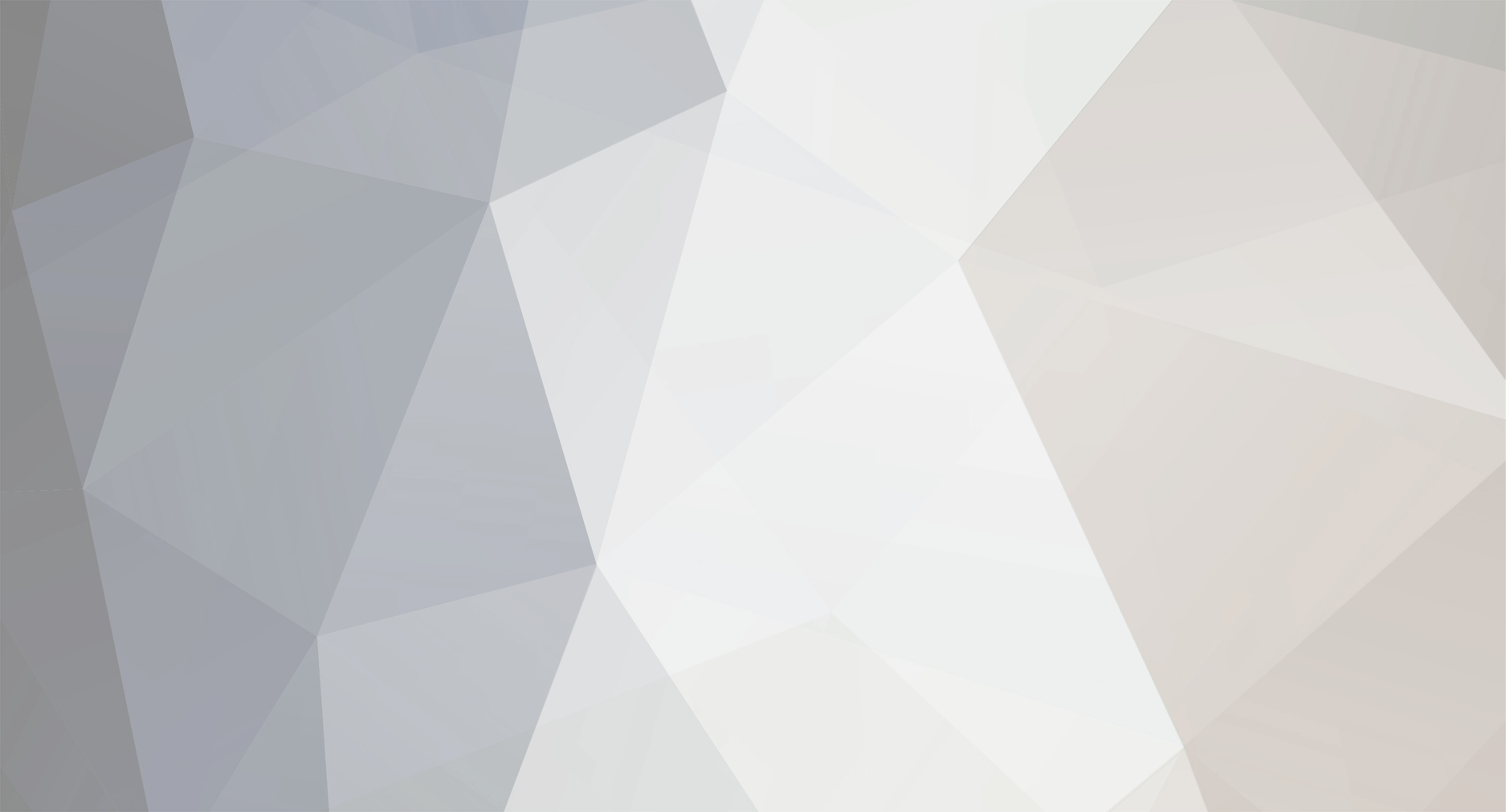
honza992
Member-
Posts
500 -
Joined
-
Last visited
-
Days Won
2
Content Type
Profiles
Forums
Events
Shop
Articles
Everything posted by honza992
-
Not too much of an update today other then side dots. Because the ebony board is quite attractive I've decided not to have lines, just side dots. However, because I can hardly play with frets, let alone fretless, I decided to have side dots at every position. To get the dots positions exactly consistent I built this jig (ok, saying 'built' is a bit of an exaggeration, and indeed calling it a 'jig', it's a bit of plastic screwed onto a bit of scrap....), which works really, really well. [attachment=252127:IMG_20170824_162716 (1).jpg] I've used cream dots for 3, 5, 7, 9 etc and white for the other 'in-between' positions. I'm not sure how successful that was, they're pretty similar. But they look kind of nice. [attachment=252126:IMG_20170825_122458 (1).jpg] That's it for today. Thanks for watching.
