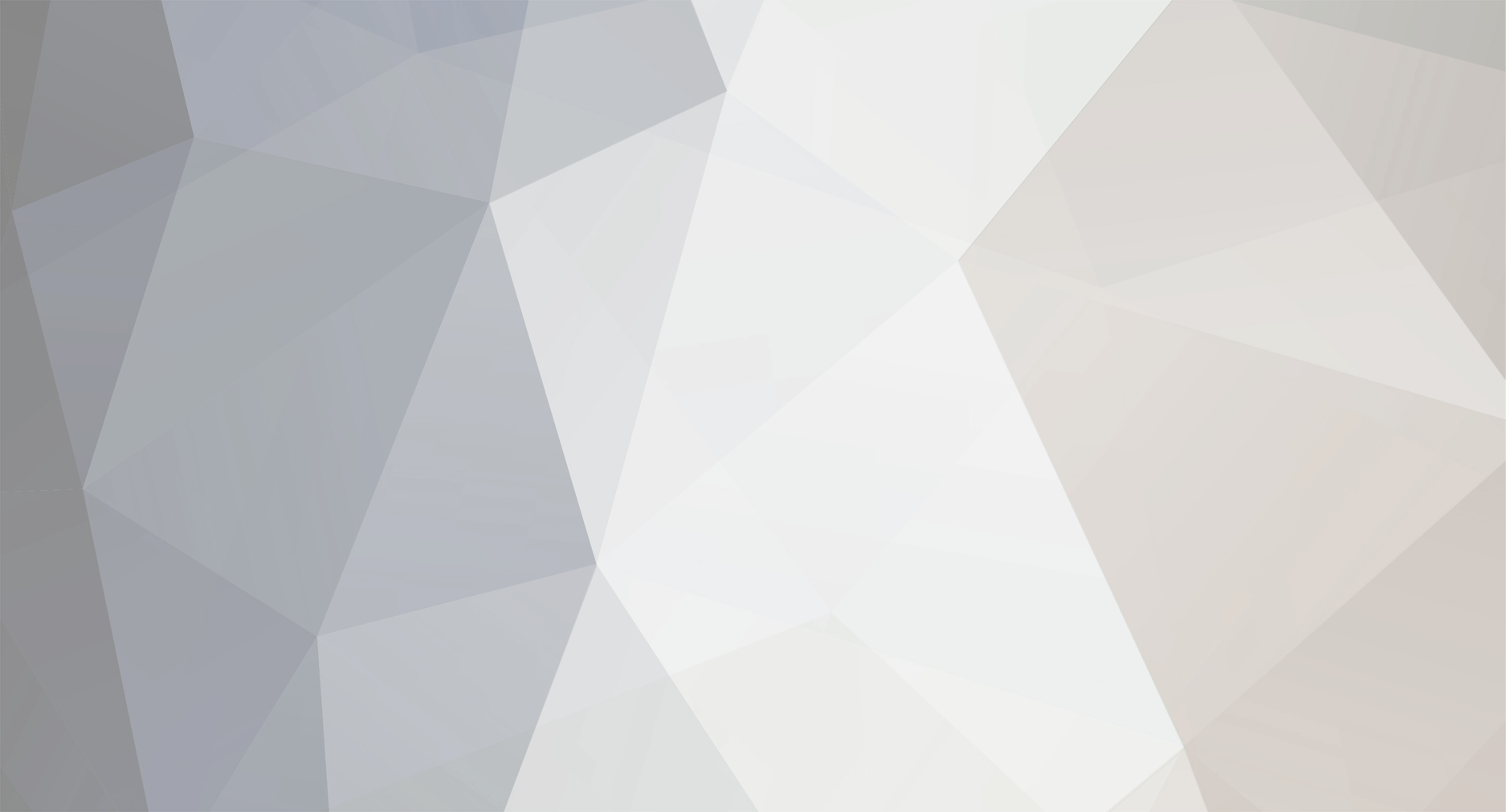
Thunderhead
Member-
Posts
71 -
Joined
-
Last visited
Content Type
Profiles
Forums
Events
Shop
Articles
Everything posted by Thunderhead
-
[quote name='Crazykiwi' post='305753' date='Oct 13 2008, 08:06 PM']There were a few problems reported with the early ones namely blown fuse holders and the valve biasing tolerances needed revising but these are very minor niggles. Everyone I know who owns one has been perfectly happy with theirs. Mine was one of the last, has been totally trouble free and I've regularly gigged with it.[/quote]Well, the two I've worked on both had blown and replaced main rectifier diodes (before I worked on them), bridged/repaired circuit traces where the originals had burned out, issues with the pots cracking their joints because the whole thing is badly designed with the entire preamp circuit board suspended from the (very low quality) pots and the jacks, plus nylon standoffs further back which make the whole thing flex as the transformers bounce up and down on the slightly too flimsy chassis, and stresses the front panel joints with every single movement. PCB-mounting pots is not inherently bad, but it must be done such that they are isolated from other forces - ie mounted on a board which is small, light and NOT connected to anything else. Likewise nylon standoffs are a GOOD thing when done properly because they allow movement and reduce shock on the board, but NOT in conjunction with other PCB-to-chassis parts - this is an absolute requirement in proper electronics design for mil-spec applications etc. The design and build quality is almost exactly like the very cheap guitar amps and low-end bass amps they made at the same time, not what should be inside a thousand-pound-plus professional bass head. It's good to hear you've had no trouble with yours (yet), but on the strength of only two that I've seen, BOTH with problems, I am in no hurry to own one. It's sad to have to say that because they're one of the best-sounding amps I've played through.
