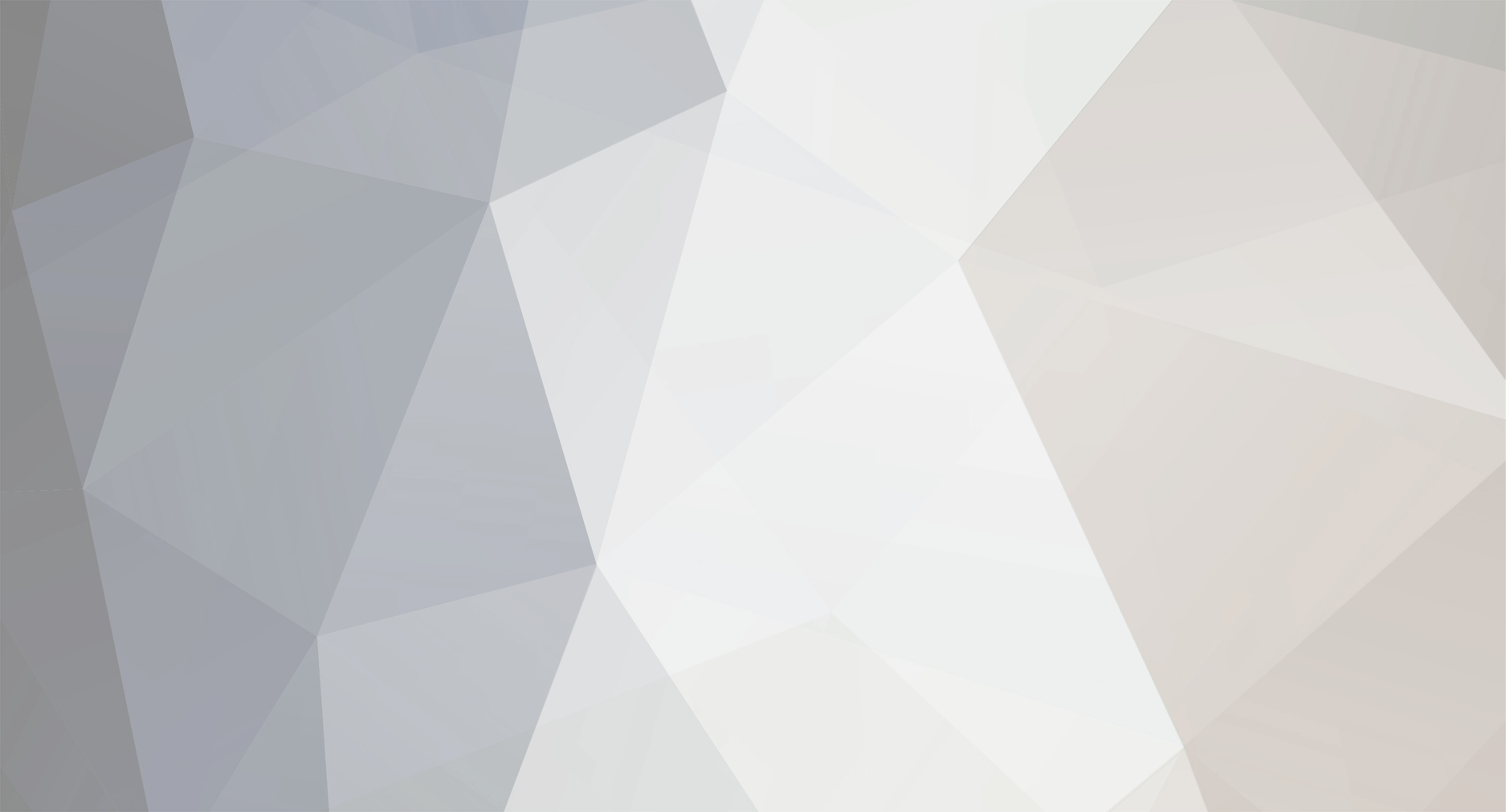
SubsonicSimpleton
-
Posts
943 -
Joined
-
Last visited
Content Type
Profiles
Forums
Events
Shop
Articles
Posts posted by SubsonicSimpleton
-
-
Is the port really 8.2 cm tall internally?
There is an enormous difference in port cross sectional area between the two porting suggestions, you could try plugging in a smaller number for the square port (either just the central portion, or just the two corner portions) bearing in mind that you can reduce the port cross section by adding material under the port shelf fairly easily.
