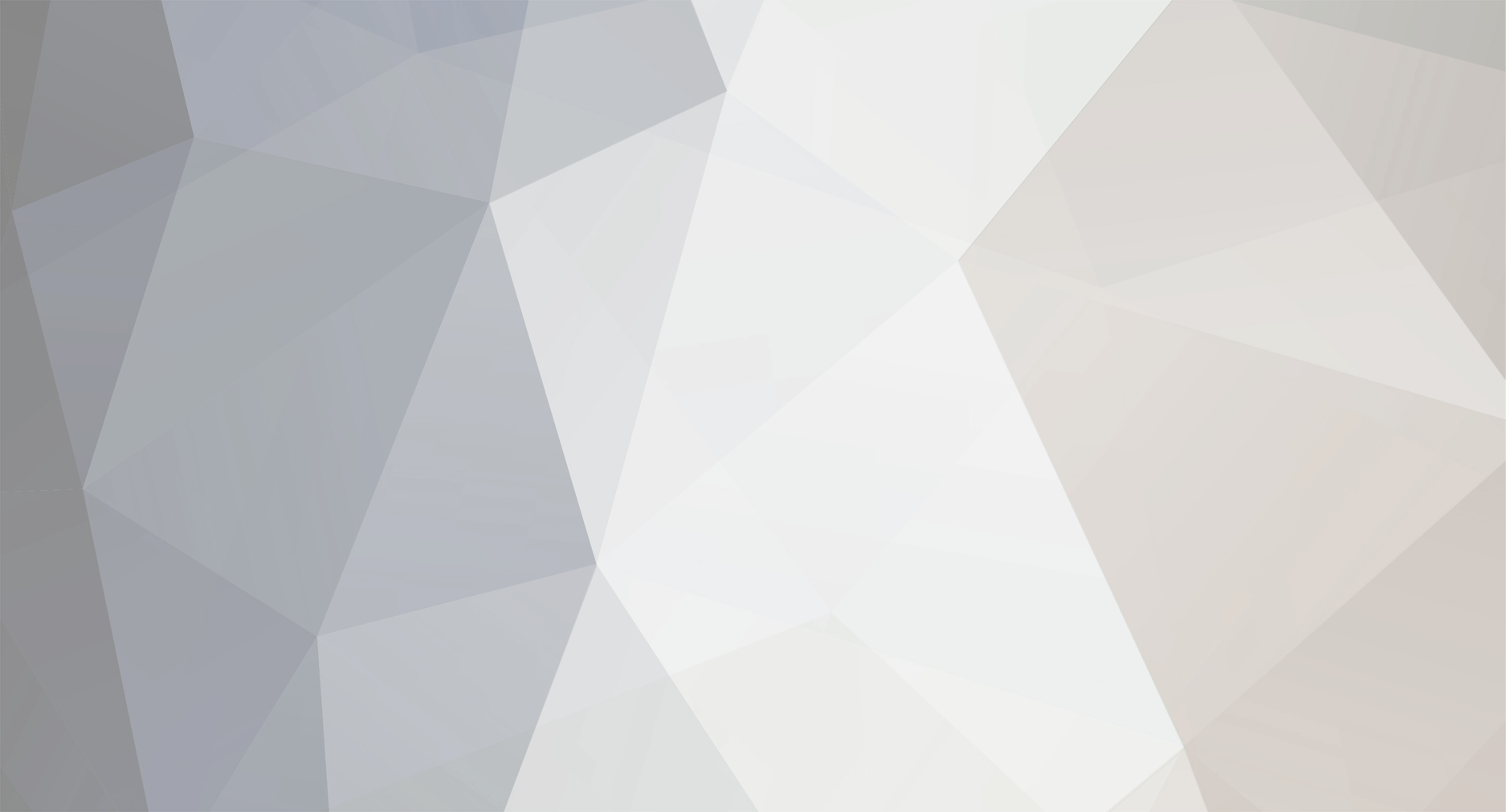
budget bassist
Member-
Posts
4,273 -
Joined
-
Last visited
Content Type
Profiles
Forums
Events
Shop
Articles
Everything posted by budget bassist
-
Sounds cool! You got a build thread for that? I really liked my old g&l tribute. Also Update: ordered a 3-piece slab of ash from Tonetech. Hoping to get machining the body next weekend.
-
Haha awesome. Download Google Sketchup and give it a go! The basic version is free, albeit slightly limited in use.
-
The polystyrene guitar body was finished being routed today, here are some photos. The next stage will be to get the stingray body routed in some sort of wood. [url="http://s4.photobucket.com/user/metallica_rock/media/IMG_1507.jpg.html"][/url] [url="http://s4.photobucket.com/user/metallica_rock/media/IMG_1508.jpg.html"][/url] [url="http://s4.photobucket.com/user/metallica_rock/media/IMG_1509.jpg.html"][/url]
-
I just spent the morning finishing off the Stingray body, making sure all the dimensions were correct, neatening it up and adding the stomach contour and control cavity route etc. Just rendered it, and I know the body shape is a little off, but I kind of like it! It's not going to have a pickguard by the way, and the control cavity, as you can see, is rear route. So it's not really a traditional stingray. In fact I'm tempted to have another fiddle with the body shape and make it more sterling-y. [attachment=170701:stingray 2.JPG] [attachment=170700:stingray.JPG] [attachment=170702:stingra back.JPG]
-
For sale is my perfect ten combo practice amp - 10" driver, 30W of power, 3 band EQ and sounds great for a little practice amp. There's an input for CD player etc., headphone out and cab extension. Good working condition. The pots were crackling a bit, however I've given it a good blast with some switch cleaner, and the problem [i]seems [/i]to have gone away. Just thought I would mention it. I'm after £50 collected from Bangor, North Wales. I may consider posting, but it's probably not worth the cost in all honesty.
