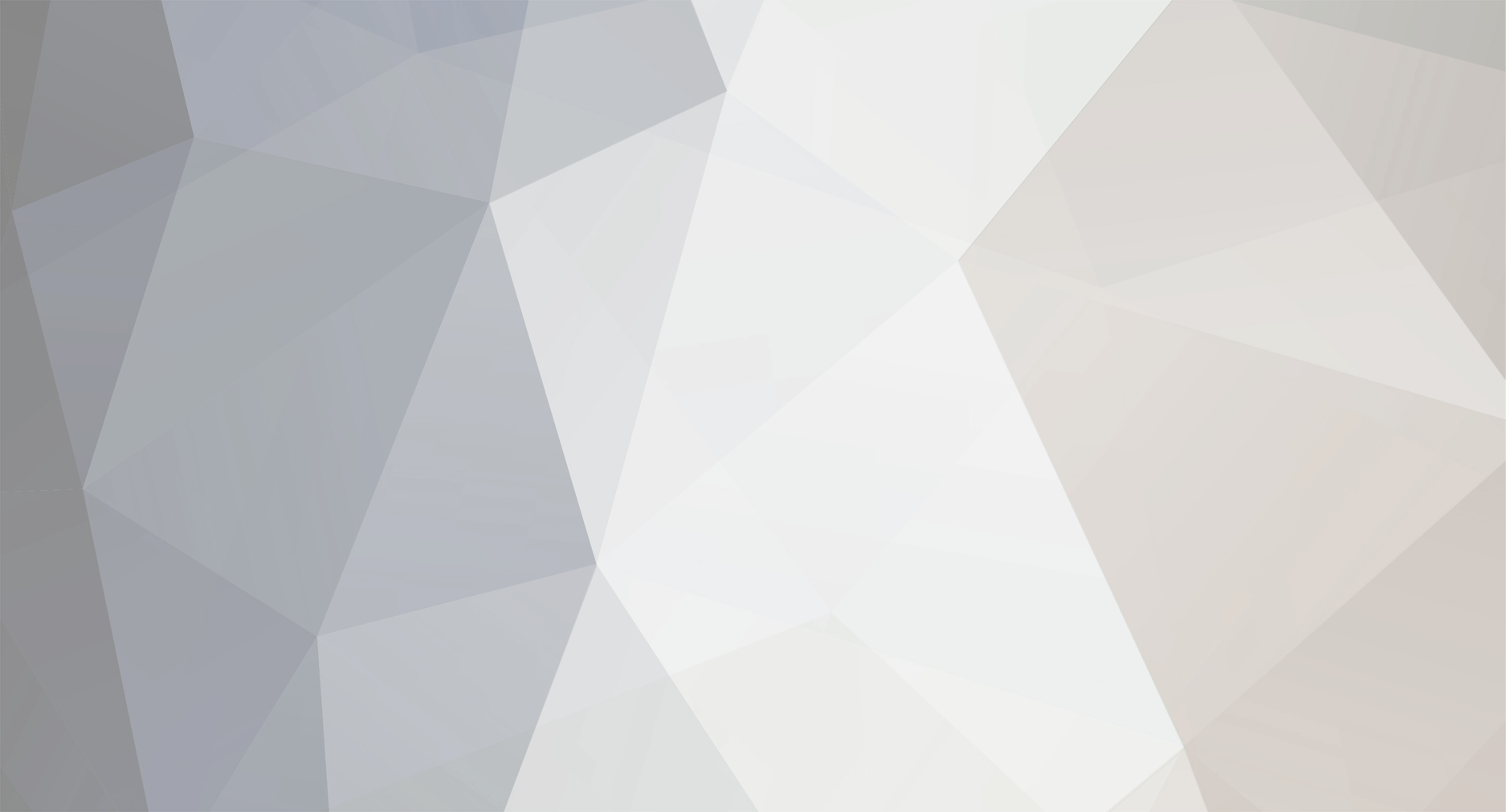
honza992
Member-
Posts
520 -
Joined
-
Last visited
-
Days Won
2
Content Type
Profiles
Forums
Events
Shop
Articles
Everything posted by honza992
-
33" Reverse P/J Jazz bass, blocks & binding (FINISHED PICS)
honza992 replied to honza992's topic in Build Diaries
Oh my oh my oh my. That's some lovely shiny shimmering lovelyness right there! (And I'm leaving my MOP as is. Actually I designed it that way from the beginning.....😁) -
I think I agree with @Jimothey I use a router with a guided bit, which more or less does exactly what a CNC does. If you think about it, that bearing is a primitive CNC! It reproduces a shape with only minimal intervention from me. I think the difference in mechanisation at this point is one of degrees. I don't use CNC because I build for the (non financial) reward it gives me. So I'm not sure using CNC would help that much. I think the key is customisation and developing a customer experience that goes beyond simply walking into a shop and picking something off the shelf. A custom builder has the opportunity to work with the client to build something that is designed for them, but also something where they have helped chose the wood, the binding, the finish etc etc . That's my goal anyway. But there's no way I would ever be able to do that to pay a mortgage.....Not when competing with CNC.
