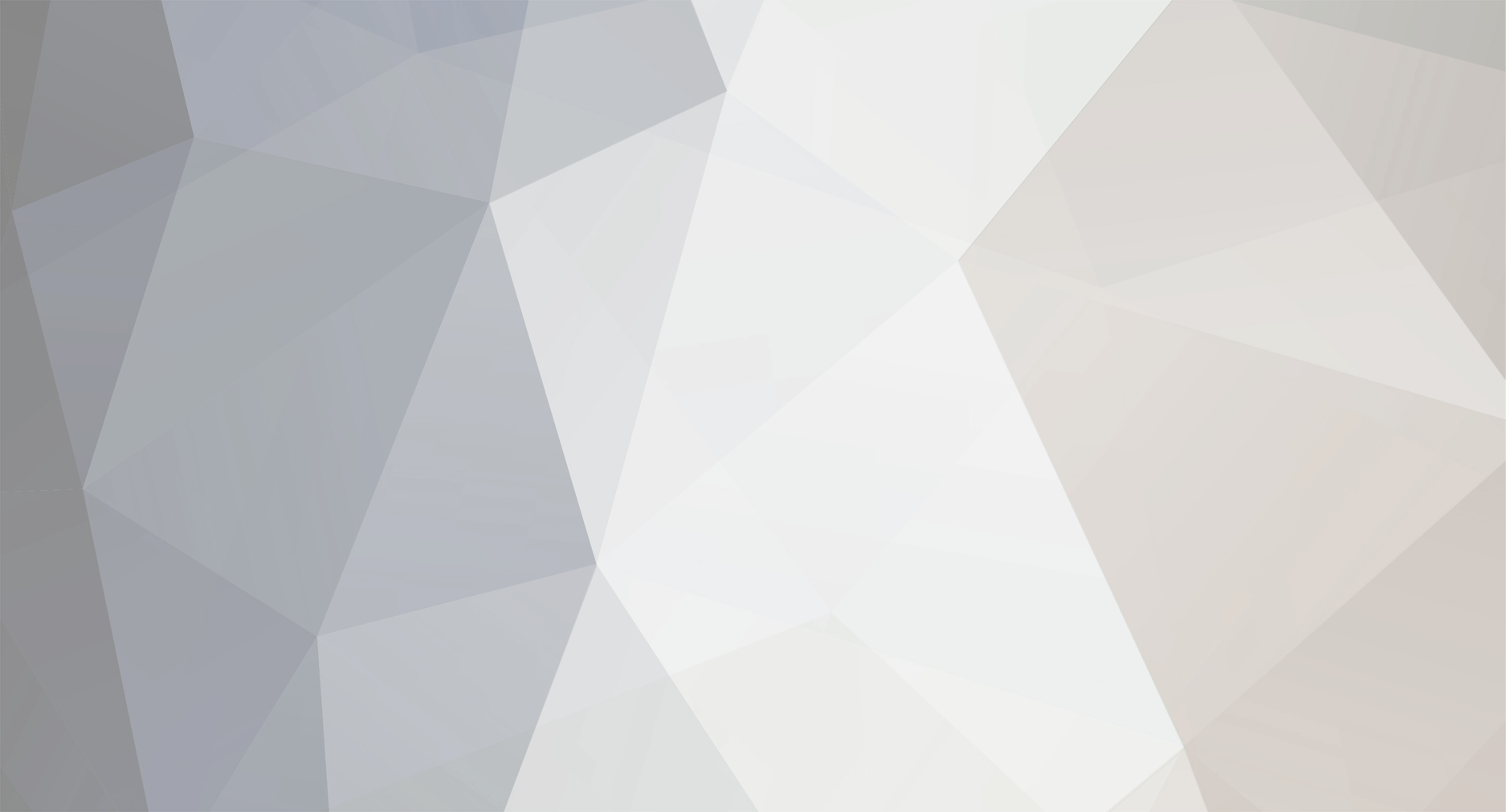
3below
Member-
Posts
2,670 -
Joined
-
Last visited
Content Type
Profiles
Forums
Events
Shop
Articles
Everything posted by 3below
-
Looking for an old school valve amp - maybe?!!
