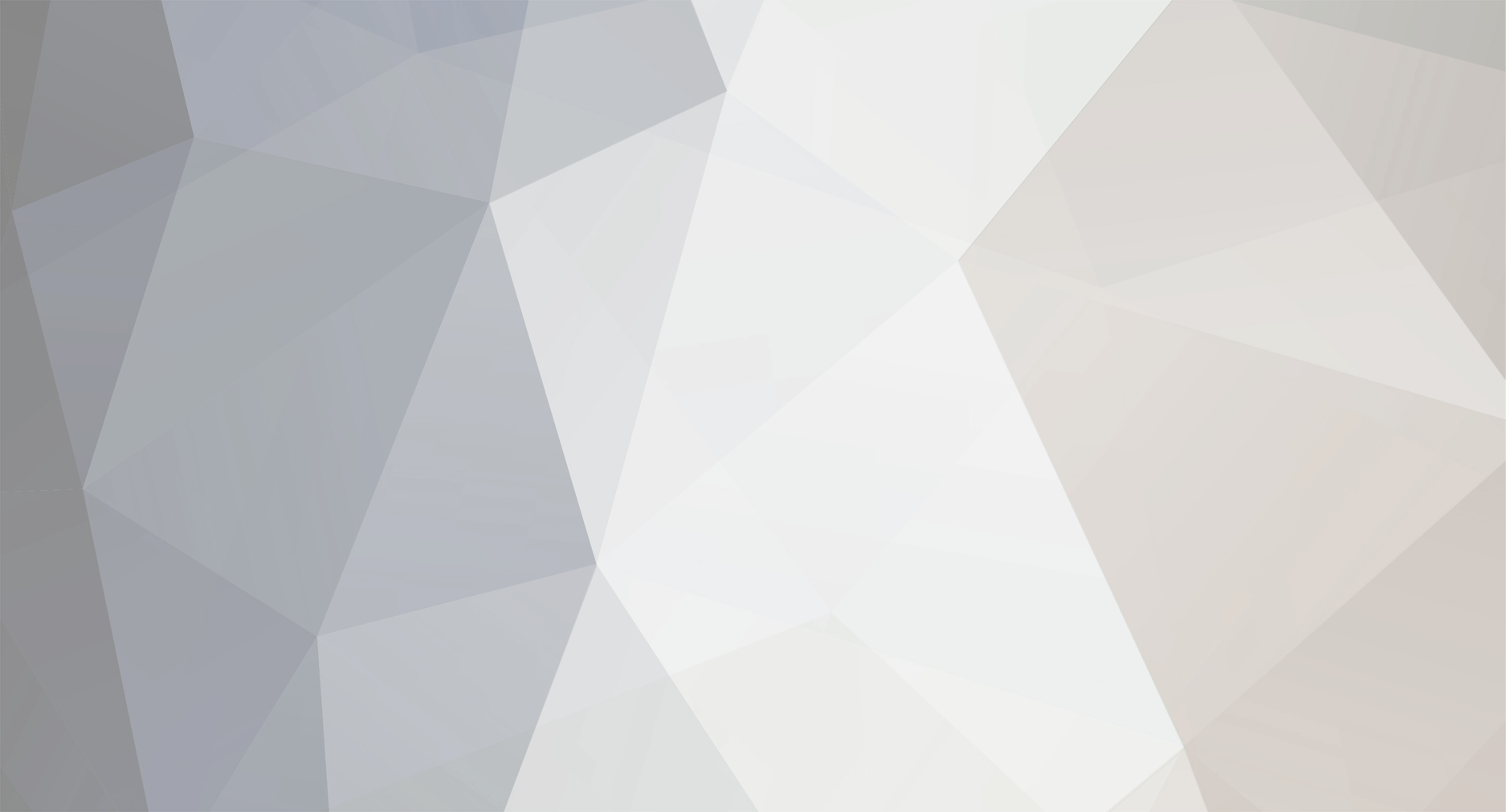
rwillett
⭐Supporting Member⭐-
Posts
1,531 -
Joined
-
Last visited
-
Days Won
5
Content Type
Profiles
Forums
Events
Shop
Articles
Everything posted by rwillett
-
Thats a good idea. Just printing pick guards and will look at that
-
Why can't I have accidents like that? My accidents normally consist of removing parts of me through incompetence and trips to A&E to meet the nurses who are fast becoming family friends. When they greet you by your first name, you know you've come too many times.