-
I think everyone here builds without CNC. Though admittedly not commercially. I don't think it's possible to earn a living making guitars without using CNC.
-
I'd like to take a look, though I'm a builder more than a player, and by the looks of it your skills are already up there. But I would give an honest opinion re build, fit, finish etc. I'm in Nottingham.
-
Ho...ly....cow... Your sanding is amazing. Really outstanding. Awe-inspiring. Curves...light and dark woods....that's hard to get clean lines. But you get it looking like it has been forged in bass heaven. No stray sanding dust, beautiful sparkly clean lines.....You are literally killing me😲 Any tips for us mere mortals?
-
33" Reverse P/J Jazz bass, blocks & binding (FINISHED PICS)
honza992 replied to honza992's topic in Build Diaries
More of an issue is this.... All the blocks are white, apart from the one at the fifth fret (block 3) which is blue. What the...?!%@%! I didn't notice before because they were only rough sanded, but once glued in and starting to sand it was obvious that it didn't match at all. This is the first time I've used MOP and as a natural material I'm sure there is some variation in hue, but that is ....well, a bit much. Very disappointing. I guess I have two options: 1. Grab my router, and zap that little bugger. Hope I can get it out relatively neatly and re-rout the channel. Get the retailer to send me one that is the correct colour, re-glue, re-radius and put it all down to experience. 2. Relax. It is at least at fret 5, so I can pretend that it's a design feature. And no one will notice apart from me anyway. Anyone with any opinions? (Oh and also I'll email the supplier and ask whether that blue is in fact within the accepted range of 'white'....🙄) -
33" Reverse P/J Jazz bass, blocks & binding (FINISHED PICS)
honza992 replied to honza992's topic in Build Diaries
A quick update on the neck. The blocks are in, glued and the neck radiused. It's.....ok. Not great, but for a first effort it's acceptable (the fill around the blocks is a bit too obvious for my liking), but I learned loads and next time it will be one hell of a lot better. A quick shot hiding the imperfections... Next time I will do the gluing a little bit better, because I think the way I did it this time contributed to a slightly sloppy job. This time I used epoxy and sanding dust to glue the blocks in, and in my head I had imagined the epoxy oozing up around the block, filling the gaps around it at the same time as gluing. And that is what happened, at least to begin with. What happened next though, was that the expoxy then sank down again, I think as the blocks rose up a little bit. So next time I will divide the gluing and the filling into two completely seperate stages. First I will glue the blocks in with a small amount of medium CA glue, using only enough to cover the bottom of the channel but no more. Then, once dry I'll use either epoxy or medium CA glue with sanding dust to do the gap fill. Oh, and the other thing I need to work on is my chisel technique, both use and sharpening☹️ But all in all, ok for a first effort. -
Here's a couple of mine..... (Edit: Mods, am I alowed to post my own? If not, please delete!😁)
- 13 replies
-
- 11
-
-
33" Reverse P/J Jazz bass, blocks & binding (FINISHED PICS)
honza992 replied to honza992's topic in Build Diaries
Wow, that's an incredibly kind officer and a gentlemen. You're but a mere hop skip and jump away. I may very well be getting back to you....Thanks again. -
33" Reverse P/J Jazz bass, blocks & binding (FINISHED PICS)
honza992 replied to honza992's topic in Build Diaries
So, I'm guessing you don't all love the idea then😋 I guess part of my issue (apart from being lazy🙄) is that I have no metal working tools at all - files, drill bits, countersinks, saws etc etc. I'm reluctant to spend yet more money on tools.....no, hold on, who am I kidding. I'm reluctant to spend money on clothes, or the bus....I'm joyful to spend money on tools 😀......though on my tool wish list, metal working tools come below woodworking..... I'll have another think.... -
33" Reverse P/J Jazz bass, blocks & binding (FINISHED PICS)
honza992 replied to honza992's topic in Build Diaries
