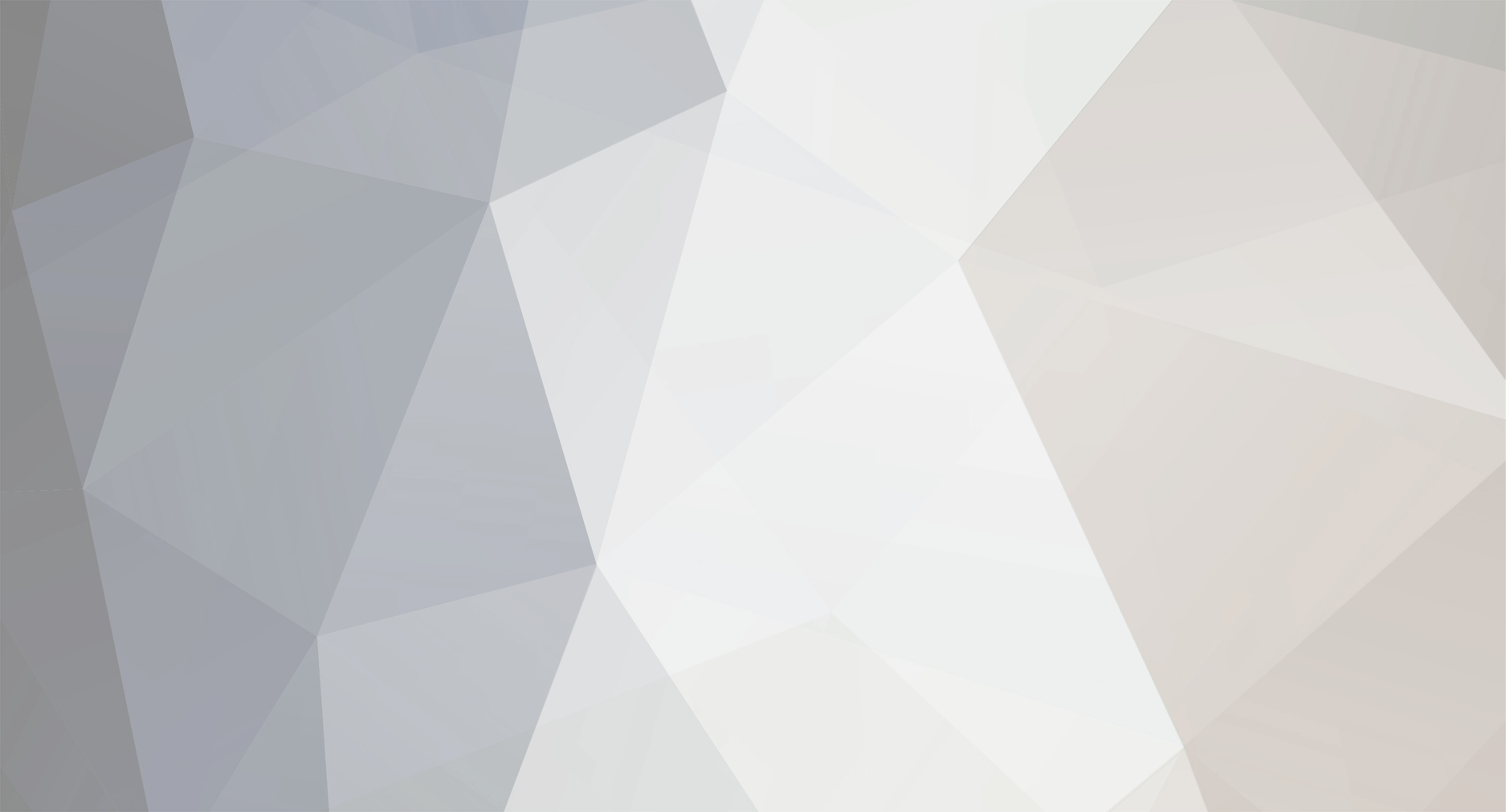
Wonky2
Member-
Posts
663 -
Joined
-
Last visited
-
Days Won
1
Content Type
Profiles
Forums
Events
Shop
Articles
Everything posted by Wonky2
-
Two pic ups - schertler stat b and upton revolution
Wonky2 replied to Wonky2's topic in EUB and Double Bass
Anyone used the Upton pup? -
Hi folks As i near the completion of my broken bass repair, my wandering mind has turned to pickups.... I initially set a faitly low budget but after reading many threads, reviews and opinions i came to the conclusion the most players seem to go on what looks like an expensive journey trying pick up after pick up to get a tone true to the bass and limit feed back issues, to name but a few issues.... So, i thought id up my budget. I have warmed to every review ive read on the upton rev solo pickup but cant seem to find a uk supplier ? Can anyone help ? Second option is, i have seen a barely used/ as new schertler set b set for sale.... This is an expensive set up but i have made a chance offer to the seller and he is considering it (considerably lower than his asking price) ....... If he agrees, it would be chance to go straight in with a peice of reputable kit at a low cost.....so i think its the bargain opportunity appealing to me here as much as anything ??? Any views on the two ? And any help with a uk supplier for the upton pup ?