-
[quote name='wulf' post='305408' date='Oct 13 2008, 12:28 PM']The major surgery wouldn't be adding an extension to the fretboard but extending the cutaway to reach the new fret. It might be possible without adjustments but if you regularly go up there, the body is going to keep getting in the way.[/quote]Just reach over it. I regularly do that sort of stuff playing high up on a non-cutaway acoustic guitar, it's just a technique you have to learn. I would never even consider altering the cutaway - I literally never thought of it until I saw your post. [quote name='neepheid' post='305441' date='Oct 13 2008, 01:13 PM']I'm not sure I agree with that assessment. Couple of hours work? Great potential for damage to the instrument.[/quote] With respect, nonsense. Cut out a small area of finish from the front, and glue in a piece of rosewood that you have already shaped away from the bass, possibly with the fret already installed if as I think the slot will not be on the join, if necessary do a small amount of work on the fret height to get it absolutely right, and possibly touch up the finish around the edge. Where is the great potential for damage there? You will not be cutting any wood at all on the instrument. I'm not saying it's a home DIY job but no competent luthier would have any kind of problem doing that.
-
[quote name='rjb' post='305571' date='Oct 13 2008, 03:41 PM']It isn't cut and dried. It all depends on how the bass is set up. When changing to lighter strings the bass neck has of course flattened slightly when I've removed them, but in some cases I've opted to raise the nut very slightly and leave the action as it is at the other end. There's not [b]always[/b] a need to further raise the right-hand playing action to fix buzzing that it happening further towards the headstock. Lets be clear, I'm not saying an adjustable nut is a replacement bridge, but it [b]can[/b] be useful to make tiny tweaks. Works for me without any problems. [/quote]It's nothing to do with the bridge either! If the neck moves backwards when you change string gauge and causes buzzing, you need to adjust the NECK, not the nut, and not the bridge! The three adjustments don't do the same things, and you can't really use one to compensate for not setting one of the others correctly. I would say that at least three-quarters of the instruments I get for a set up have the nut too high, the neck wrongly adjusted and the bridge either too low (to try to get the action more comfortable) or too high (to try to cure the resulting buzzing), largely because people are afraid to touch the truss rod and usually don't have the tools or the experience to do the nut. But if you don't get the nut right, the neck right and THEN the bridge right - in that order - you'll never get it playing as well as it can. In my opinion, of course... The good news is that once the nut is right, it's right - it's the one you don't need to change again - and the other two adjustments certainly are user-doable... if you can play it you have enough manual dexterity to tweak it! (And yes, I do get paid for doing it so maybe I shouldn't say that .)
