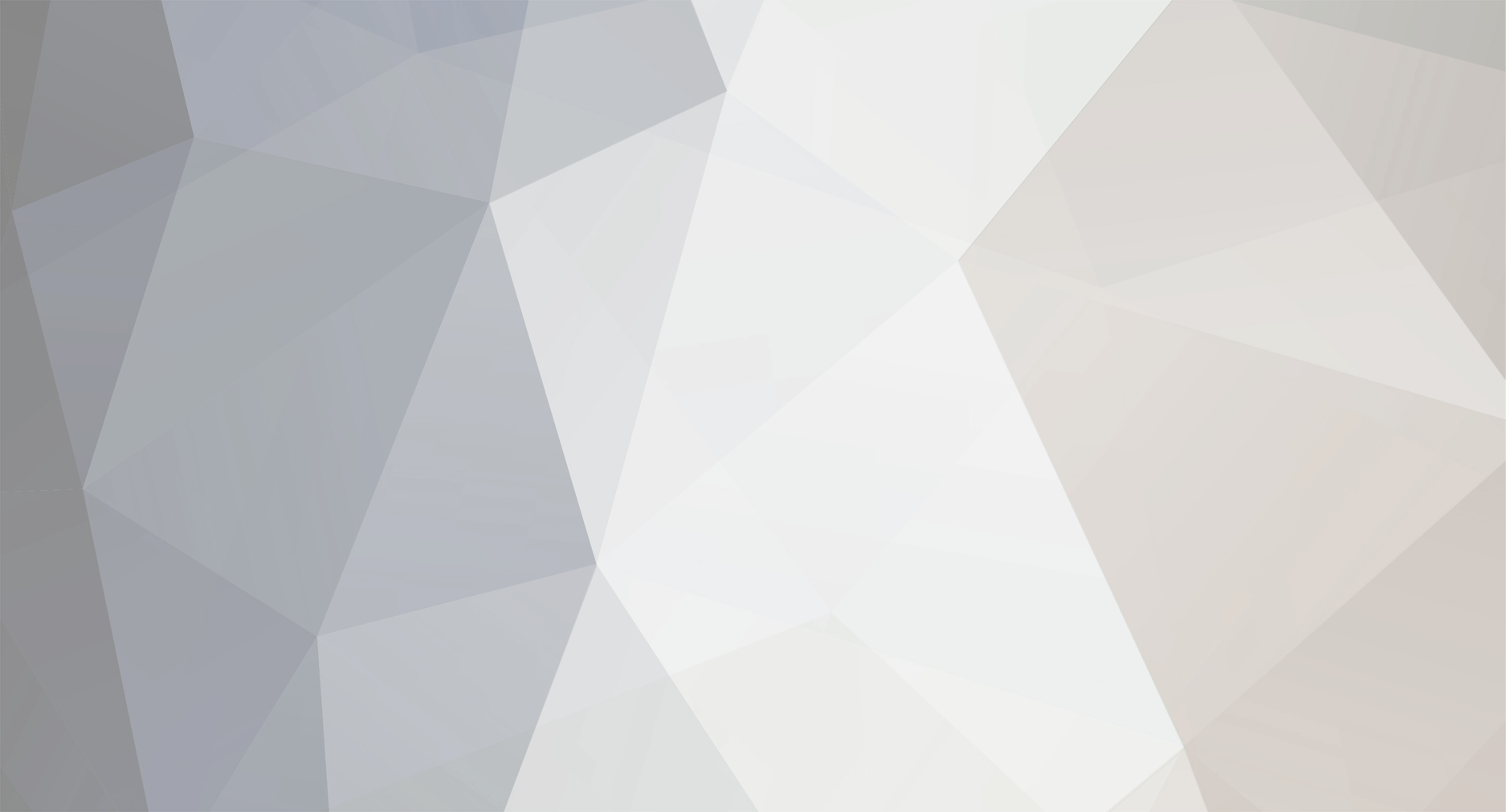
honza992
Member-
Posts
520 -
Joined
-
Last visited
-
Days Won
2
Content Type
Profiles
Forums
Events
Shop
Articles
Everything posted by honza992
-
I did a few more adjustments today, including shaving down the height of both the saddle and the bridge so that with a small amount of relief in the neck I have a string height at the 12th of approx 2.5mm on the E and just under 2mm on the G. Does that sound about right? It's higher than my fretted bass (which I have very very low) but I'm thinking with fretless its better to have a bit more space. The bass is a 33" scale, Re-doing the intonation has meant that I have ended up with quite a lot of compensation - 8mm on the E and 6mm on the G. Maybe that's not so much given it's a slightly shorter scale - my 34" P bass with a very low action has something like 5mm on the E. TIme to stop muckin around Honza, just drill the goddam holes!
