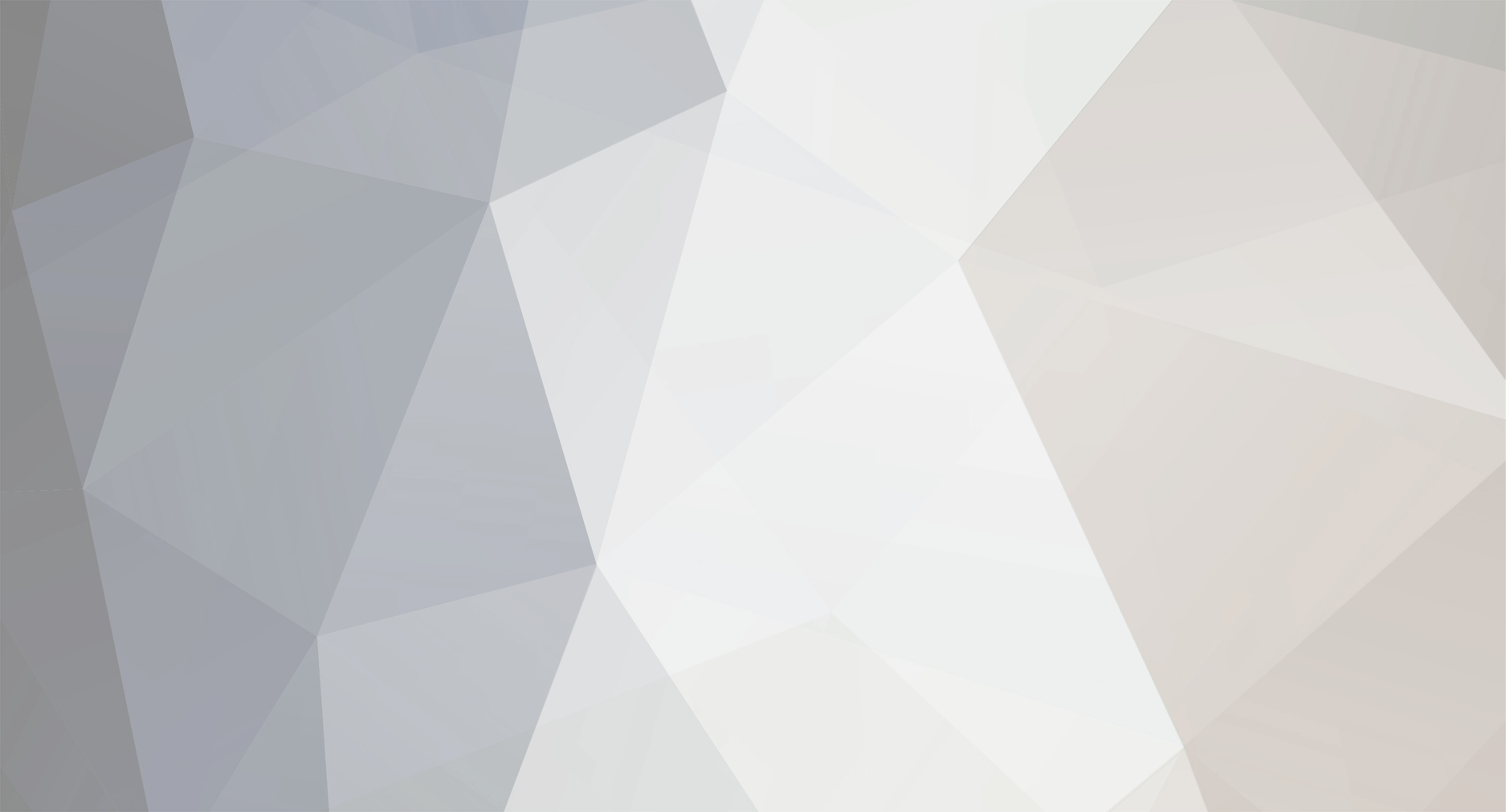
agedhorse
Member-
Posts
996 -
Joined
-
Last visited
Content Type
Profiles
Forums
Events
Shop
Articles
Everything posted by agedhorse
-
An XXcontroversial Way to Compare the Output of Class D Amps.
