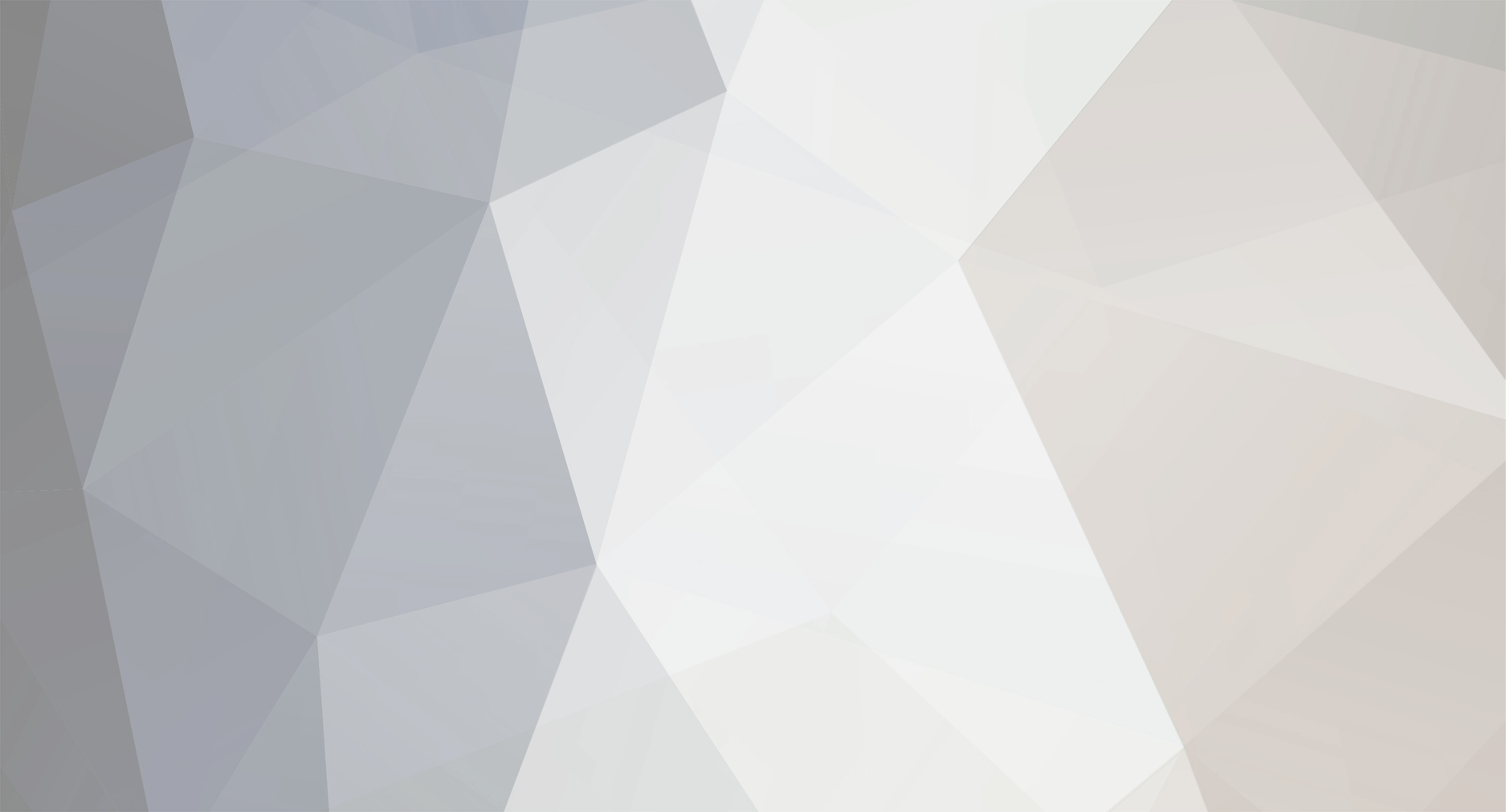
planethead
Member-
Posts
83 -
Joined
-
Last visited
Content Type
Profiles
Forums
Events
Shop
Articles
Everything posted by planethead
-
...winter approaches and my street corner is getting chilly so time for a little restoration project to see me through the yule. I know there have been disparaging comments regarding the 'nobbly' neds on we-flay but I like the approach here. [attachment=14970:P1010024_1.jpg][attachment=14974:P1010013_1.jpg][attachment=14971:P1010015_1.jpg] [u]HISTORY[/u] Short scale bought from Andy's (Denmark Street) around 1979/80; I understand they replaced the original bridge and fitted the JPUP, relocating the jack socket to accommodate the additional JPUP volume (metal knob marked 'T') [attachment=14972:P1010016_1.jpg] A quality endorsement from John Entwistle bodes well... [attachment=15166:nedc.jpg][attachment=15167:nedc2.jpg] "Ned Callan" - A pseudonym for British custom luthier Peter Cook. [url="http://www.shergold.co.uk/burnsbook.html"]Shergold[/url] were commisioned to make these guitars that were designed by Peter. Shergold are known to have produced both the "Cody" and "Hombre" under this arrangement. Due to their "distinctive" (read weird, though not displeasing) appearance these guitars quickly earned the nickname of "nobbly Neds". Some "Shaftesbury" models - made for the catch-all brand established by the Rosetti Music company to cover various unknown brand imports (principally from Japan and Korea) and home grown (typically) cheap models. The Shaftesbury brand appears on many musical items aside from guitars. [i]Shergold Guitars Forum[/i] [b]Several mentions (and a pic!) of Peter Cook for context:[/b] [url="http://www.thewho.net/whotabs/equipment/bass/equip-entwistlegear-74-85.html"]http://www.thewho.net/whotabs/equipment/ba...gear-74-85.html[/url] [b]Norman Holder (Shergold) answered a few questions about the Ned Callan's, in particular the neck.[/b] [attachment=14973:P1010018_1.jpg] [indent]"The number is not the amount, 7 could be model code and 23 the amount or 7 for July and 23 the day. Peter got us to make his guitars when he found he couldn't get the quality himself or the quantity we were the sub contractors." "The models we made were made from Mahogany (Sapele) the necks as well the truss rod was my two way design,the cases were made by a guy Henry Glass up in Essex " "The zero fret was something we inherited from Burns,so all the necks we made had the zero fret. All our necks were suplied seperately with screw holes,but the necks could have been glued in after they left our factory,Petes first ones could have been glued in only Pete could confirm this."[/indent] [b]Another post from the Shergold forum by Norman Houlder. Referring to a guitar but probably applies to all the necks he made:[/b] [indent]"The truss rod was my push pull type with Tpiece,and shaped groove,trouble with the original necks were the groove was a true segment(tapering out at both ends)which cuased the neck to S then I found out that the rod worked bettder with only half a segment and didn't need to go right along the length of the neck as you couldn't make the thick part bend unless u had a 2ton press."[/indent] [b]Some additional info gleaned from another site ([url="http://newsgroups.derkeiler.com/Archive/Alt/alt.guitar.bass/2007-02/msg02528.html"]here[/url]) the subject of discussion is one of the 'Shaftesbury' Ned Callan's and reiterates previous information.