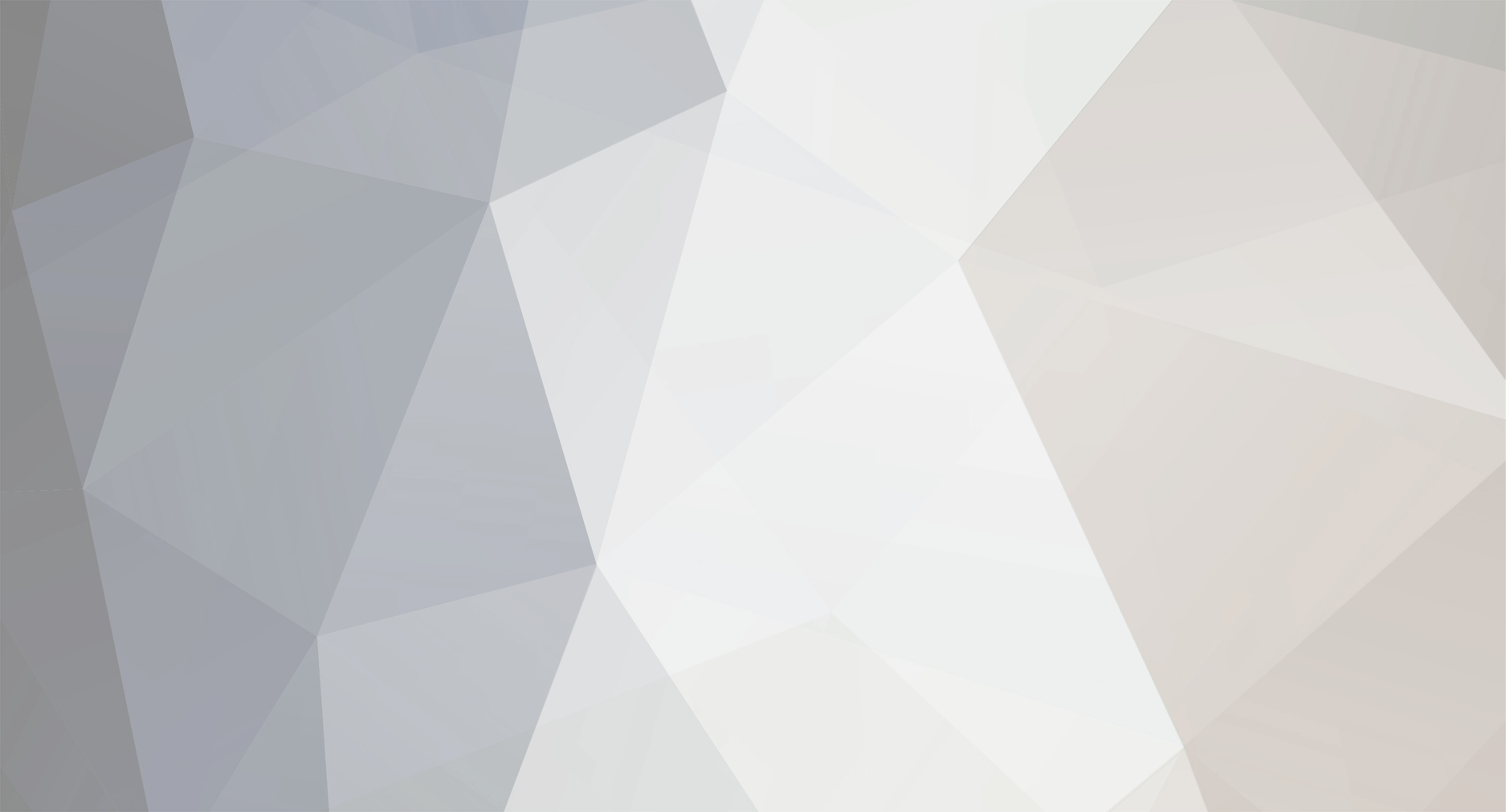
rwillett
⭐Supporting Member⭐-
Posts
1,626 -
Joined
-
Last visited
-
Days Won
6
Content Type
Profiles
Forums
Events
Shop
Articles
Everything posted by rwillett
-
@Richard R Thats such a generous offer. I'll certainly swap my two, almost but not quite feral, cats who are at this point in time doing their best to decimate the mice, rat, and bird population of the village. The cats have no fear of anything and so rabbits and pheasants are also their targets. Its such a joy when they try to bring in a butchered and half eaten rabbit through the cat flap. I have a strong stomach, but not that strong. The only reason there are no foxes is that every fox, as far as I know, has emigrated to the local towns and cities as it's easy food there and because my two ninja cats aren't there. The cats also smell really badly and love dribbling on you at 04:30 in the morning if they can get in the bedroom and the dog hasn't noticed them. The dog classes the bedroom as his turf and tries to chase them out. They also throw up anywhere they can, and their litter tray and the 100,000 acres of Yorkshire Dales literally outside the door,is ignored if they can find a corner of the house to poop in. The vet bills are enormous as well. So I accept your offer to swap cats. I'll be there in around 15 mins. Thanks Rob
-
Looks good. Keep us informed
-
These are when I do my design work in Fusion 360. I've developed the ability to track the call mentally in the background and to anticipate when I need to speak.