agedhorse replied to Stub Mandrel's topic in Amps and Cabs
Yes, but for bass guitar especially, the mid characteristics and sensitivity are very important also. There is a tradeoff between raw power handling (including both thermal and mechanical) and sensitivity, mid extension, cost, and often there is a need for a larger enclosure size. With the number of players that would be ok with these tradeoffs being quite low, it's not really all that viable (IME anyway) for a commercial product. At this point, 400 watts RMS at low frequencies (say down to 40Hz) appears to be about the sweet spot. If you were to take such a driver and high pass the signal to 50Hz, than the same driver might be ok to 500W RMS, but that's a mighty bold assumption for a manufacturer responsible for warrantying their speaker to make with confidence that it won't come back to bite them in the butt (bum). Being wrong on such an assumption could result in extraordinarily high warranty costs. -
MarkBass UK maintenance - help needed please!!
agedhorse replied to kolossusuk's topic in Amps and Cabs
I would add that your experience is quite unlucky compared with industry statistics. -
Darkglass AO500 went up in smoke. What to do next?
agedhorse replied to lewiswhitebass's topic in Amps and Cabs
There is no problem designing for 2 ohm operation with identical reliability to an amp with 4 ohm minimum load operation. In amps I have designed, the reliability statistics fully support this. There are many different protection schemes depending on the type and class of amp. These protection schemes include: - AC line over-voltage protection - AC line under-voltage protection - power amp thermal protection - power supply thermal protection -output stage over-current protection - output stage leading phase angle protection (illegal capacitve load) - DC offset protection - power supply over-current protection - excessive HF content protection - short cycle inrush current protection Some amps have many of these protections, some have just a few. There is substantial cost (and design effort) to these but when you can reduce the failure rates to almost zero by including them, in general it's a good choice. -
Darkglass AO500 went up in smoke. What to do next?
agedhorse replied to lewiswhitebass's topic in Amps and Cabs
Unfortunately, there’s little marketing value, but it does save massive costs to both the manufacturer and the player. -
Darkglass AO500 went up in smoke. What to do next?
agedhorse replied to lewiswhitebass's topic in Amps and Cabs
Most do have protection circuits, but it's important to recognize that protection circuits are not 100% effective against all faults and all fault conditions. Different designers and different companies place different amounts of importance on protection circuits since they add to the cost of the design while being almost impossible to market as a valuable feature to the majority of customers. -
MarkBass UK maintenance - help needed please!!
agedhorse replied to kolossusuk's topic in Amps and Cabs
This may be your own personal experience with limited brands or models, but my experience is that this is not true in general. -
An XXcontroversial Way to Compare the Output of Class D Amps.
agedhorse replied to Stub Mandrel's topic in Amps and Cabs
Yes, but there are also other just as valid (and maybe more-so) depending on how powerful the amp might be. What's appropriate for a 100 watts amp that's going to be driven into compression and clipping might not be appropriate for a 2500 watt amp that has the capacity to destroy most speakers if driven into clipping or compression. It depends. A designer has to come up with a method that makes their intended customer happy with the results, doesn't result in premature shut-down or self-destruction and delivers adequate performanece. -
MarkBass UK maintenance - help needed please!!
