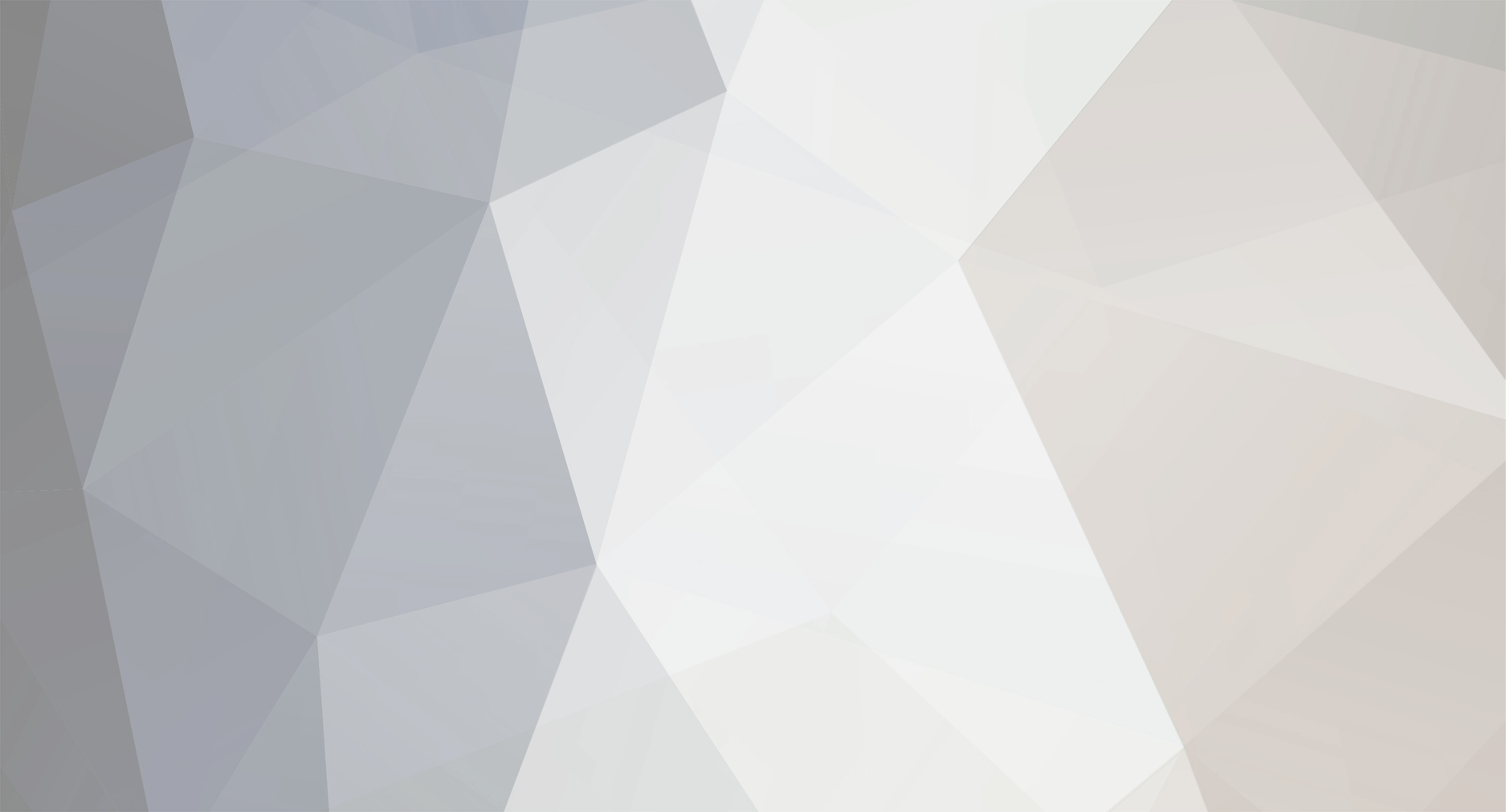
honza992
Member-
Posts
520 -
Joined
-
Last visited
-
Days Won
2
Content Type
Profiles
Forums
Events
Shop
Articles
Everything posted by honza992
-
OK, last few bits and bobs with this one. Setup first. I like to be able to get the action pretty low. 1.75mm for the E string at the 12th and 1.5mm for G string. That's with only a touch of relief on the truss rod. I've stopped using nuts and instead have a zero fret. The fretwire is the same for the zero fret but I don't level it when I'm doing the other frets. All this means that the action is incredibly light. Particularly the first 5 frets. My daughter's guitar teacher (who's a far better bass player than me) came round the other day and said it felt like playing a fretless! That's definitely my goal. Most people probably will want to raise the action a bit, particularly since this is an acoustic, but it's nice to know it can go low if necessary. My setup routine is probably similar to everyone. The only thing slightly unusual is that I level the frets under string tension. First step is getting it to tension (or actually a semitone below), then using a straight edge on top of the frets to get the neck as straight and flat as possible: I then use an aluminium C-shaped beam with 400 grit sandpaper on the bottom to level all the frets (as mentioned above, apart from the zero fret). More or less the final job is the pickup. I'm using a fishman matrix Infinity piezo which is under the saddle. This means I need to drill a hole in the top for the cable. After countless hours of work this was definitely a job not to do with a hangover. Or given I've got an eight year old, high on gummy-bears. Mark up the bridge location with tape, then a 2.5mm through the top, praying that my plans are accurate and I'm not about to drill through the X brace..... Phew. Done. Tomorrow I'll string it up again and plug it in for the first time.... One thing that has turned out beautifully on this build is the finish on the top. It was an epoxy seal coat then 5 or 6 wipe on/wipe off coats of tru oil. As a finish it look stunning. The last one had a french polished top which was nice, but dare I say it this one is better. It's hard to see in my rubbish photos, but the wood glows....
- 142 replies
-
- 13
-
-
I'll do a proper write-up once it really is finished, but some initial thoughts are: - it looks amazing! At some point I'll get some proper photos done. My phone and workshop lighting do not make for a David Bailey experience.... - the geometry has mostly come out well. The metal bridge looks nice, but is sh_te. I may replace the string retainer with a handmade ebony thing. - The acoustic sound is very nice. It's slightly louder and much more complex than the last prototype I built. More overtones, more focussed, less 