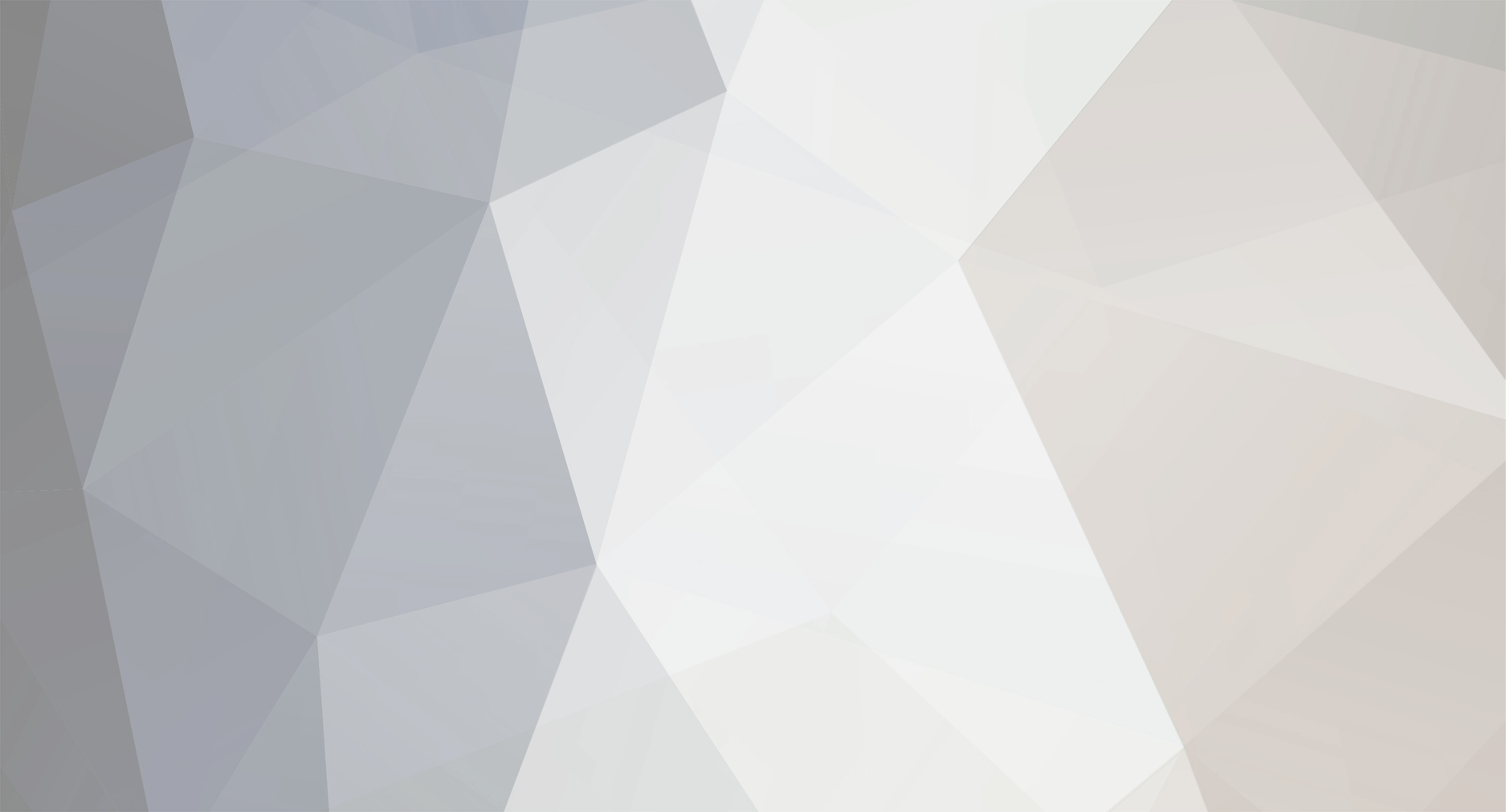
honza992
-
Posts
500 -
Joined
-
Last visited
-
Days Won
2
Content Type
Profiles
Forums
Events
Shop
Articles
Posts posted by honza992
-
-
Christine, how did the Mojo pickups turn out? Are you happy with them?
-
On 18/11/2019 at 21:59, SpondonBassed said:
I like the box of blades. Have you a link for those please?
I couldn't find any locally. I have a blade holder similar to yours only it is retractable. The tool shop that sold it to me can't get blades even on order...!
Happy shaving!