-
NDBD: Squier Affinity Jaguar H (first D is for damaged, not double)
rwillett replied to neepheid's topic in Bass Guitars
Those two look very purrty (sounds of six fingered banjo playing in the background). You must bring them to the bass bash. Do you need a van yet? Rov -
A boring MS Teams call....
-
@fretmeister How was the Tonex with the Yamaha HS7 please? I have a Tonex 3 button version and was looking for something smallish for home use. Don't need massive volume at all, but wanted something small that I can use the Tonex with both bass and guitar. Thanks Rob
-
Anybody pulled together a DIY FRFR speaker/CAB?
rwillett replied to rwillett's topic in Build Diaries
I thought I knew which thread you were referring to and after looking for it, I realise I have no idea which thread you mean. There's quite a lot of threads that this could be, any pointers welcomed. Thanks Rob -
Anybody pulled together a DIY FRFR speaker/CAB?
rwillett replied to rwillett's topic in Build Diaries
@JPJ Thanks for the reply. I have read the the 1x12 design thread, but for some reason I missed the bit about it being pretty much an FRFR design, my bad My knowledge of suitable PA amps to pair with the 1x12 design is slightly less than my knowledge of kitten surgery, I dabble as does everyone, but I'm no vet I'll ask in that thread. I did note that somebody had put a small amp with the speaker to make a combo, my intention is to make this simple (once complete) and reduce leads, power cables and what not. Thanks Rob -
Hi, I can see a number of excellent build diaries for cabinets, but haven't seen anything about building a FRFR speaker/cabinet. Given the wide number of relatively cheap class D amps that are around, I would have thought that the more technically minded would have turned their minds to this. My reasons for looking to a FRFR speaker are: 1. I have limited space as t'other half doesn't want the house "cluttered with your crap". 2. I play bass and guitar (equally badly) and would prefer fewer things. 3. I have a Tonex pedal board AND a Mod Dwarf pedal board and would like a decent FRFR speaker to use with them, especially the ToneX. 4. I don't want really want a (supposedly) 2000W Headrush 212 FRFR speaker or a Spark Cab or a Katana Boss or Spark 40 and not use the modelling element. 5. I fancy doing something along with building guitars. <-- This may be the actual reason. Any links or suggestions welcomed please. Thanks Rob
-
Worst Live Act (Pushing it a bit too far)
rwillett replied to theplumber's topic in General Discussion
Bob Dylan at the Brixton Academy, probably late 90s, supported by Elvis Costello. I idolised Dylan growing up. Never meet your heroes 😩 Elvis Costello was excellent BTW -
NDBD: Squier Affinity Jaguar H (first D is for damaged, not double)
rwillett replied to neepheid's topic in Bass Guitars
That's not fair.... Not quite in the same league as Fermats 'I have a truly marvellous demonstration of this proposition which this margin is too narrow to contain.' but not too far off... Rpb -
Well deserved as well 👏👏👏
- 33 replies
-
- 1
-
-
- brooks bass guitars
- thunderbird
-
(and 1 more)
Tagged with:
-
Played rugby on Hackney Marshes for 10 years and all round Essex. I moved to just off Railton Road in 1988, small garden flat in Milton Road, used to head up and down the Walworth Road to E&C and beyond. Those were the days of £50K flats and a decent curry in Tooting for £4. Rob
-
@Reggaebass are you sarf east London? I recall Walworth Road and you for some reason. I'll book a minibus...
-
I look forward to my invitation to your man-shed. I'll bring tea and biscuits
-
My suggestion would be "we were crap, the set list is pants". If you have two gigs and one rehearsal left, what do you have to lose. Of course the way you say it is important, but it needs to be said.
-
Still better then me 😩
-
NDBD: Squier Affinity Jaguar H (first D is for damaged, not double)
rwillett replied to neepheid's topic in Bass Guitars
Ah grasshopper, Confucius he say "Think of it as the first step on the path to a well worn relic... " Rob -
Thats a great video
-
Absolutely true.
-
Everyone is welcome, though Dorset is a fair trek. Rob
-
Ink tanks convert printers from highly expensive cartridges into a refillable tank of ink that you can fill as needed. It means you don't need to buy dedicated cartridges but can use cheaper inks. Some printers are easy to convert, some less so. Google for ink tank conversion kit and your model of printer. Rob
-
I wouldn't say you have OCD, more like organised and sensible. Why wouldn't you want to have the set list agreed before you go on? You may have options to play if needed but you all know which way you're going.