-
Gorgeous. You must tell me how to have a happy accident
-
Have now printed all pieces, I redid a few as I wasn't 100% happy with the results. Printing at 0.2mm does a lot better quality than 0.3mm but takes so much longer. Checked the measurements and the bridge is in the right position. Might like to move it back 5mm but thats a quick print of the bridge adapter and six bolts. So that seems to work (or appears to). Printed a couple of round plugs to hold the pickguard nuts. You can see the large round holes in the picture which are empty whilst the control panel has five of the plugs glued in. I'm becoming a big fan of FloPlast as its simple to use, doesn't ooze out, welds quickly, doesn't expand and is very, very strong. Aesthetically, it looks right. The proportions looks good, I know that @tauzero hates the headstock here, but it is what it is. Next steps are cutting the plywood backbone to the right size, and drilling the mounting holes in the right place. So to make it easy, I've printed a drill jig, I would have had the plywood cut accuratley using a table saw, but my neighbour has just broken his foot and can't get into his workshop, so I may have to pull out a saw or even worse, a circular saw, and do it myself. <gulp> Then, bolt the middle together, no glue, and see if the el-cheapo strings I have snap it into two pieces Plan B if they do snap, is an aluminium and ply backbone, Plan C an all aluminium and Plan D a Carbon Fibre backbone. Thats for the weekend. Rob
-
What is this FTW of which you speak? Fitness To Work? For The Win? F**k The World? Forever Two Wheels? Free the Whales? Free To Watch? Feel The Wind? For The Will? Fight To Win? Finding The Way? Feed The World? For Those Wondering? Ford Truck World? Forschungszentrum Telekommunikation Wien? Fear The Wire? Free Trade Wharf? Florida Tax Watch?
-
I did read more up about it and I found that out. I have 4-5 Arduinos anyway, so will keep using them, the 2K limit is a challenge but I can make it work. The ESP32 doesn't seem to have quite such a large eco system around it, thought it does look very capable. Perhaps V2
-
Thanks Never tried that. What's the finish on the bottom like after using 3dlac? Rob
-
I have now found that there is a limit on just how big you can print on a Prusa printer without the edges possibly lifting or warping. Some filaments, PETG is one, are slightly fiddly to print, you need a very consistent temperature across the bed and if it's too big, the edges can lift very slightly from the bed, this may only be 0.3-0.5mm but thats enough to be noticable. I found that some of the very large prints were slightly lifting and warping. The solution to this could be: Put an enclosure around the printer to keep it at a high temperature. This puts the electronics at risk, so you normally move the motherboard and PSU outside the enclosure. This is a lot of work and takes up a lot of space, so is not really an option here. Heat the bed even more. I run that at 90C already so not keen. Use a glue to hold the print down. Possible but the bed needs to be cleaned afterwards. Print micky mouse ears to the corners so that there is more adhesion. I don't have much space left to do that, so not an option, also it leaves marks on the model. Change the cooling fan so it works less. Bit tricky and I've never had much success with that. Reduce the size of the print. I'm going with the last one as its not that difficult to make the prints smaller (a few mins work) and then weld them together again afterwards. The glues I use actually weld the plastic, so it melts it and then the bond is very, very strong. This does create more join lines but since I'm printing at a higher resolution than before, the quality is significantly better than the last six string. I'm quite pleased with the finish and it's starting to look significantly nicer. I am very picky, so thats a big bonus. I may slightly redesign the pickguards to cover the join lines. However given the higher quality of print (and is noticably better), this may not be an issue. Overall splitting the model down into smaller parts doesn't increase the overall printing time, so instead of 38 hours for a print, it's 2 x 19 hours (or so). This means I have delayed actually assembling the guitar for fit, but the prints I have redone look good. I'm still intending to try and epoxy refinish with a black colour pigment. So thats black on black. I may call this model NSB-1 (None So Black) Rob
-
I don't think thats a bad looking guitar. I'm unclear as to why you would take a 12 string to a six string, but hey ho. It seems a nice looking guitar. No idea what it plays like, and I think he might benefit from a sales writing and marketing course, but if I was offered it for £50 I'd take it,
-
I've now decided that after I finish my 3d printed bass ... ... I am going to give up all my worldy goods, throw away my shoes ands walk barefoot, I will give up meat, and strong alcohol (though perhaps a small cider on a Sunday), forswear strong drugs and carnal passions, wear sackcloth and rub ashes into my hair and then sit at the feet of this master luthier so I can learn the ways of guitar building. I am clearly a novice and not worthy,.
