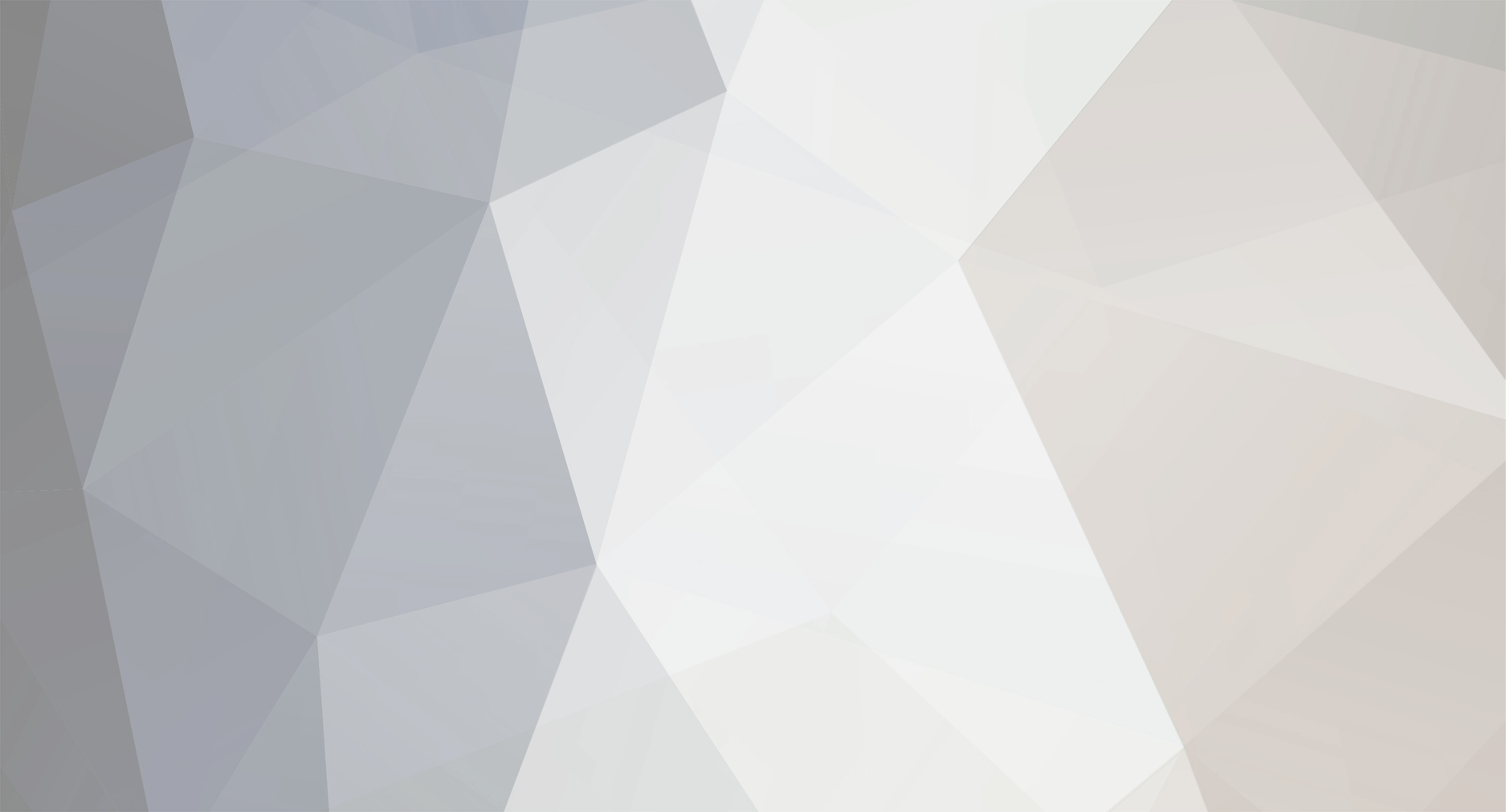
rwillett
⭐Supporting Member⭐-
Posts
1,518 -
Joined
-
Last visited
-
Days Won
5
Content Type
Profiles
Forums
Events
Shop
Articles
Everything posted by rwillett
-
Is this on the pedal or in the application? As @bntsaya just use the librarian section of Tonex. I set the pedals up and do everything there. However I do very little in the pedal apart from volume and gain. I'm quite simple about this stuff
-
The software is very very irritating. IK multimedia have made it very difficult to do anything at all. It's difficult to remember a piece of software so cumbersome to use. Then I think about the England RUFC and their Game Management System software and think I'm blessed with Tonex 😊
-
That's one way I use it. I'm also trying to work out how to use midi to totally control it so I can switch both units from a single foot switch. I haven't got a band to play with (sob) so it's for my personal interest. I'm back from London end of week so will try and show what I'm doing if anybody has the slightest interest
-
Not as far as i can remember. I have the three button version and there are loads of presets. I've just set up the first six slots for my Telecaster and the second six slots for my bass. I didn't download much from memory and having the three switch version for some 'boutique' sounds that I suspect I'll never use. I've hooked it up to Mac and Windows and whilst the interface is a pain when all want to use is the pedal, it appears that I have to have Amplitube as the authentication for Tonex. I did not have the feedback issue you had. The software has a poor interface but it does work at least for me. I think you should have all the hundreds of presets I have, that's my understanding. You should also have lots of downloads as you've brought the hardware. The free version of Tonex has a restriction of 20 downloads from memory (that's ever!). I'm away tonight so can't check anything out. However I can say that I do like the Tonex. I use the software to set it up and then ignore the laptop. I have no idea if it's accurate but it sounds great to me plugged into a Yamaha hs7 monitor. I've never played a 57 Bassman wish I could.
