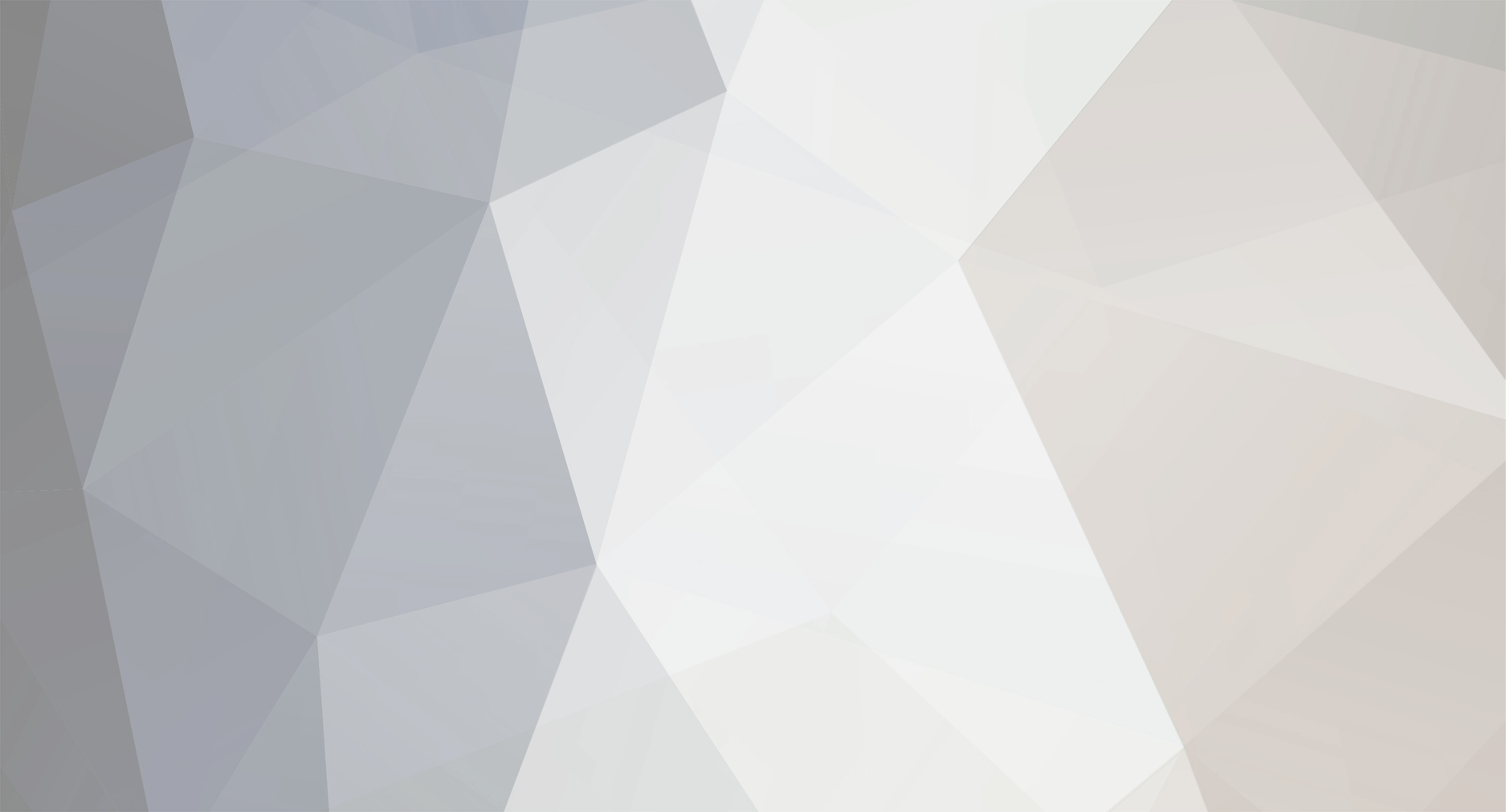
rockpig
Member-
Posts
32 -
Joined
-
Last visited
Content Type
Profiles
Forums
Events
Shop
Articles
Everything posted by rockpig
-
the buzzing is probably a combination of bad or non existing shielding and ground loops. to rectify the shielding paint the cavity with about 4 coats of carbon paint. you can get that here [url="http://www.tonetechluthiersupplies.co.uk/vmchk/Lacquers-and-Paint/Conductive-Shielding-Paint/View-all-products.html?TreeId=16"]http://www.tonetechluthiersupplies.co.uk/v....html?TreeId=16[/url] Or cover the inside of the cavities with copper foil. check out here [url="http://www.axesrus.com/axeElectronicsWire.htm"]http://www.axesrus.com/axeElectronicsWire.htm[/url] the ground loops will require re-wiring in a far more complex manner. I suggest reading this article and anything else you can find on line and then applying the ideas to your circuit. [url="http://www.guitarnuts.com/wiring/shielding/shield3.php"]http://www.guitarnuts.com/wiring/shielding/shield3.php[/url] as for the more honky sound chances are you wired the pick ups out of phase.
