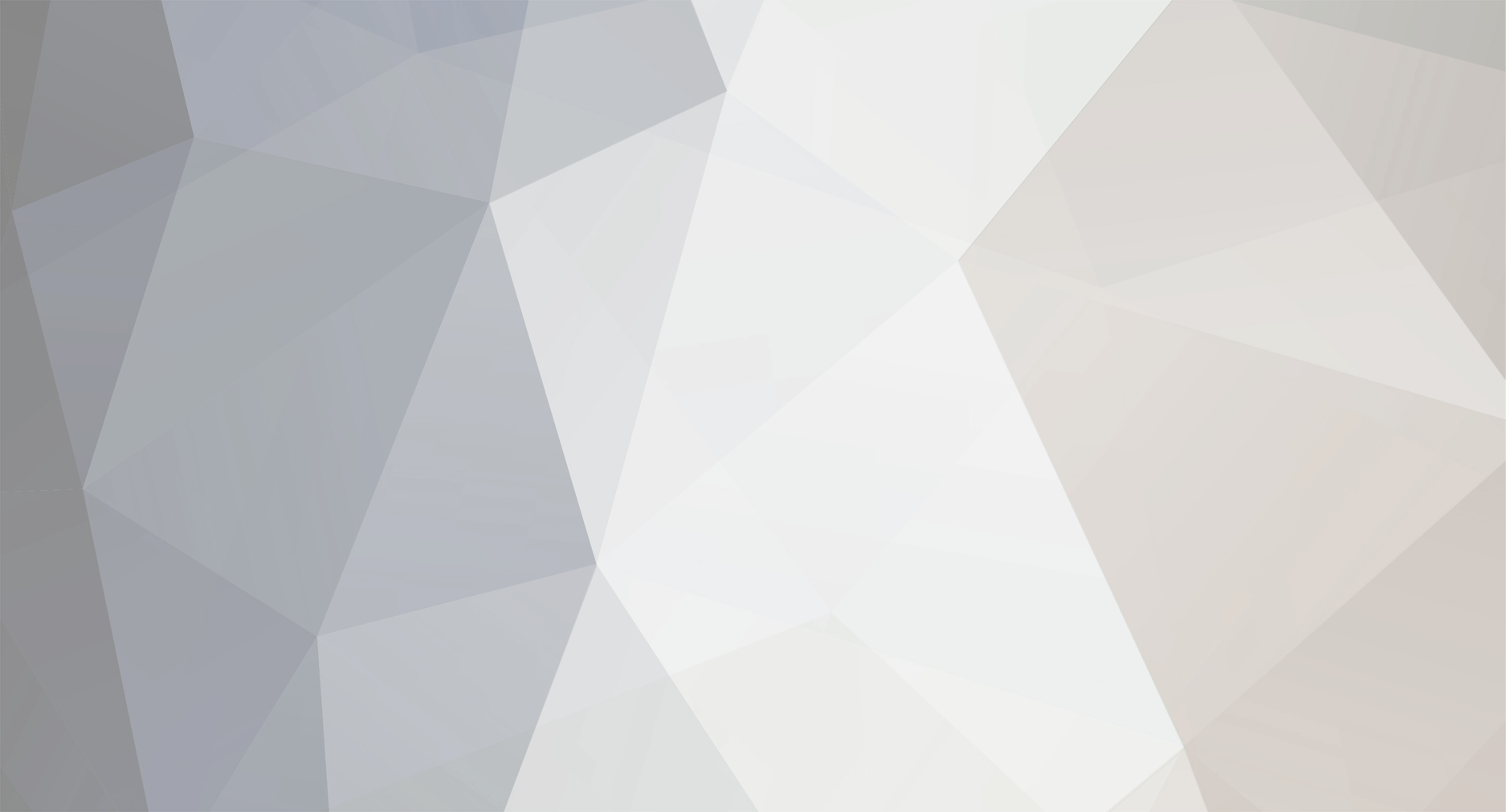
B.Flat
-
Posts
226 -
Joined
-
Last visited
Content Type
Profiles
Forums
Events
Shop
Articles
Posts posted by B.Flat
-
-
OK, thanks itu and LukeFRC for your replies.
First problem is I do not fully understand electronics but can solder etc. from a laymans diagram.
Secondly I have a Lakland preamp and controls in bits, which I want to get functional but I need the simpletons diagram, with colour coded wires if poss, to be able to do this.
So, it iis the original Lakland loom with MM & J Bartos, coil tap, mid F switch, output preset, B,M & T tone; Vol/bal and push/pull passive.