Really this needs some input from the forumites with more loudspeaker design knowledge than myself calling @stevie @Bill Fitzmaurice who can probably shed a more expert view on the port tuning aspect - the circular port suggestion has a much higher resonant frequecy than the square one, so there may be other factors to consider beyond taking the numbers from winIsd at face value.
-
1
-
-
Your cab is already ported - rather than sealing the existing port and cutting a different shaped one, surely it would make more sense to tune the length of the exiating port appropriately. There are both commercial and DIY cabs that use slot ports, here is a link to the download page for the Fearful range of cabs which use slot ports, take a look at the plans and it should become clear how the slot ports are implemented.
http://greenboy.us/fEARful/DL/
With a little ingenuity you could make a two piece shelf that could easily pass through the existing speaker opening (I would layer two thinner pieces of ply like this - viewed from the cab front)
AAAAAABBBBBBBBBBBBBBBBBBB
AAAAAAAAAAAAAAAAAABBBBBBB
..............S..........................S................
Both pieces (A) glued together beforehand into one piece, likewise with pieces (B), then you have a large mating surface to glue the two pieces together inside the cab. If you size the pieces so the long layer of each piece extends to cover both braces(S), you will be able to screw the port shelf down securely to dry fit and finesse the tuning before committing to fixing the shelf more permanently within the cab or glueing the two halves together.
-
1
-
1
-
-
Might be worth having a lesson with a pro bass guitarist - they should be able to identify very quickly whether the root of your problem is instrument setup/your technique/other signal chain issues.
If you are a beginner, it is quite possible that your understanding of setting up your instrument is flawed (I've rescued a number of intruments from bad DIY setup attempts).
Take a look in this thread
There may be a friendly basschatter local to you who would be willing to take a look at your bass with you - sometimes small adjustments can make a world of difference.
-
-
Just seen a video about the video in the OP, that sheds some more light on this by way of interview with the person who shot the footage.
-
1
-
-
Why on earth hadn't the band registered the name themselves??
Even at the lowest levels of the music industry bands get into disputes over name usage, and if you intend on selling merch or recorded music one of the first things you should do is check that the cool name you just came up with by your band isn't already owned as a trademark or likely to land you in hot water with a big corporation who already owns the name (even if none of their products are music related) - I know a band who just had to scrap all their merch and CDs because they didn't do any due diligence in this respect.
This isn't really stealing so much as it is incompetant management - it still sucks for the band, but anyone who has been involved in the music industry for half a century should be well aware how mercenary and backstabbing it can be whenever money is at stake and should have taken measures to protect themselves many years ago.
-
As no-one has mentioned him yet I'm going to have to show Mani from the Stones Roses some love - danceable tunes within the tunes, what's not to love about that.
-
They must be a bit skint after the Duke lost his no claims bonus.
-
1
-
1
-
-
Reading through the details they say they are going to provide accomodation and food for the duration, but it doesn't explicitly state that the gig is unpaid or paid.
Has anyone actually applied and raised the remuneration question?
-
-
Is Donald Trump moonlighting as a business consultant for Gibson on the quiet?
-
2
-
-
Make yourself a simple jig to test the pickup positions and combinations in the same way that Leo Fender did, and listen to the sound they make rather than other peoples opinions.
-
3
-
-
Why not just use the existing bass drum and hihat pedals which you know will work, and just assign a snare sound to the hihat pedal - you might want to rotate the snare pad out of the way, but surely using what's there already is the most straightforward solution.
-
Given that they are listing multiples in stock of various antique brass instruments at similar price to the basses, my guess would be that if you order you will receive a photo or poster of the item you have bought.
-
This Propellerheads remix is my personal favourite
-
1
-
-
2 minutes ago, Stub Mandrel said:
Judas Priest approach might work but will antique my basses pretty rapidly:
I hate to be the one to break this to you, but there was a good reason that Rob Halford used to dress like he was going to a gay BDSM dungeon....
He was a massive fan of the movie Police Academy and hoped to land a cameo role at the blue oyster club in one of the sequels
-
2
-
-
Back in the day, it was important to use the same tuner to tune all the instruments - even if you set the reference frequency the same across multiple tuners (same brand/model or not) the circuitry contained multiple discreet analogue components which are all subject to manufacturing tolerances.