-
[quote name='Norris' timestamp='1503643635' post='3359837'] When you think you've got the two halves ready for joining, hold them together and hold it up to the light. If you can see any light it's not mated well enough yet. A long ("jack" is good or "jointing" is even better) plane with a nice sharp blade is the best tool for the job to get the surfaces really flat [/quote] Thanks Norris. I use the light method for thinner things like tops, and at some point I'll put together a light box. But for bodies that are over an inch thick I've never had much luck in using the technique successfully. I've spent ages with my face squished up on the side of a body join trying to see light. Maybe a light box would help with bodies as well. Would a cheap jointing plane (a quick internet search show a Faithful one for £37) do ok, or are handplanes like so much in woodworking, cheap is a false economy? At some point I'd really like to start using more hand tools. I use a spokeshave for the neck, occasionally a chisel for this and that, and although I've got a couple of planes I never really use them. I love the idea of creating less dust though. What I'd love to do is find an evening class or something. One day..... [quote name='SpondonBassed' timestamp='1503646822' post='3359862'] I can advise you on getting full contact at the mating surfaces. PM me if you are interested. Sanding is not good for keeping surfaces flat and it might be why you are seeing the glue solidifying in a gap. [/quote] Great, thanks, I'll drop you a PM sent, but also feel free to post anything here. [quote name='rubis' timestamp='1503672319' post='3360216'] There is an Americam forum called TDPRI, about Telecasters mainly (I know, Tele is a four letter word) but I love them, they are easy-ish to build, and the the variations on a theme nearly always look cool They have a Home Build section, some set ups are more professional looking than amateur, but one bloke in particular, named Scatter Lee does some excellent builds with tools typically found in an enthusiasts workshop, and is very good at building jigs or devices as solutions to a problem, very much a "can do" or should I say "can do without" attitude, when others seem to have a machine shop in their garage His 'gater photos are a nice diversion too I have wisely spent many hours reading his numerous builds, well worth a look and very educational [url="http://www.tdpri.com/threads/completed-scatter-lees-build.467702/"]http://www.tdpri.com...s-build.467702/[/url] [/quote] I agree with you, I love the tele. The strat always looked a bit polite to me. Ok, it probably new the difference between dorian and phrygian, but I bet the tele got more girls. And yes, TDPRI is a great site. I've spent countless hours there. I can honestly say that without sites like TDPRI, Talkbass and BassChat I would never have built a bass. The internet may be destroying the high street, our ability to communicate using real words and childhood innocence, but it has also provided me with endless help, advice and encouragement. Of course whether you consider that a fair swap I shall leave to you!
-
Oh and while on the subject of gluing (will it never end??) I also glued together the two halves of the maple top. I used (for the first time) the tent method, thus: [url="https://www.youtube.com/watch?v=vwjsIp44z3k&t=29s"]https://www.youtube....jsIp44z3k&t=29s[/url] It was dead easy to do, but.....I'm not sure about the results. I've only just done it so obviously it needs to dry for a few hours, but I can already see the deadly thin black line. It looks cool: [attachment=252013:IMG_20170824_121537.jpg] Pudding, proof, though. We'll see how it is tomorow.
-
On the subject of gluing, the fretboard/neck glue joint came out great. No gaps and the woods look great together! No photos cos I'm a tease. The body join is good if not quite perfect. There's a couple of points where you can see a very feint black line. [attachment=252011:IMG_20170824_123241.jpg] The joint is a few mm above my finger. It's hard to see in the photo. It's pretty hard to see in real life - I keep on losing it. The body is still a few mm too thick so I'm hoping as I sand a bit deeper into the join the line will disappear completely. I'll leave it a day and see how I feel about it - I can always saw it in half again and re-joint and re-glue..... I'm assuming that the black line is caused by having a joint which isn't completely true. Anyone else get this? Any tips?