[/b] [indent]"Shaftesbury was a brand name covering a lot of different big name knock-offs during that period when just about anything got copied by the Japanese and no-one seemed to care. NOT made in England...the original NC bass was. A nothing special Japanese-made bass, probably screwed together by [url="http://en.wikipedia.org/wiki/Matsumoku"]Matsomuku[/url] or one of the other jobbing builders of that era and distributed in the UK by the now defunct Rose-Morris company... I think. Not expensive but OK for the money and not a collector's item I'd have thought. Don't get burnt...it's a Japanese knock off . The serial number won't help. I had a shop during the 70's and 80's and sold Shaftesbury guitars and basses. They were all copies made in Japan, some of the real cheapies were made in Italy. They were distributed by Rose Morris whose premises were in Shaftesbury Avenue, London hence the name. Shergold made the NC and were still in business during that period and would not have put 'Shaftesbury' on them...way too down market. I searched Google and found an NC for sale, totally not original and the ad stated it was made by Peter Cook under the Shaftesbury name which does not make any sense and I do not recall seeing any mention of such a tie up in the catalogue at the time. Being a bass player that would have been of interest to me. Interestingly the photo showed the bass with the truss rod cover missing which would have had the S/bury name on it. Peter Cook made Strats, Teles and P+J basses from Mighty Mite parts in those days...we sold those too and he never mentioned that scenario to me. Bottom line...the only genuine NC to the best of my knowledge was made exclusively by Shergold. Caveat emptor"[/indent] UPDATE (20/10/08) Pickguard removed to reveal routing etc. No stamps or QC stickers other than that on the headstock. moved the jack socket back to where I think it probably started. Also neck is a tight but not accurate fit in the pocket. With all electronics removed - still have to test the truss rod. [attachment=14978:P1010022.jpg][attachment=15048:P1010001.jpg] UPDATE (23/10/08) some bits and bobs.... [attachment=15912:P1010003.jpg][attachment=15913:P1010004.jpg] [attachment=15914:P1010006.jpg][attachment=15915:P1010007.jpg] old school wiring indeed.. probably pick up microwave radiation from space on those... [attachment=15921:oldschwiring.jpg] UPDATE (24/10/08) The original design may owe more to Gibson than Dan Armstrong. The '59 EB0 from: [url="http://shortscalebass.blogspot.com/"]http://shortscalebass.blogspot.com/[/url] Gibson started using the 3 point bridge (still with chrome-plated bridge cover) in 1973. This was a far more reliable design, and is still in use today. This bridge design does not incorporate the string mute of earlier models. [url="http://www.flyguitars.com/gibson/bass/"]Fly Guitars[/url] [attachment=15142:Gibson_eb2_dc.0.jpg][attachment=15160:3ptbridgesmall.jpg] UPDATE (26/10/08) Time for some measurements (suitably vintage in inches): - 22 frets excluding the 'zero' fret. - 13 5/8 from the bottom edge of the neck pocket to the rump. - 9 1/8" from the neck pocket to the original bridge fixing holes. - 30" total length of neck from tip of headstock The neck is not in line with the fixings for the original bridge - but correct for the replacement 3-point. The removed or damaged lacquer suggests the neck may have been removed and then re-glued. [attachment=15191:P1010001_1.jpg] Damage to the binding could be to replace a damaged nut (the current one is not in great condition and has not been well made (or at least not treated very well) or perhaps the wood has contracted with changes in humidity pushing the zero fret into the binding and cracking it? [attachment=15190:P1010005.jpg] UPDATE (29/10/08) ...brrrr sure is cold on the street today! More beer, more pot and more hookers required... My plan: - NOT to separate the neck (for now) - fill the JPUP cavity - fill and repair hole left by JPUP volume control mod - add hipshot supertone bridge - the footprint of the HS should cover the original bridge fixing holes and the front mounting hole - DM Model One PUP (modify cavity to fit if required) - re-use existing components/wire (replace damaged capacitor) - remake scratchplate which should look like this...I hope! [attachment=15330:ncmockup.jpg] If the instrument feels and sounds good... - strip body