-
I have been here already but I cannot find a diagram of the Lakland loom
-
It might be the onset of "oldtimers disease" but I have trawled the net to find a Bartolini wiring diagram for the Lakland 4-94, without success.
Can anyone advise ? It is the NTMB-L preamp with coil tap and mid switch (internal).
-
That is really great, BB, it looks foolproof to me, and I am greatly indebted to you. Thank you very much !!
-
16 minutes ago, BassBunny said:
I'll see if I can update the diagram tomorrow. The passive element isn't wired between any part of the existing pre-amp. It's an additional control.
Hi, OK I am grateful for any help you can give me but only when you have time to do it.
Thank you
-
Well, Bassbunny, the bass and treble pots are 100K linear, but the rest is a bit unclear for me. Are you saying the best would be to get a 250k dual pot and wire it between the existing volume pot and the preamp ? If yes how would I do that. Is there any chance you could draw it on the circuit I included in my last post and post it back ? It is important that the passive tone works in both passive and active mode.
With regard to the active bass and treble I would obtain an MEC dual concentric 100k linear pot and copy thye connections on the diagram
-
OK ,BassBunny noted, I will investigate.
However, since I posted I have thought that maybe all I need to do is stack the bass/treble pots and wire in a passive tone before the preamp. Having said that, I have no idea how to wwire it. Can anybody out there help with a laymans diagram I could follow ?
-
I would be grateful to hear opinions on four-hole commercial preamps to be used in a P/J set-up.
I understand pickup choice is an important element of this, so pickup advice also if poss.
Question arises fro wanting to mod a '95 Warick Fortess One. The existing Warwick is OK but the Sadowsky, with passive tone control, beckons.
9 or 18 volt OK, I can modify the battery accomodation.
-
I'll see what I can do, but don't hold your breath !
-
Hi again Bill.
From the heart of France, thank you again. You have been most helpful.
I will suggest to President Macron you should be reccommended for the Légion D'Honour !
Brian
-
Hi again Bill,
I forgot to ask if a variable attenuator can be added to the circuit ?
If yes, could you please advise me.
Brian
-
Thanks Bill,
exactly the clear advice I was looking for, I am indebted.
Brian
-
Hi.
So, I have a 2 X 10" cab (which is really two 1 X 10's", as the internal space is divided) to which I would like to add a high frequency driver.
The advice I am looking for is, which driver (the 10" are Deltalite 2510's) which needs to be as small as possible as space on the baffle is tight, and which x-over (off the peg if possible but would build one if not too difficult). Is the tuning of the cab important regarding this x-over ?
The cab is driven by one side of a Yamaha PX 3 power amp, 500w at 4ohms
-
I have had a message from H.P.Wilfer to say that the side tags (indicated) need to be cut off and that there are some tags on the inside also that need to be removed for easier battery replacement.
So, question answered, and it may be of interest to anyone trying to add a Warwick battery box to an instrument.
-
2 hours ago, BassBunny said:
If it's similar to one of the Gotoh ones, there are small screws used in the bottom of the casing. You need to remove the hinged battery carrier to access them.
The other Gotoh one has 4 external screws.
I've a brand new Gotoh one I bought and never used so I'll have a quick look.
Are you sure about this BassBunny ?
If you look at the photo at https://shop.warwick.de/en/parts-for-instruments/warwick-spare-parts/pickguards-covers/21524/warwick-parts-battery-compartment-for-2-x-9v-block-battery?c=3591 the lid is not the hinged variety, you will also see the side tags I mentioned.
Tell me what you think.
-
Anyone out there with experience ofthe Warwick dual 9v battery box ?
I want to fit one to my Fortress, that is why my first choice is the Warwick box, but looking at it on the sites of variuous suppliers I am not sure how it is supposed to be fitted.
there appear to be some kind of friction/pressure tags on the side of it but I cannot decide what routing will be required. Any words of wisdom would be helpful !
-
I am re-thinking this.
I have been spoilt by the neck on my Vigier Passion ii carbon, which though I did not take to immediately, I now think is probably the most comfortable neck (and bass) I have owned in sisxty years (you were right Ped!).
I can't make the Warwick the same profile etc. but after some very careful adjustments it is not uncomfortable, and I think it is better to leave it alone as it is in unbelievable original condition for its 25 years.
The preamp mod I have now configured so that it is completely reversible.
Time to get back to actual notes and music and avoid the rabbit hole of "perfection". Just further to the topic of comfortable instruments, the openening pages of "Bird Lives" by Ross Russell about Charlie Parkers' alto sax puts it all in perspective !