-
I've used all of these in the past. David Dyke is probably the best as he has been supplying tonewoods for 30 odd years. [url="http://www.lmii.com/"]http://www.lmii.com/[/url] Luthiers mercantile an american company very broad range. [url="http://www.tonetechluthiersupplies.co.uk/"]http://www.tonetechluthiersupplies.co.uk/[/url] based in the north of England, range can be a bit limited got some spectacluar burl maple off them one time. [url="http://www.luthierssupplies.co.uk/"]http://www.luthierssupplies.co.uk/[/url] David Dyke see above. [url="http://www.tonewood.ca/"]http://www.tonewood.ca/[/url] Canadian checkout there website for some stunning figured timbers. [url="http://www.guitartonewoods4luthiers.co.uk/"]http://www.guitartonewoods4luthiers.co.uk/[/url] UK based very quick got a maple back and sides set of them, bought lowest grade figure and it had a stunning flame across the sides and a very nice flame to the back as well. [url="http://www.stewmac.com/"]http://www.stewmac.com/[/url] does some woods but is more of a specialist tools shop. hope this helps.
-
if you're looking to do it yourself you can get the materials from here, [url="http://www.smallwonder-music.co.uk/"]http://www.smallwonder-music.co.uk/[/url] While inlaying the block shapes is fairly straight forward you'd probably want to do it with scrap materials a couple of times just for practice first. If you're planning on paying someone to do the work then unfortunately it is time consuming and will cost. Since it's an Ibanez the neck pocket will be fairly standardised so you could look for a replacement neck with block inlays, the advantage of this would be you can put the old neck on if you want to sell it later.
-
try tonetech in the uk [url="http://www.tonetechluthiersupplies.co.uk/Lacquers-and-Paint/Conductive-Paint/View-all-products.html?TreeId=11"]http://www.tonetechluthiersupplies.co.uk/L....html?TreeId=11[/url] the above link should be what you're looking for. But I would recomend using an undercoat of any wood primer unless the cavity is already painted.
-
here we go with another update months of inactivity then plenty of spare time and look what happens. fingerboard went on today, now the neck shape needs to be carved and then fretted. got some stainless steel fret wire from LMI so will give that a go.[attachment=34203:DSC00617.JPG]
-
another update work and holiday have got in the way and have only had time to get abck into this over the last 2 weeks. so here is the progress since last time. fingerboard of macassar ebony bound with the offcuts from tapering it. with a contrasting maple veneer. Back plate of redwood to match the top glued on and the edge radiusing and body shaping started. next fingerboard on and finishing. I've been thinking about the circuit for this instrument and am currently chasing up martin sims to see if I can get hold of one of the preamps from his enfield basses. Also I am thinking about using Q tuner pick ups. Any feed back that could be offered on either would be appreciated
-
David Dyke is probably the best source of top quality tonewoods in the UK. [url="http://www.luthierssupplies.co.uk/"]http://www.luthierssupplies.co.uk/[/url] he has an online catalog but all orders are by phone. the plus is you often get to speak to the man himself and will cutt to your dimensions if the timber is available. ohters you could try are [url="http://www.tonetechluthiersupplies.co.uk/"]http://www.tonetechluthiersupplies.co.uk/[/url] [url="http://www.lmii.com/"]http://www.lmii.com/[/url] just as an aside, having recently built an acoustic guitar in cherry I wouldn't feel comfortable with a cherry neck unless it was reinforced. since you are already using a walnut top why not go for a five piece neck with two thin strps of walnut between the cherry
-
a bit late now the job's done but, next time ,or in a similar situation you could bend the veneers while gluing them. be slightly tricy with this job and probably take longer to do. so come to think of it ignore me
-
japanese saw for the neck. but the body was with a coping saw. walnut smells just as you would expect when cutting it a very pleasant experience, left me a bit peckish though
-
latest update and some more pictures. Having recently spoken to a luthier about brushable waterborne lacquer I think I will try one of these in a gloss finish. also just finished an acoustic guitar in a similar lacquer sprayed on over french polish undercoats. the results were pretty good so brushed on lacquer over the polish is going to be hard work but achievable at home without poisoning myself with nitro spray can fumes. Anyway; important bits, the pictures, these show the body wings going on, with a contrasting veneer of maple between the front and wings. the last pic shows the fingerboard blank placed on top just as a teaser.