-
Can't see the picture. Would love to see his latest work
-
Would you?
-
It looks like the LCD itself is sloooooooow. The i2c bus works at 100K. It's not much faster than a decent modem but it's enough. The timings for changing the LCD Display are quite large, I didn't realise TBH but I am where I am. I've just got the i2c packet stuff working now. Just sending down "Hello World" from the Uno to the Mega and it's a lot more reliable and simpler. Wire.beginTransmission(1); Wire.write("Hello World 2"); Wire.endTransmission(); I'm getting 13 bytes every time which is more than I did with the serial comms. It's non-blocking as well (AFAIK), so it looks OK. Now I need to get bidirectional comms, initially an ACK and then some more informative stuff. I have Arduinos around me and shields and I've just spent a few weeks learning more about how they work. No idea about the ESP32 so will stay on these as it looks a lot more promising, I'll work with a 2K variable limit. Will force me to be creative and selective. Rob
-
Yep I know the maths. I also have never built a bass before, and to be honest, I don't have a particularly long history of building many guitars. So far I'm up to two completed. I can't imagine Fender and Gibson quaking in their shoes at the moment. So I'll build this one and learn from it before I go the next one. I have most of the parts for a headless bass but wanted to build a normal bass first to learn. Also the length of your suggested top horn worries me as it's thin and long. Not sure I would have much structural integrity there. I'm still not cutting the head off a Fender neck. If anything I'd sell it first.
-
I remember the wobbly ZX81 RAM pack. 8KB and 16KB? Didn't the ZX81 turn the display off for certain instructions as it couldn't refresh the screen display and execute the code at the same time? Was it 1Mhz or something? perhaps it was 4Khz Kids today don't know they are born. Rob
-
And for those of you who remembered when memory was expensive and we really, really, really had to save memory This is the output of one of the sketches for the Arduino. This is for an Uno which has 32KB of program space (where the executable resides) and 2K (Two f%^&*@£ing KiloBytes of memory) I have washing machines with more space. I have ball point pens with more capacity than this. My sodding cat flap has more storage space than 2KB. I suspect the dogs glow in the dark collar has more than this. I've spent athe last two hours writing string arrays to sit in readonly mode to get more space for local storage and the stack. 2KB of local variable space <shakes head and goes and opens another bottle of wine> Kids today, don't know they are born. Sketch uses 3120 bytes (9%) of program storage space. Maximum is 32256 bytes. Global variables use 368 bytes (17%) of dynamic memory, leaving 1680 bytes for local variables. Maximum is 2048 bytes.
-
What makes you think I'm not a grumpy old git now? Modbus is too professional for a hack like me.
-
After spending a number of evenings trying to get two Arduinos to talk reliably to each other through serial comms, I have given up. I can get them talking but no matter what I try, I cannot make it work reliably. I keep getting spurious characters. I suspect there is a timing issue that I simply don't understand. It's embarrassing to keep hitting my head on the table in front of the kids as I weep trying to get serial comms to work. So I'm changing my approach. I'm going to work out the i2c protocol and use that instead. I2C is packet based (32 byte messages) and looks significantly simpler, once you understand it (key point). The advantages of i2c is that it is a master/slace relationship using unique addresses for devices. The new approach will be: The Arduino Nano will be the master. This may become an Uno if I need a few extra IO pins. Its going to be tight but an Uno is no big problem. The Arduino Mega will be one slave. The 4x4 keyboard and LCD display will move from the Mega to the Uno. This simplifies comms. My original intention was to make the Uno a display only device and all the display commands would come from the Mega. The Mega may get replaced by a simpler Uno as the additional pins on the Mega are not needed now the display and keypad have moved to the Nano or Uno The Mega and LCD will be slaves on the I2C bus but this still allows bidrectional communication. to the master Nano. (Kinky) The software design now has all the LCD and keypad handling on the Nano. The Mega just does motors. The Nano master will simply send motor commands to the Mega slave in a fire and forget approach. The Mega slave will the count of motor step updates back to the Nano master every second or so via the I2C bus. The Nano will simply update as needed. The Nano master will write state into the 512Byte (512 BYTES!!!) so it remembers state after being turned off. Most of the code will continue to be used, especially all the motor code. I will refactor the keyboard and LCD code to work on the Nano and use the I2C to interface it all. Lets see how this goes.... Rob
