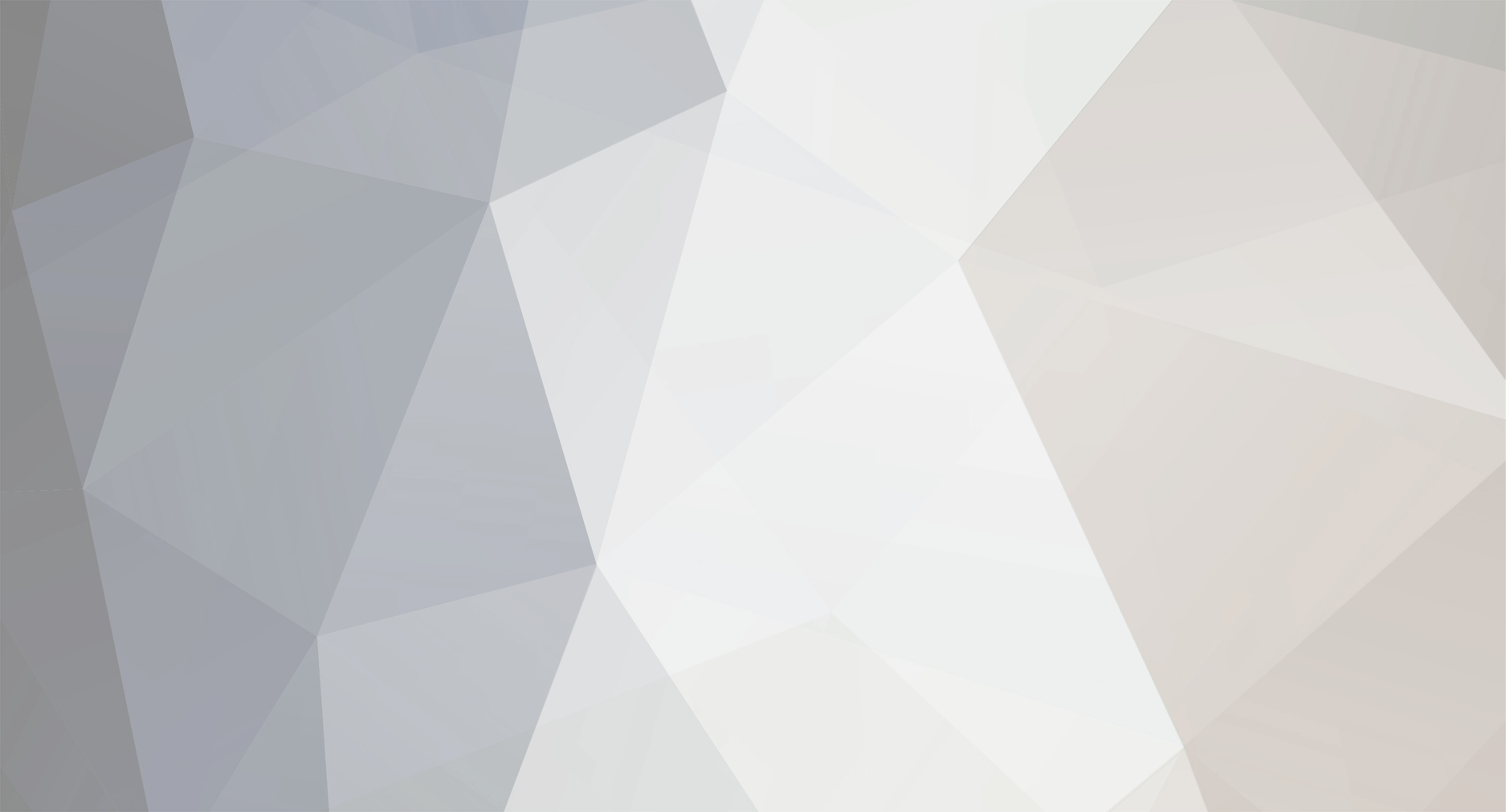
rwillett
⭐Supporting Member⭐-
Posts
1,612 -
Joined
-
Last visited
-
Days Won
6
Content Type
Profiles
Forums
Events
Shop
Articles
Everything posted by rwillett
-
Need some help on the wiring for a BFM Omini 10.5
rwillett replied to rwillett's topic in Repairs and Technical
Thanks, that would be great. -
Need some help on the wiring for a BFM Omini 10.5
rwillett replied to rwillett's topic in Repairs and Technical
I'm reasonably certain you are correct in your wiring assumptions. If not then, I assume you'll come down and fix it for me -
Need some help on the wiring for a BFM Omini 10.5
rwillett replied to rwillett's topic in Repairs and Technical
Is Bill on here? Gosh didn't know that. -
Need some help on the wiring for a BFM Omini 10.5
rwillett replied to rwillett's topic in Repairs and Technical
I've ordered some larger connectors and a spare cement resistor "just-in-case" and will rewire it. How you managed to get three wires in that choc block is beyond me! Which amp did you drive it with? We briefly touched on it at the bass bash but I completely forgot about it as I was lusting after your Thunderbird. @Mottlefeeder used a nice Warwick Gnome which could do 120W/8Ohm, the speaker is rated at 250W and is 8Ohm, so I could go quite a lot louder, but not sure if I need that much power or am I deluding myself -
Need some help on the wiring for a BFM Omini 10.5
rwillett replied to rwillett's topic in Repairs and Technical
It's possible that three wires might fit in there. I could imagine a lot of swearing to get them to fit as well 😊 I read the comment on the BFM site. Basically it has to go there in front of the square resistor. I'm going to look for bigger connectors though those look quite big. -
Need some help on the wiring for a BFM Omini 10.5
rwillett replied to rwillett's topic in Repairs and Technical
I don't think it actually goes where the red square is as there is very little gap at each end. However logically it might do. -
Need some help on the wiring for a BFM Omini 10.5
rwillett replied to rwillett's topic in Repairs and Technical
The other speaker wire goes to the other side of the choc block next to the red square. Rob -
Hi, I was lucky enough to have a BFM Omni 10.5 with four tweeters donated to me by @neepheid at the NW Bass Bash. It was a fine sounding cabinet when we tried it out with @Mottlefeeder Warwick Gnome amp. The more discerning amongst you will notice the past tense in the previous sentence. There was an issue with a switch that sometimes seemed to work and sometimes not. So I decided to pull the back off and have a look at the switch with my