3below replied to bassintheface's topic in Amps and Cabs
I have no problem using my Sound City MKIV for bass. They can be really good (near Hiwatt build quality and quiet), they can also be 'dogs' (rats nest wiring, dry solder joints and noisy). If you get a 'dog' they make the basis of a good Hiwatt clone. -
In the interests of preventing 'neck dive' place the bridge as far back as possible, extend neck pocket to where the front guitar pickup is located. Having planned (lol) and played around with a very similar idea you can use a guitar fingerboard in this configuration. The veneer or hardwood both look good, I am thinking mahogany body and neck for mine - the licence plate cigar box 3 string I recently built finished really well with Tru-oil. Maple, rosewood, ebony or what for the fretboard? Mine is not yet started, am awaiting arrival of some more wood.
-
As I understand it Titebond can also be 'unglued' (heat, water/steam,alcohol but to name few). Useful when 'blunders' need sorting (as I will soon do with a neck / fretboard I made). IMO Avoid polyurethane glue in instrument builds, it makes repairs difficult if not impossible.
-
Question: In view of the possible cracks (or finish cracks), would it be worthwhile running thin superglue (or one of the flexible superglues) in the bottom of the truss rod channel before other re-assembly starts. Hopefully it would penetrate any serious cracks and stabilise them. What are people's thoughts?
-
@stewblack We are with you on this mission. You are, with great skill, undertaking a very challenging operation. Keep the good work going. 🎸
-
@Jabba_the_gut method using small panel pins (I have forgotten what the really thin ones are called). Tack a pin (not too deep) either side of the truss rod at the neck end and then the heel end (i.e. 4 pins in total). On a normal thickness board locate the pins between frets and away from inlays, Not so critical with the Shaftesbury thick board. Cut the pins down to about 2mm height with sidecutters so they leave sharp ends. From there on combine the @Jabba_the_gut and @Reggaebass methods and enjoy. The tacks will have to remain in place since they are now glued in and hidden. Thoughts gentlemen?
-
Try clamping a wet fish sliding about on wet marble chopping board. Now think about getting the wet glued board aligned on the neck edges to within 'a gnat's chuff' .whilst clamping firmly. I may be overthinking this one however.... I await the advice of TEOTB.
-
I eagerly await the next installments of this adventure. The prolonged 'joy' of expanding the truss rod channel if it is done by hand I particularly look forward to gaining an insight from the Elders of the Build (EOTB) into getting the fretboard back on with perfect alignment (it is currently well above my pay grade, never attempted it). I have a previous build that I would like to get the board off and back on, after applying some correctional therapy (to correct a detail blunder I made). Vorsprung durch herstellung / progresser en faisant.
-
This is exactly what I would do as well. In my table of results I had missed the earlier post with the at the paint line measurement.
-
+1 Having just contemplated a truss rod I can see how I would (might?) do it by hand using a plough plane, jig and considerable skill (above my pay grade and needs more practice than I do on the bass). I would also be highly concerned about 'breaking out' the skunk stripe / crack and making matters worse. Now got thinking hat on some more. Hand tool method, slow but do-able (I think). Remember you only have to remove 1 mm width most of the way. Flat file, handle removed, non-toothed side down, slide along the channel. Eventually the rod will fit in the middle section. Adjuster end could be opened out with regular or round file. Heel end of neck, open out the slot using a chisel if needed. The heel end rather depends on the actual rod, the one I am physically looking at has a blob of weld proud of the 6mm, when I use it I will have to chisel out an inset to accommodate. In view of the thinness / state of the skunk stripe I would probably round the ends of my file over using a stone / diamond plate so that they do not catch the wood. Another tactic could be 3/4mm wood block, glue 80 grit (or less) sandpaper on, slide in the channel. Going back to a single action rod, I wonder if there will be (was) sufficient curvature available. @Andyjr1515 touched upon this earlier and should be able to advise.
-
There may be a non-router way out of this. Am going out for some time - to look at a truss rod I have in my possession. Lockdown, brings out the simple pleasures in life 😎
-
I thought I had done the same sum as you above, i.e. at start of fretboard (my 0 cm) the neck is 14.5 mm deep, channel is 9.5 mm deep giving 5 mm wood thickness under the channel. My second row, neck thickness drops to 14 mm, channel depth 9.5 mm giving 4.5mm wood thickness. Is this correct?
