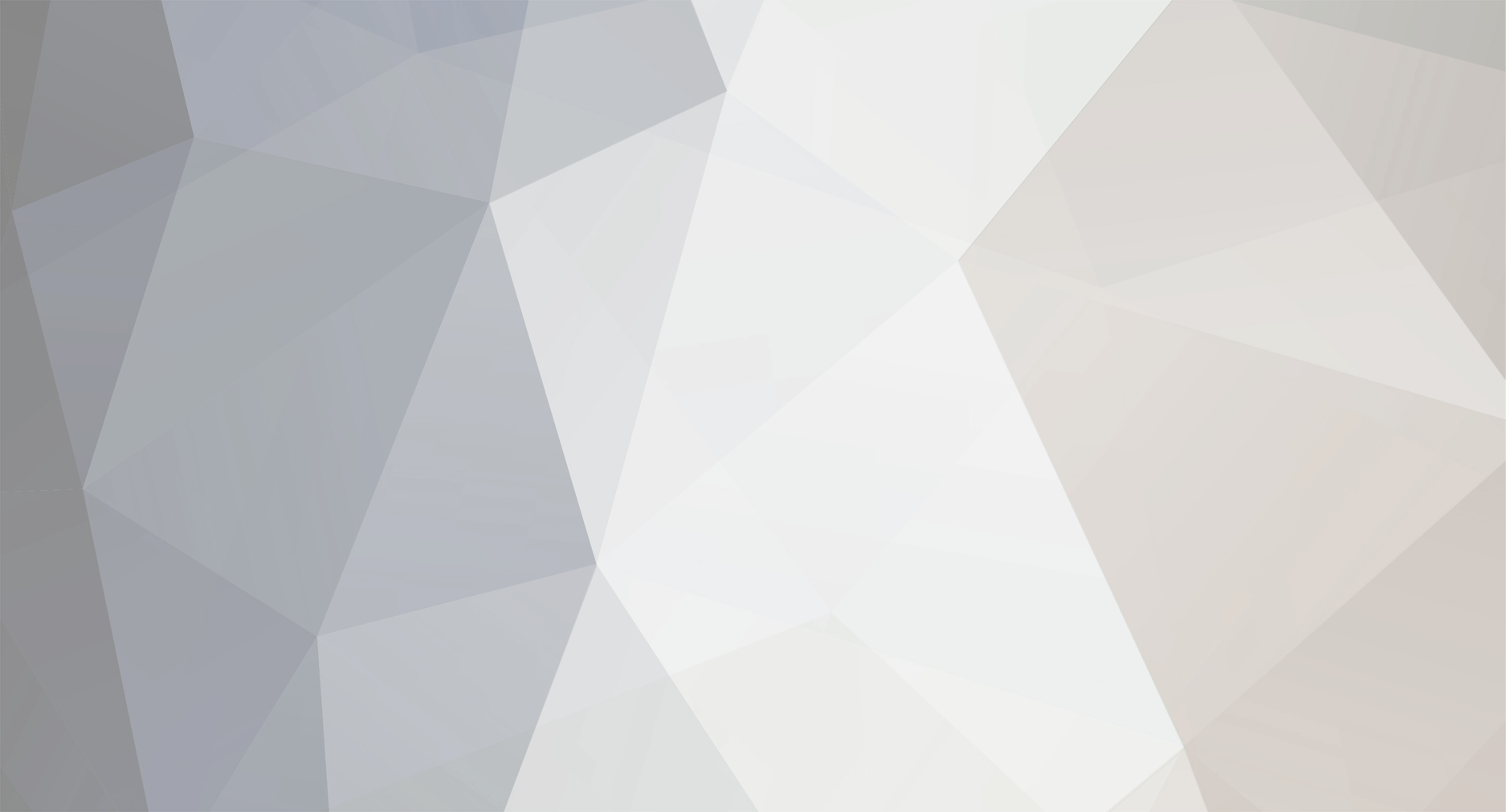
rwillett
⭐Supporting Member⭐-
Posts
1,625 -
Joined
-
Last visited
-
Days Won
6
Content Type
Profiles
Forums
Events
Shop
Articles
Everything posted by rwillett
-
I remember the wobbly ZX81 RAM pack. 8KB and 16KB? Didn't the ZX81 turn the display off for certain instructions as it couldn't refresh the screen display and execute the code at the same time? Was it 1Mhz or something? perhaps it was 4Khz Kids today don't know they are born. Rob
-
And for those of you who remembered when memory was expensive and we really, really, really had to save memory This is the output of one of the sketches for the Arduino. This is for an Uno which has 32KB of program space (where the executable resides) and 2K (Two f%^&*@£ing KiloBytes of memory) I have washing machines with more space. I have ball point pens with more capacity than this. My sodding cat flap has more storage space than 2KB. I suspect the dogs glow in the dark collar has more than this. I've spent athe last two hours writing string arrays to sit in readonly mode to get more space for local storage and the stack. 2KB of local variable space <shakes head and goes and opens another bottle of wine> Kids today, don't know they are born. Sketch uses 3120 bytes (9%) of program storage space. Maximum is 32256 bytes. Global variables use 368 bytes (17%) of dynamic memory, leaving 1680 bytes for local variables. Maximum is 2048 bytes.
