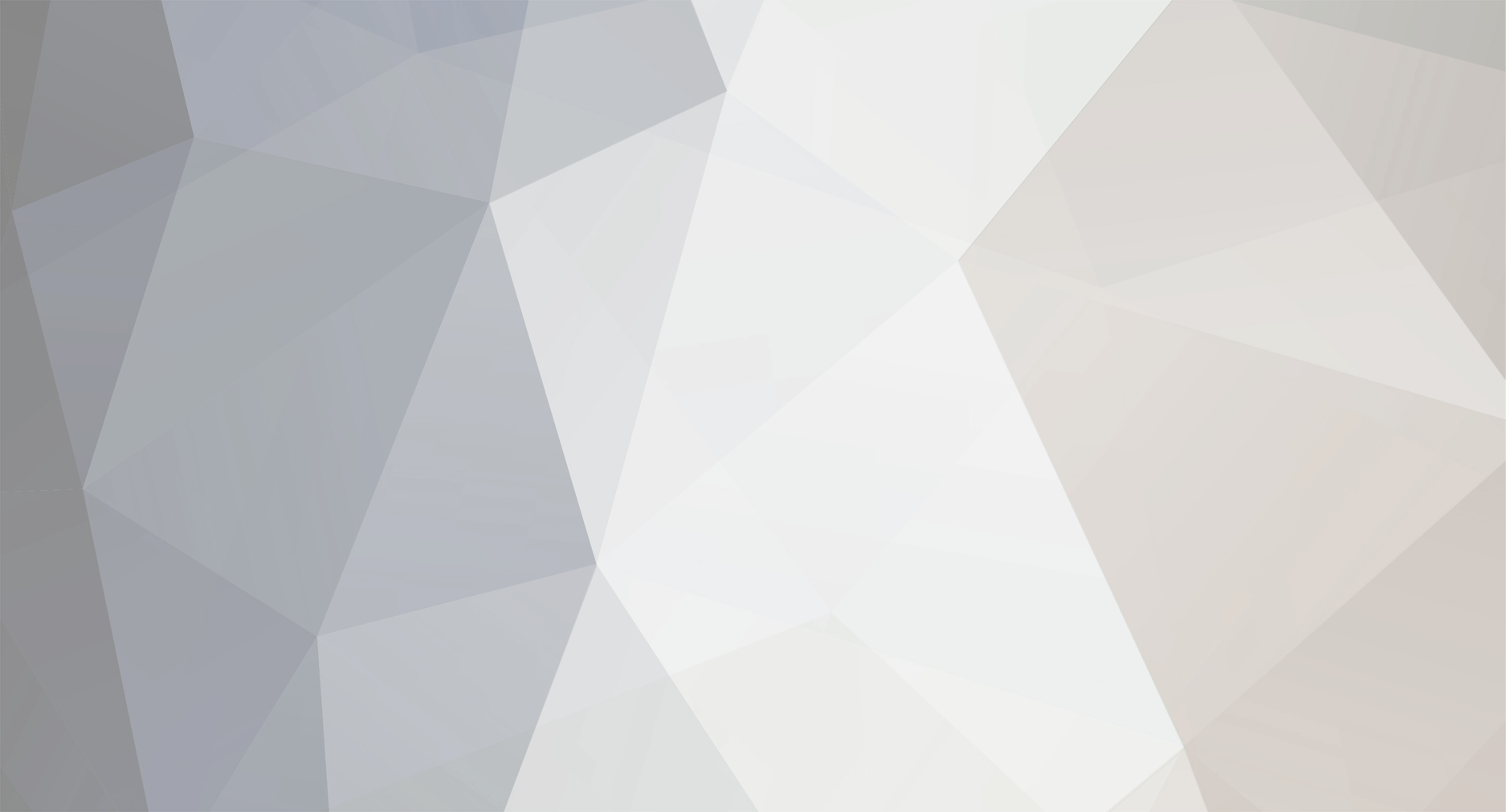
richrips
Member-
Posts
293 -
Joined
-
Last visited
Content Type
Profiles
Forums
Events
Shop
Articles
Everything posted by richrips
-
Most open gear tuners stiffness id dictated by a piece of bent metal which pushes against the screw thread. it is held under the 'cog'. if you disassemble the tuner you can remove this piece of metal and slightly reduce/increase the bend with pliers or in a clamp to reduce/increase stiffness. Some tuners do not have this piece of metal and the only way to adjust them is via the screw as described above, although this may affect the overall stiffness of the tuner assembly and effect the tone. Try both and compare, Rich
-
[quote name='Mr. Foxen' post='832298' date='May 9 2010, 04:00 PM']Since the tension of the strings is a constant, might be some flawed thinking here.[/quote] Not really. The strings exert a constant force, but the overall force on the neck (which is compressive, end to end) is a sum of the tensile force in the neck and tensile force in the truss rod (there may be other forces at play, let me know). These forces needent be equal as each depends on the perpendicular distance of the force from the fulcrum. If the truss rod is set nearer the back of the neck, the distance of the force exerted by the truss rod to the fulcrum is increased, thus the force can be smaller whilst providing the same moment as a shallower truss rod. Hope that makes sense. Just checked out the link for the technical paper. Fascinating stuff. I like the idea of putting a load bearing member beneath the fingerboard at the inertial cedntre of the forces acting on the neck, rather than rely on wood, with its weird respnses to temp/humidity. Not so sure about the modified truss rod slot, as it would imply a wide range of rod movement. if this were adjusted frequently, it seems there is potential for the rod to wear on the sides of the slot and develop the dreaded rattle.... I'd rather see what optimum flex characteristics could be acheived using a rod with a fixed position and fixed pivots which are effective (as a compromise over the 2 seperate tension/compression pivots in the moving rod suggested in the pdf). There should be an optimum curved shape, without seperate pivots, that is still an improvement on the current continuously curved rod placement which obviously is not ideal because as neck thickness varies along its length there are bound to be changes in flex characteristics. Good observation that the guitar industry is able to maintain sales growth despite a distinct lack of concerted technical engineering innovation. I guess that's why a USA p bass still costs nearly a grand after 50 years of no technical advancement. Rich
-
