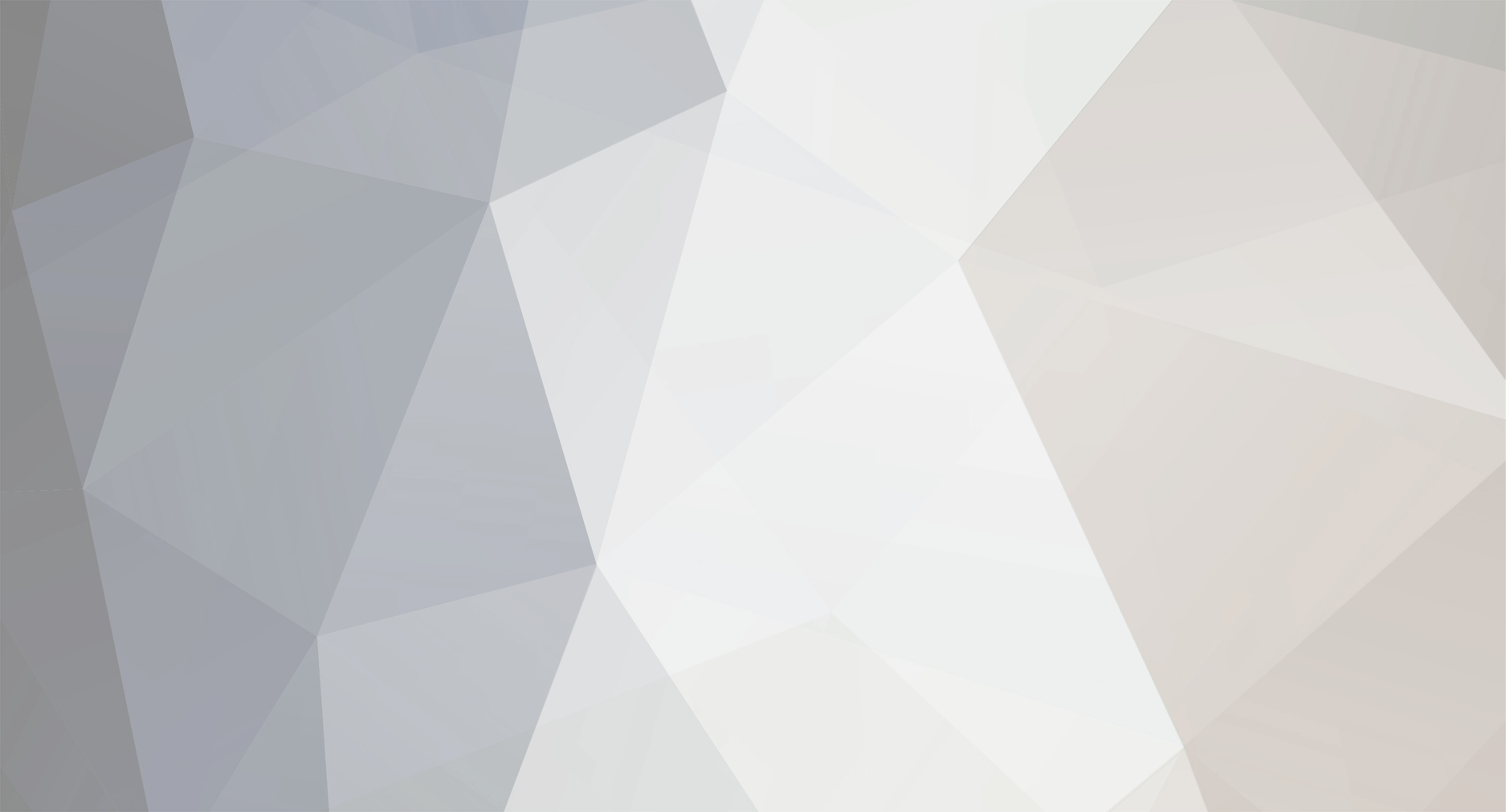
iiipopes
Member-
Posts
756 -
Joined
-
Last visited
Content Type
Profiles
Forums
Events
Shop
Articles
Everything posted by iiipopes
-
Alternatives to Hipshot Ultralite Tuners?