'flabby' sounding. - the traditionalists will crucify me, but I used Tru-oil for the spruce top and the walnut back. On the spruce top it looks completely amazing. Better than the french-polished shellac I used on the previous guitar. - The piezo pickup isn't installed yet. I'll do fret levelling, set-up and finish everything else before installing. I'll need to drill a hole in the top for the wire, so I want to make sure the bridge is in the right place first....
-
Finished! OK, it's not there's still fret levelling, etc etc, but here's a poor quality mobile phone pic...
- 142 replies
-
- 12
-
-
Oh and I also went to the wonderful Riwoods outside Milan to re-stock on walnut, maple and spruce. Can't think what for.....🙄
-
Thanks all. Things have slowed a bit because my daughter is off school for the summer holidays - all three (yes 3!!!) months of them. But, we're pretty much reaching the finish line. Literally. I started finishing the body yesterday with a seal coat of epoxy. Today I started the Tru-oil. The neck still needs a bit of tweaking before starting on the tru oil. I'll do a full finish write-up once it's done.
-
Although it's not finished, I've strung this one up to see whether the top was going to implode. It's been a couple of days, so I'm definitely pretty relieved. There's still quite a bit to do - the bridge is a temporary one, the nut is just a piece of scrap, the heel cap needs to be glued on, everything needs to be sanded properly, and of course it needs some finish applied. There's still set up and fret leveling and installing the pickup etc etc. However, I know you lot haven't been sleeping with the anticipation of it all, so here's a sneak low-res preview.
- 142 replies
-
- 12
-
-
Thanks @Mykesbass I'm well chuffed with that!
-
Once the facets were done I then used a spokeshave, and sanding blocks to get the length of the neck more or less to its final shape. Today I started on the transition. I find it easier that way, taking the transition down to the neck, rather than doing the transition first. I can see the curves better for some reason. Here's the development of the headstock transition. I also made a quick start on the heel transition. Here it is unstarted..... One of the last jobs to do on the neck is drilling the holes for the tuners. (I'm pretty pleased with the walnut veneer on the back of the headstock 😁)
-
It feels like cheating. I feel as though I should be doing it freestyle, with only my keen luthier's eye and maybe a beret..... For some reason I thought most builders just sort of went for it, rather than the slightly over-engineered process that I go through. Either way, it's really a great technique. Not fool-proof, but probably as close as you can get with neck carving.
-
OK I'll take a look. That enormous video is making me feel queasy....