-
[quote name='redstriper' post='305606' date='Oct 13 2008, 04:40 PM']Thanks for the information, I have been trying to find out more about this amp with little success. The original owner's manual doesn't mention the amp power ! It does have the serial number, which is H4143. All the writing on the back has faded away, but I'm pretty sure it's a 150, there are 2 big blue round things inside, which I presume to be the power transistors.[/quote]No, those are the filter caps. The power transistors are the silver things - a sort of round dome on a lens-shaped base - on the bracket at the left-hand end as you look at it from the front. [quote]Can you tell me the mains fuse value ?[/quote]T2A for a 150 and T3A (T3.15A in modern spec) for a 250. You do need to make sure they are T (Time lag, AKA slow-blow or anti-surge) type or they will sometimes blow on power-up even with no fault. The speaker fuse is marked as a F (fast blow), and these DO occasionally blow for no real reason. I have been known to substitute a T fuse for customers with odd cabinets that can do it (eg 6x10" Ampegs and other things with unusual impedance curves)... but I wouldn't normally recommend that, the designer will have used the F type for a reason. Never increase the fuse value to stop it blowing, either - it means something else will fry instead. [quote]To return to the original poster's question - I don't know if it's a Mark 3, 4 or 5, (how can you tell)?[/quote]I can't remember the exact details of the early amps, but it looks like a Mk4 to me. Definitely not a MkV. [quote]I recently compared it side by side to 3 new amps - Hartke LH 1000, Ashdown ABM 400, Markbass 450 and an ancient Selmer Treble n' Bass 50. I wouldn't change it for any of those, but if I had to choose one of them, it would be the Selmer which was the loudest of the lot.[/quote]Valve amps do sound much louder for their rated power than solid-state, but even so I find that surprising! Those old Selmers are not even the loudest 50W valve amps...
-
[quote name='Lifer' post='305362' date='Oct 13 2008, 11:56 AM']Thanks for the replies! Using my amazing paint skills I've knocked up a new diagram I'm hoping that's right?[/quote]Very close! You made just one small mistake, which is that the pickup ground should go to the back of one of the pots, not to the tag on the tone control as you have it. (You probably knew that, but drew it wrong! )
-
[quote name='molan' post='223371' date='Jun 21 2008, 12:53 AM']To be honest the buyer's guide is simply a list of a few tube amps & some basic specs and a pic of each one but sounds like a good starting point. Hiwatt Custom 400 rocking in at the most expensive I think at $5,500! [/quote]I've worked on two originals of those and they remain the most powerful tube amps I've ever come across. I measured them at 445W RMS and nearly 700W peak distorted... They have fantastic tone at any volume and tremendous dynamics too, you can actually play them quietly just by turning down the instrument and using a light touch. Probably the best tube amp tone I've ever heard for bass - I didn't buy either of them because they were expensive, and weigh a ton (about 90lbs if I remember right)... and would need a serious cabinet to do them justice, although I did wonder about getting one of the original oversize Hiwatt 4x12"s and loading it with EVs (making an 800W cab). It's not just the power, the head is physically wide and won't fit neatly on anything smaller. I also loved the Trace Elliot V8 (clean - the overdrive mode wasn't very good, it killed all the bottom end), but they have build quality and reliability issues, and I had to pass on owning either of the ones I've been offered too.
-
[quote name='BassBod' post='299832' date='Oct 5 2008, 12:23 PM']From memory, this is a potential problem for some older amps (like my SWR220) but much less likely to cause a problem on anything designed in the last ten years or so (since phantom power has become commonplace). I run a passive transformer DI from a jack output, and connect that to the PA, which blocks it completely. Also has the advantage of never overloading, which seems to happen with a lot of active DIs when you connect a line level amp output. BB[/quote]+1 Those passive "cheap", "old fashioned", transformer DI boxes also sound very nice for instrument amp DIs too - much nicer than any modern active DI, to me. Transformers (even high-grade audio ones) have some limitations which actually make them sound very nice for slightly distorted signals, which the output of an amp often is even if it's not actually clipping. This is one of the reasons valve amps sound so good for both bass and especially guitar, since they all have output transformers whereas solid-state ones generally don't. I generally dislike active DI boxes entirely except for things like acoustic instruments where they do sound much better, partly because they are capable of reproducing everything cleanly but mainly because they don't load the instrument down like a passive one does (which doesn't matter when the signal is coming from an amp).
-
[quote name='The Burpster' post='305182' date='Oct 13 2008, 07:13 AM']Hummn an extra fret to that fretboard would require pretty major surgery I'm afraid, I guess not impossible but very expensive. ....[/quote] Shouldn't be... All it needs is to have a small piece of extra fingerboard fitted to the top, and a fret added. If you're really lucky the fret position will coincide with the end of the existing fingerboard so it will cover the join - although it doesn't quite look like it in the pic. It will involve carefully cutting through the finish on the top to make a good joint, but I wouldn't have thought it would be more than a couple of hours' work at most, and probably less. You don't even necessarily have to make it a full-width extension, if you only ever play the G string up that high - that would make it much easier since you wouldn't have to get the height and curvature correct across the whole width of the neck.