These look absolutely wickid. Weird shapes are the future!! I could definitely see myself with one of these. People are funny about shapes.... recently an Ovation Magnum 1 sold on ebay for £820, yet around the same time an Ovation magnum 3 sold for just over £400. The difference? Only the body shape- the 3 is much more traditional, precision-esque whereas the 1 looks like a space ship. Same woods, same pickups, same electronics, same sound. Makes you wonder.... there's obviously a huge market for quality basses in non-traditional shapes. Now who can sell me an unmarked used Big Al at a knockdown price? Rich
-
After toying with the idea of making my own bass, and having several weeks free this summer, i've been looking in to materials, shapes, pickup positions etc etc and had a thought about truss rods. The truss rod is usually situated just beneath the fingerboard. It's job is to counter the bending effect of having strings under tension on one side of the neck. To do this it provides a tensile force of its own. A couple of things strike me as strange in the standard arrangement. 1.The moment of the force the truss rod can exert is a function of the tensile force within the truss rod (how tight it is) and it's position in relation to the pivot about which that force operates. In the standard arrangement, it would appear that the pivot is the wood between the strings and the truss rod, which is essentially the fingerboard, hence the distance from the pivot is increased as the truss rod is set deeper in the neck (furthur from the strings, deeper below the fingerboard). 2. If the truss rod were routed in to the back of the neck, rather than just below the fingerboard, it could be between 1.5 and 2 times farther away from the strings than it currently is. The distance from the point at which the truss rod acts and the pivot (which would be the position within the neck at the mid point of the 2 opposing forces- string tension and truss rod tension) would then be increased. This would mean less tensile force would be needed in the truss rod to produce the same neck-straightening force (moment) as a truss rod located nearer to the strings (such as a traditional position directly beneath the fingerboard. Less tension in truss rod = less overall force acting on neck. This would appear to have benefits such as: -Less chance of truss rod being damaged since it is under less tension. -potential to use lighter truss rod as its strength requirements would be lower = lighter neck -Possibility that the truss rod could be just beneath the lacquer on the back of the neck, so replacement would not require removal/damage of fingerboard if it did break. I'd be interested to hear from luthiers/builders as to why this is not common practice as i have never seen this, yet to me it seems logical??? Any responses much appreciated! Rich
-
-
[url="http://cgi.ebay.co.uk/NATIONAL-VAL-PRO-85-BASS-GUITAR-/140405368235?cmd=ViewItem&pt=UK_Musical_Instruments_Guitars_CV&hash=item20b0cfe5ab"]http://cgi.ebay.co.uk/NATIONAL-VAL-PRO-85-...=item20b0cfe5ab[/url]
-
Fretless Question - Lining an unlined neck!?