-
[quote name='Andyjr1515' timestamp='1508456331' post='3392393'] ^ this. As fftc says, move the bridge, retune to pitch, then check the 12th harmonic against the 12th fretted. Excactly the same thing happens on a conventional bridge when you adjust the intonation.... [/quote] Thanks fftc & Andy. Well blow me down. As Andy says, the same thing does happen with a conventional bridge. If you play an open E then adjust the saddle so the string gets longer the pitch (of the open E) actually goes up, not down! Weird How could I never have noticed this before.....I think it must be because before moving the saddle I would de-tune, move the saddle, then re-tune, so I never actually noticed what the effect was of moving the saddle. I'm still a bit unsure as to exactly why. And does the fact that I'm using a secondary bridge to hold the strings mean that they act differently (and will intonate differently) when the strings go through the body? Or is it completely irrelevent what happends to the string once it's gone over the saddle?
-
Ok, I think my brain has melted. The little one has Foot n' Mouth (no doubt from kissing sheep or something) so sleep has been hard to come by. I'm trying to position the bridge so that the strings intonate correctly with the side dots. Rather than guesstimate this time I thought I'd do it more precisely so I made another of my attractive jigs. And here it is.... The strings are held by a secondary bridge and tuned to pitch as usual using a clip-on tuner. The plan was that I can move the bridge up and down until everything intonates correctly, then I can mark the position and drill the holes through the body for the strings. That was the theory, and I've seen other people do it this way on that there t'interweb. The trouble is if I tune the strings to the correct pitch then shift the bridge slightly towards the secondary bridge, ie making the string longer, the pitch goes up rather than down! What the ?!?!?! For example, if I tune open E correctly then play E at the 12th but find it's a bit sharp, if I move the bridge a few mm to effectively make the string a bit longer the pitch goes up. Which was not what I was expecting. I'm assuming the reason is because as I move the wooden bridge towards the secondary bridge the vibrating length gets longer (which would lower the pitch) but the tension goes up. But either I'm too stupid or too tired (or both) to work out why. Does anyone have any ideas what I am doing wrong? Is this jig ever going to do what I want it to do? Edit: I think I've made it sound a bit complicated. I play an E string. I tune it. I then move the wooden bridge away from the nut, making the string longer, and the pitch goes up, not down.....
-
Wonderful neck joint! What oil are you using for finishing? Same for neck & body?
-
I'm still doing experiments with finishing. It's made more complicated by the fact that the fretboard is primarily brown, and it really doesn't go well with anything amber. For the top I'm therefore going to use the Osmo Raw that Andy used on Psilos, probably coupled with a brown stain and sand-back to emphasise the flame. The back is causing more problems. It's a pretty pale mahogany that I would like to darken to increase the contrast with the top. Like with the top, anything amber (or red) just doesn't go with the fretboard.... So I'm thinking something like this: 1. Sand 2. Dye black 3. Sand back so black dye only remains in the grain 4. Dye brown 5. Osmo Satin Does that make sense? Or am I better to use a black grain filler rather than black dye in step 2? I'm happy not to grain fill from a feel point of view, but I do want the mahogany to be a bit more interesting. Just Osmo leaves it a pretty uninspiring slightly murky brown/amber. Cheers all.