and re lacquer (shellac) -replace nut - repair damaged lacquer on neck UPDATE (07/11/08) Not a lot of progress but moving in the right direction....new scratchplate underway; Shiny tuners...; Replaced old 3 point with Hipshot Supertone... [attachment=15680:P1010001_3.jpg][attachment=15685:P1010003_1.jpg][attachment=15688:P1010004_2.jpg] restrung yesterday with cut down long scale 'heavy' gauge (not a good idea with hindsight) and noticed considerable increase in sustain...the bridge is not yet sitting flush and the action even with the bridge saddles set down is an astonishing 5mm... having fired off a few arrows with the nedster will have to rethink the approach. Trying to avoid removing the neck so may have to rout into the body; lowering the height of the bridge block by a few mm. and since I'm going to be getting the router out to fit this... [attachment=15686:P1010006_2.jpg] It might turn out fine on the corner again :-) UPDATE (08/11/08) Had the router out this morning to fit the Model One.. and managed to fit the hipshot flush to the body. Replaced the cap and lashed together some temporary wiring ready to take pics and record some samples... only to discover one of the riff-raff had been off taking pictures and used up all the juice.... ..so detuned strings to avoid launching hipshot at neighbours..left camera on to charge..and wil return in short while with some sound samples and pics...splendid Camera still charging so press on with audio... that's one hot pick-up! The action with the saddles down is approx 3/32 at the 12 fret and 5.5/32 at the 22. The pickup pole (set as low as possible) is 6/32 from the E. Pulled the saddles back as far as they go but cannot get intonation correct at the 12 fret still a few points sharp - probably doesn't help using cut down long scale guage 50-110!!!! Time for some audio (nothing fancy now...) : tone full up - the E sustains to silence [attachment=15724:NC_tone_up_sus.wav] tone down [attachment=15723:NC_tone_down.wav] tone / volume variations [attachment=15725:NC_tone_vol_var.wav] some cheeky chords [attachment=15726:NC_two_note.wav] and a bit of noodling with vol pot lower [attachment=15722:NC_noodle.wav] Going to remove bridge as tension is pulling out the fixings - don't want any catapault incidents so no pics but the nedster looks like the mock-up image. UPDATE (09/11/08) String tension is pulling the bridge insert out of the badly repaired wood. [attachment=15742:P1010002.jpg] And since a whole new discussion is starting up as to whether to remove the neck - I've decide to call in the supercharged oxford detective and get busy! Dirty.....but sweet! [attachment=15846:P1010001_10.jpg][attachment=15847:P1010002_10.jpg] Patch up some holes (the neck pu needed two blocks!); cut the plugs down to size; PU glue and clamp (or mallet!) ; plug in and glue from the inside...ready to work from the outside. [attachment=15848:infill1.jpg][attachment=15849:infill2.jpg] [attachment=15850:infill3.jpg][attachment=15854:infill5.jpg] [attachment=15851:infill4.jpg][attachment=15855:infill8.jpg] [attachment=15831:P1010001_13.jpg][attachment=15853:infill7.jpg] [attachment=15852:infill6.jpg][attachment=15832:P1010002_13.jpg] UPDATE (12/11/08) Re-measured the scale length again from crown of the zero fret to crown of the 12th = 15" giving 30" scale. Set bridge saddles to intonation 'mid' points. Positioned the supertone with the original 3 point bridge fixing holes. Measured a distance of 30" from the crown of the zero fret to a point just in front of the E,A saddles and just behind the G,D saddles. So the old bridge WAS in the right place (I'm the duffer here :-O adding 2/8" from the nut!) Fashioned a 5mm ply template for the pickguard (first two attempts OK but could do better!) and one for the PU. Re-measured scale length for the umpteenth time settled on bridge position approx 5 mm back from the original holes ... [attachment=15919:templates.jpg][attachment=15920:commitment.jpg] Drilled so committed. Shudder....! UPDATE (15/11/08) Sand everywhere...nothing but sand and sandpaper. 