-
[quote name='SpondonBassed' timestamp='1503565021' post='3359140'] I hear you re: creeping joints. [/quote] On this one there are no fretlines and I haven't done the side dots yet so it doesn't really matter if the fretboard shifts a bit anyway. On a fretted board though (and assuming you've already done the fret slots at the point of gluing) it's really critical to make sure there's no creep at all. Dowels and doing the clamps up slow enough to let the glue ooze out in a laid back fashion...that's my 1/10,000th of a bitcoin worth. If anyone else has got some good tips I'd love to hear them because I struggle with it every time.
-
Well today was something of a glue-fest. I felt like Paddington covered in marmalade. First up was the fretboard. I'm always nervous when using titebond to glue critical joints like the fretboard/neck. I'm worried the water content will cause everything to expand then retract in unpredictable ways. So I prefer to clamp the neck to something flat to try to stop any movement. I don't, though, have any kind of flat surface in the workshop - the table I have isn't even vaguely flat. So I did this..... [attachment=251950:IMG_20170823_093739.jpg] This is a mahogany body blank onto which I've clamped the neck/fretboard. (This is a dry run, before I put the glue on. No photos post-glue, far too much going on.) The mahogany blank also isn't entirely flat, so on top of that I put a piece of MDF then used a few layers of masking tape to make up for the slight sag that the mahogany had in the middle. It turned out to be surprisingly accurate a method. Two pieces of masking tape was enough to get the MDF base completely level. Gluing went pretty smoothly. One thing I have learned is.....patience. I take at least 5-8 minutes to do the clamps up. Every minute or so I give the clamps a further bit of a turn. This allows the excess glue to ooze out. It's amazing how you can do them up tight, then go back a minute or two later and they can be loose again. I also prepared the maple top for gluing. I jointed the edges by sticking the two halves together, sticking a straight edge on top then routing the edge using the same bearing-guided bit I used to rout the sides of the neck. Some light sanding and I hope it's ready to glue. I think I'm going to use the 'tape tent' method. But that's tomorrows update..... [attachment=251949:IMG_20170823_105833.jpg] Lastly I glued up the body blank. It's really a nice piece of mahogany. Bought from David Dyke who said it was from Fiji, and who am I to argue. I jointed the edges in the same was as the maple top then glued it vertically in my vice - largely because I no longer had a free horizontal surface. [attachment=251948:IMG_20170823_142904.jpg] And that campers was pretty much it for today. Tomorrow is squeaky bum time when I unclamp the neck. If the body join is rubbish I can always saw it in half again and re-glue it. The neck & fretboard is a different matter. I'm told you can heat up a butter knife to take off a glued fretboard, but that sounds complicated and painful. So let us say a short prayer to god of invisible glue lines...... Thanks for reading.
-
Couple of quick things. First, I should say that I don't advise you to take any of my advice. Or least not until you've double checked with someone who actually knows what they are doing. Second, let me know if there's anything you want to see in more detail. Or if I've bored you senseless let me know and I'll have single word updates from now on
-
First I prepared the blanks - neck thicknessed to 20mm and fretboard to 5.5mm. Next up is the truss rod channel. This is 1/4" wide by approximately 9mm deep. I used a router running along a straight edge. When using routers remember they go left. Meaning they will naturally pull to the left as they cut. Which is why you always lift the router up at the end of a cut, you never go back along the channel you've just made. The longer straight edge is the one guiding the router, and the shorter one is just there to provide support to the router base. [attachment=251872:IMG_20170822_112628.jpg] I rough cut the neck on the bandsaw then use a bearing guided cutter on the router table to rout it to its final shape. I use a template for the headstock but the sides of the neck I just use a straightedge. The advantage of this is that I can easily do any nut width and any string spacing at the bridge. I just stick a straight edge onto the top of the neck blank with double sided tape. It works surprisingly well. [attachment=251871:IMG_20170822_130036.jpg] My absolute least favourite part of building is gluing on the fretboard. It's always fraught, and I've completely buggered it up a couple of times, normally because the fretboard moves as you clamp. I've therefore developed a fool proof (even if not quite Honza proof ) method. I leave the blank a bit longer at the heel, and leave some excess below the nut on the treble side. I can then use two dowels when gluing to prevent the board from moving. At the nut end is a 3mm drill bit .... [attachment=251870:IMG_20170822_140755.jpg] and at the heel is 6mm dowel.... [attachment=251869:IMG_20170822_140810.jpg] I'm not gluing at this stage, just making sure that the holes for the dowels are drilled in the right place, ie with the board clamped absolutely flat on the neck blank. Finally today I prepared the neck for gluing. I put the truss rod in, then cover the channel with very thin masking tape. This prevents glue from getting into the channel and I leave it there, the fretboard just goes on top. I also put tape on the side of the neck so that glue squeeze-out oozes down the tape which can just be pulled off. Here's everything ready for gluing: [attachment=251868:IMG_20170822_144510.jpg] So with everything ready, I ....... went home. The single most important thing I have found about gluing is never ever ever ever (did I say ever?) do it last thing in the afternoon. If you are like me you will rush to get it done and you will boll_cks the whole thing up. Glue in the mornings when you are relaxed. I can't tell you how many blanks I have ruined by being in a hurry. So far so good. Perfection still a theoretical possibility. Sleep well.