I'm pretty sure the answer to this is...no, clearly not, what were you thinking you complete numpty.... ....but is there any reason why brass can't be routed? Make a template for the plate from 12mm mdf, sandwich 2mm brass stock with another piece of 12mm mdf then trim it on my router table with the speed as low as possible. Just, you know, a thought😋 -
33" Reverse P/J Jazz bass, blocks & binding (FINISHED PICS)
honza992 replied to honza992's topic in Build Diaries
Thanks Jez, I'd be really interested in the chrome plating idea. Doing my own plate would be the ideal solution. How difficult is brass to cut and shape? -
33" Reverse P/J Jazz bass, blocks & binding (FINISHED PICS)
honza992 replied to honza992's topic in Build Diaries
I'm a great one for never following my own advice. Part of which is ALWAYS have all hardware to hand for doing layout before starting to cut. Paticularly if you're doing non-standard scale lengths (which I normally do🙄) because that throws everything out. So anyway, there was a delay on receiving the control plate, but it's only a control plate, right, no need to delay building....? Wrong. Goddam it. It hadn't occured to me that a 33" scale and more ergonomic design means that everything is shifted by about 2 inches in comparison to a normal fender 34 inch. So if the control plate is in the right position, nicely parallel with the side of the bass, it's completely mis-aligned with the pickups.... Or if I align it right with the pickups, it's completely misaligned with the side of the body. And that's the sort of thing that would give me sleepless nights.... Ho hum. I think the best solution (other than following my own advice) is to fill in the Precision pickup rout, and re-rout it a centimetre or two nearer the nut. That will just allow enough space for whole pickup to be underneath the pickguard. Though obviously means the tone will be slightly affected. The other option that occured to me, was to reverse the two halves of the P. Fender themselves do it with the Mark Hoppus jazz... The thinking is that the bass strings are a big tighter sounding (being a bit close the bridge) and the top two strings are a bit warmer. Or at least I think that's the idea. Anyone tried out a reverse P? Maybe I'll do that, edit the thread title, hope no one notices and pretend that was my intention all along😏. Any opinions? -
33" Reverse P/J Jazz bass, blocks & binding (FINISHED PICS)
honza992 replied to honza992's topic in Build Diaries
Today I glued in the MOP blocks. I used West Systems Epoxy which is great, but is a pain if you are only using small quantities, as I normally do. So I've started using medicine syringes to meausre out very small quantities, taken direct from the can. No waste, no scales, no hassle. I use a children's Nurofen syringe for the Resin (half a syringe is 2.5ml) and a Vitabotics one (0.5ml). It really works great, and a vast improvement over the pumps that West Systems sell that only measure out large quantities and leak all over the place. And cost twenty quid... I started off with some rosewood sanding dust (400 grit) but on my test piece I found that it was a bit light. So I added some black powder, in this case Behlen's black furniture powder. It's been sitting on a shelf for years and I've never used it. No idea why I bought it, but this seemed like the ideal time to bring it out. Anyway, I added maybe 20% black to end up with this... Then I syringed on 2.5ml of resin onto the top of the sawdust, mixed it well then added 0.5ml or 205 hardener. Mixed it well for a minute or two, then glued on the blocks... Following @Christine's advice, I just held them in using finger pressure, no clamps or anything. Tomorrow I'll sand, and judgement will follow😲 -
33" Reverse P/J Jazz bass, blocks & binding (FINISHED PICS)
honza992 replied to honza992's topic in Build Diaries
He he 🤣the neatness of the work (and the camera in this instance slightly exaggerates) is inversely proportional to the utter, complete, all encompassing, overpowering and overwhelming mess and chaos in the workshop 😧 I need to have more visitors, cos it's the only time I tidy! -
33" Reverse P/J Jazz bass, blocks & binding (FINISHED PICS)