-
[quote name='redstriper' post='304960' date='Oct 12 2008, 07:02 PM']I'm just adding my experience to the pot. I think I have an AH 150, I say 'think' because it doesn't say anything about the model or wattage apart from GP11 on the front, which is the pre amp. It was part of a 1115 combo bought new in 1985 and I have recently removed the amp head and re housed it in a plywood sleeve to reduce the weight of the combo. I also replaced the Fane driver with a new Eminence neo unit to further reduce weight, but I digress............. The amp is excellent and has never had a problem in 23 years of regular use. I have tried lots of other amps and done many direct comparisons and I have not found anything that can give me the deep smooth tone that I get from this amp. It is very loud for the rated output and is more than enough for the 450 watt 8 ohm 15" speaker that I use with it. I would have no hesitation recommending a TE amp of this vintage, providing it has been looked after and the GP11 pre amp is first class.[/quote]The power amp number was probably written on the back in one of the little green boxes, but the writing usually fades. Do you remember seeing if it has two or four power transistors, when you had it apart? If two, it's a 150 (most likely if it came out of a combo) and if it has four it's a 250. You can also tell by the speaker fuse value, 5A for a 150 and 8A for a 250, but the writing often fades away too. (This is a brilliant piece of design that all solid-state amps should have by the way - just last week I fixed a 150 combo that some idiot sound engineer had plugged a DI box into the second speaker out of - I'm not sure exactly what then happened but the amp's speaker fuse blew, which means that if it hadn't, probably in any other amp it would have taken out the power transistors instead. 10 seconds and 35p to fix it, instead of an hour's work and a few pounds in parts. I didn't even charge the customer, I never had to move the amp into the workshop!) I've also compared one of these amps to a new 600W Ashdown, through the same cabinet, and the AH150 held its own - seriously. It had much more punch and dynamics, and although it probably wouldn't quite shift as much air it would certainly stand up at least as well in a mix. It just sounded better, too...
-
[quote name='obbm' post='304182' date='Oct 10 2008, 09:12 PM']I think you will have great difficulty finding a stacked log + ganged log/antilog with centre detent for vol/blend.[/quote]I would say impossible without custom ordering it from a pot manufacturer. But there is another way - you can use a standard dual-concentric linear, with the pickups wired in series - that way you only need one pot for the blend. It works fine - I had a blend pot like that on my last bass, and actually a linear pot is OK for a volume as well. To connect it, you wire the pickups in series (ground of pickup 1 grounded, hot of pickup 1 to ground of pickup 2, hot of pickup 2 to volume pot, while keeping any separate shields grounded), then connect the blend pot in parallel with the volume pot except that the middle tag is connected to the junction of the two pickups instead of the output jack. The volume taper is pretty good, since the voltage sum of the two pickups is always equivalent to either pickup alone, no matter where the knob is set (assuming they have roughly equal outputs), and doesn't have the slight drop that you get in the middle of a normal log/antilog blend pot. The both-pickups sound is somewhat different from parallel blending though, it's a little darker and more midrangy. However, if you're not bothered about a tone control the simplest by far is just to go for two volumes wired exactly like a Jazz. This also has the least compromised volume and tone when both are full up.
-
The old Traces are great - I think the peak for both tone and reliability was the MkV series, but they're all good up to and including Series 6. (Actually my current AH200 is a Series 6.) There's no particular service issue with any of the older ones in that they use pretty standard parts, but they ARE definitely getting on a bit and you can expect some issues. Be careful of ones that have a history of repair work - the circuit boards are sometimes damaged (including by poor workmanship) and they can be difficult to make really 'right'. The graphic EQ sliders in the really old amps are a size which aren't too easy to get these days either. Unfortunately after Series 6 the bean counters got in charge and progressively ruined Trace until they came out with some really poorly designed and built crap in the 90s (particularly most of the guitar amps), some of which sounded good but none of which were really reliable, and unfortunately that even applies to the last valve bass amps - including the mighty V8, sadly. The warranty returns must have become a major liability, having seen the failure rate that I did as a tech back then. You'll also notice that the older amps sound louder in proportion to their rated power than the later post-Series 6 models. I don't know for certain since I'm not connected to the company, but I saw the warning signs on my workbench long before the buy-out by Gibson, and I don't think the popular version that Gibson 'ruined' Trace Elliot is at all correct - if anything, Trace did it to themselves and Gibson had to pick up the pieces, especially on things like transformer replacements and then a re-design on the Velocette/GoldTone guitar amps, and eventually sold the brand on again. Happily the new Peavey-made amps look a lot better, I've seen precisely one failed one so far (with a blown mains transformer though).