-
OK, polls are closed. And the People's Choice is..... MAPLE and EBONY. Yeh! I have to say I nearly ignored the lot of you and went with maple and rosewood. I wasn't sure whether the maple and ebony was just a bit...busy. You know, that american thing of flame and burl and stripes and birds eye and quilt and veneers and bells with knobs on. Then I thought, no, the people have spoken. Who am I to resist the overwhelming outburst of popular opinion? So today work started in earnest. Standby for updates.....
-
Ok i was hoping to at least make a start on the neck this week.....but no. And tomorrow we are off to Wales for a week of wind, rain and sand in our sandwiches. Quite how the British even ended up with a word for 'summer' I don't know. Thanks all for voting. Any waverers among you have got a bit more time to consider the options.....
-
[quote name='SpondonBassed' timestamp='1502227589' post='3350165'] I will sand it to as good a contour as I can and just oil it. I like the idea of the grain texture looking and feeling almost as if it is not coated in anything. Also, I want to keep my first build simple. [/quote] You just want to be a bit careful with those finishes (like Tru Oi, Danish Oil, Teak Oil etc) that sound like they are oils, when in fact they are hard-drying, more like a varnish. What that means is that on open pored wood like ash, if you don't grain-fill the finish drops down into the pores, hardens, and becomes shiny. If you are after a satin type finish it's easy to rub with 0000 steel wool to make the flat parts of the ash satin, but it's really really hard to get rid of the shiny bits that are down in the pores. That's why ash is generally grain filled. Or at least that that's been my experience. I'd really advise you to test out your finish on a scrap piece of ash first - I realise this is a kit so if you don't have any scrap let me know and I can send you some. Or I may be completely wrong, and someone with more experience can chime in! I'd love to know how to do a 'hand rubbed' satin finish on ash without grain fill! I'm now on build 8 or 9 and finishing has been the worst part with all of them. I'm only now, finally, beginning to get my head round it.....
-
Looks great. Nothing like putting on that first coat of oil..... Speaking of which, what's your plan with the teak oil & the body? Are you doing a grain fill on the ash?
-
Spent the day mulling. If I use the rosewood board then I will use full veneer lines, if I'm using the ebony board then it will be unlined (side dots only).
-
Help me choose some wood. Surely everybody's favourite time, when the illusion of future perfection is still possible..... OK, I'm going to give you 4 options, two choices of top and two choices of fretboard. The top can either be flamed maple or spruce. The fretboard can either be rosewood or ebony. The ebony is unusual in that, well it isn't black. It is though quite dramatic. So here are the four possible combinations. Ignore everything other than the wood itself - the knobs are practice ones that I had lying around, the bridge I made for the previous version (and won't be reused) and the pickup is a random jazz cover. So, here they are: Option 1: Flamed maple top and Rosewood Fretboard [attachment=250904:IMG_20170808_105054.jpg] Option 2: Flamed maple top and Ebony Fretboard [attachment=250903:IMG_20170808_105028.jpg] Option 3: Spruce top and Rosewood Fretboard [attachment=250902:IMG_20170808_104700.jpg] Option 4: Spruce top and Ebony Fretboard (with free feet....) [attachment=250901:IMG_20170808_104627.jpg] It's a bit hard to fit in all of the fretboard in the photos, so here they both are in a full frontal shot..... [attachment=250905:IMG_20170808_110339.jpg] And if I can work out how to do it, I'll add in a poll so you can vote. Presuming of course that you give monkey's.... Edit - OK, the poll is up and running. VOTE VOTE VOTE.