-
What makes you think I'm not a grumpy old git now? Modbus is too professional for a hack like me.
-
After spending a number of evenings trying to get two Arduinos to talk reliably to each other through serial comms, I have given up. I can get them talking but no matter what I try, I cannot make it work reliably. I keep getting spurious characters. I suspect there is a timing issue that I simply don't understand. It's embarrassing to keep hitting my head on the table in front of the kids as I weep trying to get serial comms to work. So I'm changing my approach. I'm going to work out the i2c protocol and use that instead. I2C is packet based (32 byte messages) and looks significantly simpler, once you understand it (key point). The advantages of i2c is that it is a master/slace relationship using unique addresses for devices. The new approach will be: The Arduino Nano will be the master. This may become an Uno if I need a few extra IO pins. Its going to be tight but an Uno is no big problem. The Arduino Mega will be one slave. The 4x4 keyboard and LCD display will move from the Mega to the Uno. This simplifies comms. My original intention was to make the Uno a display only device and all the display commands would come from the Mega. The Mega may get replaced by a simpler Uno as the additional pins on the Mega are not needed now the display and keypad have moved to the Nano or Uno The Mega and LCD will be slaves on the I2C bus but this still allows bidrectional communication. to the master Nano. (Kinky) The software design now has all the LCD and keypad handling on the Nano. The Mega just does motors. The Nano master will simply send motor commands to the Mega slave in a fire and forget approach. The Mega slave will the count of motor step updates back to the Nano master every second or so via the I2C bus. The Nano will simply update as needed. The Nano master will write state into the 512Byte (512 BYTES!!!) so it remembers state after being turned off. Most of the code will continue to be used, especially all the motor code. I will refactor the keyboard and LCD code to work on the Nano and use the I2C to interface it all. Lets see how this goes.... Rob
-
Just put the sodding embedded nuts in to the last big piece. It's 00:11, so pretty much on time and when I expected it to be, however I really want to be in bed. Spent the last two hours staying awake trying to debug serial code on my guitar winder, not sure the 0.5L of Chablis helped, but suspect I may now sleep well. I do hate programming serial code, I forgot how much I hated it, everything has to be perfect for two systems to work. Network code is so, so much simpler, write a packet and send it. Oh well, perhaps a good nights sleep will help me. Rob
-
I love the front of it, but the paint work around that access port is rubbish. Looks like someone tried to do it with their teeth. I'm not even certain if that access hole is even round. I'd be embarrased if I'd printed that in draft mode on my printer. After saying that, the frontand the rest is gorgeous. Very jealous, Enjoy it. Rob
-
4 x Chrome tuners unused
rwillett replied to MungoBass's topic in Accessories & Other Musically Related Items For Sale
Hi David That seems very narrow, I wonder if we are talking at cross purposes? Here's the neck, it currently has chome bushings in that have an internal diameter of 13.75mm. I can pull these chrome bushings out though (or I think I can). The backside of the headstock has a hole circa 17.15mm, probably supposed to be 17mm. I was wondering what the external diamter of the component below is. it looks bigger than 10mm but I could be talking nonsense as normal. Many thanks Rob -
@JohnH89 Thanks very much, keep hold of the vaneer for the moment. I'm going to focus on getting it built and working. Fripperies such as veneer backed headstocks are way down the list. It will work and sound fine without the walnet backing or I hope it will. The top middle is being printed and I have a midnight alarm set to add some embedded nuts in to it. Not happy about that, but paid and real work got in the way, delaying my personal and unpaid work. Just finished the design of the bridge adapter. This is specific to each bridge and bolts down to the middle sections below. Thats one of the reasons for the embedded nuts. It is supposed to be a genuine MIJ Fender Jazz Bridge, it looks like a piece of folded crap to me, but I'm assured its real. This will screw into the bridge adapter. The bridge adapter will screw into the body. This was a feature that worked well on my six string guitar as I made a measurement mistake on the six string and had to move the bridge back by 5mm, I just printed off a new adapter and used that instead. The above bridge screws into here. The eight outer holes are slighly resessed so they don't interfere with the bridge. The seven smaller holes hold the bridge, or at least thats the intention. Lets see if they pull themselves to pieces. You can also see the earthing strap exit hole on the top and the front entrance hole underneath a little cut away,
