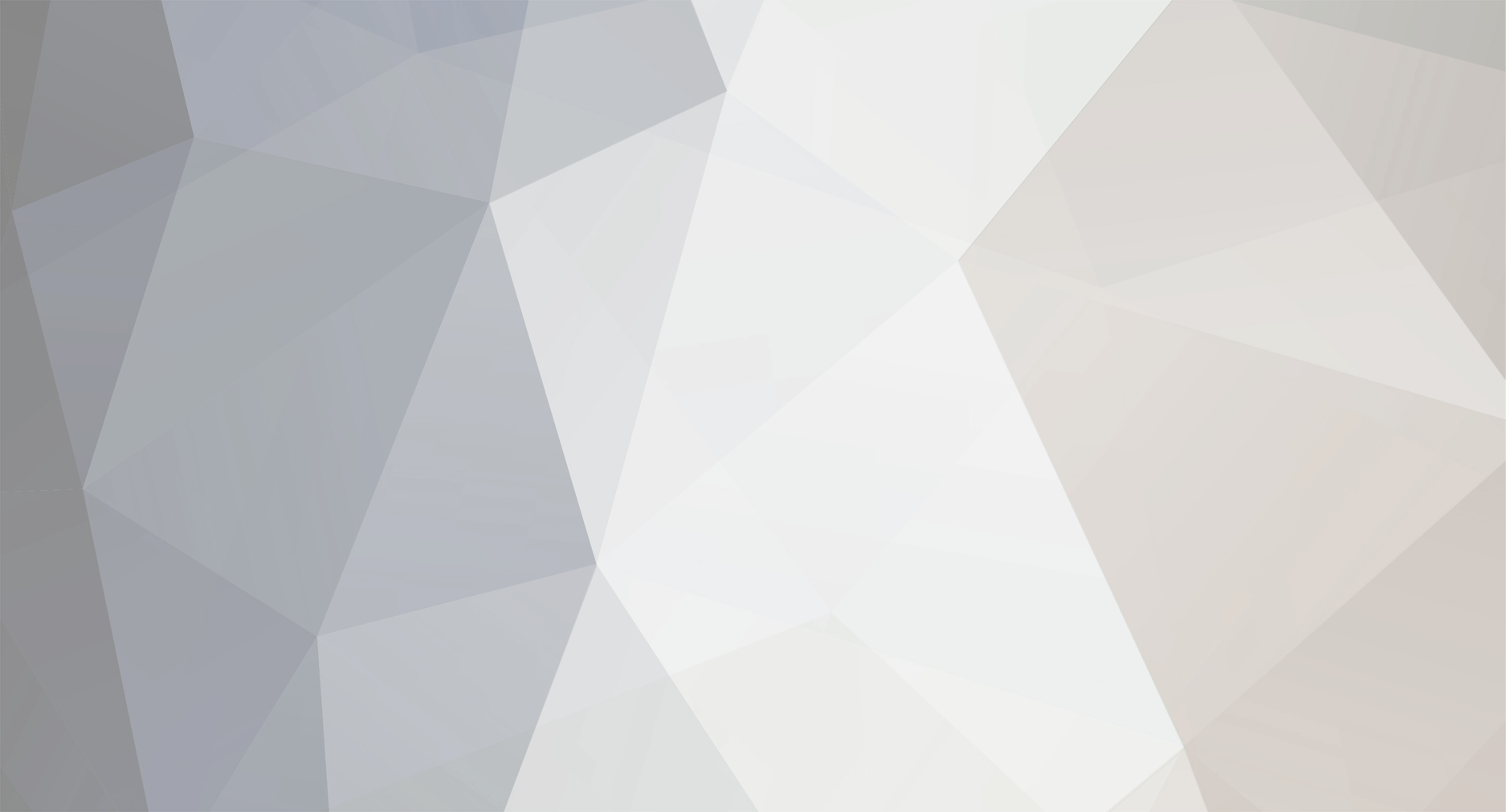
honza992
Member-
Posts
508 -
Joined
-
Last visited
-
Days Won
2
Content Type
Profiles
Forums
Events
Shop
Articles
Everything posted by honza992
-
33" Reverse P/J Jazz bass, blocks & binding (FINISHED PICS)
honza992 replied to honza992's topic in Build Diaries
I've just weighed all the parts and I think final weight will be about 3.4kg (7.5lb). Perfect. -
33" Reverse P/J Jazz bass, blocks & binding (FINISHED PICS)
honza992 replied to honza992's topic in Build Diaries
I'm deep into the neck carve at the moment. This time I'm doing it slightly different to my normal method. Only slightly differently, mind, and if you look away you;ll not notice. But, this time I have cut my facets only as far as the start of the transitions like this....(rather than trying to cut facets through the transitions, if you see what I mean). And I sanded the bulk of the neck to 90% of the finished shape before starting work on the transitions. It's worked out really well. Having the neck virtually finished meant I could 'feel' the transitions more clearly somehow. I should finish the carve tomorrow and I'll post some pictures.... -
33" Reverse P/J Jazz bass, blocks & binding (FINISHED PICS)
honza992 replied to honza992's topic in Build Diaries
Ha ha, yes the pain and suffering is definitely a feature of guitar building. In fact, the more my skills grow the more I realise that guitar building is, like tennis, mostly about avoiding unforced errors. The lapse in concentration, the inexplicable routing using a template that's upside down, drilling too deep, or too shallow, or not at all, not checking fret slot depth etc etx..... I've done them all. Several times. New swear words have been invented. The occasional infantile tantrum. But as @SpondonBassed says, it's inevitable and you just have to rely on your skills or improvisation! -
33" Reverse P/J Jazz bass, blocks & binding (FINISHED PICS)
honza992 replied to honza992's topic in Build Diaries
I haven't actually routed the pickguard itself yet, I won't do that till the last minute. The one's I've done before though have been no problem, no melting, though I do turn the router down to a slower speed. -
Finished Pics! Dreadnought acoustic (guitar) for me?