-
Wow, so many great things in this build. Love the beech. Is it soft by the way, like spalted maple is? For some reason in the the photos it looks hard. (Why do my comments also end up sounding like double entendres? They're not supposed to be, honest) I'm just about to build a piezo bass with an artec and a Cafe Walter pre amp, so really interested to see how yours ends up. I've never heard of Shadow, and didn't know of the existence of that John East MPM01 either, so this is already worth the price of entry. Do you mind if I ask a question? I see that you are gluing the top onto the two halves separately. I think I've mostly seen people do it the other way round, ie glue the top together, glue the two halves of the bottom together, then stick the top on the bottom. I've sheepishly copied this method without really thinking about it. Why do you do it the other way? Does it make jointing the two edges easier?
-
[quote name='Andyjr1515' timestamp='1502047956' post='3348996'] Hi, Honza Welcome! I share your interest in ergonomics and weight - I've been doing quite a bit of work myself in that area over my last 4-5 builds and I think there is a LOT of potential with some relatively modest design changes. I'm Derby so would be very pleased to [s]drool over your drum sander[/s] talk through the various successes and failures sometime. I'll drop you a pm. In the meantime we are all very interested to see how your present project develops and, if you encounter any challenges or uncertainties, just ask anything at all - there is bound to be someone dropping along who can help Andy [/quote] Great, thanks for the post Andy, look forward to hearing from you. Agreed re modest changes, particularly with neck dive. I aim the strap button to be level with at least fret 11, the bridge to be as close to the other strap button as is aesthetically and practically possible, and ultralites. The holy trinity! And no neck dive means the body can be lighter, thinner, chambered etc......Of course I'm only building P basses.......
-
[quote name='SpondonBassed' timestamp='1501945030' post='3348396'] Not so far away as I'd first thought then. I got the notion that you were abroad for some reason. Brain fart probably. If you are into ergonomics then you must have read this; [url="http://basschat.co.uk/topic/303531-navarone45-43multiscale-headless/"]http://basschat.co.u...scale-headless/[/url] A maple fret marker inlay on ebony would be striking. On rosewood it would still be stunning. I understand ebony is not the easiest of materials to work with though. Oh and Welcome to the forum. I know you've been here for a bit but it's good of you to pull up a chair and share your build story with us so to speak. [/quote] Yes, I had seen that thread. Now that is ambition. Headless, Fanned fret, torzal.... It makes me feel slightly seasick just looking at it. One day though, you never know. The headless thing is definitely very close to being next on my list. One of my favourite builders is an Italian luthier called Biarnel ([url="http://www.biarnel.com/liuteria/scorcio/seriescorcio.html"]http://www.biarnel.com/liuteria/scorcio/seriescorcio.html[/url]) who's based in Pisa close to where my wife is from in Italy. I love his headless series called Scorcio. They have a slight....80s feel to them. Which, having grown up in the 80s I quite like. Now you've got me thinking I've used veneer fret markers with rosewood and it looked great. The same as ebony though one problem is sanding dust getting into the pores of the veneer. I don't have an air compressor so it's hard to get out and you can find the veneer markers look a bit 'dirty' from the dust. It's not bad, and probably the average person wouldn't even notice, but that's the trouble with building....you know where every mistake is. I read once (though now can't find the link) about soaking the veneer markers in shellac first, to fill in all the gaps in the veneer so the ebony sanding dust has got nowhere to go. I may do a bit of experimenting this week - I've got a bottle of Zinsser SealCoat (which as far as I know is 2lb cut shellac) and some veneer so we'll see. Thanks everyone for the welcome. Biscuits all round.
-
Brilliant. I fully intend to steal this technique in its entirety. Particularly for pickups, all the templates I've ever tried have been a waste of money and good Mdf. Thanks for posting.
-
[quote name='Norris' timestamp='1501925139' post='3348228'] Welcome. Colour me jealous that you have a drum sander I have to make do with good old elbow grease. [/quote] The gods smiled on me as I found it on eBay, cheap, and for sale just up the road. It looks like it was lying in someone's garden under a pile of nettles for a decade, but works perfectly! The offer's a serious one....
-
Yes, of course, a few words of introduction. I'm 47, live in Nottingham, and have the incredible good fortune to have a pretty well equipped workshop in the centre of town, a few yards from Nottingham Trent Uni, if anyone is from round here. I've been building as a hobby for a few years, only for myself, with painfully slow progress. I'm beginning to gain a bit of confidence and competence, but for now I'm really focused on simple builds that will allow me to perfect the basic techniques before moving onwards and upwards. I'm also really focused on the ergonomic aspects of building. I suffered from tendinitis for a while, so perfect balance, scale length and weight are important to me. It always amazes me how poor so many basses are in that respect..... Anyway if anyone is local and wants to pop in and say hello drop me a line. Or if you've got a top you want to put through a drum sander, or want to cut some frets on a radial arm saw or whatever then I'd love to help out. Though I have a pretty expensive taste in biscuits in return...... I hadn't thought about the dremel. I'll dig it out and have a think. My initial plan though was to use maple veneer as I would on a normal fretless fret marker.