-
Since you're all there, here's a few random photos. I realise I fretted without taking a single pic. So here's the all important preparation before fretting. I've learned the very very hard way to check every slot is deep enough before starting to fret. A bent over piece of fretwire with the tangs filed off is perfect. When I glued on the black/white veneer on to the bottom of the fretboard, some of the epoxy seeped through into the slots. Time to bring out the world's tiniest saw... Then side dots. With another of my fugly jigs. Honestly, there should be a law against it....
- 142 replies
-
- 10
-
-
Neck Carve! I always cheat when it comes to neck carving. I start by carving a series of facets onto the neck. These are carefully measured and calculated. Once they're done there's still quite a lot of wood to take off, but they give the neck it's final shape. Here are the first two facets: Here I'm starting on the next one. The tape is there to remind me where the line is I'm supposed to be carving to. You really don't want to get carried away and go to far beyond the line. It's veeeery late in the day to start a new neck. And on dark wood a pencil line can be darn hard to see. I end up with.....ummmm...is it 8 facets, something like that. I spend quite a long time getting these pretty flat and consistent. I think it reduces the amount of 'shoe-shine' sanding which is needed, which is the god-awful final stage.... So here we are: VID_20240607_121041~3.mp4 If I can over the weekend I'll make a start on the headstock transition. Edit: Hmm...that video is masssssive! Does anyone know how to make it smaller?
-
I stole it from Gore, so steal away!
-
Ah it's not. I've remembered there's more🤣
-
I think, I'm not sure, but I think this may be the last veneer of the build. So enjoy it.....
-
Just to very quickly finish the neck joint description, I put a T nut onto the fretboard extension to hold it down. So a screw through the heel and bolt through the back. It's quite a lot to get all lined up and the neck pointing in the right direction. One of the biggest steps up from making electric to acoustics, is that with acoustics there's no flat surfaces. Everything is curved and nothing is in the same plane.
-
Thanks @Mykesbass The stripe continues through the nut and round the headstock😁
-
For the neck joint I will have a single screw holding the heel against the body, then the fret board extension will act a long horizontal tenon, held by a single bolt through the body. Sounds complicated, but isn't. It worked really well on the last build, it's completely stable and seems to be plenty strong enough. I rout the mortise for the fretboard extension/tenon in one go. A simple MDF jig with a locating strip of wood that slots into the truss rod channel. This makes sure everything lines up, and makes clamping a lot easier. I've already drilled the hole for the wood screw through the heel and into the neck block. Again, the screw helps with keep everything aligned while I rout. Here's the jig: Routing: Once the tongue/fretboard extension has been glue and sanded flat, it looks like this: The fretboard then goes on top. I haven't glued it at this point, still a few jobs to do first......
-
OK, the box is closed, so time to crack on with the neck. First up is working out the neck angle. I stick one of he sleeves of my spindle sander onto the guitar top at the position where the bridge will be. A straight edge and a digital level* gives the required neck angle as being 5.1 degrees. The sleeve is a bit higher than I need, so a quick bit of maths gives me a final neck angle of 4.2 degrees. Ne Next I glue up the heel block, with my usual excess of veneers.... Talking of veneers the other thing I've got to do is get a white and black line under the fretboard, so that they meet up with the lines underneath the headplate, like this: The fretboard is already radiused so it's not easy to clamp, so I need to use a vacuum bag. I use one of these skateboard vacuum bag things with a wine pump. I've used it a lot over the years and it is a brilliant bit of kit, perfect for guitars. And compared to a proper veneer pump and bag it's a bargain. Here's the fretboard in the bag, glued with epoxy. Next I need to cut the neck angle on to the end of the neck heel. This is a right old faff. Getting the Radial Arm Saw set up takes ages. I always do a test cut on a similar sized piece of scrap wood because you pretty much only get one chance. As you can see in the picture I ended up using a neck angle of 4.6 degrees, slightly different from my initial guess of 4.2. That's why I always do a test cut... Once that's cut, I've then got to fit the neck to the body. I'm happy that he angle is right, but I've also got to refine the left/right alignment. In other words the neck has got to be pointing exactly at the bridge. It doesn't. I stick the neck in the clamp, and rest the neck on the body. I put a thin strip of scrap wood into the trussrod channel so that it points down to where the bridge will be. I can see from that how I need to sand the base of the heel to get alignment. The sanding I do with a triangular strip of sandpaper, so it progressively sands one half of the heel. Hard to explain, but a picture may help: Rinse and repeat until the stick points straight down the middle of the guitar: (I know the top looks a mess. I put on a couple of layers of shellac just round the edge before binding. This helps pulling the binding tape off without getting tearout on the spruce top. It'll clean up nicely. I hope....)