80g to get rid of the sanding sealer and dye. Back up through 120g to 180g for the grain filler. This reveals the scratches left by going against the grain with the 80g..so back we go... still too much stain left inside the horns and waist. Need a sanding drum for the drill. Quite hard to get around the neck joint without causing damage to the lacquer on the neck. UPDATE (19/11/08) Took back to 80g but made the filler too thin - by the time it was dry and sanded back to 180g a lot of it had disappeared! So 3rd time lucky with the filler! Meanwhile got a sanding drum which enables you to replace sandpaper as required no pre-made sandpaper sleeves. Best to use the fabric backed sp - the paper stuff is too difficult to work into the drum. Another good tip picked up from [url="http://www.reranch.com/101.htm"]here[/url] - use a single edged or stanley knife blade to scrape up the excess filler once it has dried to a pinkish colour. Dragging the blade 'across' the grain using as little pressure to move it as possible. Definitely saves time and mess when sanding. [attachment=16174:scraping.jpg] Decided to grain fill twice on the front and once on the back to compare. Having sanded up to 240 grit on both sides the front is *considerably* smoother so should provide a good base for the lacquer. Also noticed quite a few pinholes appearing once the filler has been sanded back. I think this may be to do with changes in temp or humidity although did notice tiny bubbles appearing while applying the stuff. So maybe its trapped air? These 'eruptions' dry proud of the surface and probably get wiped scraped or sanded off leaving a pinhole. Finally managed to put a bevel on the scratchplate using a chamfer bit - this was something of a performance! But worth it to get this not very clear profile 45 deg angle across the top two plys then straight down the third ply. [attachment=16173:pickguard2.jpg][attachment=16172:pickguard1.jpg] Key to this was constructing a jig which ensured the surface of the router remained level at all times - managed to skid of the edge of the test piece a few times before figuring this one out! Single edged blade or stanley knife again to tidy up any uneven moments. I think with patience you could do some quite nifty stuff to a pickguard with a blade - I started experimenting with slightly more daring curves and bevels - oooh! UPDATE (21/11/08) Short pause while waiting for the first coat of sanding sealer to go off. This stuff stinks. Face mask and ventilation required - didn't check the brush carefully and noticed bits of old paint and whatnot starting to appear :-( Off for a second coat. Bl**dy h*ll this stuff really stinks and dries very quickly - to reiterate; dust free environment and a super clean brush essential. I'm doing this in stages: front first, back second and finally the sides because it dries quickly and I imagine trying to do this in one go would be a nightmare of stickiness and.. stench! Nearly double-coated everything. Sand paper out again this afternoon. The sealer does make the wood look good. Amazing - bit dark to take pictures but will do so tomorrow. The colour is almost back to its post-lacquer striptease tint. Got to watch out for drips down the sides - end up sanding right through the sealer to get them out. UPDATE (22-23/11/08) Disaster! ..ish. Managed to sand through two small areas in the sealer - quick drop fill - sand - aagh not quite dry now I have a bigger hole to fill. After several attempts to rescue the prep - its starting to look like the Somme! No choice but to do the front again. Bum!!!! However. This is a good opportunity to try doing something the wrong way round. Originally I had applied sealer sanded then added a coat of 'deep' (naturally) mahogany stain. This time I'll stain the bare wood