agedhorse replied to kolossusuk's topic in Amps and Cabs
When an amp is not designed to be repaired at the component level, you generally get the benefit of a more inexpensive purchase price but then suffer the consequences of needing to replace assemblies rather than component level repair. This is not a big deal where the designs have a history of long, reliable life, but can be very costly (for both the manufacturer and end user) if the failure rate is high and the failures affect amps less than say 10-15 years. At this point, doing the "true cost of ownership" calculations shows that the cheaper amp built this way may in fact be more expensive than the more expensive amp that has a longer, more trouble-free life. As a society, we have become more accepting of "disposable" consumer goods, and there are companies within our industry that specialize in this model. Ultimately, when these products are manufactured "off shore", not only is there the loss due to the cost of a product that is considered disposable, but there is also the loss of income to those within your region who would have built the product "in region" or "in country" that affect the local health of the economy. This is something that we began studying in engineering economics back when I was in university (a very long time ago, I assure you), I assume that it has taken on added importance in recent years. -
Darkglass AO500 went up in smoke. What to do next?
agedhorse replied to lewiswhitebass's topic in Amps and Cabs
If the amp's specs have been revised to operate at a minimum 4 ohm load and you had problems that may have been contributed to be being operated into a 2.67 ohm load, you might have another path to get this resolved in your favor. You should not be responsible for somebody else's mistakes, heck it's tough enough being responsible for our own, right? -
An XXcontroversial Way to Compare the Output of Class D Amps.
agedhorse replied to Stub Mandrel's topic in Amps and Cabs
There are a couple of things going on here that the marketing departments jumped on like rabid dogs... First, there is the obvious limitation of the high frequency driver which is no more than about 35-40 watts RMS above 800hz. There is dynamic mechanical power handling above this, but in practice, due to the sensitivity difference between the HF and LF sections, this doesn't even come into play. Typically the HF section is at least 10dB more sensitive than the LF section on a cabinet like this. So, even if the amp is nominally capable of delivering "1000 watts" (or whatever number), the internal processing limits this back to no more than 100 watts for "survive-ability" reasons. Second, looking at the LF section, the driver is not going to be capable of more than 400 watts RMS at low frequencies, therefore in the processing, the limiting and HPF algorithms are often dynamic and increase the amount of limiting as level gets higher and frequency gets lower. This too improves "survive-ability". Since this is a biamped speaker, the easiest and most common solution is to use the same power amp design for both channels, and use the driver's impedance plus processing to manage the real world power levels delivered to the speaker. For example, the amp might be rated at 1000 watts RMS at 4 ohms, but if the drivers are 8 ohms (or even 16 ohms in the case of the HF driver), the unprocessed power available would be 500 watts RMS to the LF and 250 - 500 watts to the HF. There's nothing wrong (and a LOT right) with managing power this way but IMO the real issue is with the way the numbers are manipulated by the marketing folks in a way that appears deceptive even if that's not the intent. Incidentally, this is a major conflict at many companies, between the design/engineering departments and marketing departments. -
An XXcontroversial Way to Compare the Output of Class D Amps.
agedhorse replied to Stub Mandrel's topic in Amps and Cabs
It's not quite so easy, though there are rules of thumb that engineers can use to determine the validity of specifications (called cross-checking or cross-verification). The AC input power is required for any amp to be the current draw at 1/8-rated RMS audio power at the lowest rated nominal impedance for any amplifiers compliant with IEC 60065 or 62368 safety standards. The standards also include a provision that if an amplifier is intended to and marketed to drive more than 1/8-duty cycle, the stated AC input draw MAY be increased to account for the increased (more severe) duty cycle. That said, the rated AC input power is verified by the test lab and really can't be fudged. RMS rated power can be calculated from the input power using the following method. Using an assumed efficiency of 80% for a class D/SMPS, the 110W is multiplied by the efficiency then the result is divided by the duty cycle for rated RMS audio power. Using the 110W input example: (110W x .80eff)/.125dutycycle = 704 watts RMS (presumably 4 ohms) With the Orange Terror, to me it looks like they are using a more severe duty cycle because roughly (500 watts input x .8 eff)/.125 = 3200 watts. In fact, what it looks like is that the rated input is actually the maximum rated input rather than the average rated input. This would conform to a duty cycle of 1 On the Subway amps, I typically use a duty cycle of between 1/4 and 1/3, therefore the rated AC input is higher than what it would be if we used 1/8-duty cycle (IIRC, I use ~400 watts rated AC input for an 800 watt RMS rated amp). This is because the amps are advertised and marketed to be able to be overdriven, and these numbers would then be accurate.- 66 replies
-
- 14
-
-
-
Darkglass AO500 went up in smoke. What to do next?