-
4 hours ago, HazBeen said:
The neck finish I understand is a mix of melted wax and lemon oil. These are readily available and it should therefore not be an issue to redo the neck after thinning.
And indeed, different grits and steel wool.
Wrt how much you can reduce depends on several factors and I would take it slow. You can always reduce more, never less.
Do you have a picture if the neck? If it is a 1995 I imagine this is the rather large slide in trussrod, which actually limits how much you can thin the neck quite a bit. A couple mm max.
Thanks for the replies.
Yes, HazBeen, it is the slide-in trussrod. I have never seen one out of the neck, I did not realise it was bigger than the two-way.
-
Hello again.
Further to the re-furbishment of my Warwick Fortress One, 1995, (subject of a previous thread for preamp upgrade) I am hoping for advice on the possibility of reducing the front-to-back thickness of the neck.
I would be interested to hear how much wood people think, if any, could be removed without compromising the structural integrity of the neck, and possible ways of deciding this. A luthier once told me there was a way to decide how much wood was underneath the trussrod by using a magnet and shims, anyone else know about this ?
Also, assuming I go ahead with this, would reducing grades of sandpaper followed by reducing grades of steel wool reproduce the existing finish on the wenge neck ?
Answers on a postcard, the winner will be drawn at mid-day.............Brian
-
4 hours ago, A.G.E.N.T.E. said:
Can´t be shure about your`s , but both my 93 thumb Bo and the 96 streamer BO, had the alloy version. Anyway, you can tell one from another by the casting marks of the alloy version.
Thank you, that answers it, I have those marks so it must be cast. The only thing that made me query was its weight. On the Warwick site the brass version is shown to weigh 0.15Kgs, and mine just the bridge, without the base plate, weighs 0.156kgs. Must be a heavy alloy !
-
Can anyone tell me what material the 3D bridge on a '95 Warwaick Fortress One would be made of ?
Was it alloy or brass or what ?
-
Hi Hazbeen.
Yes that is what I thought you intended and I think probably the best solution so far.
Brian
-
1
-
-
8 hours ago, HazBeen said:
Basically you need to carve out the cavity. I would use my Dremel with 45 degree angle attachment and a fine router bit.
https://www.dremel.com/en_US/products/-/show-product/tools/575-right-angle-attachment
I have used it in very tight spaces effectively. What you cannot get around though is the fact that the original barrel jack hole is larger than the 1/4” jack threaded bit and will leave a gap if you do not use a jack plate.
I would probably sacrifice the barrel jack, in essence using the external flange of the barrel jack as my new jack plate. If you make the cavity just right (As I believe the 9 pole one is squarish) you should be able to pull the jack plate tight to the wood with the screw on the new jack, and not worry about it turning. And you can also drill 2 small holes for screwing it to the body.
Then should you sell it, you can just but a barrel jack back in place and the outside will look as before/original.
I hope I am making sense.
Hi Hazbeen.
This is sounding interesting but my elderly brain is having difficulty visualiising.
Do you mean cut the end off the barrel jack and thread it internally to match the thread on the 9 pole socket ?
At this time I do not know the relative diameters ( internal and external) of the two sockets. Maybe you can enlighten me !
-
56 minutes ago, Acebassmusic said:
For me I would make a hole of the correct size and use a metal jack plate recessed into the side of the bass. The metal plate will give you a much sturdier socket than removing wood from the inside of the cavity and then attaching the jack to whatever wood is left (2 - 3mm?)
Yes, this is my only idea. I did not elaborate on the wood plug idea but that is what I thought, a metal plate recessed and a wood plug, of the correct maple and grain direction, glued to the plate and radiused to match the body contour. Only prob. is that it would be noticable. I am not OCD but before commiting to doing that I was interestested to see if anyone had a better idea, as I am afraid I am not as inventive as I used to be !
-
1
-
Advice on drop-fill carbon neck
in Repairs and Technical
Posted
I have a carbon neck with a chip, which I think I can drop-fill myself with a bit of advice from someone who has this experience.
The questionh is what to use. The manufacturer of the bass says polyester will be OK, but the polyester I have in stock is amber-coloured, not clear.
I have tried a spot of EVERBUILD MITREFAST (with accelerator) which seems clear enough, but I do not know if it will adhere to the carbon and polish up correctly.
All advice on materials and method gratefully received. I have watched several Youtubes of drop-fill, but they are all on flat surfaces, and also I do not want the finished job to look wirse than it is now, as the playability is unaffected by the chip.