and then apply sealer - hopefully the sealer which darkens the wood anyway will intensify the colour. UPDATE (24/11/08) mmm... did I say hopefully? Tried staining first let dry and apply sealer the sealer sank! slap a bit more on that's better arggh pinholes where are they coming from - more sealer...more pinholes. As you can tell this was an idea way ahead of its time. Back to bare again. Third time lucky I hope. Sorry there aren't any pics it's just too depressing :-( UPDATE (28/11/08) Marathon sanding sealer session complete, not sure if that's a great improvement but in danger of chasing my own tail so moving on. Routed out pickup for Model One - fitted scratchplate. Damn managed to cut a gnats too much off for the heel so have to move the sp forward to cover. If the sun comes out I'll take some pics. Well the sun hasn't come out but here's a pic of un-finished work so far.. actually looks a bit darker than this [attachment=16544:latest.jpg] I think it's mojo remains intact - quite the dapper! [attachment=16574:nedwide1.jpg][attachment=16575:nedwide2.jpg] Unfortunately I had to put this together to cheer myself up among the list of disasters today. some misalignment with the pu cavity/scratchplate screwholes etc - soluble I think. slight concern re alignment of bridge. cocked up the scratchplate around the bridge... and the previously damaged and badly repaired nut broke loosening the binding as well. Fast coming to the conclusion I should have taken that bloody neck off in the first place!!! UPDATE 14/12/08 Nothing really new to report. Too cold now to get into spraying nitro so will leave this until the New Year. Have a nice Christmas. ttfn BTW only sticking everything in this post so I can find it again - love to hear your thoughts (not in any psychic paranormal way - that would be deafening! :-O )
-
[quote name='timloudon' post='299790' date='Oct 5 2008, 11:00 AM']I did start reading that sentence thinking he was talking about scores, I had to read it twice. This is fascinating. The question I want to ask is does this help in any way when trying to improve one's sight reading? Surely the mention of looking too far ahead and 'overloading' the brain, among other points, could be useful pointers. Planethead, Where did you find this article? Was it in a journal?[/quote] Good morning I was looking for some less proscribed information on SR...how to develop my own systems for improving MY sight reading so trying to understand what the brain does in order to sight read seemed a good starting point. this ties in with another thread on here about singing what you play which I believe is probably a very good way of speeding up the process of sight reading - anyway beats standing around on street corners hustling for change! ttfphc
-
[quote name='phil_the_bassist' post='293908' date='Sep 28 2008, 02:45 PM']Does anyone have a decent transcript of P.o.T, preferably bass clef, but tab'll do! Any help'll be much appreciated![/quote] PM me with your address ttfn
-
Anyone recommend a suitable string cleaner for use with the Sadowsky's lovely waxy neck!! ..and looking for a transparent (perspex/acrylic) Precision pickguard - not the self adhesive stuff for acoustics ttfn
-
[url="http://www.musica.uci.edu/mrn/V5I1W98.html#sightreading"]http://www.musica.uci.edu/mrn/V5I1W98.html#sightreading[/url] ...and expanded upon [url="http://en.wikipedia.org/wiki/Eye_movement_in_music_reading"]here[/url] [url="http://www.rhythmpatterns.com/"]....also interesting[/url] ttfn
-
[quote name='stonecoldbass' post='263455' date='Aug 16 2008, 01:20 AM']Hey Guys, Here's the three songs my new band recorded last month. >>>>snipped>>> Feedback mucho appreciated!![/quote] Ok here's M2CW straight from the hip - like the feel/vibe of track 1 - like the bass line on track 2 but don't like the distortion on the bass - track 3 didn't move me either way like the singers voice; tight sound overall; balanced arrangements; drum sound's a bit 'pinched' for my taste. TTFN