-
Hi All Bit of a delay in posting. The front and back are now glued on and i've cut the binding channels. I forgot to take photos but I use a router and take many passes.... Next, a very simple end graft made out of two bits of binding stuck together. It's not glued yet, first is binding. There was then a slight delay as while I was cutting up some veneers for the binding I managed to slice my finger open. Turns out surgical scalpels are actually quite good at cutting humans..who'd have thought! A quick trip to A&E and a few sutures later, I'm fine. As usual, mistakes like that happen because I was hurrying. Sharp things and haste do not go together well. Being a numpty doesn't help of course. Anyway, the bindng channels I cut with a router, the side binding though is done by hand. First a gremel, then a chisel to clear out the channel. The binding gets bent on the iron the same as the sides. The binding layout I'm doing has got black/white inner lines that will be mitred to the lines of the back stripe. The most difficult part is here where they meet at the bottom: In the picture above it isn't glued. I'm trying to get those white and black inner lines to line up nicely so it looks like one continuous line. The black one is fine, but you can see that the white one still needs a bit more work. I glue everything together (bindng plus white and black veneers) all at the same time which is not the normal way of doing it. And next time I may well try doing the purfling lines first. The back is bound, so we'll see tomorrow how successful the mitres were. Edit - In case you're wondering, the two white strips on the left hand side are teflon. I slide them into the joint so that when I glue the binding on the right hand side it doesn't gum up the left hand channel. Dried titebond is difficult to get out of small gaps like that. Speaking of titebond I've gone back to using it for binding. For a while I used superglue, which seems easier because you can get everything completely ready and taped into place before wicking in water thin glue. What it doesn't do is soften the binding, so it's a quite unforgiving process. Because titebond is water based it seems to soften the binding allowing it to bend into the corners better. So for now I'm sticking (ooh nice pun) with Titebond (original). Though next time I may try fish glue which apparently has a longer open time. Binding can be pretty fiddly so being able to take it more slowly would be good....
-
Thanks Andy, I love your opptimsm🙂 Let's hope it's ......founded.
-
Don't forget this is an archtop with a tailpiece so most of the string tension is absorbed by the sides. It's only the downward forces which need to be resisted by the top (something like 15% of total string tension). A normal guitar has all the string tension pulling on the bridge itself which is glued to the top. The arching itself also provides strength. Having said that, I shall be sh_tting bricks when the time comes to string it up! My best guess is that it will be fine, but it's hard to know.
-
Today I finished the braces. There are huge differences in the heights of braces that other builders use. Benedetto goes from 12mm in the centre to 4mm at the sides. Ken Parker goes from 5.5mm (!!!!) in the middle to virtually nothing at the edges. I've decided to aim for 8mm in the middle, to 1.5mm at the ends. This is really significantly less than most acoustic bass guitars have. But it seems to me that for bass frequencies you need flexibility. I'm flexing it with my hands all through the process, trying to memorise how it feels so that during the next build I've got a comparison already in my muscle memory. Anway, here's my carving station: Here are the braces at their final heights. I found it really usefuly to write the heights every 30mm all along the braces. They ended up being 8mm (16mm for the flyover) in the centre, thinning to 1.3 & 1.6mm at the ends. It's pretty flexible. Will it withstand the downforces of the strings? Ummm.......not sure. Let's hope so! For this bass though, that's as far as I dare go. The top needs a bit of cleaning up, sanding etc but we're pretty much there. I'm excited!
-
In the short breaks between eating fresh pasta and drinking prosecco, I started on carving the brace(s). There only one glued on for the moment: My plan is to have one jump over the other, rather than an X-brace which is glued together. Having shaped the first brace into a sort of conical shape, the handle of an iwasaki file was the perfect shape for the corresponding hole in the other brace: So they fit together like this: Clearly, that second brace has still got some work that needs to be done. Just a tad oversized.... Those iwasaki file are the nuts by the way. Hands down the best files I've used. Much better than the Dragon files that Stewmac sells. They create shavings rather than dust and leave a ridiculously smooth surface. Even the handles are the perfect shape.
-
Yep, I realise it's entirely unjust. Nor deserved. I've led a terrible life being unkind to the young and infirm and listening to progressive rock. Just goes to show that there really is no justice in this world.