-
Finished Pics! To the dark side Build One - Alembic-esque Electric
honza992 replied to Andyjr1515's topic in Build Diaries
[quote name='honza992' timestamp='1506938443' post='3382056'] Andy that looks amazing. Stylish but subtle. I'm sure you've seen this idea before for sanding fretboards, but adding handles looks to be a great idea. I bet it helps with applying even pressure and hand cramps! I keep on meaning to do it but never get round to it..... I stole the photo (I'll return it, honest) from the Simnett Guitars website. [/quote] Andy, rather than adopt the elegant approach that Simnett Guitars takes, I decided I would try sticking two lumps of mdf onto my radius block with double sided tape...et voila: [url="https://ibb.co/hOWVJw"][/url] Very ugly, but really made a huge difference. Just in case you haven't come across them.....on the subject of radius blocks, the one I've got is from a site called G&W ([url="https://guitarsandwoods.com/"]https://guitarsandwoods.com/[/url]). To me it looks exactly the same as the stupidly, ridulously, outrageously expensive Stewmac ones, but is a third of the price - £41.10 against £113.54. I only ever use 12" radii, so buying one wasn't too much of a problem. I highly recommend them. -
[quote name='SpondonBassed' timestamp='1507539864' post='3386073'] I hope I haven't misled you into thinking that the links I provided are for helicoils. They aren't. They are for solid inserts. The link you posted is suitable for wood as well. This link shows the helicoil a bit better; [url="http://www.toolsinstock.com/search?q=helicoil+birmingham"]http://www.toolsinst...coil+birmingham[/url] I shouldn't have mentioned them in retrospect as they really only work for metal parts. It was the question of how they are driven into the parent component that made me think of them. If you look closely at the third photo down you can see where there is a notch in the wire insert to allow the tang to be broken off. [/quote] All understood. The inserts I use are like the ones you linked to. I still like the helicoils for their elegance! There's a video on their site which shows how they work - very cool.
-
[quote name='SpondonBassed' timestamp='1507462001' post='3385553'] I can only think of heli-coil inserts used in light engineering. They have an internal tang that provides the drive when installing the insert. The tang is then snapped off with a reverse twist of the installation tool. It is sometimes called a wire insert as it is fabricated from wire that has the inside and outside thread forms in cross section. Probably not suitable for wood. They used to be used for things like engine exhaust manifold studs where they've pulled the old thread out from the head. This might help; [url="http://www.lawsonproducts.com/images/DV_WebLarge_P_635_LD2.jpg"]https://www.lawsonpro...e_P_635_LD2.jpg[/url] [url="https://www.lawsonproducts.com/lawson/Wood-Thread-Insert/96747.lp"]https://www.lawsonpr...Insert/96747.lp[/url] [/quote] Thanks SB. I've never seen those heli coil inserts before. They look fantastic, a really elegant solution. A quick google search shows amazon sells an M5 kit for £13 including a tap, drill bit etc etc: https://www.amazon.co.uk/Silverline-127589-Thread-Repair-Helicoil/dp/B001C7QYB4/ref=sr_1_2?ie=UTF8&qid=1507484881&sr=8-2&keywords=helicoil+kit I think I would still want to have the tap in a drill press so that it was at 90 degrees to the wood. I may well give it a try at some point. Another possible solution has occured to me. The inserts I've been using are hex-driven. So one method I tried in the past was to put a short piece of hex rod into my drill press then drive the insert into the neck using that. The problem I found was that the M5 threaded inserts (which I buy from here http://www.theinsertcompany.com/index.php ) are supposedly sized for an M5 allen key. However either the hex hole in the insert isn't exactly 5mm or the hex rod I had wasn't accurately 5mm, but there was so much slop that the insert wasn't being driven in at 90 degrees. It occurs to me though that maybe buying 4.5mm hex rod (or alternatively a 4.5mm allen key then cutting off the short side) then sanding it down so that it was a tight fit in the insert would also work. Again, I'll give it a go at some point.