-
Fender USA 70's Vintage Hot Rod Jazz Bass - usa - SOLD ON FACEBOOK
Wonky2 replied to Wonky2's topic in Basses For Sale
-
For those who like the acoustic sound, watch Austin to Boston. Fantastic road trip film/ docu For those who like the urb, (no, not the upright bass) watch the culture high.
-
Buying a broken bass for repair - amateur repair with pics
Wonky2 replied to Wonky2's topic in EUB and Double Bass
I thought that would likely be the case...... I prefer the unfinished look and id imagine it will have some degree of tonal influence, even if only minute... More sanding tonight...... Cant wait to get the thing strung up but must resist the urge to plough on with out care.... -
Buying a broken bass for repair - amateur repair with pics
Wonky2 replied to Wonky2's topic in EUB and Double Bass
So tonight I've been at it again....... Another (I think) final coat of the sickens to the neck heel to get the finish just a tad darker.... I had wired wooded it flat again too as there were just a few specs that were not as I'd like..... Some tiny places just don't seem to be getting darker, possibly a bit of glue left in nooks I cannot sand too well ? Hardly noticeable but still ..... Also,my he finger board.... When I last worked on it (before the weekend) I had Danish oiled the neck...... I think some may have gotten onto the fingerboard and in places some finger prints on the finger board....well, it seemed to contaminate the finish and dull it down This was kind of a good thing though really as the high gloss finish that the laquer had given, although very good, I felt it should really be dulled somewhat as it seemed out of context with the rest of the bass....... So, decision was made for me, I had to remove the Danish oil contaminants now anyway.... I took some 0000 grade steel wool and flattened the finger board off again, this also provided good opportunity to blend and smooth the transition from neck to finger board on the edges of the neck. I didn't have any really fine wet n dry paper left to final finish it so i used some cutting polish (autosol !) it worked a treat. Removed the swirls the wire wool had left and gave a finish somewhere between dull/ Matt and gloss, much like the original finish. I've checked the finish now to see how it deals with finger grease/ sweat and it doesn't leave horrible marks like it did before.... So hopefully this finish will be good. A final buff with a clean cloth to make sure no contaminants will affect the strings and I think I can move on. (I'll get it strings up one day I promise!) After that I was back onto bridge fitting. Sand paper on the deck again and back and forth about ten million times. I now have the height right at the feet and it's time to go down a few grades on the paper and try to get a closer fit. This is very time consuming and labour intensive. The bridge will need thinning on the front side as it's quite thick and then I'll be onto marking up the night from the fret board and applying my radius template..... Can I ask, does anyone apply a finish to the bridge such as Danish oil or are they to be left bare..... -
Buying a broken bass for repair - amateur repair with pics
Wonky2 replied to Wonky2's topic in EUB and Double Bass
When im finished ill try and put pics up better from photobucket and maybe do a write up, im sure others may feel they have the skills to do the donkey work like i have and save on luthier costs.... Maybe taking it to a luthier for a final set up afterwards to keep costs down. Its just wood. -
Buying a broken bass for repair - amateur repair with pics
Wonky2 replied to Wonky2's topic in EUB and Double Bass
Yes, i have done a few decent bass/ guitar set ups beofre and i know just hiw important nut hight or string slot can be... Never done frettless though so new territory for wonky The heel varnish to neck finish on the pics on the web site (great site by the way) ive done it differently, most due to not seeing any before but also i doubt ill be venturing down that far for a while yet ! My finish..... Almost done.... Another 0000 grade wire wool session over the lot before final finish i think.... -
Buying a broken bass for repair - amateur repair with pics
Wonky2 replied to Wonky2's topic in EUB and Double Bass
Thanks guys.... Thanks for the link ..... -
Buying a broken bass for repair - amateur repair with pics
Wonky2 replied to Wonky2's topic in EUB and Double Bass