richrips replied to bassatnight's topic in Repairs and Technical
i did this to a yamaha. i'd recommend sawing slots VERY carefully then putting in hard maple markers with as little (decent) epoxy as possible. I used wood filler instead and the markers slowly 'sank' as the filler gradually contracted as it continued to dry out, but luckily i soon snapped the truss rod so i didn't have to live with my mistake for long! To start some heated controversy, i'm going to step out and say: Ahem... I think the idea of not having fret markers on a fretless is just to show off and can't see a logical reason not to have them. The argument that a neck looks better without them is on a par with saying you'd happily drive a car with no speedometer because the dashboard looks more refined, plus people will be impressed at how well you can accurately judge your cars speed without it! And if you really don't need them, why do unlined fretless's usually have sidemarkers? Why do i feel i've just put myself against a wall facing a firing squad of irreconcilably angered fret-marker-less fretless bass players? ....and i guess the upright brigade will be after my blood as well..... well it was nice knowing everyone! Hope the first bit is of some use! Cheers, Rich (in a deliberately inflammatory mood after watching this. Why can't UK politics be this honest and exciting???) [url="http://www.youtube.com/watch?v=SfCRyLlyqJI"]http://www.youtube.com/watch?v=SfCRyLlyqJI[/url] -
These look very similar in design to my BFM Jack Cabs which sound great. Seriously cool and a massive deal too!! [url="http://cgi.ebay.co.uk/Pair-15-200w-Bass-Bins-/200466223076?cmd=ViewItem&pt=UK_ConElec_SpeakersPASystems_RL&hash=item2eacb7cfe4"]http://cgi.ebay.co.uk/Pair-15-200w-Bass-Bi...=item2eacb7cfe4[/url]
-
Who can make me a reasonably priced jazz neck?
richrips replied to richrips's topic in General Discussion
[quote name='waltsdog' post='827708' date='May 4 2010, 06:04 PM']Just had a quote from a local luthier for a bog standard neck replacement they were talking £300.[/quote] Ouch! I've just been looking at tonewood suppliers. Seems the maple and ebony will cost me less than £100. set of router bits = less than £20. and i can make my dream bass for little more than several hours fun in the garage. Also been looking at vacuum bagging carbon construction with interest.... Rich -
Who can make me a reasonably priced jazz neck?