-
[quote name='clauster' post='258023' date='Aug 8 2008, 01:02 PM']Cheers for that bit of insider info matey[/quote] You are welcome... BTW if you discover a neat way to clamp the horn throat and brace section while gluing and screwing do let me know - this bit got me in to a right b*ggers muddle and covered in glue to boot!! TTFN Actually scratch that having thought about this and looked at the plans again I see where I went awry. The plans appear to suggest that the throat panel and baffle brace are attached and then the horn braces added. I see now that the horn braces should be attached to the throat panel and the baffle brace added afterwards.
-
[quote name='clauster' post='257872' date='Aug 8 2008, 10:32 AM']Cheers for the tips Planethead. Most of that I had been aware of, but I can't see why you'd need the sled if you've got a guideboard and can do arithmetic. Am I missing something?[/quote] - being an instant gratification junkie myself (and certainly no woodworker) - they might be useful for others of a similar disposition - its the 60 degree angle for the horn throat panels - having clamped them as per the instructions (in a Z shape) I thought I could cut with the guide board alone using the horizontal brace panel to slide the saw shoe along while the vertical blade renders the angle - but this left the saw too low - it just made cutting the angle much easier by screwing(temp) a piece of wood to the brace and then using the guide to run the saw along - which is exactly what the sled would have done had I had the foresight/patience to build one first. +1 for latex gloves tip but don't call me Errm ;-) TTFN
-
[quote name='clauster' post='256874' date='Aug 7 2008, 07:43 AM']I received my piezos this morning at 0:30! They'd been delivered to my neighbour yesterday while I was at work. Wish I didn't have a couple of important meetings today so I could "work" from home and start cutting and glueing.[/quote] I started my omni 10 yesterday and am now covered in glue! Probably nothing new but this is what I've learnt in 24 hours. 1) if you don't have a table saw then the cutting guide and sled are a must 2) ensure your cutting surface is as stable and level as possible - my improvised support system means I now have to keep going back and shaving pieces off to make things snug 3) if you ignore 2) get ready to use more glue! 4) Found the horn panels and braces very tricky to clamp (note 3 above) 5) I could only get 12 mm (7) ply so I've had to move one of the horn panels slightly to preserve internal volume - which I'm sure is OK (isn't it?) 6) that stuff about measure twice cut once - don't forget it ;-) Not looking for enormous power handling so went with the 2010's and didn't bother with tweeters - probably too old to hear anything above 500hz!!! ^^^^^^^^^^^^^^^^^^^^^^^^^^^^^^^ (this statement is in fact a preamble to my latest gripe (cutting 'engineers' who insist on 're-mastering' old recordings by 'refreshing' the audio in order to add more HF than was ever intended) - but I'm not hijacking your thread so... good luck with your build TTFN
-
[quote name='Alun' post='254721' date='Aug 4 2008, 05:49 PM']Yes! Assuming there are no copyright issues that is. Cheers Alun[/quote] Well most of this stuff has been floating around for a long long time but I'll stick em up and if the moderator is in any doubt he will act ..... swiftly!!! 84_3205 - moved to the Vintage Breaks mp3 thread 85_3741 - moved to the Vintage Breaks mp3 thread 94_8302 - moved to the Vintage Breaks mp3 thread 98_5658 - moved to the Vintage Breaks mp3 thread 98_9686 - moved to the Vintage Breaks mp3 thread 100_3471 - moved to the Vintage Breaks mp3 thread 103_3361 - moved to the Vintage Breaks mp3 thread and because it really is the only way to play drums...here's Pucho! [attachment=11574:111_0039.WAV] 119_3 - moved to the Vintage Breaks mp3 thread 123_8155 - moved to the Vintage Breaks mp3 thread