Great, thanks for that info.... If I'd have gone off what I "thought" I'd have been tryin to get a far lower action (ignorance is not bliss) The reason I asked was every bass I saw seemed to have an action of about what you have said,10mm, so I figured it should not be as low as I had originally thought..... It will take some getting used to ! Second coat of sickens has just gone on after wire wool flat down... Colour is a great match now...... Should be able to oil neck tomorrow then it's just the bridge.... (I've been putting it off Hahahah) I can't tell you how much I am dying to get it strung up !!!!!!!!! -
Buying a broken bass for repair - amateur repair with pics
Wonky2 replied to Wonky2's topic in EUB and Double Bass
If possible, can any uf you guys take some measurments of string hight on your bass at end of finger board to bottom of string ? I know they will all be different but an average would give me a rule of thumb starting point ....... If you could measure string hight at fb end to bottom of string and list : E= xx mm A=xx mm D=xx mm G=xx mm It woul be a great help. And for my own clarity, am i right to think in general the radius should be lower on e side ? -
Buying a broken bass for repair - amateur repair with pics
Wonky2 replied to Wonky2's topic in EUB and Double Bass
Great! Ill give it a go... -
Buying a broken bass for repair - amateur repair with pics
Wonky2 replied to Wonky2's topic in EUB and Double Bass
Good idea Ive got a guy local whi i kniw and another i dont know but is happy to have a chat.... Not sure either know much about repairs but both good players so some comparrisons wiill be good.. -
Buying a broken bass for repair - amateur repair with pics
Wonky2 replied to Wonky2's topic in EUB and Double Bass
Ok, so tonight was colour refinish on the neck heel.... Ive used sikkens mahogany 045. The match is great! Bit more to do once its cured, wire wool and another coat should see a good colour matched gloss finish which makes the repair invisible, you simply cannot see it. Another coat should even it out and take it just that bit darker to match perfect... So a bit more tomorrow and then its onto danish oil for the neck.... -
Buying a broken bass for repair - amateur repair with pics
Wonky2 replied to Wonky2's topic in EUB and Double Bass
Thanks for your kind and constructive comments The feet are quite thick and from looking at pics of bridges on basses i figured they need quite a bit coming off them, as much as the reasons you give (yes perfectly valid) i figure the thicker the feet are the less resonance will transfer from string through bridge to body... So yes, plenty to come off them as most i see are probably only aroun 4mm thick by sight.... One area i need advice on.... Cut bridge height. My intention is to set adjusters to mid point, then with bridge positioned correctly in respect of f hole notches and centred, use a straight edge lay on the neck to transfer its projected angle to the face of the bridge. I will then add appox 10mm too this line and use this eeference point to offer up the paper jazz radius template i have. This should give me a close/ rough line so the once cut shaped it should be close. After notching out for strings this 10mm difference will be reduced to perhaps 6mm, which hopfully should give s good action from which i can use the adjusters on the bridge to dial in or out as required. If any one see's any problems with my approach please do speak up before i end up having to but another bridge hahaha... -
Buying a broken bass for repair - amateur repair with pics
Wonky2 replied to Wonky2's topic in EUB and Double Bass
Final coat has given a finish which has made the reapair COMPLETLEY invisible .... I am so happy, i hooe the finish cures very hard and lasts a long long time Its likley the learning curve will continue long after the full repair is completed in terms of the longjevity of the repair but i see no reason it should fail in any way .... Again, this isnt a high value or crafted bass.... Its a stentor 1950 student bass, rrp)£1700 , cheapest i can find on line is b stock at £850.... The bag it came in cost more than i paid for it so i am deffinaitly winning here... Ive seen similar basses with repairs that dont look half as good going for £600/550 so i am very happy indeed. just cosmetics niw and the bridge and i can get to hear its voice fir the first time ! Pic below: they are reflections , the finish is flawless -
Buying a broken bass for repair - amateur repair with pics
Wonky2 replied to Wonky2's topic in EUB and Double Bass