richrips replied to richrips's topic in General Discussion
[quote name='umcoo' post='827138' date='May 4 2010, 09:44 AM']What would you consider a good price? I've got a maple/rosewood Warmoth jazz neck with tele headstock and hipshot hb-2 tuners on it.[/quote] i'm looking to spend around £150. Given the cost of materials, i'd have thought someone could make me one for around that. I don't need block inlays, vintage lacquer (i can lacquer it myself if needs), or binding. just the two bits of wood, shaped and fretted with a truss rod. I'd be happy with a paddle headstock and would probably be up to shaping the back of the neck myself (don't have the tools for levelling, radiusing, cutting fret slots, etc so would rather have this done by an experienced builder). Thanks for the offer Umcoo, i'm not 100% keen on a tele headstock or rosewood fretboard, but if you want to PM me a price the worst i can do is say no! And they are tasty tasty tuners.... Cheers Rich -
[quote name='chriswilliams666' post='826768' date='May 3 2010, 07:31 PM']Definately agree with Chris there. I wacked a BadAss on an old squier. It definately enhanced the top-end and also i was in a Drop C Tuning, and the old-school Fender saddles moved about. The BadAss doesn't budge![/quote] I think this is actually where the badass fails. The saddles may run in grooves, but the grooves are not a tight fit, so the saddles can still move slightly from side to side. My friend has an original 75 jazz with a badass 2 and if you play the g string hard, it clicks. This wouldn't be a problem if the saddles had absolutely no lateral movement, as is the case with the gotoh and, from the looks of it, the schaller 3D. GOOD example: (note how the grooves for the grub screws are narrow to provide an 'interference' type fit to the end of each grub screw = no lateral movement) [url="http://thumbnail.image.rakuten.co.jp/@0_mall/m-shower/cabinet/parts/schaller_bass_bridg4.jpg"]http://thumbnail.image.rakuten.co.jp/@0_ma...bass_bridg4.jpg[/url] BAD example: (scroll down for best view. note grooves flat-bottomed and wider than grub screws where slight lateral movement is a definite possibility) [url="http://cgi.ebay.co.uk/5-STRING-BASS-GUITAR-BRIDGE-THROUGH-BODY-CH-BK-GD-/160288461040?cmd=ViewItem&pt=UK_Guitar_Accessories&hash=item2551efd0f0"]http://cgi.ebay.co.uk/5-STRING-BASS-GUITAR...=item2551efd0f0[/url] WORSE example: (nothing to prevent lateral movement) [url="http://cgi.ebay.co.uk/CHROME-BRIDGE-ELECTRIC-5-STRINGS-BASS-GUITAR-/390190278462?cmd=ViewItem&pt=UK_Guitar_Accessories&hash=item5ad927273e"]http://cgi.ebay.co.uk/CHROME-BRIDGE-ELECTR...=item5ad927273e[/url] Hmmmmmm. Rich
-
Who can make me a reasonably priced jazz neck?
richrips replied to richrips's topic in General Discussion
Mighty mite are very good. i had a p bass neck maple/maple by them which was solid and very well made. they just don't make an maple/ebony/21fret neck as far as i know. WD, Allparts and Mighty Mite seem quite similar, whereas Warmoth use steel bars inside the neck for extra stability and removal of dead spots. Both WD and Warmoth do very nicely finished necks from what i've seen. Afriends Warmoth Jazz neck is possibly the nicest jazz neck i've seen.... Ebony/maple/21fret anyone??? Rich -
[quote name='lemmywinks' post='827001' date='May 3 2010, 11:54 PM']The Mastotron isn't all that expensive, i got mine for £76 new and they're £89 now. Some Zvex pedals are stupidly expensive (£220+ for a Wooly Mammoth? no ta!) but the Mastotron is IMO opinion reasonably priced, especially considering it has features most other fuzz pedals lack suck as impedance, wave shape and the 3 way sub switch[/quote] havn't seen these looks much more reasonably priced! any bass videos/demos anywhere?? rich
-
There's loads of fuzz pedals out there. Best site to help you: www.bassfuzz.com I got the Malekko assmaster silicon and its a wickid sounding pedal, but each to their own and all pedals are sound sampled on the site. ZVEX = grossly overpriced (insert verbal abuse HERE from zvex owners, with extra abuse for me in particular for owning a mammoth clone which cost very little to build) Hope bassfuzz sorts you out! Rich
-