-
[quote name='Si600' timestamp='1507284177' post='3384460'] How do you screw the inserts in? I'm refurbishing a garden bench at the moment, and on all the inserts I've seen the thread goes all the way through, so using a threaded rod like that won't screw the insert in. I did think of lining it up with a piece of plain bar, but again you can't get the hex key in the end to screw it in as the bar/threaded rod is in the way. Confuddled [/quote] The method I use came about by accident rather than design. You can't quite see in the photo, but I put two inserts on the threaded rod at once. So in the picture, the one you can see is actually the upper one, and the lower one (the one that will live inside the neck) is already screwed in and out of sight. I found that once two inserts were on the rod and finger-tightened next to each other, that is enough to stop the threaded rod simply turning and the inserts not moving. I guess the inserts aren't machined completely precisely, so they sort of jam together and that's enough to block the movement of the threaded rod. I'm not sure I've explained that very well but give it a go! It can be annoying because having been jammed together by the pressure of being inserted into the neck, they can sometimes be hard to get apart - I've had to resort to pliers on occasion. I nicked my general method from the Manchester Guitar Tech site, but I can't quite remember how he stopped the rod simply from turning in the insert, and for some reason he's taken down that blog entry. It occurs to me now that maybe just by making an indent on the threaded rod (so that the thread is no longer continuous) would be enough to force the insert in. I've got no doubt that there is an extremely simple and widely used methodology for doing this. So if anyone knows what it is, please let us know. Ta muchly.
-
Finished Pics! To the dark side Build One - Alembic-esque Electric
honza992 replied to Andyjr1515's topic in Build Diaries
Andy that looks amazing. Stylish but subtle. I'm sure you've seen this idea before for sanding fretboards, but adding handles looks to be a great idea. I bet it helps with applying even pressure and hand cramps! I keep on meaning to do it but never get round to it..... I stole the photo (I'll return it, honest) from the Simnett Guitars website. -
[quote name='Norris' timestamp='1506344842' post='3378051'] I used an adhesive called Weld-On for my celluloid binding. It has a high acetone content. I had no issues getting it to stay put and with no visible glue line. The only slight issue was the 10 minute working time, but that's not an issue if you've pre-bent the binding and prepared your masking tape strips in advance [/quote] OK, thanks, that's good to know. I may well give that a try next time.
-
OK, not much of an update. Other than I pulled off the binding are re-did it with a new piece. I don't know whether the material it's made from has changed slightly, but the acetone seems to be making it much softer than I remember. No issue, but the second time I left it for two days before taking off the tape and this time it seems to have worked fine. Glued solidly. I've scraped it flush with the body so really all that remains is putting everthing together then stringing it up so I can mark the exact bridge location and get the through body holes drilled. The other thing I've been doing is a million experients with finishes. I've got a few lying around - Tru oil, Liberon finishing oil and Osmo Satin (3032). On the maple top they are all very very similar in look, you'd be hard pressed to tell them apart other than the Tru oil is slightly darker. Obviously they all give an amber finish to the maple which unfortunately clashes a bit with the fretboard, which is brown. So I think I need to keep the maple a more natural colour. I think there are two possibilities. First is use the Osmo Raw which Andy used with great success on his Psilos build, the second is to spray General Finishes High Performance without any tint. It seems a bit of a shame though not to make the most of the flame in the maple, so I may try the dye-and-sand-back method to highlight it before applying the finish. I;ve never done that before though, so it makes me a bit nervous. So yet more experimentation awaits. Though it will have to wait a couple of weeks before I can get back in the workshop. Oh, I forgot that I also made the nut. I sanded the blank to thickness on my high tech nut making jig.... then put it in the neck to get the width right so the nut is nicely flush....(plastic piping is a great sanding block) Then I cut the slots with some nut files, finishing up with the blank in the neck to get the depth right. There's two layers of sensitive masking tape on the neck, so when the file starts scraping that I stop. I'm hoping that will give a tiny bit of mwah ( ) in the open position. 'Course I'm a fretless newbie so this is all experimentation! That's it. Thanks for stopping by.
-
[quote name='Jabba_the_gut' timestamp='1506103658' post='3376541'] So more routing today - and a close shave where I missed locking the plunger because I'm not too familiar with my new router! Luckily it was when I was just starting and was where the arm shaping was going to be so no harm done - would have been a different story it if had been anywhere else on the body and I'd be writing a post about how I need to make a new body..... I started off by thicknessing a leftover piece of spalted beech to use for the control cavity cover. I made a couple of templates, one in mdf and another in Perspex. The mdf one is used for making the cover, the Perspex one is used for drilling the holes in the cover. I put the Perspex template in place on the body and mark where the holes will be. I made the cover slightly undersized so I could put a black trim round it - I also countersunk the holes a little deeper so I could line those as well. I did this on the short scale bass I made recently and it looked really nice so I thought I'd do it again on this one as it is using the same woods (the line on the body at the bottom left is just where the body still needs sanding). [/quote] Wow, this whole build is just inspirational. Your work, sir, is sparkly clean.