-
The bushings took 5 mins to design, and 20-30 mins to print. I'll do them for free for anybody who wants them, in just about any (sensible) size. Its changing three parameters to design them, internal diameter, external diameter and height. They're easy to print as they need no special handling. I realised after fitting them, that they can't deform as there is laterally nowhere for them to deform to as they are such a tight fit. Quicker than metal as well. @JohnH89 I could easily print a backing layer and attach it, but I do like your walnut veneer. Perhaps if you need something printed, we'll do a swap and you can do my headstock Thanks Rob
-
A quick sanity check to see if everything fits. Just laid this out, no proper assembly at all. It's 430mm from the nut to the 12th fret and 430mm to where the supports are on the bridge. The bridge doesn't have a lot of room but just enough, phew. If I was out by 5-10mm, I'd reprint the top left part and move the neck out by 5-10mm. Something is missing but can't put my finger on it
-
@JohnH89 That's really helpful, I'll look at doing that. The back of the neck looks a lot easier for a veneer than the front. I can easily clamp it, as I do have a lot of clamps. Didn't know about the towel and hot water trick. The neck is maple (I think), but a heavy weathered finish. I am very unlikely to find a veneer that will closely match, so using a contrasting veneer would be best. I do like your walnut finish. That Black Bison Wax is expensive though I've just finished making the bushings to make the Hipshort Ultralites fit the neck. An easy 3D print even at 100% infill of about 10min each, nice and tight and the plastic won't deform (or at least I hope not, otherwise I'll have to do it in metal). 18.5mm external diameter and 16.75mm internal diameter. You can see two of them below. I've screwed the two Hipshots on to make sure they all fit. Now printing the last big piece of the guitar Relatively small at 22 hours Rob
-
Is it on here? http://75.151.102.194/DDOS I just searched for the file XUSBAudioDfu.exe which might be the right installer or might not. I don't have the x32 so not 100% sure. which file you might need. I suspect there are other sites that might have it as well that are more legitimate. Personally speaking I wouldn't download it from the above but depends on your level of risk or need. If you can find the checksum of the the file that'll give you some level of comfort. Rob
-
Now that is a good idea. Didn't think of that. is that a wood laminate or something else (I have no idea what else it could be). Is it easy to apply? The front of the headstock is fine, its the back that I want to cover up. Just looked at the back and it's very flat and might be easy to do (for some value of the word easy). Let me know what you did to get that lovely finish please. Between the two of us, you're fine with wood and metal, and I'm find with computer/CAD we might make a complete artist Rob
-
So far so good. The picture below is the Top Right of the guitar. 22hrs 43mins to go. The hexagon pattern is the support for the undeneath of the middle of the guitar. This support will be cut away as the middle of the guitar is H shaped. The bottom part of the H will be the plywood backbone. This is a cutaway of the guitar so you can see the H. This helps provide strutural integrity This the the top left and middle. This was 38 hours long and now down to 18 hours or so. The section on the right in the picture below is the top left of the guitar. The section on the right with the the holes is where the bridge and pickups will go. The holes on each side allow pickups to be mounted directly to the guitar OR I can mount the pickups on a pickup shield. There's one more major section to print after this and then I can think about assembly. I now have the Hipshot lightweight tuners, thanks @Raslee. I will need to make some bushingsso that they are a tight fit. I have also been filling the back of the guitar neck wher the old mounting screws were with bamboo skewers and TiteBond. It was suggested that Bamboo is a good choice as its a very hard wood and it comes in 3mm wide skewers which are a bit big, but I trim them down. The only problem is that the colours don't make at all Any suggestions as to handle the colour difference welcomed.