-
@stewblack, thanks for the measurements, summarising as far as fret 5 (22cm approx) if I have understood correctly: position /cm neck depth/mm channel depth/mm wood thickness/mm 0 14.5 9.5 5.0 1 14.0 9.5 4.5 2 13.5 9.5 4.0 3 13.0 9.5 3.5 4 12.5 9.5 3.0 5 12.5 9.5 3.0 6 12.5 9.5 3.0 7 12.5 9.5 3.0 8 12.5 9.5 3.0 9 12.5 9.5 3.0 10 12.5 10.0 2.5 11 12.5 10.0 2.5 12 12.5 10.0 2.5 13 12.5 10.0 2.5 14 12.5 10.0 2.5 15 12.5 10.0 2.5 16 12.5 10.0 2.5 17 12.5 10.0 2.5 18 12.5 10.0 2.5 19 12.5 10.0 2.5 20 12.5 10.0 2.5 21 12.5 10.0 2.5 22 12.5 10.0 2.5 My take would be that you have sufficient depth for a two way rod (9.5mm). You will need to bring the adjuster nut as far towards the headstock as far possible - allowing for allen key insertion and truss rod cover clearance. I would aim to get the 'bearing' end of the two way rod into the 4 ~ 4.5mm zone. Look for a rod with a 'short' adjuster length. The bearing point is the threaded block in the diagram. What do my esteemed colleagues think now that we have the neck profile established? @stewblack you have kept your beard in much better trim than mine, I am going for the ZZ top version
-
Keep going with the measurements, need the neck thickness in the same way so we can get to the wood thickness under the channel. if we get lucky a two way rod inserted at a strategic position with wood strengthening may still work. The simpler the solution the better (as long as the solution is valid).
-
Eminently possible but again not for the 'faint-hearted' I can see this considerably simplifying the jigs needed to do the routing. The existing truss rod channel would act as a bearing guide for any routing. OTOH the refinishing would increase significantly.
-
Totally agree, I would be making alignment jigs etc. to attempt this one. Getting the board on correctly afterwards would also challenge me. It would be my solution of last resort. Far easier if we can get a rod in the existing location.
-
Point 2 above is a key part of the solution. Some measurements every cm along the the neck and channel for the first 7 frets or so would really help establish the profile and what room is available. I am pondering the forces situation, my Physics degree is very rusty these days lol.
-
Another possibility entered my consciousness last night. Infill the truss rod channel with suitable wood glued into it to give a level bed depth of say 6.5 mm. This should stabilise the crack (if it is one) and give sufficient wood depth behind a dual action rod. With the fingerboard being so deep it should be possible to router (or chisel or router plane / plough plane) a 3 mm groove in the board so that the flat surface of the rod sits in the board. Stop the groove at a suitable length so that the the rod emerges from a flat (non grooved) end of the board at the nut end. By doing this the truss rod cover will sit against the fingerboard as before and no sign of the channel in the board will be visible. The 6.5 mm / 3 mm dimensions are obviously subject to the actual truss rod, board and neck depths available. I am sure there are flaws in this plan that will be picked up by others
-
All is not lost, it has just become rather more involved Hopefully it is just the laquer, however if not there are several ways out. How handy are you with the router?
-
This looks like it will be a close decision between two way or single rod. Some more measurements will help. I would suggest starting at the nut and repeating the measurements of neck depth every cm down the neck until you get to the 7th fret. This would aid accurately determining the overall profile and whether a two way rod could go in further into the neck (longitudinally not depth) aiming to get the pressure point away from the 'too thin' timber. If you then install the rod with the flat upwards you also have some latitude to strengthen the 'thin' wood under the adjusre nut with epoxy / epoxy + carbon fibre.
-
I am lost for words :). Does this mean that you need to deepen the channel, no infill needed? I was just warming the planer-thicknesser and bandsaw up
-
The unmentionable bass (looks very similar to yours) that I owned many years ago also had an incredibly thick fingerboard with the same style binding. In this respect the Shaftesbury is being faithful. Really good work so far and so rewarding when a DIY job saves the day. Having recently encountered (for the first time ever) a neck with a back bow I would use a double action rod if you can. If you need a strip of maple to fill the truss rod channel bed for the double action rod put the dimensions up on here.
-
P Bass bodies and necks clearout.
3below replied to Raslee's topic in Accessories & Other Musically Related Items For Sale
-
P Bass bodies and necks clearout.
3below replied to Raslee's topic in Accessories & Other Musically Related Items For Sale
-
ABC Music Retail from the 1980’s , any memories ?
3below replied to BritBass 2's topic in General Discussion
USA Strat circa 1990 bought by telephone and email from ABC. Still have it, as it was as good as they said.