honza992 replied to honza992's topic in Build Diaries
A bit more progress on the neck. Lots, and lots, and lots of tape.... Then on to sanding the radius.... Man I love rosewood. It's just so beautiful to work with. I know the CITES restrictions are for our own good, but every time I think about it I feel genuine sadness. 😢 -
Wow, that's a work of art! I use an equivalent which is a 3mm slot routed in some mdf. Keeps the nut nicely at 90 degrees when sanding. Works surprisingly well😎
-
33" Reverse P/J Jazz bass, blocks & binding (FINISHED PICS)
honza992 replied to honza992's topic in Build Diaries
Mock-up time. I'm usng what (I think) is standard 60s pickup placement for the bridge - 8% of scale length away from the bridge. The P will be what is standard for a precision, 16%. Tomorrow I'll get the templates done and start routing😁 -
33" Reverse P/J Jazz bass, blocks & binding (FINISHED PICS)
honza992 replied to honza992's topic in Build Diaries
Next up, pickups. Guess what's in this beautiful box? Pickups! Yay😁 They're a matched '62 set from House of Tone. Now, I don't like to complain. I chose them because I wanted to use British made artisan pickups. I'm sure they're going to sound great. But if you were a boutique pickup maker wouldn't you spend an hour or two making a template so a nice and neat pickup hole can be routed? Pickups are all slightly different sizes. And the generic templates are rubbish (and I've got plenty of them). Clearly, you must have a drawing in CAD for the moulds to have been made......I don't know....maybe I just expect too much, but I'd happily pay a fiver for a template to save me the couple of hours it'll take to make my own. Anyway I guess the important thing is how they sound....... -
33" Reverse P/J Jazz bass, blocks & binding (FINISHED PICS)
honza992 replied to honza992's topic in Build Diaries
A little bit of progress today. First up, binding. On @Norris 's advice I took another look at the binding issue. The binding I had been trying was ABS plastic and was a pain to bend - either it was straight or it was melting. So I ordered some celluloid binding from Rothko & Frost and the difference is obvious. Here's a test piece that I was easily able to bend using a hairdryer... So bindings are back! Hurray! Here with the channel cut... Celluloid rocks🎸😎 -
33" Reverse P/J Jazz bass, blocks & binding (FINISHED PICS)
honza992 replied to honza992's topic in Build Diaries
@Andyjr1515 Andy, having now done the routs for the blocks, I would strongly endorse what Christine says here. Trying to score round a wobbling piece of MOP on a radiused board would be a nightmare... -
Now you have a router table, have you thought about using router bits? They're available in the UK and (reasonably) cheap... https://www.amazon.co.uk/Yonico-13005-Radius-Guitar-Radiusing/dp/B06W2M7892/ref=sr_1_1?ie=UTF8&qid=1536173060&sr=8-1&keywords=fretboard+radius+router+bit I've got a similar 12" one and it cuts scrap beautifully. I'm still trying to work out though how to fit it into my normal work flow ( I normally glue the board on first, which is problematic). I think you radius then glue? Supposedly that's more easy to do.
-
I've seen those and was tempted....the only issue I could see (other than the cost, clearly) is that the base of the radius jig itself aren't wide enough to take a 5 string bass fretboard. The max width is 70 mm (I checked with G&W) which isn't really wide enough. I can't understand why you would go to all that trouble to spec, design and produce (what I presume is) a top quality product, but not make it 10mm wider. What luthiers only make 6 string guitars? Surely a 5 string bass is the minimum you would design for. Very very odd. And a great shame, and opportunity wasted.
-
33" Reverse P/J Jazz bass, blocks & binding (FINISHED PICS)
honza992 replied to honza992's topic in Build Diaries
OK, nice tip about the acetone. I'll give it a go. Thanks! -
Finished Pics! Dreadnought acoustic (guitar) for me?
honza992 replied to Andyjr1515's topic in Build Diaries
Nothing constructive to contribute other than admiration. I hoestly believe that if you can craft an acoustic then you are a luthier. The rest of us are just builders. Great work. Carry on!