multimeter. I assumed a loose connection. As I removed the back of the cabinet, I somehow managed to disconnect one of the cables to the bass driver. The bass speaker is a rather nice "Eminence DELTALITEII2510 10-Inch Neodymium Series Speakers - Series II" according to Google reverse image lookup. To be honest I'd never have got it from the markings on the speaker itself but that's another story. So one of the bass speaker cables is off and I can't work out where it came from. I think it's one of two places, either the red square or the purple rectangle. The light green is the end of the wire. I've checked the BFM website and community section but it's light on photos and so have come to bow down with sackcloth and ashes and ask for help. This is so embarrassing. Oh and if anyone has a Warwick Gnome for sale, ping me a message Any help welcomed Thanks Rob
-
Been thinking about this again (another sleepness night). The die used in the machine to stamp this out can't have been broken otherwise more material, not less, would be left. If it was broken and then repaired (die heads aren't cheap to make so repairing it makes sense, toolmakers are skilled craftsmen) then there would be more material in the tuner head. I'm going with a different die was made and perhaps they were looking to align this with something else. I will now do my best not to think about this as I walk the dog. Rob
-
More than happy to take it off your hands at a "load of junk" price if you want Absolute beauty as already said. I love little things like this 'notch'. I doubt I'd ever notice it if it wasn't for other people....
-
I would expect early 60s metalwork to be stamped out on a machine. These are fairly cheaply made with bent over tags to lock the barrels on. That's not a comment to annoy people but a reflection on how things were done then Whilst you could mill them, the costs would be 50-100x the cost of stamping and bending. Cheap CNC did not exist in the 60s. I would assume a different stamping machine did the tiny notch and these could be just a different die used at the time. It could have been designed to fit against something else for orientation and Leo did a deal. Or it could be something else. Rob
-
I'd actually hope it isn't enigmatic for that sort of money...
-
This is Bev. She's a really good drummer and allows me to jam with her and wreck her timing.
-
We're just looking at a lovely eight string, a few Warmouths, some old Fenders. Enjoy the house work 😄
-
Today's the day. It's gorgeous here in Clapham. Currently 9C expect high of 20C. Not a cloud in the sky. Finiahing my coffee and will open up the village hall.
-
He has cut down...