-
[size=4]OK, shall we all try this again? From the top? Here goes.... [color=#000000][font=Arial]Hi All[/font][/color] [color=#000000][font=Arial]This will be my second build thread. The first is on a bass forum where there’s more talking than chatting, if you know what I mean. Largely because I didn’t know you all existed. I know I know, my invite to the good times got lost in the post. Well I’m here now, so it’s Blighty for me from now on. [/font][/color] [color=#000000][font=Arial]I build for a hobby. And for the moment I build P basses. Which I realise will cause most of you to turn back to Love Island. Not that I don’t want to someday build Carl Thompson-esque masterpieces for the adoring masses, but for now a P is challenge enough….[/font][/color] [color=#000000][font=Arial]That said, I want a fretless. So I’ve decided to build this. Or, for the lawyers among you, I’m going to build something inspired by this. [/font][/color] [attachment=250649:TLB1.jpg] [Edit - for those of you that haven't seen one before, it's a Fender AE Precision, made in Japan, briefly, in the 90s. They weren't a success!] [color=#000000][font=Arial]Actually it will be my second version. But this time I want it to be perfect. [/font][/color] [color=#000000][font=Arial]Honza, shut up and show us some wood….[/font][/color][/size] [attachment=250652:IMG_20170728_121258.jpg] [size=4][color=#000000][font=Arial]OK, and some rock solid decided fo' sho specs:[/font][/color] [color=#000000][font=Arial]Fretless[/font][/color] [color=#000000][font=Arial]Mahogany (chambered) body[/font][/color] [color=#000000][font=Arial]Flatsawn maple neck[/font][/color] [color=#000000][font=Arial]33” scale[/font][/color] [color=#000000][font=Arial]18.5mm spacing at bridge, 40mm nut[/font][/color] [color=#000000][font=Arial]Hand made wood & bone saddle bridge & knobs[/font][/color][/size] [size=4][color=#000000][font=Arial]Piezo under the saddle with Cafe Walter preamp[/font][/color] [color=#000000][font=Arial]And some specs open for negotiation:[/font][/color] [color=#000000][font=Arial]Lined, unlined, or partially lined (if I can work out how to do it. How do you cut a slot only part way across the board? Any ideas?)[/font][/color] [color=#000000][font=Arial]Ebony or Rosewood board[/font][/color] [color=#000000][font=Arial]Maple or spruce top with single ‘f’ hole. The original Fender AE had a spruce top. Which I like, but I think I may want it a bit more pimped. So flame maple? Possibly dyed? In the photo the maple is on the left, spruce the right. [/font][/color] [color=#000000][font=Arial]Black, white or Black & white binding[/font][/color] [color=#000000][font=Arial]Single Jazz pickup in the bridge position (ie no P pickup at all)[/font][/color] [color=#000000][font=Arial]Finish-wise it will have a water base clear coat (General Finishes High Performance) which I’m using on my other build. Probably satin. [/font][/color] [color=#000000][font=Arial]For the top, if I decide to go with the Spruce then I think it will be natural. If its flame maple then I quite like this:[/font][/color] [attachment=250648:ctvp153a.jpg] [color=#000000][font=Arial]My goal is to hit 3kg total weight. [/font][/color] [color=#000000][font=Arial]Any thoughts?? Hit me. [/font][/color][/size]
-
Given that my 6 year old IT Consultant nephew is in bed, rather than just laughing and pointing can anyone help me out? Ped's video is all very well and good and lovely, but I can't see the "attach" button.... [Edit - yes I can, hold on, I'm coming] [Further edit - this must be the least convincing start to a build thread ever]
-
[quote name='TheGreek' timestamp='1501872376' post='3347997'] Is that what Mrs Honza says? [/quote] As I always say, I've never had any complaints....In writing.....
-
The photo that is. Fu_k me I hate technology. I'm using google, I've got a shareable link, but when I put it in here using the 'Image' button it comes up broken. ARRGHHH (I used to be able to do this on basschat. I'm getting old.)
-
[font="Arial"][color="#000000"][size=4]The trouble is I just can't get it up...[/size][/color][/font]