-
1
-
-
On 18/10/2019 at 07:52, Christine said:
I think that is very doable, just do it in small sections and keep your blade tight against the side of the slot in your bird's mouth type work surface (which will need a tiny slot just enough to let you work). 4 hours work and you should be faced with the more demanding job of routing your headstock.
I like your optimism! I'll give it a go on a test piece before commiting myself😁
Have you ever used the pearloid celluloid type sheet that R&K sell? Do you think that might be easier than real shell?
-
On 20/10/2019 at 13:27, Norris said:
Thanks Norris, I've emailed them. I'll see what they say.....and will also try doing it myself on a test piece....
-
On 13/11/2019 at 18:34, owen said:
I would love to contribute to this thread in a meaningful way. But I cannot. But I will say YES! Very cool.
Yep, this. Lots of skills and knowledge which I really wish I had! Really looking forward to this one....
-
Thanks everyone, I really appreciate the compliments. 😁😍
They're definitely premature though. I've learned not to count my guitar making chickens till they are well and truly hatched. The process of finishing, in my experience, is fraught with danger! The plan for the body is an epoxy grainfill followed by a hand applied polyurethane varnish, probably to a low gloss finish. The neck will be wipe on poly again, satin.
i've tried all sorts of grain fill methods and not enjoyed any of them. So I'm returning to epoxy, which I thnink is the best of a bad bunch. I'm using West Systems and tinted it with Mixol dark brown and a bit of black to make it darker still. Ive done two coats on the back and it is smoooooth.....one more on the front and I'm done. This time it's gone pretty well. The thing that's really made the difference is using a razor blade to spread a tiny amount of epoxy. For the entire back of the body I probably used about two pea-sized drops, maybe less. The razor blade is really effective at spreading the epoxy around without pulling it out of the pores. I rounded off the edges of the blade slighly so there was no chance of them digging in, and slightly dulled the blade using 400 paper on a very flat surface. It worked really really well. These are the type blades I used:
Here's a photo of mid fill, I love the way you can see the difference between grain that hasn't been filled, and the grain with the brown epoxy. It does a great job of highlighting....
-
5
-
-
2 hours ago, owen said:
You and me both!
Yes, sorry. I feel bad now☹️
But the next one definitely definitely definitely will be a bass. 😁
-
1
-
-
Mostly pics today.
The neck is pretty much finished. It ended up with an interesting scarf joint - I'm not sure I've seen one like it before!
Other than that, it's mostly just little jobs before finishing. There was bit of a chip in the binding so I repaired it using epoxy and black furniture powder. It seemed to work pretty well. I may use it to grain fill....time to do a few more experiments.
Finally I did the pickup routs. Me being me I decided to rout the neck heel at the same time. So I double sided taped the neck in, cut the side off the template, and whizzed away, praying the tape didn't fail!
A test fit and the pickup ring was right up against the end of the neck. Perfect!
-
9
-
-
On 05/11/2019 at 21:25, Pea Turgh said:
Oh lordy! That’s some bloody lovely work right there! What bass bash will this be attending in 2020?!
I've been meaning to go to a BB for ages, but what with one thing and another just never made it. We leave for Italy in March though, so it'll have to be before then. Anyone one know, is there one???
-
-
On 03/11/2019 at 12:30, Sidlanir said:
I've always wanted to do a zero fret, but never quite dared. I don't know what template you use for slotting, but most are designed for fretboards that are cut off or Fender style, rather that a zero fret (which effectively lengthens the scale length by half the kerf width of the saw). How is the intonation? I'm guessing the extra 0.3mm doesn't make much difference....
-
No problem. As you've discovered there is always a next one!
And actually I think round overs on your design is better. It has almost a Carl Thompson feel to it. It's great that you're doing your own thing.
-
On 01/11/2019 at 09:33, Rexel Matador said:
I'm toying with the idea of binding. I assume a single plastic strip, Les Paul style would be the easiest option for a first timer. Any thoughts?
Yes, plastic is probably the easiest. R&K have what they call celluloid binding which bends more easily that most of the cheap plastic stuff out there. Or if you want an ivoroid style then I recommend the one from David Dyke, it's more attractive than the one R&K sell. For plastic binding your basic choices are either to glue using pure acetone (I buy it in small bottles from Sainsbury), which is probably the easiest method, or with a glue like Uhu Hart, which is what I now use for plastic. There's a good video here:
The advantage of using acetone is that you can get the binding stuck down with tape first, and get your mitres and curves sorted before doing any gluing. The disadvantage is that acetone may not be that good for you, and also you can find that slightly discoloured acetone (from the binding) can run down the side of the guitar and into the end grain. The other option may be to use thin CA glue I guess, though I haven't used it with plastic binding, so test on scrap first. I've used CA with wood binding, and it worked great. Uhu Hart glue is acetone based, I believe, but because it's thick you don't have the issue of it running down the side. I still tape off though down the side to ease clean-up.
