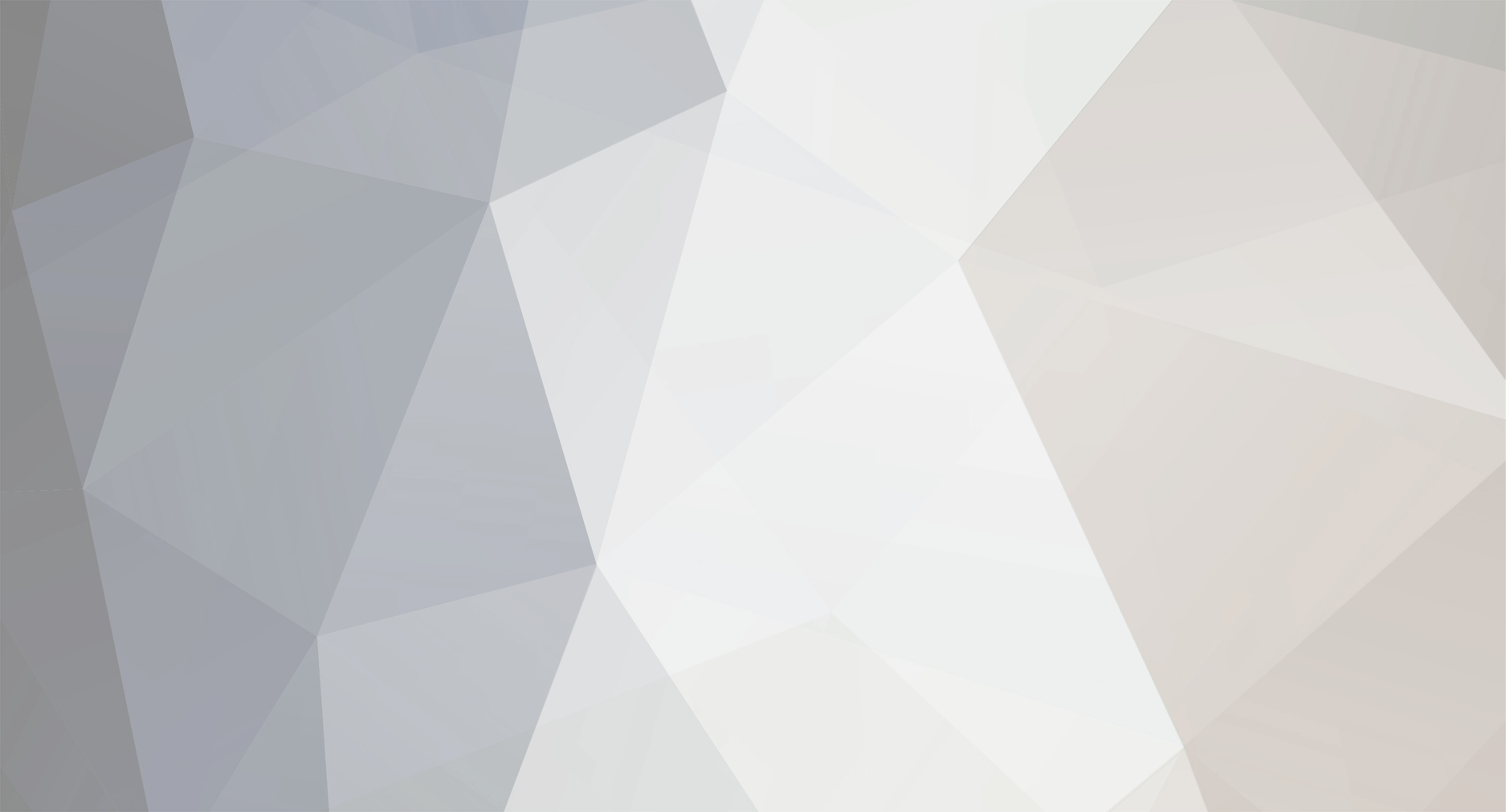
honza992
Member-
Posts
520 -
Joined
-
Last visited
-
Days Won
2
honza992 last won the day on February 24 2024
honza992 had the most liked content!
Recent Profile Visitors
The recent visitors block is disabled and is not being shown to other users.
honza992's Achievements
-
OK, last few bits and bobs with this one. Setup first. I like to be able to get the action pretty low. 1.75mm for the E string at the 12th and 1.5mm for G string. That's with only a touch of relief on the truss rod. I've stopped using nuts and instead have a zero fret. The fretwire is the same for the zero fret but I don't level it when I'm doing the other frets. All this means that the action is incredibly light. Particularly the first 5 frets. My daughter's guitar teacher (who's a far better bass player than me) came round the other day and said it felt like playing a fretless! That's definitely my goal. Most people probably will want to raise the action a bit, particularly since this is an acoustic, but it's nice to know it can go low if necessary. My setup routine is probably similar to everyone. The only thing slightly unusual is that I level the frets under string tension. First step is getting it to tension (or actually a semitone below), then using a straight edge on top of the frets to get the neck as straight and flat as possible: I then use an aluminium C-shaped beam with 400 grit sandpaper on the bottom to level all the frets (as mentioned above, apart from the zero fret). More or less the final job is the pickup. I'm using a fishman matrix Infinity piezo which is under the saddle. This means I need to drill a hole in the top for the cable. After countless hours of work this was definitely a job not to do with a hangover. Or given I've got an eight year old, high on gummy-bears. Mark up the bridge location with tape, then a 2.5mm through the top, praying that my plans are accurate and I'm not about to drill through the X brace..... Phew. Done. Tomorrow I'll string it up again and plug it in for the first time.... One thing that has turned out beautifully on this build is the finish on the top. It was an epoxy seal coat then 5 or 6 wipe on/wipe off coats of tru oil. As a finish it look stunning. The last one had a french polished top which was nice, but dare I say it this one is better. It's hard to see in my rubbish photos, but the wood glows....