-
[quote name='rjb' post='304709' date='Oct 12 2008, 09:56 AM']They are useful, the JAN IIs were crap and prone to breaking, but the JAN IIIs do the job well. You can, for example, drop lower gauge strings onto a bass and reduce the increased buzzing from lower tension without having to touch the bridge or trussrod.[/quote]But that's the wrong solution. If the string tension is lowered and the neck moves backwards as a result, you NEED to adjust the truss rod, period. Anything else is addressing the wrong part of the equation. Two wrongs don't make a right - if you raise the nut instead you will possibly cause intonation issues at the first position and may still have buzzing in the lower fretted positions. There are some things that need to be adjustable on an instrument because the right setting varies with string gauge, playing style and even climate, but the nut is not one of them. There really is only one correct nut height, regardless of string gauge or playing style - just a hair higher than the first fret - and once it's set it should never need changing unless you fret dress or refret the bass. Raising the nut when the neck needs adjusting is like trying to fix a wheel alignment problem by changing the tyres... I admit this new version is better than the original brass thing with individual string screws they used to fit (which I what I mistakenly thought the thread was about - I had one on an early Warwick Dolphin, and always hated it - and I've had to fix quite a few others for customers), the only advantage I can see to this one is that it's easier to set for someone who doesn't feel confident enough to do their own nut filing - which is maybe why I haven't seen any to set up, since the nut is the major cause of factory set-ups being poor on most instruments. I'm also still not convinced it will sound as good, since the top part is still resting on two little screws not fully attached to the neck, but maybe I'm just old-fashioned .
-
[quote name='rjb' post='304703' date='Oct 12 2008, 09:36 AM']Errrr, so use a quarter turn? [/quote] Ah! I see now... I thought we were talking about the old version. My mistake! That will teach me to post before having my coffee I still can't see the point, personally. Once a normal nut is fitted correctly you shouldn't have to adjust it, so why not just do that?
-
[quote name='Alun' post='304505' date='Oct 11 2008, 06:29 PM']Hi all. Just looking at the Just A Nut over at the Warwick online shop and wondering if anyone has ever tried one on another bass?[/quote] I wouldn't bother. I've never liked these things - they don't actually give you quite fine enough adjustability (it's possible to find one setting is too high, and the next half turn lower is too low - so you end up having to file the groove slightly anyhow), they can easily turn by themselves when changing strings so you have to check the set-up every time, and I suspect they affect the tone. And you shouldn't ever need to adjust the nut height anyway, once it's right in the first place... just an overcomplicated solution in search of a problem, basically. Just put on a normal nut (brass if you like that) and cut the grooves correctly. Job done - permanently. (Just for what it's worth, when I have to set one of them up, I superglue the adjusters once I've got it right. Saves it needing setting up again when the unfortunate owner changes strings and accidentally moves them! You can always undo the glue by lightly heating the screws with a soldering iron.)
-
[quote name='thepurpleblob' post='304563' date='Oct 11 2008, 08:46 PM']To add a bass (cut) reproduce the existing tone (which is really a treble cut) exactly except the capacitor needs to be 0.0047uF (ish). The existing connection that went to the output jack now goes to the centre tag on the bass cut pot, the cap is soldered between an outer terminal and the case and the case is grounded somewhere handy.[/quote] No, that will just produce another treble cut with a higher roll-off frequency. To make a passive bass cut, the signal needs to go THROUGH the pot and cap, not to ground via it. You have the cap value correct at .0047uf (ie 1/10th of the value of the normal tone cap), but you need to wire it like this: First, connect the pickup hot connection to the normal (treble cut) tone control middle tag, with the normal tone cap between the anticlockwise tag and the pot casing, exactly as standard. Now connect the same pickup hot/middle tag connection to the clockwise tag on the new bass-cut pot. Connect the bass-cut cap between the clockwise and middle tags of this pot. Then connect the middle tag of this pot to the clockwise tag of the volume pot, and the middle tag of the volume pot to output as normal. None of the connections on the bass-cut pot should be grounded. Obviously the pickup shield (bare wire), the volume pot anticlockwise tag, and the casings of all the pots should be grounded as normal. It must be this way round (pickup > treble-cut > bass-cut > volume) or you will lose almost all the output when you turn down both tone controls. It will still get quite a bit quieter anyway, will passive controls. It doesn't actually matter which way round the connections on the bass-cut pot are, if it's neater to wire it the other way round - as long as you use the middle and clockwise tags. I would also connect the unused tags of both tone controls to the middle tag, as it slightly increases reliability and can reduce noise when turning them, especially the bass-cut.