-
Well I'd better keep reading into it then, and hopefully I'll come out with something half decent! To be honest, if I end up with something that sounds similar to my Ashdown kit but ends up a lot lighter, I'll be winning.
-
I appreciate the help, I know I'm not going to get it right straight away, and if that is the case, then I'll only have wasted some plywood and my own time. So no big deal really. I'll have a read of that link, I've been reading around, trying to get my head around the whole thing - I have a little knowledge of acoustics (and electromagnetics, which seems to cross over a little), the biggest hurdle to me is the terminology it seems! I'm not expecting to build anything amazing, but it's a decent little project to embark upon given the tools I have available. You might ask "why?". Well, why not? If what you're saying is true, then surely I can't do much worse than an ill-considered mass-manufactured box would be?
-
I have considered that, but as you said, half the satisfaction will come from having designed the thing myself! And fair enough, haha! Another question, does it matter where the driver is positioned on the front baffle? Does it need to be perfectly central, or can I move it around a little?
-
I have another question - I've been using WinISD and some other online speaker dimension calculators, and they're all throwing up rather large box sizes in order to get the optimum sound for a specific speaker, which I understand. But how are all the manufacturers using such tiny enclosures and still getting a good sound? I'd like my cab to be as small as possible really, I just don't understand how they're doing it.
-
That's the plan... Are you local?
-
I've had a bit of a google, and according to a number of sources, the best/easiest way to do it may simply be to use wooden doweling, I think I'll go with a combination of this and 12mm birch ply. This [i]should [/i]give me a fairly lightweight and good sounding cab, I think.
-
Thanks. Any tips for bracing?
-
Yeah it's a similar idea, I think hackspaces are typically more geared towards elecrtronics and programming etc. though a few are sort of linked together. The Bangor Pontio innovation centre will have a FabLab, hackspace and media lab, as well as some more high tech manufacturing kit elsewhere.
-
Warmoth Flame Maple jazz body - Sanded back black dye finish
budget bassist replied to Dolando's topic in Build Diaries
Hahaha, that looks good too What dye did you use by the way, and where from? Iwant to have a go at a dyed finish soon. Any tips? I have no idea where to start or even how it's applied. -
Got the whole of the back done! The guy at the fab lab says he'll flip it and get the front done on Tuesday. Next time will hopefully be wood, possibly the weekend after next. I may see if I can get some bits for a cab done next weekend.
-
Of sorts
-
More progress: [attachment=170470:image.jpg] The photo isn't great, but you can see it's doing the finishing pass here, it's basically doing diagonal lines across the body putting in the small details - have a look at the control cavity if you're struggling to see it. This is the long part!
-
To be honest, It's going to take hours whatever I do! I've got my laptop here and other things to do (plus coffee ) so it's no bother. 6-8 hours per side really isn't too bad when you think what I'm getting out of it!
-
Erm, yeah I suppose you could do it that way, and it's something that did cross my mind, but in all honesty, I just couldn't be bothered to change the CAD file.
-
To be honest, I'm not really sure. I've not had a proper play with the software - somebody else guided me through it pretty quickly. Perhaps when I get int it a little deeper i'll find some shortcuts
-
Pretty much, it takes a lot of passes as it only goes down 3mm each time, and you need to do a roughing pass (I'm using a 6mm bit) to get the basic shape cut, which takes a couple of hours, and then the finishing pass (using a 3mm bit here) which is going to take about four hours. To do the whole thing with a 3mm bit would take forever, and to use a 6mm for the whole thing would just end up with a crap finish, so you need to do two passes really. Then it needs flipping over and doing the other side. I'm not sure if there is anything I can do to get the time down a little though, that's something I need to look into. Obviously it helps to have the right thickness of material so that you're not just wasting time taking material off (This polystyrene is 5.5mm thicker than necessary so the first couple of passes on the other side will be just material removal). Cutting flat pieces of wood e.g. for my speaker cab is much faster, as it's far less detailed.
-
I'm currently sat watching the router go over the roughing pass of the guitar body in polystyrene. I was going to try the bass, but there are some slight issues with the CAD file that need sorting, but I have plenty of polystyrene to do that at a later date. It's a long old process, so it's going to take around 6 hours just to do the rear of the thing - the front may be a little quicker, but I won't get it done today. Anyway, here's a photo.
-
Having spent a good while using WinISD to work out dimensions and porting etc. I've knocked this up in sketchup to get an idea. Still need to work out what I'm going to do in terms of internal bracing (any recommended reading?), but it's looking okay thus far. I decided to go with rabbet joints in the end, as I remembered half way through designing the enclosure with box joints that a router won't cut the internal corners properly. Shame, because it would have looked good. [attachment=170444:bass cab 2.jpg]
-
Haha yep, there is one in manchester - near enough identical, but the manchester one has embroidery machines. They're awesome for prototyping - they have business rates too, but the public days are thursday-saturday. The world is your oyster One lad in the ellesmere port fablab had made himself a daft punk mask for his band, looked really good! Did CAD in sketchup, then CNC'd it in wax, cast a silicone mould over it, and then cast it in plastic (the fablab has casting/moulding equipment too). So cool!
-
I should add - I do hope to do a neck and fretboard at some point too, but I think it will be a little more complex to design, and will take a lot more work and specialist tools to finish (frets etc.).