honza992 replied to Andyjr1515's topic in Build Diaries
Thanks Andy, really really useful info. I've heard of eggwhites being used before but only ever on accoustic guitars. Very interesting. Yet another technique for me to try at some point! -
Neck carving - what do you use and how do you do it?
honza992 replied to honza992's topic in Build Diaries
Oh sh_t😲 I didn't realise there were so many. And all so.... beautiful 🙄. That's great @Jabba_the_gut. Yeah, really thanks for that. Like I need more tool GAS.... 😎 -
Hi All I'm just starting the neck carve on my current build, and I noticed that the tools I use has completely changed over my last few builds. I started using rasps and files, mostly a dragon file sold (at great expense😲) by Stewmac. Recently, though, I've started using one of these, an iwasaki carvers file. It was actually the first file I ever owned, bought on the recommendation of some random poster on some random guitar forum. I remember being singularly unimpressed when I tried to use it, too unpreditable and niggly to use, and it sank down onto the bottom shelf. For this build I dug it out to give it another go, and my god it rocks. It's not like using a file where you file harder to take off more, in any direction, any speed. This needs a much more subtle touch. The angle you use it, the pressure you apply and the direction of the grain all make a huge difference to the effect it has. It can go from taking off massive amounts of wood with little effort, to almost burnishing a completely smooth finish. It really is a remarkable tool. And while not cheap at £20, it's a joy to use. I use the facet method of neck carving, and previously I've always used a spokeshave to smooth down each facet before moving onto the next one. With the Iwasaki there's really no point. It leaves a surfacce plenty smooth enough. It does though, need a careful touch. If you apply too much pressure at the wrong time it can dig in but if you're careful it really does a great job in a very rewarding way. I just thought I would share! I'd love to hear what anyone else uses, and what method you use. If you don't use the facet method what do you do?
-
33" Reverse P/J Jazz bass, blocks & binding (FINISHED PICS)
honza992 replied to honza992's topic in Build Diaries
Into the grunt work. I re-did the frets. Cursing as I went 🙄. Though to be fair, all went smoothly. I then filed them level with the edge of the neck, then added the bevel, taking it down slightly into the binding so there isn't too sharp an edge. I then did the neck taper, going from 20mm at the first to 22mm at the 12th. Slim, but not too slim. It's then on to the neck carve. I use the facet method, which makes for a lovely photo! Oh, and the body needs sanding. Lots and lots of sanding. But is at least looking more or less bass shaped. -
33" Reverse P/J Jazz bass, blocks & binding (FINISHED PICS)
honza992 replied to honza992's topic in Build Diaries
Sounds strange, but in some ways I think making the pickguard is the most difficult thing about building an electric. Unlike wood, plastic is completely unforgiving, and there's something about it that means you really have to be accurate for it to look good. It has to follow exactly the curve of the body, fit exactly round the neck pocket and have exact placement of the pickups and control plate. I've finally got a process that I'm pretty happy with, but it's taken me a long time to develop it, and it still takes a long time to do. Of course, if you're doing a standard size P or J bass then you can simply pick one off the shelf, or use a pre-made template like I've got in the first photo. Everything I do is custom size, so no such luxury for me. First up I do a drawing on some baking parchment (one of the most useful things in the 'shop). I use this to rough cut some 12mm mdf to size. Next I rout the pickup hole into it. At this point the rest of the pickguard template is just rough cut. Having got the pickup rout done, I mount the pickups and make sure that I'm happy with their positioning. Then without moving anything, I use a guided bit running along the edge of the body itself to do the lower horn (where the pickguard runs parallel with the body). At the same time I also rout the neck pocket, using the pocket itself as a guide. This means that the fit of the pickguard is perfect. I then use a guided router bit with different size bearings to rebate into the pickguard template along the lower horn. This results in a template that is smaller than the lower horn, but runs parallel to it. Finally, I cut out the 'V' shape where the pickguard meets the control plate. And that's it! Several hours work. My last insurance policy is that I don't drill the holes for the control plate till after finishing and I'm fitting the plastic pickguard itself. The positioning of the control plate has a couple of mm wiggle room, so if the thickness of the finish, or who knows what else has moved everthing by a mm or so, I can absorb that by moving the control plate slightly, and everthing still fits together perfectly. I told you it was the hardest bit of making a guitar! -