-
No, the manual is crap, it wasn't you.
-
That's if they would even deign to speak to you... I had a Parisian girlfriend for a while, she would often never speak to me or acknowledge me, mmm.... now that I think about it, I wonder if it was me....
-
The bass sale that turned a (massive) corner… - *SOLD*
rwillett replied to AndyTravis's topic in Basses For Sale
-
The bass sale that turned a (massive) corner… - *SOLD*
rwillett replied to AndyTravis's topic in Basses For Sale
-
The bass sale that turned a (massive) corner… - *SOLD*
rwillett replied to AndyTravis's topic in Basses For Sale
-
The bass sale that turned a (massive) corner… - *SOLD*
rwillett replied to AndyTravis's topic in Basses For Sale
-
The bass sale that turned a (massive) corner… - *SOLD*
rwillett replied to AndyTravis's topic in Basses For Sale
-
The bass sale that turned a (massive) corner… - *SOLD*
rwillett replied to AndyTravis's topic in Basses For Sale
-
The bass sale that turned a (massive) corner… - *SOLD*
rwillett replied to AndyTravis's topic in Basses For Sale
-
The bass sale that turned a (massive) corner… - *SOLD*
rwillett replied to AndyTravis's topic in Basses For Sale
-
The bass sale that turned a (massive) corner… - *SOLD*
rwillett replied to AndyTravis's topic in Basses For Sale
-
The bass sale that turned a (massive) corner… - *SOLD*
rwillett replied to AndyTravis's topic in Basses For Sale
-
The bass sale that turned a (massive) corner… - *SOLD*
rwillett replied to AndyTravis's topic in Basses For Sale
-
Something don't smell right about this Rick
rwillett replied to Jean-Luc Pickguard's topic in eBay - Weird and Wonderful
I found what I think is the first pic on an older advert from Reverb from a month ago. I looked at the case marker on the right. I was going to say I'm no Rickenbacker expert but will now just say I'm no expert. The pictures look identical to me. Sadly I have no idea how to look at old sold stock on Reverb. The second pic in the sequence of two is a standard pic. Wouldn't touch this with a barge pole TBH Rob -
I saw that and thought
-
No it doesnt pass under the strings. Camera angle makes it look it does. However the angle is quite acute.
-
Nah. Just spent a few evenings with it doing first aid courses, concussion (headcase) and now got safeguarding to do. We're trying to get all the coaches through it and DBS checked and it's driving me up the wall. I hate it with a vengeance. However it did come across aggressively.apologoes Rob
-
I doubt it. I will fight to the death that the UK RUFC Game Management System is worse than yours.
-
The bass sale that turned a (massive) corner… - *SOLD*
rwillett replied to AndyTravis's topic in Basses For Sale
-
Clearly some people will The AI phrases that are always there: "Perfect for any..." "Whether you're a beginner...." "Must-have..." "... sure to impress" I sell on eBay and have never used the AI description generator. I put more effort into the description for my Dremel router table (don't laugh) for £20 than this bloke did for a circa £4K bass. Lets see if it sells Rob
-
The bass sale that turned a (massive) corner… - *SOLD*
rwillett replied to AndyTravis's topic in Basses For Sale
Hi To help the fund raising, I'm offering pedal risers for your pedal board. These are made to measure and I can make them just about any (sensible) size. All you need to do is make a donation to this fund. More information here. If funds are a bit tight, then contact me, the aim here is to raise money, not for me to make a profit (if only), so every penny goes to Andy and his daughter, Thanks Rob Rob