-
Just discovered a CD's worth of old break beats I'd forgotten about. There .wav files with the tempo in the title DOS style....happy to u/l em if you want... just say yes! TTFN Ian
-
Translating hand positions from DB to EB
planethead replied to planethead's topic in EUB and Double Bass
[quote name='velvetkevorkian' post='253689' date='Aug 3 2008, 12:19 PM']The position moves are indicated by the brackets above the stave. The roman numerals do refer to the strings. If you're translating that to electric I wouldn't recommend using the indicated fingerings/position shifts though.[/quote] Thanks K - I've abandoned most of the fingering/positions in the book now and plotted my own - prefer to use as many strings as possible to play a scale rather than wandering up and down one string using my index and pinky ;-) -
Translating hand positions from DB to EB
planethead replied to planethead's topic in EUB and Double Bass
[quote name='dougal' post='253396' date='Aug 2 2008, 05:08 PM']Given that there's one place to play a given pitch on a string, a combination of roman numeral and finger gives you hand position: no matter what you call it The Simandl positions are explained here (see fingering guide): [url="http://musiced.about.com/od/lessonsandtips/a/doubleblesson.htm"]http://musiced.about.com/od/lessonsandtips...ubleblesson.htm[/url][/quote] Very good link thanks for that... I'll err on the creative side of your signature for now... TTFN Ian -
Translating hand positions from DB to EB
planethead replied to planethead's topic in EUB and Double Bass
[quote name='dougal' post='253066' date='Aug 2 2008, 12:30 AM']I [i]believe [/i]that the roman numerals are the string (especially if written underneath the stave) - I've just checked my grade 1-5 book and this looks like what they are. If you're looking for something classical guitar like to indicate the position then you won't find more than this. Unlike the guitar there isn't a universal set of positions - The 'first degree' is sometimes called the 'half position' (Simandl) or 'fist position first degree' (Nanny). There's also Rabbath, who has his own road map of the bass. Check out Jason Heath's blog about the differences: [url="http://doublebassblog.org/2006/11/rabbath-versus-simandl-comparative.html"]http://doublebassblog.org/2006/11/rabbath-...omparative.html[/url] Hope this doesn't cloud the water too much.[/quote] Thanks Dougal and... Yes and no.. if the numerals [i]are[/i] strings then it makes slightly more sense. Its the absence of a clear definition of 'position' that's throwing me. In my scale book the author refers to 'position moves' indicated by the numerals which suggests hand not string unless position indicates vertical and not horizontal movement of the hand. The Jason Heath article refers to position without ever being clear what it means - I assume he means hand.. Perhap's a thread to establish a meta-syntax to alleviate analysis paralysis would be useful...? and there's probably a market for 'fist position first degree Nanny' in the darker corners of Amsterdam or Berlin ;-) TTFN Ian -
Hello Steam Bassers (my friends electric!) Decided to brush up on musical theory scales etc so bought the ABRSM Book 2 Grade 6 - 8 scales for Double Bass. The author suggests fingering for the second octave as well as hand positions which he notates using roman numerals I, II, II etc - I cannot get my head around this. Assuming I'm as thick as a brick I would be grateful if someone can explain this system to me? Is position I from 1st fret to fourth , II from fifth to eighth etc - If so his fingerings would leave most of my digits looking like a balloon animal. TIASOB Ian
-
Alphanumerically speaking - My 2 cents worth! TTFN
-
[quote name='cheddatom' post='250531' date='Jul 29 2008, 04:12 PM']Anyone know the difference between "slope" and "compression"?[/quote] Slope could be variable knee from hard to soft; compression is probably ratio 1:1 - infinity:1 (or limiting as it used to be known) M2CW