If you haven't done binding before, it's definitely a step up in terms of building difficulty. Rout the channel in several passes.
Oh, and I don't know how Fletcher gets away with using so little tape. For a Tele size body I cut 60 (yes 60) 3 inch strips and they all get used. You;ve got some pretty tight curves so that will be pretty much solid tape. Get them all cut first before you start gluing and do the whole body in one go. You don't want to get half way and run out of pre-cut strips.
If you do use acetone, resist the temptation to take the tape off too soon. I used to take it off the day after doing it and occassionally in places I would find the binding was still a bit soft, particularly parts that were under tape. So be strong and wait another night!
-
1
-
-
2 hours ago, Jakester said:
I can’t stop looking at this bass. It really is probably the most lovely thing I’ve seen in years. Absolutely stunning.
Ha ha @Jakester you can definitey come again! Thanks for that, I'm really glad you like it. There's a build thread somewhere.....'old up... (albeit I notice some of the pic links are broken....)
-
1
-
-
More annoyingly in between sessions on the neck I did a grain fill on the back of the body using West Systems epoxy. I did a couple of layers of (3 month old, hand mixed) shellac then grain filled. Leaving it a couple of days and it was tacky. I use a lot of WS epoxy and used the exactly the same for a couple of glue joints on the same day, both of which were fine. I sanded it off and tried again yesterday, same thing. The ratio and stirring were definitely right, so it's something else.
Annoying. Anyway, I've put it out for discussion on TB, and there's a suggestion it may be amine blush, but if anyone here has any ideas, please shout up!
-
2
-
-
Neck carve progressing. Everyone has their own way of doing it, I start by ignoring the difficult bits (ie the transitions) and getting the straight bit of the neck close to its final shape. I know lots of people start with the transitions, but I find it easier to have the main part of the neck done first, so I can sort of visualise what the transition needs to look like to join up with main. So here, after the pink tape the neck is more or less carved:
It's now just a question of hand carving till there is a gentle curve from the pink tape at one end, to the pencil line of the volute at the other. Here I've done the rough carve on right hand side:
The left had side is always more difficult (if you're right handed) because I've got to hold the file in my left hand. I don't know if there's also a left/right brain thing going on, but I also find it more difficult to visualise. Anyway, so far so good...
-
4
-
-
4 hours ago, Rexel Matador said:
Amen - routers are the ultimate necessary evil. They can do amazing things but they're utterly terrifying.
I do almost everything with a router. I have a table mounted monster, and a hand held one. In my opinion, safe and successful routing can be boiled down to two key rules:
1. Always rout into the wood (so you are feeding wood into the cutter).
2. Take multiple passes to take off tiny amounts of wood.
When I am routing bodies I take off an aboslute maximum of 0.5mm at a time. A sturdy guided router bit (mine has 4 blades and is a monster), a slow feed rate and a very very shallow cut and you will rout successfully and safely.
If I can have only one power tool, it would be the router.
-
Ha Ha @Rexel Matador welcome to the wonderful world of building. Nice to have you. It is, as you rightly point out, addictive.
Joining....is something I have been battling with from the beginning. In order to join two pieces of wood together invisibly you need to have a joint that is more or less perfect. In my experience, pressure during gluing won't help hide a bad joint. I've torn my hair out over years trying to get a good glue joint both for bodies and tops.
I think the problem is that to make a surface of a piece of wood flat (or straight) you need something that is flat (or straight). So if you want to use the shooting board method you need both a shooting board that is flat, and a plane that is flat. So to make a shooting board that is flat you need straight pieces of wood. But where do I get straight pieces of wood? Back to square one. And even getting a plane flat sounds easy, but in my experience isn't. Because you need a flat surface. And the Scary glass I have just isn't flat. Not even close.
So I've ended up using the router table and straight edge method. Even this isn't that straightforward (sorry for pun). Obviously you need to have a router table for one, and secondly your straight edge needs to be straight. I have 3 straightedges from Stewmac. Only one is straight enough to give a reasonable joint. I have (had) two straight edges from Axminster. Both were almost comically lacking in the single most important feature of a straightedge.
At the end of it all of that though, if you can find a straight edge that is straight then the router table method is reliable and very quick. As you say, joint one at a time to avoid amplifying gaps.