-
wait until the stain hits that maple and all the figure pops out it will be stunning. here's a pic of something similar I did for a friend
-
Quick update my workshop is a box room off the lounge of my flat but it's functional. the bass will be a natural finish probably in nitro celulose lacquer maybe pre cat stuff. french polish would be nice but not really tough enough. I a gree there are ricky elements in the shape and I was stealing from spector in treble horn. the lower bout is kind of jazz bass really and the top horn is sort of ricky meets modulus. extends a long way for balance.
-
here are some pictures I have been taking to document the build of the second bass I have made for myself. Started last august been slow progress job gets in the way too much. Just thought I'd share and maybe encourage others to have a crack at knocking one up themselves. the instrument will have a redwood back and front with black walnut body wings and a three piece neck through made of maple and mahogany
-
Hey all looking to off load my L5500 lovely bass but I need the money to complete a second 5 string I'm building and got a wedding in oz to go to. so having to part with my old friend. Bass is in excellent condition with only a couple of minor scratches that don't go through the lacquer. It is one of the first 5 strings G&L made and has the EMG pickups that were standard to this model. I beleive it is from 92 or 3, comes with the original hard case and certificate of authenticity signed by leo fenders widow. £750 PM me if your interested.
-
the super glue and bicarb trick is the best. use good quality super glue like lok tite.
-
veneers are generally only 0.6 mm thick so I can't see how they would make any difference to the sound if you onlt use 1 or 2. or if your good with tools you could make a replacement cover for the pickups out of your prefered wood.
-
number 4 all the way.
-
hello all. I've been here for a bit but didn't read about intros until recently as I;m a bit lazy. Anyway briefly I'm an Aussie living in Edinburgh and am just finishing the last couple of monthes of a 2 year musical instrument making course in Glasgow.
-
tung oil gives a nice finish is cheap easy to apply and food safe so you don't have to worry about getting it in your mouth. smells quite nice too.
-
heres some I have around the house. left to right top to bottom indian rosewood, californian redwood x2 spalted maple, flamed ash, alder macassar ebony, bloodwood, amboyna
-
try french polish rubbed on by hand looks stunning very thin, let's the wood breathe. however less hard than spray lacquers but very easy to touch up.
-
-
This post cannot be displayed because it is in a forum which requires at least 1 post to view.
-
hide glue is the best option as anyone doing further repairs later on will expect hide glue on this kind of instrument. it works the same as other glue you just have to be aware that it works best when it and the pieces being glued are hot. the glue should be mixed up fresh and will need to be cooked at a gentle simmer for about half an hour before use. the break should be heated with a hair dryer before applying the glue. if the wood feels hot to touch this is good. the glue must be applyed and clamped before it gels this only takes about two minutes so do a dry run first and have all your clamps and cauls set out ready to go. heat the pieces to be joined apply thge glue clamp done.
-
my first tip would be don't use a dremel for pick up route. it will not be able to cut deep enough. next be very careful a router will completely shred a finger if it so much as touches it. always unplug the thing when changing bits. after that bit of gruesome seriousness do some practice on bits of crap first and learn how the router kicks. as far as buying goes bosch makita or dewalt. relatively cheap but effective I would say a bosch laminate trimmer.