iiipopes replied to Dolando's topic in Accessories and Misc
I don't know if they are less expensive, but both Shaller and Gotoh (copy of Shaller) make mini bass tuners. I don't know your preferred headstock layout, but for example: [url="http://www.ebay.co.uk/itm/GOTOH-CHROME-3-2-SEALED-MINI-BASS-TUNERS-/251009128398?pt=Guitar_Accessories&hash=item3a714f57ce"]http://www.ebay.co.uk/itm/GOTOH-CHROME-3-2-SEALED-MINI-BASS-TUNERS-/251009128398?pt=Guitar_Accessories&hash=item3a714f57ce[/url] -
Jazz bass "strat type" toggle switch
iiipopes replied to mentalextra's topic in Repairs and Technical
[quote name='brensabre79' timestamp='1353593866' post='1876389'] I have a 5 position rotary on my main Jazz (in place of the second vol. control) the 'in-between' positions have a pre-set variable resistor in to turn down one of the pickups. After setting the blends where I want them, now I can recall the sound exactly every time![/quote] I like that idea! I did the same thing on the neck pickup of a couple of guitars to get them to balance with a master volume, and Rickenbacker guitars have the famous 5th knob for the same thing as well. Good show! [quote name='BigRedX' timestamp='1353595040' post='1876396'] According to the Fender web site the switch on the Tony Franklin bass is just a 3-position giving each pickup on its own and both together in the centre position.[/quote] As I suspected: Tele wiring. -
I should have said "conventional" paint won't stick. Painting aluminum involves a complex process of chemical priming and other steps, such as: [url="http://www.finishing.com/1200-1399/1318.shtml"]http://www.finishing.com/1200-1399/1318.shtml[/url] or [url="http://www.therpf.com/f9/how-do-you-paint-aluminum-105203/"]http://www.therpf.com/f9/how-do-you-paint-aluminum-105203/[/url] The problem with powder coating is involves heat which may distort the parts. If you insist on black, it may cost a little more, but Hipshot and Gotoh both make a mini-bass tuner and I believe so does Shaller, that can both be ordered in black. Better to save money and order them in black and know what you're getting instead of risking ruining the tuners trying to change them.
-
Jazz bass "strat type" toggle switch
iiipopes replied to mentalextra's topic in Repairs and Technical
If it's wired conventionally, being a two-pickup instrument, it would be wired more like a Tele than a Strat. -
They're aluminum alloy case with steel post and screw. They won't hold paint.
-
Some tuners just can't lock on to the low fundamental of a B string. Try tuning it with the octave harmonic and see what happens, after you've done everything to make sure a good quality string is installed properly and the bass is set up properly as I set forth above.
-
On my 5-er, to keep things simple, instead of active preamp and controls that can get a bit unwieldy on stage, I have the Ibanez version of the EMG EXB after the V-V-T. It variably cuts mids while boosting treble and bass. So it's a combination "vintage-to-modern" or "slap contour" knob. I find it most useful for those songs that require some tone shaping beyond the stock pickups. So with four knobs, V-V-T-EXB, it sounds like it has a dozen.
-
Labella and D'Addario publish tension specs. Not many, if any, of the others do. CircleK only makes rounds at this point.
-
These reviews should help: [url="http://tubedepot.com/12ax7reviews.html"]http://tubedepot.com/12ax7reviews.html[/url] [url="http://thetubestore.com/12ax7review.html"]http://thetubestore.com/12ax7review.html[/url]
-
High C does not necessarily have higher tension. It may feel that way because of the lesser diameter feeling more pointed on the fingertip. Some folks, not liking low B, but wanting the low range, tune the lowest string to C so it is C-E-A-D-G instead of B-E-A-D-G. Even I experimented with that for awhile before going to a size larger B string and tuning conventionally.
-
The most versatile option is to go with a vintage-style P pickup, good pots and caps, add a noiseless or humbucking J-pickup (like a DiMarzio J or UltraJazz, or Fralin or Aguilar end-to-end, Fender Noiseless, or Seymour Duncan vintage Stack), wire it V-V-T, like a J-bass, by adding another hole in the pickguard on an arc to match the existing V-T-jack, and rock on. As you bring up the volume of the J-bridge pickup, you will get a good slap.
-
[quote name='ikay' timestamp='1353171323' post='1872396']Basic geometry comes into play here. The narrow nut on a Jazz means the strings are splayed out towards the bridge (a little more than on a Precision). The top and bottom strings in particular are therefore running at quite an angle to the centreline of the neck. Doing this on a neck with a small fixed radius means that the outer strings will choke/buzz (around the middle part of the neck) if the action is too low.[/quote] Yes, if the strings are played in "bends" guitar style to slide up to pitch. At any given point, however, if you sight down the neck, it's still straight or has just the same relief. Otherwise there couldn't be such instruments as fanned frets or helix necks (Lace Helix, Little Guitar Works Torsal).
