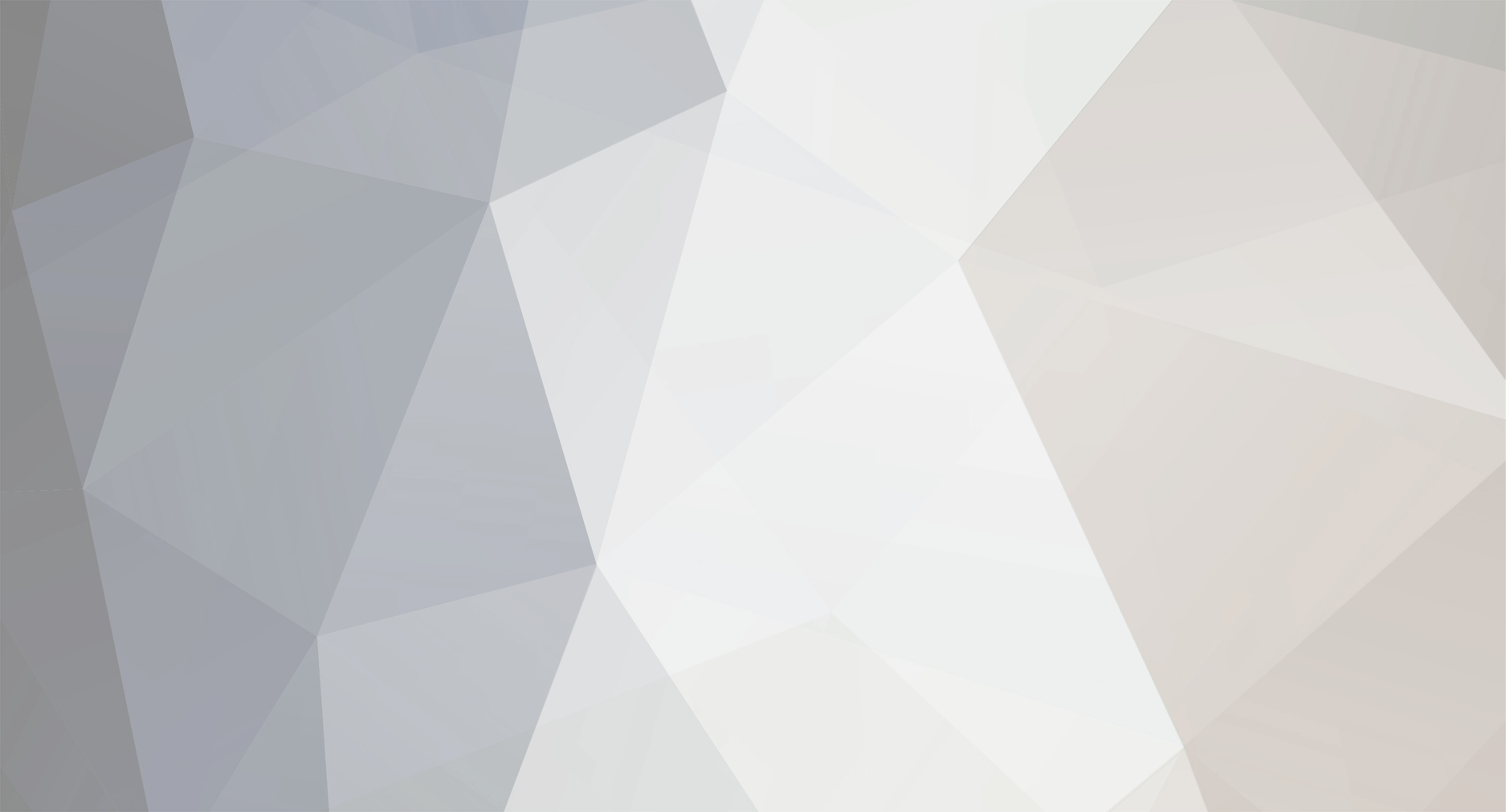
rwillett
⭐Supporting Member⭐-
Posts
1,621 -
Joined
-
Last visited
-
Days Won
6
Content Type
Profiles
Forums
Events
Shop
Articles
Everything posted by rwillett
-
Hi Strange definition of "fun" I hadn't seen before The original work for this started with a Prusacaster (https://blog.prusa3d.com/the-prusacaster-how-to-design-and-3d-print-an-electric-guitar_71962/). I built that using an Ender 3 Pro 3d printer. I can't remember the neck I used but contrary to what the reviews said, it wasn't a very good guitar. Its bulky, quite awkward to use and I thought I could do better. The last version is a very long way from that Prusacaster and has nothing in common with it, possibly apart from a bridge. This is (I think) the sixth version. I could have brought a genuine 62 Strat if I put my own time in as a cost To build the latest version requires: 1. A pillar drill. There's a quite a lot of aluminium inside and on the back of the six string. It requires quite a lot of either drilling and then tapping screw holes in OR using industrial adhesives to bond aluminium together. The adhesives are not fun to play with. Drilling and tapping aluminium is easier but hard work. A hand drill is not accurate enough. 2. You need to be able to cut and shape aluminium to get the cut aways, so a finger file tool is helpful. You could do it by hand but thats a lot of work. 3. You need to make a lot of tools to get the drilling right OR to hold the aluminium in the right place if bonding. 4. You need quite a few clamps to hold things in place for glueing the body together. 5. There are a range of screws, from M2.5's for the back plates to a section of M3's of different lengths and different heads. I have two screw boxes each with 20 compartments of just M3 bolts. Button headed, countersunk, black, silver, cheese headed and so on of different lengths. 6. You need to be able to design a pickguard as they are specific to the pickups. You need to choose pickups. 7. You need to design and solder a wiring loom. 8. You need to be able to use a slicer to create negative volumes for printing (this makes sure there are voids) and to pause printing to add in a number of M3 square nuts. Octoprint is a help here. You also need to create different printing infills for different parts of the model. 9. You need to design the neck module to hold the neck in the right place, I have always brought second hand (and decent) necks but every one is different, so I have a 3d scanner to scan the neck to get it right. 10. You need a glue that will weld the plastic together. In the UK I use FloPlast, not sure where you are. 11. You need to be able to properly use Fusion360 as that's where all the files are. 12. You need copper tape. The actual printing isn't too bad. It's around 70-100 hours depending on your printer, a modern printer will do it quicker, such as a Prusa Mk4. I have thought about doing a BOM and releasing the files but I cannot support it and I know from bitter experience releasing free software, I had loads of people wanting help or changes, and I simply