Tonight i have been able to rw finish the finger board.... Its not an expensive ebony board, its possibly maple ? Anyhoo, the hole where the stud/bolt has been counter sunk was filled and flatted several times before a good overall key with some fine grade sand paper. Next i applied several coats of matt black enamel paint and left to cure... Once hardened i used wet n dry paper with water to flatten the finish further to what was a very pleasing finish with no evidence of said hole/ bolt/ filler..... I considered leaving it at this but feared the finish may wear or degrade strings, so i have opted to finish with several coats of clear hardened acyryllic laquer. The result is fantastic ! I am really pleased with the result! Next is restain and gloss neck heel and apply danish oil to back of neck.... Then its just the bridge..... "Just" he says..... I fear the bridge will take a very long time to get right. Cant tell you how much i have enjoyed this and whats more it has proved to be a succesful repair so far...... -
-
Cheers chard thats cured it Can't believe I didnt put the actual link in the original post ! Thats almost as bad as my log in fau par..... Maybe even worse ? Errr.....it was the two year old.....
-
Duarte, interested to know hiw this went in the end..... More so, what did you use to refinish ? Im midway through a fairly intensive repairwhich has meant a refinish on fingerboard is necesarry too. The bass, like yours is not a megs expensive one (stentor 1950 bass) and luckily i think the sound post has been glued in as its still in place after much man handling ! Im interested to know what you used to refinish the finger biard and if the rssult was good from a cosmetic point of veiw and also in stopping black rubb off ? Ive stripped my fb down using sand paper and foam block, came off quite easy too..... Inhave some matt black enamel paint which was closest match to what was on i think ? Any comments are helpful and welcomed
-
Buying a broken bass for repair - amateur repair with pics
Wonky2 replied to Wonky2's topic in EUB and Double Bass
Forget to mention.... The top of the bridge seens to be quite thick ? Any suggestions what thickness it should be at the top where string notches will go ? I think it will need some sand here too to taper the thickness ? Also, silly question...it just occured to me looking at the picture..... Is the a front/ back side ? Still plenty of sanding to do, as the feet fit is still not right..... This is going to take a loooooong time -
Buying a broken bass for repair - amateur repair with pics
Wonky2 replied to Wonky2's topic in EUB and Double Bass
Im happy with the neck joint now snd the hole i drilled through fret board throught to heel where the bolt runs has been filled and sanded back to a invisible match, well at least when the fret board it refinushed with the matt black enamel paint i have for it.... Should be a good undetectable repair if i can get the finush right..... Tonight i have started with the new bridge. I ordered an adjustable maple bridge which seems to be good quality, a nice peice of maple too. But man alive is shaping this going to take some time ! I have masking taped a sheet of sand paper to the deck and slowly sliwing working the bridge back and forth i am begining to shape the feet. I understand the fit has to be immaculate but its tricky to see against the sand paper so constant checks are a must, but its a slow process and difficult to hold the (loose) adjustable feet square in the bridge as it moves back and forth.... I may mark the sheet with lines and remove the feet to do them individual in order to get a better square hold on them however i am mind full that tgey get and equal amount removed...... This will take some time.... I have strapped the bass to a large cardboard box for a stable work surface, it works quite well with rags under the strap to avoid any rubbing...... Once the feet are shaped i will move on to reducing the hight and begin to shape the radius. I have a template as i understand the radius is not symmetrical/ uniform...... Im nervous about the radius and part of me thinks ..... Go see a luthier.... The other part thinks "its only wood " hahaha.... I figure if i get it wrong i can always go see a luthier with a 2nd new bridge... At least this way i will have tried and whats more enjoyed the experience....! -
Buying a broken bass for repair - amateur repair with pics
Wonky2 replied to Wonky2's topic in EUB and Double Bass
