood itself. The slurry sanding fills in the grain but there isn't much build of finish on surface of the wood itself. This gives a natural feeling finish. The 'oil' finishes which are in fact varnishes, or varnish-like, (like Tru Oil and the Danish Oil used by @Bassassin in the photo above) can be used for this type of minimalist finish, or they can built up to give layer of finish on the surface of the wood itself. Tru oil can be built up in this way to give a completely gloss finish, or as I've done in my Tele at the beginning of this thread I've gone half way. It's definitely building a layer of finish on top of the wood, but I haven't gone completely gloss. There was a builder called 'Quarter' who built lap steel guitars and used Tru oil to get a shiny finish that from the photos looks much like nitro. The nice thing about the slurry sand technique is that you use the same stuff to finish and grain fill. So no worries about compatability etc. @Andyjr1515 Can I ask why you've moved to DO for necks? Ronseal Hardglaze and the 'slurry sand' technique also works very well, and I think is probably my preferred choice for necks if you want a hard, satin finish. It doesn't feel like wood as it does build on the surface, but it's smooth and 'cool' to the the touch. Polyurethane is harder than oil finishes, as I understand. You do have to thin it with white spirit, and it maybe itsn't as instantly easy as tru oil....
-
@Christine I've taken your advice and invested in a Record Power whetstone, and I have to say it's something of a revelation. As is your suggestion of hand-held sharpening on a whetstone. No jigs, no hassle, takes 20 seconds.... The only issue I have is that at the moment I havent got the RP grinder set up properly. When I grind, it's not doing a it perpendicular to the chisel, if that makes sense. Here's a photo, you can see the surface it's grinding isn't straight........off the top of your head, what would you try adjusting? Not the easiest it see as it's only on a 3mm chisel, but I thnk you can see the ground surface isn't at 90 degrees to the side of the chisel.
-
The binidng is rocklite and the 'white' wood is whatever the standard veneer is that you buy by the metre - sycamore probably?
-
Ummm....who....me...??!?? It would be fair to say that I haven't yet found a finish that I like. If you want a satin or low gloss wipe-on finish to go over the top of natural wood, then I'd suggest Tru-oil or Liberon Finishing oil. Both are hard drying varnishes, rather than oils as such, the names are misleading. If you're happy with a matt finish then Danish Oil (which is an oil finish) is as easy as it gets. I have also used wipe on polyurethane (Ronseal Hardglaze thinned approx 50% with white spirit) for satin necks which is pretty good, but I haven't had much luck with it for a whole body in terms of getting it up to gloss. It's still a technique I'm working on. The one thing I would say is that the single most important part of finishing is not, in fact, finishing, but is grain fill. If you don't have a flat and even surface to begin with, then it doesn't matter what finish you apply, it's always going to be really really hard to get a flat and professional looking finish. I'm not sure any of that is any help? This guitar is going to have tru-oil on the neck (slurry sanded till smooth), and a french polished (ie shellac) body and headstock face. Or at least that's the plan at the moment. (Just remembered the easiest finish ever is Osmo polyx oil, which is an oil/wax finish. Wipe it on 3 times and you're done)
-
Volute anyone?
-
I guess that's part of designing and making guitars, pushing the boundaries to see how far you can go. I've made 3kg full scale basses, so given this is 31" and is using guitar tuners, I'm confident this will have zero neck dive. And should be sub 3kg.........
-
Just a bit more work on the fretboard. The epoxy and mixol worked fine, as it did last time....🥴 I had a couple of small tearouts with the fret slots, so rather have to dig out dried epoxy I used some 'dams' made from a cut up sheet of 0.5mm teflon. They're the perfect thickness for the fret slots, and teflon is one of the few things that expoxy doesn't stick to at all. Just stick 'PTFE teflon' into ebay and you can buy it by the small sheet. Then just radius sanding block to 400, then hand sanding to 2000..... Talking of sanding blocks, the quickest and best I've ever made was this one. Makes radius sanding much quicker and much less stress on the hands. It's just a plastic push block that came with a cheap set that I think came free with my planer. 2 bits of double sided onto the foam on the bottom, then stick it directly onto the back of the radius block and hey presto! cool, glow-in-the-dark custom handles...
-
That's great. It's occurred to me. On holiday in Italy last year we stayed in a place that had a massive 4 inch thick mahogany garden table. Enough for probably 10 bass bodies! Once we've moved to Italy, I may try and sneak it off under my jacket.....😎 Ha ha probably not the vehicle of choice for the Extinction Rebellion activist🤣🤣 But the reality is, what you drive makes no difference. What's important is that we recognize fundamental changes are needed in the way we all live our lives, then apply political pressure so that society-wide solutions are enacted. If we depend upon all of us willingly giving up our carbon-intensive lifestyles, then I don't believe there's any hope. There's just not enough time. Or at least that's what the United Nations and scientific community tell us.
-
Andy, any comments I make are those of a total amateur with no training in anything useful, like engineering or physics. But this is an really interesting build so thought I'd chip in.... First off most guitar necks are frankly over-engineered. I've put one of my (standard Fender size) necks betweens bricks and completely failed to break it despite jumping up and down. Not even close. No movement at all. And I agree with wood inserts. I always use them and they are absolutely rock solid. I also love the design, it's really ingenious, I shall almost certainly steal it in the future (with credit of course). But.....I just have a bit of an uneasy feeling about the neck wood that lies between the body/neck join and the 'ramp'. I can understand the logic to a biscuit, and I'm sure it's adds some strength, but I wonder whether it adds some risk as well. Once under string tension I think the biscuit is going to be pushing on the back of the ramp of the flush heel joint. And at that point the neck wood is probably 5mm thick (ie directly above the biscuit). Two thoughts. First, do you want to think about grain direction of that wood. Maple can be amazing stable until you apply force down grain lines, at which point it can split into wafers very happily. Second, would a neck plate that crossed the body/neck join provide more strength to the join, without leaving a weak point that I think the biscuit may introduce. Or maybe use both? Just thinking out loud.....