have no time to do that. Simple things like their bridge has different screw holes to my bridge, how do they change it in Fusion 360? Perhaps FloPlast isn't available in the UK, can they use brand X or brand Y glue? I use metric screws for everything, in the USA, metric screws are less popular than imperial, so can they use a 1/8" as opposed to an M3. Can they even buy an M3 square nut in the USA? How do they align the neck properly, I made a laser guider to check its correct, why did I do that? Because I made a mistake in the measurement, cut and drilled aluminium and was out by a mm. Learnt my lesson the hard way as I threw about 2-3 days of work away. Nothing in the above is difficult to do in isolation, it's a lot to do if you've never printed a guitar before. If you really want to print it, I'll help you do it, with no issues from me, but I don't have the time to put the files up and show people how to make it and make a BOM out of it all. Thanks Rob
-
Ah OK, Misudnerstood
-
@itu That would be this document that describes that (I think) https://www.emgpickups.com/pub/media/Mageants/p/_/p_p5_p6-b245_0230-0107rf.pdf That link was working yesterday as I used it but it is not working today. A screen shot from the PDF. If you wish to donate for free a few different EMG pickups, I'd be very grateful and will even name the guitar after you can't say fairer than that. Lets get one working first, Rob
-
@Delberthot It is an active EMG pickup. I'm hoping it doesn't need a ground BUT I may change this depending on mood, tone and whether the dammed EMG pickups actually work This is work in progress to see how things might fit. From looking at this, the tone and volume are too close and I'll probably move the tone to the back and put the output socket in the middle. The battery will probably be in the bottom, thats the bit underneath the pickups. But all of this needs further modelling. This is all about the "art of the possible". Model as much as you can in CAD and then print as little as you can. Rob
-
I did see that film. I don;t have a phobia about them (yet) but they are creepy.
-
That is genuinely frightening....
-
A few years ago I hit a tree quite hard whilst mountain biking, my retina started to come off my right eye. It was fixed through an emergency op (Big shout out to St Pauls Eye Clinic in Liverpool for a late night op). Things like angled holes and subtle details need to pointed out to me now. That and getting old is a bummer.
-
I had to blow that picture up to see that. I can now see an angled hole when I look very closely. I still had to look very carefully though Thanks Rob
-
That's really helpful. I can't see where the bridge is grounded on the treble side in the photos. I'm sure it is from other photos of the inside but I can't see it here. What have I missed? Just to be clear, I am going to ground the bridge to the rail and it's very likely to be on the treble end and is possibly going to be through the tightening screw. I have 3-4 different methods and trying to work out the easiest and 'best' method, though unclear what best actually means here.