@Unknown_User The method you mention of putting the two pieces of the top in different orientations is if you are doing it on a jointer (or shooting board) and the fence (or plane) is not exactly 90 degrees. It means that if one is jointed at 89 degrees the other will be at 91 degrees and you still end up with a good join. That's a different problem to the one I've mentioned above. But will still give you sleepless nights just the same!
Rexel, welcome!
-
1
-
-
In between bl_ody Halloween preparations (I know, I know, and I agree with you, but how do you say that to a 3 year old?) I've made a bit of progress.
First up I glued the neck heel in place, and of course added in another pin stripe. Yippee! You may wonder why it's laughably oversized, poking way out of the neck pocket? The reason is that I knew I was going to want to rout it flush with the side of the neck so I needed it large enough to provide at least some stability on the router table. Thus:
So, putting the neck in and checking on height at the bridge? Really at this point there shouldn't be any surprises, cos I've measured several thousand times, but it's to within 0.5mm, so happy with that.
I then start to shape the neck itself. First of all I do the taper, going from 21mm depth at the 1st fret to 24mm at the 12th. As usual, I use a router to do this. It leaves a lovely flat (but tapered) surface for me to be able to draw on the facets that I use to shape the neck itself. Here's my taper jig. Like most the jigs I have they were prototypes that were supposed to replaced with better ones made out of baltic birch and beautiful machined clamps and stops and such like. The trouble is they work as they are, and I really really hate making jigs. If you are easily offended by crude MDF with router stops that are just taped on rulers, look away now....
Next up, neck carve. I started by doing the curved profile for the volute and the heel on the spindle sander, then started my usual technique of carving flat facets that give the neck it's rough shape, before filing/sanding off the sharp edges to leave what is hopefully a fairly standard C shape.
More on the neck carve tomorrow😁
-
4
-
-
-
Ok, frets filed. The second part of the process is to file them at an angle. One option which I like is to file 'into' the neck, so the angle takes off the sharp edge of the fretboard. Later I'll sand it so that it's a comfortable rolled edge. I also like the way with trimmed frets they look as though floating. And love Evo gold!
Now, at this point I can never resist putting two halves together to see what we have. Remember the body hasn't been sanded at all so ignore the blotchiness, that will disappear, honest. This is what I have in mind, more or less. Gold humbuckers, maybe black or cream surrounds....oh and maybe one of those floating type pickguard things that Gretsch always do....
-
10
-
-
Bit of progress today. First of all, I got the frets in. This is a always a bit nerve wracking. I press them in and the little buggers occasionally decide to jump around, gouging the top and leaving me in paroxysms of anger. Not this time though, oh no. Lovely well behaved frets. I'm using Evo gold, which look nice against the black ebony background that MOP dots...
Unlike most builders, I fly in the face of convention and sometimes don't glue in the frets. I've never had one come loose, maybe because I use a radial arm saw (and a stewmac blade) to cut the slots so they are a very consistent size. These ones went in very smoothly, tight but no issues, so they're going to be glueless.
As I go I check each one is seated properly (meaning I can't get the thinnest fealer guage underneath; 0.038mm), and when sighting down there's a consistent look to them...
I then cut the frets back as close to the side of the neck as possible before starting filing them flush. This. takes. forever. Even with a diamond file. And gives me tennis elbow, so I've only done half of it. Photo to follow tomorrow once I've done the other half. Looks lush though😁
Also today I finished the binding the f holes. I didn't find it easy at all. I always think guitar building is all about process, getting an order of jobs down that causes the least amount of aggravation. I can plainly state now that I will NEVER do f hole binding again on a guitar that has already had the top glued on. Having said that, it has turned out rather nice, even if not perfect - there are some gaps at the sharp pointy ends that need to be filled, but that's what epoxy is for, right?
I'm now officially looking foward to introducing the body to the neck😎
Edit: forgot to mention, that my technique for bending the binding (which in reality is just thin strips of constructional veneer) was just to soak them in water for a minute or two, then bend them by hand around a drill bit that was approximately the right size. No heat, just water. I found the key was not to soak it for too long. The ones I left overnight immediately split.
-
6
-
-
Just now, Si600 said:
I still think that you should stripe the inside of the headstock slots.
Just sayin' 😜
Oh for god's sake, will this never end?!?
-
3
-
-
4 minutes ago, SpondonBassed said:
Castor oil might help.
But yes, That'll add a touch of class.
Ouch! 😂
-
1
-
Shuker Custom J Build
in Build Diaries
Posted
Curved. Case closed😎