-
[quote name='Mr. Foxen' post='299038' date='Oct 4 2008, 12:16 AM']Dunno if this is a lucky score or an extra wardrobe. Figuring its a lot like a 18" folded horn a lá Acoustic 361. Think the 150W is wrong from the valves I can see. Anyone know anything about these?[/quote] I've never seen one before either, but it looks like another of the 'also ran' British valve amps from the very late 60s or early 70s, and might have been built by one of the same subcontractor companies that did one of the brands you're more familiar with (although that doesn't mean the circuitry is the same, necessarily). 150W is not out of the question from four EL34s (which is what that looks like), although it's at the upper limit. If they're run over the specification ratings, which many companies did, that sort of power is definitely reachable especially if it's quoted at a higher distortion figure than the 1% normally used for hi-fi type amps. Standard Marshall Super Lead and Super Bass amps from this period usually measure 130 to 140W at the onset of audible clipping (probably about 5 to 10% distortion if you really care!). The mains input connector is an old in-line Bulgin type, and is illegal these days. It should be considered dangerous since it's never possible to make the cable retention effective on them, they are simply a poor design and always were. If you want to keep the socket on the amp original, you can get right-angled versions of the plug which are much safer, although still illegal - all these connectors are only rated for low voltages now. Of course you may still use it without the Police knocking on your door, but it may cause trouble if you ever want to sell it on via a shop or even to use it at some venues where Health & Safety rules are enforced. Personally I would replace it with a modern IEC pair (AKA "kettle lead"), since it's safe, legal and means that if you ever break or lose the power cable you can easily find another. This does involve a small amount of work on the chassis as an IEC socket will not quite go through the same hole, but five minutes with a file will make it so. Old speakers and cabs do lack clarity, definition and power handling - but NOT tone! Some of them sound wonderful, IF you want that old, soft, warm, lo-fi bass sound. It's not the SAME as a modern bass sound, but if you DO want it then the new stuff won't do the job either. But be careful, because most old cabs were never really capable of taking the power of the amps even when new, and blown drivers are very common - and not all the problems show up at low volume.
-
DO NOT rout the body or do anything drastic like that!!! It's totally unnecessary. You simply need to add a shim at the body end of the neck pocket. There's no need to raise the entire neck either, in fact it's far less effective - the relative lengths of the neck pocket and the neck itself mean that a very small movement at the end of the heel will make a much larger difference at the headstock, and create a small back angle on the neck which will drastically lower the string height over the end of the fingerboard. This is absolutely standard practice with bolt-on necks where the angle isn't quite perfect. You also don't need fancy materials, stiff cardboard is ideal - Fender used this or thin fibreboard from the 1950s onward, and still do on instruments without a neck-tilt mechanism. Simply cut a piece which fits into about the last quarter of the neck pocket, and preferably covering the two end screw holes so the screws will push through it rather than missing it, as this helps avoid causing an upturn at the very end of the neck. I would use a piece of something like a cornflake packet to start with, and if that isn't enough just find something a bit thicker and of the same type - or you can use a couple of pieces on top of each other. (That's exactly what I use, and I do this sort of thing professionally.) Don't be afraid of it 'killing the tone' or any other popular myth. In fact, there's good evidence that these traditional shims actually sound better than the so-called "improved" method of making a tapered wood wedge which you will sometimes hear recommended. Think about it... many vintage Fenders have cheap shims from the factory and they're some of the best-sounding instruments ever made. If you really can't live with 'cardboard in your bass', a small piece of wood veneer is a good alternative, and you could glue it to the floor of the neck pocket if you want to make a really good job (after you've found the right thickness of course). Gaffer tape is not the right material though! If the neck is still too straight, you'll either need to give it more time to settle down (if it's been left for months with no strings you can expect it to take about the same amount of time) or use a slightly heavier string gauge, at least until it does. 'Dead straight' is not a problem though - provided that it is, and not back-bowed.