-
Standing in the Shadows of MOTOWN
planethead replied to philsimmonds's topic in Theory and Technique
[quote name='philsimmonds' post='249967' date='Jul 28 2008, 09:21 PM']thought i'd just say how amazing, and helpful this book was and is. for reading, and for learning the works of motown great james jamerson. if theres and bassist that want to develop there groove, knoledge of there instrument and reading. get this book. does anyone know any books along the same level and standard, with dots only... for Arangements.. and ensemble works in jazz...??? Cheers. Phil[/quote] +1 Re Motown/JJ book If you're interested in Latin vibes I recommend Funkifying the Clave by Lincoln Goines and Robby Ameen - can be used as a primer; covers most of the popular flavours; and includes CD's for bass and drums. TTFN -
[quote name='Fran Diaz' post='249360' date='Jul 28 2008, 09:10 AM']These are not 'ultra vintage'. On NYC basses you can order the standard 21 fret, 'square' fingerboard or the 20 fret 'round' one like mine. I like the round looks better for 4 string, vintage style Sadowskys.[/quote] I agree the round looks better IMO -
-
[quote name='Fran Diaz' post='249166' date='Jul 27 2008, 09:51 PM']anybody said PJ? [/quote] Fran I'm curious - are the twins 'ultra' vintage I note the necks have a curved heel. On my (non-ultra) vintage the neck (maple) is the same as the bass pictured with the girl. Did they change neck profiles at some point or did you request that shape? BTW - I prefer tortoise shell pickguard to the black :-) cheers Ian
-
Hello otpj no I don't think they do that unless requested - I've seen a few moans about this elsewhere - personally doesn't bother me. My Fender US Jazz has a laquered neck and the clean up round the frets is v. poor - hope that helps cheers Ian [quote name='OutToPlayJazz' post='241150' date='Jul 16 2008, 06:37 PM']Does your Sadowsky NYC have a glossed fingerboard, PlanetHead?[/quote]
-
Hello Anthony, yes I particularly like that cherry bomb precision - not so often you see a nice top on a P - immediately playable and with the darker tone that I had been looking for (this one's a keeper!) to complement the brightness of the Sadowsky ash/maple combo (which was to replace/usurp my fender also ash/maple). Full marks and kudos to the men that made them. PM me for a detailed review ;-) cheers Ian [quote name='Nino Valenti' post='235700' date='Jul 9 2008, 01:38 PM']Nice pair you got there!!!![/quote]
-
I posed the question a while back Sadowsky v Valenti - look I got to find out. The wooden floor is Nino Valenti's... the duvet's mine.... [attachment=10421:P1010002.JPG][attachment=10422:HPIM4459.jpg] [attachment=10420:P1010003.JPG][attachment=10423:HPIM4474.jpg]
-
First up thanks to all who supplied meaningful information, comment and insight in response to my original query. It wasn't my intention to start a fire but you give some folks matches.... My NYC J-bass is now on order from Sadowsky and my P-bass from Valenti. Next project on the drawing board is a custom valve serial compressor loosely based on the Altec 436C TTFN Ian
-
Hello all I have a an older style 65w Ashdown 5-15 practice amp bought cheap and (I suspect) as ex demo. Take the treble knob past seven(dots) and the distant sound of of the pacific breaking gently on the shore appears. Can anyone suggest the most likely cause of this and can it be rectified (preferably by me). My guess would be incorrect component replacement at some point in its life but have no way of knowing (I've never opened it up) or it could be that older versions suffer this. Apart from this I don't mind the overall sound of the amp it's not hifi but is more than adequate for practice and projects reasonably well in a small room. Any suggestions - other than dump it and get something else - gratefully received. TIA + TTFN Ian