-
I'm trying to work out if this is actually an issue or not. I know nothing about Rickenbackers apart from Macca and Lemmy played them. I keep hearing that the bridge is difficult but surely after all these years they must have fixed this problem? Or is it just a running joke that nobody does adjust them? Thanks Rob
-
Have they a cheap 62 Jazz as well?
-
@neepheid We'll take everything I can find in the house. We'll make it work one way or another. Rob
-
Ron All help welcomed but it's chairs and tables so it's not a.massive amount of work. However it would be good to see you and you then get the advantage of an empty (ish) hall to play in 😊 I have asked if the lady I jam with will come and bring her mobile drum kit. Her main drum kit appears to be larger than John Bonhams set from LZ 😊
-
Food now sorted. I've arranged for a special tea delivery for @ossyrocks from Farrers Tea & Coffee merchants in Kendal, they're sending a local van just for me, and a local dairy farm has helped chip in with milk. The village hall will be open from around 08:00 for people to get in. Will anybody apart from myself (and possibly @neepheid) be coming at that time? The intention is to finish around 16:00 (ish) as I have to be in York later than evening. Rob
-
Will Basschat survive the Online Safety Act?
rwillett replied to fretmeister's topic in General Discussion
You are correct that most will be, I hadn't considered that, but how are Ofcom going to know? If they develop a Web crawler, does it respect the robots.txt file? This is going to be very difficult for them to police. -
Will Basschat survive the Online Safety Act?
rwillett replied to fretmeister's topic in General Discussion
I think this is the key line here "Websites will have to change the algorithms that recommend content to young people and introduce beefed-up age checks or face big fines, the UK media regulator has confirmed." My emphasis added. This is targetting the social media apps that push things to you. Basschat doesn't recommend things, also we don't have any young people. I will get around to reading the legislation and the Ofcom stuff once the bass bash is over and I have a free few hours. Just for information, there are circa 11.1M .co.uk domains registered, not all of which are live. A simple thought experiment on how much work is needed to process this information if its only 10 mins per website per year manually. You can't do everything by computer yet. UK law isn't very happy with fully automated decision making by UK Govt depts. Assume 50% are live so that's 5M websites = 5,000,000 * 10 = 50M minutes So 50M minutes = 833,333 hours. 833,333 hours = 120,000 days (ish) Assuming lunch breaks 120,000 days = circa 550 people As of 31/3/23 Ofcom had circa 1,300 employees. So even a cursory 10 min check will require a 41% increase in employees. I know that the civil service is doing it's best to cap new recruitment. Ofcom is considered a quango and whilst it is not subject to civil service recruitment blocks, its funded by frees from industry as well as grants from central govt. It will not be capable of recruiting 550 people or 275 people or even 140 people for a 2.5 min check. Somebody has to answer the phones, report on how many websites are checked, this is all manual. There are no robots here. I'm also not aware of any software development that might be taking place to do this work. That doesn't mean it hasn't happened as I'm focussed around certain areas of UK Govt, but I might have heard. As I've said before, the focus here will be on the large social media companies. Basschat is in the low level noise here (pun intended) Rob -
We're down to our last few days, so I think we have 15 bass players plus one very significant other who may or may not join us for lunch (though she is very welcome) and may or may not bring mutt (that's the dog, not @bigthumb) @rwillett @bigthumb+ 1 <-- Vegetarian @neepheid @ead @80Hz @GreeneKing <-- Vegetarian @stevie @nekomatic @ossyrocks <-- Endless tea @peterjam <-- Eats anything, likes small children. @doomkeeper @Frank Blank @zbd1960 @bagsieblue <-- Vegetarian @Mottlefeeder <-- Vegetarian I count five vegetarians so that leaves 10-11 non vegetarians. Thankfully we have less than twenty otherwise I run out of toes. I'll ensure we have a collection of circa. 30% vegetarian pizzas and the rest a range of fairly mild pizzas up to quite spicy ones. As I have no sense of smell, though I can taste but its reduced, I tend to go for the spicier one. I do not judge people here I'll also get some salads, 300 tea bags for @ossyrocks, 4 gallons of milk for @ossyrocks (do you want sugar as well?). We'll have the village hall from when I drag myself out of bed, say 07:30 to around 16:45 or so on Saturday afternoon. We can park on the road outside the village hall. Can I ask that people unload and then move their cars please onto the main road please and not park behind the village hall as it is in use for other things and I have to live with the neighbours for another year. There is power in the hall but you might want extension leads. We have loads of tables and chairs. Any questions please ask. Rob