33" Reverse P/J Jazz bass, blocks & binding (FINISHED PICS)
honza992 replied to honza992's topic in Build Diaries
Sometimes I really despair. Last week when I was lying on my (2 yr old) daughters floor as she held my finger to go to sleep, I specifically remember thinking to myself, Honza don't forget to check that the fret slots are deep enough before you glue the binding and start fretting. Well...I didn't, and they weren't. Even more annoyingly (and for the first time ever, what was I thinking) I started fretting from the nut end rather than the heel end. Which meant the first dozen or so went in perfectly before they started bottoming out. So to cut a long story short I had to take them all out.... Pulled 'em out with this... There was virtually no tearout, apart from one small chip near the end. I used a feeler guage and some baking paper as a dam to stop the CA medium glue getting into the fret slot. Ended up being virtually invisible. Then I deepened the slots using this teeny tiny saw. All in all it went pretty smoothly, but I wasn't expecting to have to do a re-fret quite so soon🙄. I'm going to have a whiteboard surgically attached to my forehead so when I have these thoughts in the middle of the night, I don't immediately forget them in the excitement and impatience of building.... I've re-sanded the fretboard and it looks pretty good. I just need to put on a few layers of finish then I can re-fret. But can someone please remind me to remember the things I have forgotten. Thanks. -
Finished Pics! Dreadnought acoustic (guitar) for me?
honza992 replied to Andyjr1515's topic in Build Diaries
Can't wait for the finishing de-brief 😀 It's amazing that man-on-the-moon is almost half a century old, but there's still no recognized method of sealing, protecting and enhancing the grain of a piece of wood.... Andy, you're doing great work. -
Guitar build.co.uk can do whatever you need. Edit: Ah, sorry do you mean you want a guitar shaped lump of wood? Or a finished guitar minus neck, knobs and control plate? If the first then guitarbuild are good, if the latter then ebay or gumtree is your friend. Buy a cheap bass body and most sellers will throw in the neck for free😉 😆
-
33" Reverse P/J Jazz bass, blocks & binding (FINISHED PICS)
honza992 replied to honza992's topic in Build Diaries
The body is now nearly finished. The arm/belly contours are done. I filled in the old pickup rout, and re-did it for a reverse P. I spent ages cutting out paper control plates of different shapes (including the Sandberg style suggested by @songofthewind , which look great) but just couldn't get anything I was happy with. Because of it's location (nearer the bridge) there wasn't much contour to it, which meant it just ended up mostly looking like a not-very-happy penis. And I'm not sure that's exactly the look I was after 😕. So in the end I simply decided to re-shape the body so that it followed the shape of the control plate, rather than the other way round. I think it's ended up looking pretty good. I also did drilled the holes for the pickup and bridge ground wires. Because the bass is going to be painted, the easiest way to do the bridge ground was just to drill through the side of the bass. I don't have a bit anywhere long enough to drill all the way through from the bridge pocket. One thing I forgot is that those long bits drop, so by the time it came out into the control cavity it was worryingly near the bottom. Luckily there were a few mm to spare, and I may fill the bottom with a bit of epoxy just to make sure it remains strong enough. Tomorrow, fretting and doing the roundovers on the body..... -
33" Reverse P/J Jazz bass, blocks & binding (FINISHED PICS)
honza992 replied to honza992's topic in Build Diaries
Oh my oh my oh my. That's some lovely shiny shimmering lovelyness right there! (And I'm leaving my MOP as is. Actually I designed it that way from the beginning.....😁) -
I think I agree with @Jimothey I use a router with a guided bit, which more or less does exactly what a CNC does. If you think about it, that bearing is a primitive CNC! It reproduces a shape with only minimal intervention from me. I think the difference in mechanisation at this point is one of degrees. I don't use CNC because I build for the (non financial) reward it gives me. So I'm not sure using CNC would help that much. I think the key is customisation and developing a customer experience that goes beyond simply walking into a shop and picking something off the shelf. A custom builder has the opportunity to work with the client to build something that is designed for them, but also something where they have helped chose the wood, the binding, the finish etc etc . That's my goal anyway. But there's no way I would ever be able to do that to pay a mortgage.....Not when competing with CNC.