-
Rickenbacker 2006 model 4003 in Jetglo ('black' to the rest of you!), totally standard except I took the bridge pickup cover off (doesn't everyone?) and rewired the pickup to RWRP to help with the hum (why doesn't Rickenbacker do this?!). You know what it looks like!
-
little idea - stereo jack sockets in passive basses
Thunderhead replied to ahpook's topic in Repairs and Technical
[quote name='Jean-Luc Pickguard' post='298906' date='Oct 3 2008, 08:45 PM']I guess that would help if the original socket was one of the flimsy cheapos, but I always put in a standard mono switchcraft if I replace the socket in a passive bass/geetar & they're sturdy enough that the contact doesn't lose its spring.[/quote]It's not the contact losing its spring that is the usual problem - it's the inside of the barrel getting corroded and making poor contact, and Switchcrafts can go like this the same as any lower-quality jack. This contact is not sprung at all (unless you're using something like a Planet Waves cable) so it is inherently a pure 'touch' contact and prone to making a poor connection. ahpook is correct that using a stereo jack is better, exactly because it provides a positively sprung ground contact. In fact, it's [i]always[/i] good practice to use any unused connections or poles to duplicate the ones you need, in any application. It always increases reliability with no downside. It's not necessarily a reason to use a more expensive part in every case, but if you have done it makes no sense to not connect the other contacts as well - and yet you very often see things like double-pole switches with only one half used. -
[quote name='Spikeh' post='296644' date='Oct 1 2008, 02:16 PM']A bit of blurb I found on another forum in relation to solid state amps: OK, so, this pretty much explains my current situation - I run an Ampeg SVT-4 PRO, which has the following output power ratings: 1600 Watts Mono-Bridged @ 4 Ohms (1200 Watts Continuous) 1200 Watts Mono-Bridged @ 8 Ohms (900 Watts Continuous) 2 x 900 Watts @ 2 Ohms (600 Watts Continuous) 2 x 625 Watts @ 4 Ohms (490 Watts Continuous) 2 x 350 Watts @ 8 Ohms (300 Watts Continuous) I currently run it in to a single Ampeg 8x10 running @ 4ohms through the single mono-bridged output, whice gives me the maximum output I can get with the amp, which is great. However, I'm looking at "downgrading" and getting two new cabs to replace the single 8x10 and its too damn heavy. Looking at getting a 4x10 @ 4ohms (EDEN D410XST) and a 1x18 at 8ohms (EDEN D118XL). I'll be running them in stereo mode in order to take advantage of my crossover control. Am I right in my calculations here: Total cab impedance: (4/2)+(8/2) = 6ohms Total "visible" impedance to the amp in stereo mode: 6/2 = 3ohms So the mimimum load on the head would be 3ohms, which puts me between 625W and 900W output per side? The EDEN D118XL is 500W output, and the EDEN D410XST is 1000W output. Does this mean that the D118XL will be overloaded? Or will the wattage be added together too? I don't know how this bit works - I'm afraid one of the bi-amps will blow the D118XL?[/quote]It's much simpler than you think! The two sides of a stereo power amp work totally independently when they are not bridged, and only deliver the amount of power that each can into the impedance that is connected to it. So one side will deliver 625W into the 4-ohm 4x10", and the other will deliver 350W into the 8-ohm 1x18". Both are well within the ratings of the cabs, and everything will be fine. There will be less power going to the 1x18", but since one 18 is likely to be a little bit more efficient than four 10s, it will probably work out about right overall - you should be able to balance it with the crossover anyhow. Just by the way - cab power ratings are [i]input[/i], not output. Your calculations for combined impedance would also be wrong, if the cabs were actually working in parallel from the same amp. Total impedance in parallel = 1/(1/Impedance1 + 1/Impedance2), so a 4-ohm and an 8-ohm cab in parallel is 1/(1/4 + 1/8) = 2.67 ohms. 2/3 of the total power will go to the 4-ohm cab, and 1/3 to the 8-ohm. Hopefully that makes sense, even if you don't need it!