-
Just put the sodding embedded nuts in to the last big piece. It's 00:11, so pretty much on time and when I expected it to be, however I really want to be in bed. Spent the last two hours staying awake trying to debug serial code on my guitar winder, not sure the 0.5L of Chablis helped, but suspect I may now sleep well. I do hate programming serial code, I forgot how much I hated it, everything has to be perfect for two systems to work. Network code is so, so much simpler, write a packet and send it. Oh well, perhaps a good nights sleep will help me. Rob
-
I love the front of it, but the paint work around that access port is rubbish. Looks like someone tried to do it with their teeth. I'm not even certain if that access hole is even round. I'd be embarrased if I'd printed that in draft mode on my printer. After saying that, the frontand the rest is gorgeous. Very jealous, Enjoy it. Rob
-
4 x Chrome tuners unused
rwillett replied to MungoBass's topic in Accessories & Other Musically Related Items For Sale
Hi David That seems very narrow, I wonder if we are talking at cross purposes? Here's the neck, it currently has chome bushings in that have an internal diameter of 13.75mm. I can pull these chrome bushings out though (or I think I can). The backside of the headstock has a hole circa 17.15mm, probably supposed to be 17mm. I was wondering what the external diamter of the component below is. it looks bigger than 10mm but I could be talking nonsense as normal. Many thanks Rob -
@JohnH89 Thanks very much, keep hold of the vaneer for the moment. I'm going to focus on getting it built and working. Fripperies such as veneer backed headstocks are way down the list. It will work and sound fine without the walnet backing or I hope it will. The top middle is being printed and I have a midnight alarm set to add some embedded nuts in to it. Not happy about that, but paid and real work got in the way, delaying my personal and unpaid work. Just finished the design of the bridge adapter. This is specific to each bridge and bolts down to the middle sections below. Thats one of the reasons for the embedded nuts. It is supposed to be a genuine MIJ Fender Jazz Bridge, it looks like a piece of folded crap to me, but I'm assured its real. This will screw into the bridge adapter. The bridge adapter will screw into the body. This was a feature that worked well on my six string guitar as I made a measurement mistake on the six string and had to move the bridge back by 5mm, I just printed off a new adapter and used that instead. The above bridge screws into here. The eight outer holes are slighly resessed so they don't interfere with the bridge. The seven smaller holes hold the bridge, or at least thats the intention. Lets see if they pull themselves to pieces. You can also see the earthing strap exit hole on the top and the front entrance hole underneath a little cut away,
-
The bushings took 5 mins to design, and 20-30 mins to print. I'll do them for free for anybody who wants them, in just about any (sensible) size. Its changing three parameters to design them, internal diameter, external diameter and height. They're easy to print as they need no special handling. I realised after fitting them, that they can't deform as there is laterally nowhere for them to deform to as they are such a tight fit. Quicker than metal as well. @JohnH89 I could easily print a backing layer and attach it, but I do like your walnut veneer. Perhaps if you need something printed, we'll do a swap and you can do my headstock Thanks Rob
-
A quick sanity check to see if everything fits. Just laid this out, no proper assembly at all. It's 430mm from the nut to the 12th fret and 430mm to where the supports are on the bridge. The bridge doesn't have a lot of room but just enough, phew. If I was out by 5-10mm, I'd reprint the top left part and move the neck out by 5-10mm. Something is missing but can't put my finger on it
-
@JohnH89 That's really helpful, I'll look at doing that. The back of the neck looks a lot easier for a veneer than the front. I can easily clamp it, as I do have a lot of clamps. Didn't know about the towel and hot water trick. The neck is maple (I think), but a heavy weathered finish. I am very unlikely to find a veneer that will closely match, so using a contrasting veneer would be best. I do like your walnut finish. That Black Bison Wax is expensive though I've just finished making the bushings to make the Hipshort Ultralites fit the neck. An easy 3D print even at 100% infill of about 10min each, nice and tight and the plastic won't deform (or at least I hope not, otherwise I'll have to do it in metal). 18.5mm external diameter and 16.75mm internal diameter. You can see two of them below. I've screwed the two Hipshots on to make sure they all fit. Now printing the last big piece of the guitar Relatively small at 22 hours Rob