-
I think everyone here builds without CNC. Though admittedly not commercially. I don't think it's possible to earn a living making guitars without using CNC.
-
I'd like to take a look, though I'm a builder more than a player, and by the looks of it your skills are already up there. But I would give an honest opinion re build, fit, finish etc. I'm in Nottingham.
-
Ho...ly....cow... Your sanding is amazing. Really outstanding. Awe-inspiring. Curves...light and dark woods....that's hard to get clean lines. But you get it looking like it has been forged in bass heaven. No stray sanding dust, beautiful sparkly clean lines.....You are literally killing me😲 Any tips for us mere mortals?
-
33" Reverse P/J Jazz bass, blocks & binding (FINISHED PICS)
honza992 replied to honza992's topic in Build Diaries
More of an issue is this.... All the blocks are white, apart from the one at the fifth fret (block 3) which is blue. What the...?!%@%! I didn't notice before because they were only rough sanded, but once glued in and starting to sand it was obvious that it didn't match at all. This is the first time I've used MOP and as a natural material I'm sure there is some variation in hue, but that is ....well, a bit much. Very disappointing. I guess I have two options: 1. Grab my router, and zap that little bugger. Hope I can get it out relatively neatly and re-rout the channel. Get the retailer to send me one that is the correct colour, re-glue, re-radius and put it all down to experience. 2. Relax. It is at least at fret 5, so I can pretend that it's a design feature. And no one will notice apart from me anyway. Anyone with any opinions? (Oh and also I'll email the supplier and ask whether that blue is in fact within the accepted range of 'white'....🙄) -
33" Reverse P/J Jazz bass, blocks & binding (FINISHED PICS)
honza992 replied to honza992's topic in Build Diaries
A quick update on the neck. The blocks are in, glued and the neck radiused. It's.....ok. Not great, but for a first effort it's acceptable (the fill around the blocks is a bit too obvious for my liking), but I learned loads and next time it will be one hell of a lot better. A quick shot hiding the imperfections... Next time I will do the gluing a little bit better, because I think the way I did it this time contributed to a slightly sloppy job. This time I used epoxy and sanding dust to glue the blocks in, and in my head I had imagined the epoxy oozing up around the block, filling the gaps around it at the same time as gluing. And that is what happened, at least to begin with. What happened next though, was that the expoxy then sank down again, I think as the blocks rose up a little bit. So next time I will divide the gluing and the filling into two completely seperate stages. First I will glue the blocks in with a small amount of medium CA glue, using only enough to cover the bottom of the channel but no more. Then, once dry I'll use either epoxy or medium CA glue with sanding dust to do the gap fill. Oh, and the other thing I need to work on is my chisel technique, both use and sharpening☹️ But all in all, ok for a first effort. -
Here's a couple of mine..... (Edit: Mods, am I alowed to post my own? If not, please delete!😁)
- 13 replies
-
- 11
-
-
33" Reverse P/J Jazz bass, blocks & binding (FINISHED PICS)
honza992 replied to honza992's topic in Build Diaries
Wow, that's an incredibly kind officer and a gentlemen. You're but a mere hop skip and jump away. I may very well be getting back to you....Thanks again. -
33" Reverse P/J Jazz bass, blocks & binding (FINISHED PICS)
honza992 replied to honza992's topic in Build Diaries
So, I'm guessing you don't all love the idea then😋 I guess part of my issue (apart from being lazy🙄) is that I have no metal working tools at all - files, drill bits, countersinks, saws etc etc. I'm reluctant to spend yet more money on tools.....no, hold on, who am I kidding. I'm reluctant to spend money on clothes, or the bus....I'm joyful to spend money on tools 😀......though on my tool wish list, metal working tools come below woodworking..... I'll have another think.... -
33" Reverse P/J Jazz bass, blocks & binding (FINISHED PICS)
honza992 replied to honza992's topic in Build Diaries
I'm pretty sure the answer to this is...no, clearly not, what were you thinking you complete numpty.... ....but is there any reason why brass can't be routed? Make a template for the plate from 12mm mdf, sandwich 2mm brass stock with another piece of 12mm mdf then trim it on my router table with the speed as low as possible. Just, you know, a thought😋 -
33" Reverse P/J Jazz bass, blocks & binding (FINISHED PICS)
honza992 replied to honza992's topic in Build Diaries
Thanks Jez, I'd be really interested in the chrome plating idea. Doing my own plate would be the ideal solution. How difficult is brass to cut and shape?