-
It's the first layers that normally go wrong. So far, so good. Both printers running, just changed the filament on them so they'll now run through the night. Thats the idea anyway. I'm normally up around 06:30 so will check in on them. if these go OK, then two more to go, similar times to print. I'll set up the webcams on the next lot so I can do time lapse recordings. Rob
-
Might have underestimated the printing time a wee bit This will take 28 hours <gulp>. No embedded nuts so fire and forget. This one is 37 hours 82MB of g-code, hoping nothing goes wrong. Lots of embedded nuts 18 hours in, so around 09:00 tomorrow morning.
-
Not sure what the difference will be here as the body is plastic and there is a plywood back. I've just had a blast on the 3d printed six string and compared it to my Telecaster, its different but the sustain feels the same. Now I am not a good guitarist, I'm not even sure I'm good enough to be even a bad one, so other people will have a different opinion. I'll bring all my guitars along to the NW Bass Bash so people can play and find out. The bass might be finished by then (I hope). Rob
-
No problem, let me book myself into a hospital to have all my good taste, common sense and aversion to bling removed Give me a few days. Rob
-
After a lot of thinking about how to simplify things, I think I've got the design finished. I've been trying to work out how to simplify the printing and print at a higher resolution so it looks good. The issue was and still is, printing at a higher resolution takes a lot longer, a hell of a lot longer and when you have to do things like embed nuts to allow the pickguard to attach, you find that this needs to be done at 03:30 in the morning which is not conducive to a good nights sleep. So I have experimented with gluing nuts and similar in AFTER the guitar has been printed. This means that I focus on getting the nuts embedded early in the guitar print and then, let it print for the next 26 hours. You can see this with the twelve large circular holes below. Ignore the large number of M3 holes, they still stay there. I've now split the model to make each piece as big as possible so the bits only just fit on the printing bed. Before I had nine pieces, I'm now down to five (plus the neck adaptor). I have most of the rest the pieces as well, neck, lightweight tuners, bridge, pickups (though I may wind my own), control knobs and tone controls. So I've about 7-10 days of printing but I have six 1Kg rolls of black so should be OK.
-
4 x Chrome tuners unused
rwillett replied to MungoBass's topic in Accessories & Other Musically Related Items For Sale
-
The Hipshots have arrived. Thanks very much. Lovely piece of kit, I will need to print a 1mm spacer 18mm in diameter to make them fit, which I knew I'd have to do. Not paying £5 each for a spacer, so wen the printer becomes free, sometime tomorrow as there are two big jobs running, I'll get those printed and installed. Probably 30 mins top. My scales have them down as 215g for 4 = 53.75g each. I suspect my Jazz tuners are double that. Looking forward to getting them on the 3d printed guitar. Very happy, thanks Rob
-
Sounds like everytime I try to play....
-
That's exactly my point as to why I shouldn't be let near power tools.
-
I'm tired of playing with fire... and electricity greater than 0.1A and 5V... and circular saws that jump off the bed...and heat sinks that can melt lead...and toxic fumes from playing with ABS...and picking up hot metal from forges... I just about have 10 fingers and thumbs, though I look at them and I have knocked chunks off them and have had bits sewn back on. Rob