-
[quote name='MiltyG565' timestamp='1353281212' post='1873302'] cannot be tuned. do you mean, you tune it and it quickly goes out of tune, or you literally can't tune it to B? If it was going out of tune quickly... i'm not sure, i would look at the simplest thing first- the string. try putting a different B string onto it. make sure the nut isn't too tight that the string binds in the slot, and not so wide that the string can move about in there. If that fails, you have to look at the neck, truss rod, bridge. Do all the other strings stay perfectly tuned when you try to tune your B string? [/quote] Get a new B string. Before you install it, make sure there is no binding: burnish the bridge saddle slot and the nut slot (making sure you don't dull over the "witness point" on the front of the nut) then rub them both with pencil graphite. Cut the string to length so that two or three windings wrap neatly around the tuner post and install the string slowly and evenly. Give it a couple of good tugs once up to pitch, bring it back up to pitch, press carefully down on the string right in front of the bridge saddle and the fingerboard side of the nut to seat the string, tune again and play.
-
For stability, the best solution is to rout out the bass in the size of the bridge and glue in a piece of wood, preferably maple or the same as the body or top (if it has a separate top) of the bass, so half of it will lend stability and the other half raises the bridge as necessary.
-
[quote name='flyfisher' timestamp='1353075303' post='1871323']There is usually plenty of depth available for such fixings (in solid-body instruments anyway) so why not use it?[/quote] It depends on the bass. Fender? Yes, probably. My Ibanez SRA305? Definitely. Rickenbacker? No.
-
"C" and "D" necks, when talking about actual Fender basses, also can apply not only to the contour of the back of the neck, but to the width of the nut as well: 1 1/2 is the "A" neck, 1 5/8 is the "B" neck, etc., as set forth on the bottom of the Fender link above. Oversimplified: rounder radius is easier for chords, flatter radius is easier for string bending. That's why Warmoth and some other companies have gone to a "compound" radius board, for ease of chording in the first frets and ease of lead guitar playing up the neck. So for bass, it's whatever is comfortable. For me, after trying many different necks, I settled on 10" for my custom fanned fret bass.
-
Any good .047 capacitor will do, and the physically smaller, the better. As your picture, RIC prefers capacitors with axial leads for ease of installation. As far as the .0047 inline capacitor to the bridge pickup, I sincerely recommend you do install it with a bypass switch as is current RIC production. The capacitor gives the bridge pickup the classic Rick tone with Rotosound Swingbass rounds, as with Chris Squire and others, and the switch gives you the tonal options.
-
Can somebody give an answer on Ric wiring!
iiipopes replied to Iheartreverb's topic in Repairs and Technical
Pots: Yes, current RIC production is 330kohm pots for both volume and tone for simplicity of parts sourcing and manufacturing. 500kohm pots will give a slightly higher presence peak, or a slight edge, and 250 kohm pots will give a lower presence peak, or very slightly more mellow tone. The difference is very slight, and a lot of folks can't tell the difference. What you use is up to you to to decide how much peak you desire, but if you want more of the classic Rick edge with Rotosound Swingbass roundwounds, go with the 500kohm pots. If the edge is too much, you can always bridge the pot lugs with a 1megohm resistor later to bring the effective value, and therefore the resonant peak, down a touch. One option would be to use the 500kohm pots on the bridge pickup and 250 kohm pots on the neck pickup to get more contrast. Caps: when you jumper the .0047 inline cap, it effectively takes it out of the circuit. It is still there in the wiring, just bypassed at will. The current schematic on the RIC website for the 4001/3 shows the capacitor, but not the jumper of the newer instruments with the switch. The current wiring takes a wire jumper from either side of the .0047 inline capacitor to the switch that is the bottom half of the tone pot so when the switch is engaged it bypasses the capacitor. The two .047 tone capacitors are still necessary and are not affected so you retain an independent tone control (treble roll-off) to each pickup. Here is a link to the published factory schematic: [url="http://www.rickenbacker.com/pdfs/19507.pdf"]http://www.rickenbac.../pdfs/19507.pdf[/url] Pickups: nothing sounds like a Rick pickup. My advice is to save your money and go for the real pickups, even if you have to purchase only a treble pickup. But if they are simply unobtainable, I'd look at the Bardens first. Legend? Probably not. But I do have a thread on the RIC factory forum: [url="http://www.rickenbacker.com/forum/viewtopic.php?f=2&t=7928&hilit=iiipopes+mod"]http://www.rickenbac...it=iiipopes+mod[/url] -
For a Rickenbacker bass, the players on the west side of the pond tend to prefer an automotive product called Zymol: cleans and polishes to a high gloss. I don't know if it's available in the UK or not. [url="http://www.zymol.com"]http://www.zymol.com[/url]
-
Damaged my Full Circle pickup - yay, fixed!