All those +/- 2/5/10% variations add up, which results in "identical" circuits not behaving in an identical manner, in mass produced items the components are just slapped in to keep price down, in some professional level recording equipment the manufacturer will measure and reject components that fall too far out of spec or place extra time and care matching components when they are to be used for example as a stereo pair.
-
You can use this type of music stand and cut down the top to a more suitable size
https://www.amazon.co.uk/Tiger-Orchestral-Conductors-Adjustable-Music/dp/B002GOHCTA
Its a more agricultural approach than the clips, but wont fall to pieces or need replacing with a different model if you change your tablet/case.
Worth looking around if you go this route as these type of stands can be picked up for as little at £10 new from some of the big music etailers, and even less used.
-
Is it worth revising the horn cutout so it can be used in either orientation and allow the cab to double for PA duty?
-
Do Fractal actually have any dealers where you can walk in and hear a unit in person?
-
Just a thought, but it might be worth disinfecting the cavivites and neck pocket with tea tree oil to kill any potential mould/spores. Looks like you got a nice result from the application of a bit of elbow grease though.
-
One important factor here is what is driving the prices up at the moment?
I might be wrong about this totally, but for the most part it would seem that the primary market for expensive vintage/collectors instruments is mostly middle aged and older people with money - if you want to offload a bunch of expensive instruments, what happens if all the old farts are needing to sell off their collections to fund living expenses and the younger generation are either too skint, or not that interested (on the basis that music tech has moved on, and their musical heroes don't have the same associations with certain instruments in the same way that someone growing up in the 50/60/70s would have witnessed but been largely unable to afford at the time).
If you are a famous old fart with a large instrument collection like Geddy Lee or Joe Bonamassa, then the celebrity association inherently adds value and desirability, but if you are joe public then I'm not so sure.
-
1
-
-
20 hours ago, LukeFRC said:
It seems to be more of a thing in US culture of smaller one man bands setting up semi professionally and then things falling to bits. I guess in the UK we tend to be less entrepreneurial and people would probably keep it small scale rather than try and scale up beyond their abilities.
This type of thing happens here too - people start making instruments at their own pace, then a bit of a buzz develops around the instruments they are producing, followed by a sudden stampede of orders and if the luthier in question has some sort of real life hiccup like a health issue or family problems they can end up spending customers pre-order deposit money to pay their bills and dig themselves into a hole very quickly, unfortunately this often seems to result in a spiral of bad practice. We had this on here a few years ago (cant remember the guys name off the top of my head, but I think it eventually got resolved) and over on the fretboard there is a current on going situation with another builder.
-
Milling the bodies out of a billet has two big potential pitfalls, weight and coldness(aluminium is a very efficient conductor, so will wick heat away from any body parts in proximity to it).
You could get a very accurate idea of how heavy your finished body will be fairly easily;
-after removing neck, bridge and pickguard, carefully measure the displacement of the body by dipping it in a suitably large container of water (I'd put the body in a bin bag to keep it out of direct contact with water and hold by the top horn - air will be forced out of the cavities. You can then get the displacement of your hand separately and get an accurate figure)
-calculate out the finished weight of the alloy body and weigh the existing body
-procure enough lead flashing from your local builders merchant to make up the difference in weight, and gaffa tape it to the back of your existing instrument (assuming it has a poly finish, and taking care to place a protective layer of cloth between the flashing and the instrument to avoid scratching)
-see whether you can live with the extra weight, and publish the finished weight on here to get some feedback on whether other musicians could live with it.
The good thing about homogenous engineering materials is you can accurately predict how much material you need to remove to hit a target weight, so you might be able to make a swimming pool rout under the pick guard, or change up the design to be routed entirely from the rear and go hog wild with the weight relief given that you will be easily able to make a large one piece flat cover from flat plate and have it anodised to match the rest of the body should you decide that it is necessary.
Can't get Enough
in General Discussion
Posted
If you identify the riff variations,
then practice them individually till you have them spot on,
then practice swtitching between the different variations with a metronome until the transition is smooth,
you will absorb the phrases into your own playing vocabulary and they will come out naturally after a period of time.
In the short term, as long as you have a couple of the easier variations down it will get you through the gig - as @peteb pointed out having a handle on the underlying chords which form a simple repeating chunk of information is more important than trying to process a long stream of notes if you are struggling to retain the structure.