Ok, heres a pic of the repair so far... Ive stripped back the finish so that my re-finish is even .... I want to keep the back of the neck finish free so may well wax or oil ? Dont lnow whats best really ? Im curious as to how the finish on the neck heel and head stock is dealt with in the transition between the hard glossy varnish (?) coat and the bare or oiled neck ? Is it just a curve ? Im sure what ever i do here will be not as good as i want it to be ! Hahaha -
Buying a broken bass for repair - amateur repair with pics
Wonky2 replied to Wonky2's topic in EUB and Double Bass
The repair is mid way through I have taken my time rather than jumping right in.... I cleaned up the two faces, being as minimal as possible in order to retain the majority of original wood removing very little.... If anything, just the slpinters. I worked at this untill i was sure the joint closed fully and was a snug fit. I have chosen to use a length of M8 stud with a washer and lock nut at both ends. I started by using an auger bit large enough (around 15mm) to allow a socket in to tighten the nuts and drilled out to a depth wihich allows the nuts to be hidden and filled over, then used an 8mm auger to drill the full way through. Big holes drilled first followed by the smaller hole, this allows you to keep a centre for the drill.... If you do it the other way around you will have drilled out your centre for the larger auger and the drill bit will flap around leaving an untidy cored hole..... Ive allowed for a decent deapth of filler over the too of the nuts to afford the filler itself some strength and mass. This was done by applying the filler, packing tightly, 5mm at a time to ensure even drying and adherance) I applied lock tight to the thread of the stud and gorrilla epoxy to one face of the timber. The joint has closed up well and both nuts are sunk well enough to allow a decent plug of timber or filler..... I Have sanded the finish off the back of the neck to remove a few tiny dinks and make nice and smooth and followed the sanding down the heel to allow an even refinish.....various grades of sand paper and wire wool (oooo grade) ,wetting the wood between each sanding brings out the grain. Doing this and rubbing back down will help when a finishing oil is added and ensures the grain stays putt to provide a smooth finish/ feel. The are are a few dinks here and there and some cosmetic damage to the finish on the body top under the neck.... I thought long and hard about how to best repair or try to hide the repair somehow, but given the nature if the repair, the cost of the bass and the elements of damage i have to try to hide, i have chosen to try a bit of road ware type look and i have to say i am rather pleased with the results. On the whole, the original glossy finish remains, but i have taken a bit of wet/dry and oooo grade steel wool to the bindings and reduced the finish in places mostly still there but dulled and in some places bare... It looks well i think and helps make the dmage look a little more natural rather than the results you would expect from the reality of a neck and a body rattling round a box in a courriers transit van for days..ware looks better than damage and unless done extremely well wear also looks better than a poor attempt at a cosmetic repair....touch ups always looks shabby ..... I guess many will at this point be vomitting at the thought of what i have done, steel studs, fake road ware, but i think it looks far better now looking worn than it did when it looked damaged....and the repair is as strong as possible. I once bought a fender jazz which had some horrific wounds... I took it in the garage and after a short while it came out looking pretty much like one of fenders road worn or light relic jobs, which again looked far better than damage. Whats more, that bass was fantastic to play as i guess having been so intimate with it i didnt mind treating it very closley rather than being careful all the time.... Lounging round with your favourite bass is great and far far better than the ones that just stay in the case and come out once youve wrapped your belt buckle in bubble wrap ...... (Sorry, im rambling....) Waiting for expoxy to go off properly before i seal/ plug or fill the two 15mm holes in order to allow any moisture out.... Once i have refilled the holes and sanded back to original shape i have bought some mat black enamel to refinish the fret board. I may oil the back of the neck or stain back to match original colour... When all done, i have the new bridge to trim down and shape which again, im not going to rush.... Its gone well so far and i think despite how it sounds, the results look well. I just hope the expoxy bonds well and the repair lasts well. Cant wait to get it strung up and hear it.....