iiipopes replied to Clarky's topic in EUB and Double Bass
[quote name='Mr Bassman' timestamp='1353019827' post='1870721'] It's happened to me a few times with the full circle & bassmax Those after length fittings are not the best design, trouble with the bassmax is the cable is too short for an alternative fixing. If one must use this type of jack mounting it's advisable to wrap the instrument cord around the tailpiece a couple of turns or use a cable tie to prevent the mounting being pulled away. Then if you trip on the cable the pup is safe, you only risk breaking the neck [/quote] Good advice. I must confess, however, that I continue to use the string afterlength bracket because it is serving very well as a wolf eliminator on my E and A strings, which clarified my tone significantly. -
[quote name='BigRedX' timestamp='1352981573' post='1870033']Edit: Having had a better look at the photo, that's a pretty big hole. You might be better buying some appropriately sized hardwood dowel, drilling the hole out and gluing that in place. Then trim and drill a new pilot hole for the screw.[/quote] The best way.
-
[quote name='Big_Stu' timestamp='1352906974' post='1869230'] I'm still looking for a "soap-bar pickup" which is cunningly disguised as a humbucker sized single coil. [/quote] Gibson P-94 [url="http://www.gibson.com/en-us/Divisions/Gibson%20Gear/Pickups/P-94/"]http://www.gibson.com/en-us/Divisions/Gibson%20Gear/Pickups/P-94/[/url]
-
What concerns me more about blowing amplifiers is dissipation of heat. Even when operated "in parameters," valve/tube amps can get mighty hot. That's how I got my 2203. Someone had killed it - it had gotten so hot the top plastic vent plate melted down into a trough! (It's now a great place for putting spare connectors, preamp tubes, picks, etc. for the gig). I had it rewired for EL-34's instead of the stock 6550's that it had for the American market, and I run a pair of Electro-Harmonix "big bottle" 6CA7's (think 6L6GC on steroids -- clean, with a nice breakup -- 6550 plates but EL34 grid bias). Properly ventilated, biased and loaded, when I played more guitar, I could run it all night cranked with two of the four output tubes pulled, run a 32 ohm cab (wired four nominal 8-ohm speakers in series) instead of a 16 ohm cab so I could push it harder to get tone without necessarily increasing volume, and it would run all night only moderately warm, keeping it away from the back wall and not putting anything on top of it. Yes, these new class D amps are great for efficiency, cooling, clean tone, and light weight, and I run a new Carvin MB12 with an extension cab as my gigging bass rig for both electric and double bass, but nothing beats what Jim Marshall's large power transformers can do for guitar for the output stage of his amplifiers! You don't worry about underpowering. You worry about damaged ear drums and loosening fillings, with tone!
-
Yes, but don't beat around the bush. Tell me how you really feel. I love a good debate. Now, I own a Marshall Master volume 2203 from 1975, and have played both guitar and bass (and keys, and tuba, and...) since then, and trumpet since 1973 and piano since 1970. I've been cranking the stuffing out of the preamp knob on my 2203 for probably longer than many of the people posting on the forum have been alive. My amp is just fine. My Celestion Vintage 30's, and before that my Jensen Concert Series speakers (a notoriously low-power handling, but great tone for jangle speaker), are just fine. I wondered how much flak this post would receive. I expected gentlemanly disagreement, but not the emotional outbursts. There you have it. The only speakers I have ever blown, personally, were those which had damaged or deteriorated suspensions, and therefore were going to blow anyway in time, or from massively overpowering them. (100w through a 25w speaker, bass through a guitar speaker in an open back instead of sealed or ported cabinet, etc.)
-
D'Addario Chromes and Warwick bridges?
iiipopes replied to Ben Jamin's topic in Accessories and Misc
I think Warwick makes a great tailpiece, but installs it incorrectly for this very reason. I would unscrew the B side of the tailpiece and simply rotate it back away from the bridge as far as possible, or as far as necessary to clear silk, and still be able to have a screw hold tension in the body, and not offset the notch too much.