-
In better news I've more or less finished the bridge. First I routed the slot for saddle using this abomination. In case it's not clear, the router (with a bushing) runs along the left straight edge and is supported by the other. The short straight edge and ruler are stops to make sure the slot is routed the right length. Does it fit? Yes. Ok, it's a bit long. Mearsuing was never my strong point. Mm, inches, furlongs? All the same to me. I then marked on the string locations, drilled and counter sunk the string holes, shaped the top then did lots of sanding to end up with this: I'm pretty happy. Ebony is such a joy to work with. Or at least it's a joy to sand. Each time you go up a grit your grin gets bigger! (The saddle is scrap, still waiting for a thicker blank to arrive, but I thought it added to the composition!)
-
[quote name='honza992' timestamp='1505414498' post='3371815'] Well I used acetone for the first time a year ago and it's holidng fine. It seems to be a farily recognized technique so fingers crossed it holds ok. [/quote] Fate? Want to see some puppies? Trully the worst timed post ever. The binding is not holding fine. Annoying, I've never had this issue before. Though as I was doing it I felt like something wasn't quite going right. I'm undecided whether to repair it (by wicking in a bit more acetone in the spots where its lifted) or rout it off completely and try again. I shall sleep on it.
-
[quote name='Jabba_the_gut' timestamp='1505334096' post='3371196'] Really liking this build! I know what you mean regarding the pickup vs clean lines. I guess ultimately you could fit a jazz pickup later if you decide you want more than the piezo offers. Cheers [/quote] [quote name='SpondonBassed' timestamp='1505387249' post='3371494'] You could make a wooden case for the pick-up if you have enough scrap from your top. [/quote] Or I could do a combination of both excellent suggestions. I'll keep it plain for now, with a view to making a wooden pickup cover at a later date. Deal. [quote name='SpondonBassed' timestamp='1505387249' post='3371494'] I like the avoidance of messy glue on your binding. Do you know how resilient the bond is likely to be long term? [/quote] Well I used acetone for the first time a year ago and it's holidng fine. It seems to be a farily recognized technique so fingers crossed it holds ok.
-
[quote name='Jabba_the_gut' timestamp='1505334630' post='3371200'] Cheers Honza. The finish on this was Osmo oil (can't remember which one off the top of my head but I'll find out and let you know). No technique as such; wipe it on, leave for a few minutes, wipe it off, leave to dry, light sand with very fine paper and repeat. This is the first time I had used it and I'm really pleased with how it turned out and how easy it was to use. The only thing to consider is that is does darken the wood a bit but that was fine for this build. Cheers Jez [/quote] If you could look up to see which one it was, that would be great. I'm going to start doing some tests.... It looks like you didn't grain fill the mahogany? Did the oil fill the grain, or does it have that nice grainy feel to it? Sand to 320 or so before starting? One coat per day?
-
[quote name='Jabba_the_gut' timestamp='1494094318' post='3293264'] [/quote] I realise i'm very late to the party, but i think its worth pointing out how wonderful this neck joint is
-
OK, just a quick update about the binding. I've decided to go with the ivoroid so first up was to prepare some binding tape. Cut 66 pieces and I'm beginning to run out of suitable surface.... The plastic binding dissolves in acetone, so rather than use glue I just wick in some acetone using a pipette and that melts the binding enough that it sticks to the wood. I hold it with my fingers for 10 seconds or so then use some tape to clamp it. It works pretty well. Taped up for the night.... Once the binding is done the body is more or less complete apart from sanding. The neck is also pretty much done so if I get some time tomorrow I'll start the bridge and the nut. The eagle-eyed among you will notice that I haven't done a pickup rout. I'm in two minds. Part of me wants a jazz pickup in the bridge position to complement the rounder tones of the piezo, part of me wants to keep the top as clean as possible, and a pickup would detract from the woods. Decisions decisions.....