agedhorse replied to lewiswhitebass's topic in Amps and Cabs
Maybe they discovered an error and revised the docs and chassis? Happens sometimes in spite of best efforts. The 900 watt models are 2 ohm capable and use a switch to operate at 2 ohms. -
Darkglass AO500 went up in smoke. What to do next?
agedhorse replied to lewiswhitebass's topic in Amps and Cabs
Not according to the docs on the Darkglass website: https://www.darkglass.com/app/uploads/2022/05/AO500-Manual.pdf Maybe you are looking at the wrong model, or there is an error in your documentation? 3 ohms minimum, which is 4 ohms nominal with room for excursions into sub-nominal territory. I am very familiar with the module they use and the following is accurate. -
Darkglass AO500 went up in smoke. What to do next?
agedhorse replied to lewiswhitebass's topic in Amps and Cabs
According to the docs, it’s 4 ohms minimum load. I wonder if this is the root cause? -
Darkglass AO500 went up in smoke. What to do next?
agedhorse replied to lewiswhitebass's topic in Amps and Cabs
Is there a switch that needs to select 2 ohm operation? -
As a reminder, this is similar enough symptoms of an intermittent SpeakOn plug. I have seen intermittent plugs for two main reasons: 1. Counterfeit or knock-off, non-Neutrik branded plugs (major issue, and a cause of a fair amount of warrant claims unrelated to the amp) 2. Improperly assembled SpeakOn plugs where the assembler trimmed the wire, which then cold flowed under the pressure of the binding screw and loosened. Both of these are well known issues that I deal with way too often in customer support.
-
Any amp designed to IEC-60965 or 62368 in the EU must operate (and is tested by a nationally recognized test lab) at 230V +/-10%. That would be 253V high line and 207V low line. If the amp needs certification to operate in regions with nominal 240V, this would include Australia and New Zealand), the national differences approvals would add a 264V high line test. Virtually everything of any quality these days is designed to operate at a high line of 264V because it makes no sense to design multiple versions (at least with SMPS) because it would add more cost to the certification process than could be justified. The homogenization limits tolerances really do work quite well in practice, and in fact utilities have adjusted their generating and distribution voltages a few percent to improve compliance as well. Australia has some additional challenges, primarily around voltage regulation on long transmission and distribution lines with varying loads in the Outback.
-
That’s unfortunate.
-
Most repairs include a warranty on the repair. Did you follow up with them on this?
-
I posted before hearing the news...
-
If not in the UK, Italy isn't THAT far from the UK (though admittedly farther appearing since BREXIT)
-
Contact MarkBass and see what service options they have for you.
-
The following post is from TalkBass, ahead of you post about looking at a cheap 1300W x 4 channel Chinese amp. Yes, the information was provided and discussed by other members in detail. Some manufacturers understand the value that premium platforms like ICEPower bring to their customers. They also tend to follow safety and EMC rules, and avoid no-name amp solutions because they know the pitfalls in performance and reliability. Some manufacturers also understand how to exploit unpublished attributes of the ICEPower platforms to go farther than the published specs might (inaccurately) indicate.
-
The harmonizing of the UK to 230V nominal European standards means that the high line limits are the same. For amps that truly comply with CE under the CB scheme, they are tested at the high line limits, it’s one of the required tests that the amp must pass. Most of the “no name” amps available on the various websites do not carry valid CB safety or EMC certifications, and those that have the CE mark applied are often not eligible to carry that mark.
-
IIRC, some of us tried to warn you (didn't we?) We have a saying here... when you choose to sleep with snakes, it's likely that you will get bitten. It goes hand in hand with "buy once, cry once".