-
Not forgotten
-
As I need something to keep me going during some hairy times at work, I thought I'd build a simple type of rail guitar. I also wanted a small, light(ish) travel guitar. Unsure at the moment if this is a headless or headed which is not actually a big problem at the moment (or I don't think it is) The Westone "The Rail" is an inspiration but nothing more than that. There's a separate thread on how the earth grounding works on it elsewhere So far I have the mental image in my head, I have an active EMG precision bass pickup(s) which I brought from the parish, but I've never used it or even tried it so who knows. I've got a headless bridge and neck bits and bobs as well as some aluminium tubing to test this out. If it works, I suspect I'd use stainless steel tubes. Printing the stuff is no problem, and I have worked out how to keep build the strength in with some clever (and simple) design (and some more aluminium). The neck will be either an Ibanez TMB100 (I think) if headless or an Aria with Hipshot tuners if it has a head. I'm tending to think it will be headless. The design is based around the pickups working outwards. All my other guitars are from the outside in to get the right curves. This has no curves and is extremely functional. So here's the pickups layout. I need to add in the tone and volume controls as that's what the EMG has. That will determine the width and then the neck and bridge just follow on depending on the scale. What could go wrong ? Rob
-
Westone "The Rail" Bass - A down to earth question
rwillett replied to rwillett's topic in Bass Guitars
Thats helpful and does seem to indicate that the screw was connecting and possibly grounding on the metal tube. I've worked out a way to do it that isn't too complex (or I think I have). I'll build this from the pickup outwards. I have a a choice on an Ibanez neck of some description or an Aria PRO II Std one with Hipshots. One advantage of a rail design is that its quite easy to adapt between headless and normal necks. I suspect though that it might be headless though and the Ibanez might be sacrificed here. Decisions, decisions, decisions... Rob -
Westone "The Rail" Bass - A down to earth question
rwillett replied to rwillett's topic in Bass Guitars
Oddly enough I have that sitting on my desk -
Westone "The Rail" Bass - A down to earth question
rwillett replied to rwillett's topic in Bass Guitars
When I searched for this earlier, a lot of the responses say that the bridge should be grounded. A few say it makes no difference but a number of sites state it is essential to reduce hum and for safety. https://www.google.com/search?q=do+guitar+bridges+need+to+be+grounded+safety&num=10&client=firefox-b-d&uact=5&oq=do+guitar+bridges+need+to+be+grounded+safety We are going slightly off topic here, but I'm interested in safety as its me. A statement such as "There is no safety issue (and an argument the other way)" could do with being expanded as I couldn't see anything that said grounding the bridge could be dangerous. I am not an expert in electrical stuff, so I'm trying to follow best practise here. I recognise that t'internet is sometimes wrong so I'd be interested in finding out why. Thanks Rob -
Westone "The Rail" Bass - A down to earth question
rwillett replied to rwillett's topic in Bass Guitars
I read that with great interest. A good insight into how things were done. -
Westone "The Rail" Bass - A down to earth question
rwillett replied to rwillett's topic in Bass Guitars
The point is how are the steel rails connected to a sliding middle section. Something that rubs against the rail is a poor option as the rails will have grease from fingers. A friction type of option is not elegant and I don't think Westone would do that. My 83 westone guitar is very well made I'm struggling to believe Westone just allowed something to rub against a rail and also some of the rails may be powder coated so that can't be the option there. I could be wrong but I would like to get to the bottom of this problem with a definitive answer. Thanks Rob -
Westone "The Rail" Bass - A down to earth question
rwillett replied to rwillett's topic in Bass Guitars
Still unclear as to how it's earthed though. Given various regulations around the world I would have thought legislation would insist on it. -
it's a while since one of these came up... Westone Rail.
rwillett replied to alyctes's topic in eBay - Weird and Wonderful
Too expensive for it's condition fo me. -
Westone "The Rail" Bass - A down to earth question
rwillett replied to rwillett's topic in Bass Guitars
Thanks for this. It does look like the bridge isn't earthed. One way to check would be see if there is electrical conductivity between the bridge and the ground on output socket. My thoughts here are NOT to build a Westone clone and replicate crappy electrics, but something a little more interesting. I've got decent pickups and decent pots so the electrical side isn't an issue. Building the open nature of the bass is more of a challenge but I've some ideas on how it might work and look. Thanks Rob -
Westone "The Rail" Bass - A down to earth question
rwillett replied to rwillett's topic in Bass Guitars
Seen the diagram. Doesn't show if the bridge is earthed sadly. Thanks Rob -
Westone "The Rail" Bass - A down to earth question
rwillett replied to rwillett's topic in Bass Guitars
It's a puzzle -
Westone "The Rail" Bass - A down to earth question
rwillett replied to rwillett's topic in Bass Guitars
@Stub Mandrel Nothing I've seen shows a contact strip in any picture. If one tube is hot and the other earthed then surely that would create issues if you touched both parts? the current is virtually zero, but your body would interfere (I would think). Rob -
Westone "The Rail" Bass - A down to earth question
rwillett replied to rwillett's topic in Bass Guitars
Hi Si That would probably scratch the tubes, but not definitely. Rob -
Westone "The Rail" Bass - A down to earth question
rwillett replied to rwillett's topic in Bass Guitars
That might be how it's done but that would probably also scratch the tubes and I've seen pictures of immaculate guitars. No scratches at all. Its a puzzle and I can't work it out. It might be that the bridge isn't earthed but I'm sure there would be hum. Rob