-
[quote name='SpondonBassed' timestamp='1504766611' post='3367089'] I'd be inclined to try a bleaching solution on the bare wood first as an experiment. [/quote] Yep, good idea. I once tried the Liberon Wood Bleacher on ash and it made no difference whatsoever. It may work differently on maple of course. I'll give it a go. My instinct though is that it may need a stronger two part bleach, I think Rustins do one. Though this may be an experiment too far, we'll see how I feel!
-
I made some alternative knobs today. James at JC Tonewoods (where I got the fretboard from) sent a couple of bridge blanks from the same lot of ebony. They're quite dark, mostly dark brown/black rather than the more light brown of the fretboard, but I think that will work quite well for the bridge. The blank I'm using was big enough for the bridge and to make some knobs, so that's what I did.... I think I prefer them to the ones I made earlier. They'll match the bridge and also the ebony (ok ebano, a fake ebony) binding I'm thinking of using.
-
Thanks everyone. Yes, from the build thread for Psilos he says its Osmo Raw I've actually already got some of the Raw and the normal Osmo (without the whitener) which I've never used. I bought it to do some tests then ended up going with something else. I'll drop him a PM if he doesn't chime up in the meantime. My aim with finishing is: 1. Satin finish 2. Reasonably toddler resistant (I've found the General Finishes High Performance polyurethane holds up pretty well) 3. Good grain pop 4. Keep the maple as white as possible on the body, happy for the neck to be a bit more tinted 5. Warm up and darken the mahogany as it is a bit pale. However, it does have some lighter sap wood in the middle which I don't want to obscure. 6. Application by a numpty I realise that some of these may be mutually incompatible. My initial experiment of applying shellac (to warm the waterbase finish) then sand is back so the 'fields' return to their un-shellaced colour was not a success. As I feared it came out a bit blotchy. So my current plan is to use blonde shellac on the maple (including the neck) and the garnet shellac on the mahogany. Over everything I will then spray the polyurethane. I hear different opinions about how to achieve a satin finish with spraying. One school of thought is to use a satin version of the clearcoat. The other school of thought is that that can obscure the grain (becuase of the flatteners) and you are better spraying gloss then rubbing it out with 0000 or 1-2000 abralon. I'm currently sitting slightly precariously on the fence. If anyone has any views I would love to hear them. I also need to grain fill the mahogany. Maybe if I were to add a stain to that it could warm and darken the mahogany that way without have to add in an extra seperate staining stage. Any thoughts or advice? God I hate finishing.....
-
Just a quick question today. I'm going to use General Finishes High Perforance as the top clearcoat on both the body and neck. It's a water based polyurethane which seems to be pretty forgiving in application (I'll be spraying it) but it lacks the warmth an 'pop-ability-ness-itude' which oil based finishes have. So, does anyone have any idea how I can pop grain under a waterbased finish? Without using dye or stain? And ideally without darkening the maple? If I can I'd like to keep the maple as pale as possible. I'm hoping the answer is shellac, so today I started doing some tests on some scrap. On the left is some Zinsser SealCoat, which as I understand is 2 pound blonde shellac. I've diluted it with meths to make a 1 pound cut. On the right is some garnet shellac, made fresh from flakes, also a 1 pound cut. I'm going to try applying each of them to some maple scrap, then seeing if I can gently sand it back so that the maple remains natural in colour, but the shellac that has sunk into the grain will still pop the flame in the top/neck. Anyone know if this is going to work? Or can anyone think of any other way of poping grain but not darkening the wood too much? That's compatible with polyurethane?
-
[quote name='SpondonBassed' timestamp='1504680269' post='3366462'] Leave it to the tool makers to tart up jigs. [/quote] Ha ha ha, ironically I come from a family of tool makers. Or at least my mother does, and Archdale is the name that will go on the headstock. Admitedly they made machine tools not too relevant to guitar making, but I guess the principles are the same. [And if anyone has any memories of working with Archdale machine tools, or even more amazingly still uses one I'd love to hear about it.]
-
[quote name='owen' timestamp='1504641898' post='3366344'] Proper lush. If you have the right wood the whole aesthetic looks after itself. You have the right wood. [/quote] Ha ha, you clearly haven't seen the crimes against humanity that I have committed on a range of beautiful, rare and exotic wood that has resulted in little more than a mangled pile of (probably poisenous) firewood.