Hey team, Warmoth and WD both make the neck i want, but by the time you have paid for their 'brand reputation' and import tax, they cost a bomb. what do i want? Jazz neck to fit standard pocket, ebony fingerboard, 21 frets with overhang. I've looked at chinese stuff and the reviews are mixed. i'm pretty sure there are guys on here who could do a much better job. Any suggestions? Cheers, Rich
-
[url="http://www.guitarpartsworldwide.com/p/product/0909131310-BASS+NECK+PADDLE+HEAD+EBONY/"]http://www.guitarpartsworldwide.com/p/prod...DLE+HEAD+EBONY/[/url] I'm particularly keen on the paddle headed ebony/maple, but would like to know A: Has anyone tried a neck from this place? B: Anyone know where i can get a maple/ebony neck cheaper? Cheers, Rich
-
Yeah the Fender HMV looks good, again not because it is high mass, but it seems to have been stiffened in all the correct places: Grooves to stop lateral movement of saddles, Strengthened/thickened at the end where the original fender bridge was just bent, Brass saddles. I still think it's overpriced, but looks like a great bit of kit. Anyone got one of these? Are the grooves for the feet of the saddles a snug fit for the bottom of the grub screws? i've seen a few designs where the saddles or their feet have grooves, but the lack of a tight fit means they may as well not be there.... Pretty good looking too! Rich
-
[quote name='Musicman20' post='825770' date='May 2 2010, 07:01 PM']Basic Flea lines (ive found a few) are probably a good place to start,[/quote] Yeah get you "Black eyed blonde" on!! best bassline ever???
-
Damn! way too fast for me! Typical after i just start looking for one having examined one on a friends bass and found it to stand up to mechanical scrutiny..... If youneed to sell it again due to unforseen circumstances (bribary, corruption, tabloid campaign, or ....getting a guitar) , let me know! cheers, Rich
-
[quote name='OutToPlayJazz' post='825526' date='May 2 2010, 02:21 PM']The only slight problem you may have with a Gotoh is that the base plate is a lot thicker than the Fender bridges, so sometimes a neck shim (or adjustment on the micro tilt if you have one) is required, otherwise the action will be too high.[/quote] This seems to be a common problem with "hi mass" bridges. Had this with a badass on a 75 jazz reissue. couldn't get my g string down..... Got me thinking. if thinness is required, mass (in my opinion) not particularly relevant, stiffness very important, maybe i should design and high pressure molded carbon fibre bridge assembly? Brass saddles, gotoh-esque grooves for the saddle grub screws, thin, upper surface structure to provide maximum stiffness resulting in a low profile bridge, with very low movement and flex, reducing vibrational losses between the string and body. Hmmmmm...... Rich
-
[quote name='OutToPlayJazz' post='825521' date='May 2 2010, 02:17 PM']Is someone digging up old threads? Bored today, are we? [/quote] Busted! i Just found out that Orange have been charging me £5 per month extra for internet on my mobile for over a year which i never used and never new i was paying for. This made me rather angry, and the poor engineering of the much over-hyped Badass 2 seemed like the obvious target to vent some rage! Luckily i'm not bored, as i have a 3000 word review paper on the "effecst of climate change on european salmonids" to enthral me.... Rich anyone got a Gotoh 201 kicking around the shed??
-
I think the Badass is flawed. The deep cast grooves that each saddle is meant to rest in are not a tight fit to the saddle so they are free to move slightly side to side. There bay be an improvement in stiffness, compared to the bent metal fender bridge, but nobody has yet been able to explain in logical scientific terms why a bridges mass imparts something on the tone of an instrument. From an engineering perspective, the stiffness with which the string is held would have much more effect (as long as mass of the bridge does not have a significant effect on the mass of the bass). The gotoh may lose some structural stiffness by being a thinner unit than the badass, butthis is more than compensated for because, unlike the badass, each saddle's grub screws rest in concave grooves with absolutely no side to side movement possible. Humf!! Rich