- 142 replies
-
- 13
-
-
I'll do a proper write-up once it really is finished, but some initial thoughts are: - it looks amazing! At some point I'll get some proper photos done. My phone and workshop lighting do not make for a David Bailey experience.... - the geometry has mostly come out well. The metal bridge looks nice, but is sh_te. I may replace the string retainer with a handmade ebony thing. - The acoustic sound is very nice. It's slightly louder and much more complex than the last prototype I built. More overtones, more focussed, less 'flabby' sounding. - the traditionalists will crucify me, but I used Tru-oil for the spruce top and the walnut back. On the spruce top it looks completely amazing. Better than the french-polished shellac I used on the previous guitar. - The piezo pickup isn't installed yet. I'll do fret levelling, set-up and finish everything else before installing. I'll need to drill a hole in the top for the wire, so I want to make sure the bridge is in the right place first....
-
Finished! OK, it's not there's still fret levelling, etc etc, but here's a poor quality mobile phone pic...
- 142 replies
-
- 12
-
-
Oh and I also went to the wonderful Riwoods outside Milan to re-stock on walnut, maple and spruce. Can't think what for.....🙄
-
Thanks all. Things have slowed a bit because my daughter is off school for the summer holidays - all three (yes 3!!!) months of them. But, we're pretty much reaching the finish line. Literally. I started finishing the body yesterday with a seal coat of epoxy. Today I started the Tru-oil. The neck still needs a bit of tweaking before starting on the tru oil. I'll do a full finish write-up once it's done.
-
Although it's not finished, I've strung this one up to see whether the top was going to implode. It's been a couple of days, so I'm definitely pretty relieved. There's still quite a bit to do - the bridge is a temporary one, the nut is just a piece of scrap, the heel cap needs to be glued on, everything needs to be sanded properly, and of course it needs some finish applied. There's still set up and fret leveling and installing the pickup etc etc. However, I know you lot haven't been sleeping with the anticipation of it all, so here's a sneak low-res preview.
- 142 replies
-
- 12
-
-
Thanks @Mykesbass I'm well chuffed with that!
-
Once the facets were done I then used a spokeshave, and sanding blocks to get the length of the neck more or less to its final shape. Today I started on the transition. I find it easier that way, taking the transition down to the neck, rather than doing the transition first. I can see the curves better for some reason. Here's the development of the headstock transition. I also made a quick start on the heel transition. Here it is unstarted..... One of the last jobs to do on the neck is drilling the holes for the tuners. (I'm pretty pleased with the walnut veneer on the back of the headstock 😁)
-
It feels like cheating. I feel as though I should be doing it freestyle, with only my keen luthier's eye and maybe a beret..... For some reason I thought most builders just sort of went for it, rather than the slightly over-engineered process that I go through. Either way, it's really a great technique. Not fool-proof, but probably as close as you can get with neck carving.
-
OK I'll take a look. That enormous video is making me feel queasy....
-
Since you're all there, here's a few random photos. I realise I fretted without taking a single pic. So here's the all important preparation before fretting. I've learned the very very hard way to check every slot is deep enough before starting to fret. A bent over piece of fretwire with the tangs filed off is perfect. When I glued on the black/white veneer on to the bottom of the fretboard, some of the epoxy seeped through into the slots. Time to bring out the world's tiniest saw... Then side dots. With another of my fugly jigs. Honestly, there should be a law against it....
- 142 replies
-
- 10
-
-
Neck Carve! I always cheat when it comes to neck carving. I start by carving a series of facets onto the neck. These are carefully measured and calculated. Once they're done there's still quite a lot of wood to take off, but they give the neck it's final shape. Here are the first two facets: Here I'm starting on the next one. The tape is there to remind me where the line is I'm supposed to be carving to. You really don't want to get carried away and go to far beyond the line. It's veeeery late in the day to start a new neck. And on dark wood a pencil line can be darn hard to see. I end up with.....ummmm...is it 8 facets, something like that. I spend quite a long time getting these pretty flat and consistent. I think it reduces the amount of 'shoe-shine' sanding which is needed, which is the god-awful final stage.... So here we are: VID_20240607_121041~3.mp4 If I can over the weekend I'll make a start on the headstock transition. Edit: Hmm...that video is masssssive! Does anyone know how to make it smaller?
-
I stole it from Gore, so steal away!
-
Ah it's not. I've remembered there's more🤣
-
I think, I'm not sure, but I think this may be the last veneer of the build. So enjoy it.....