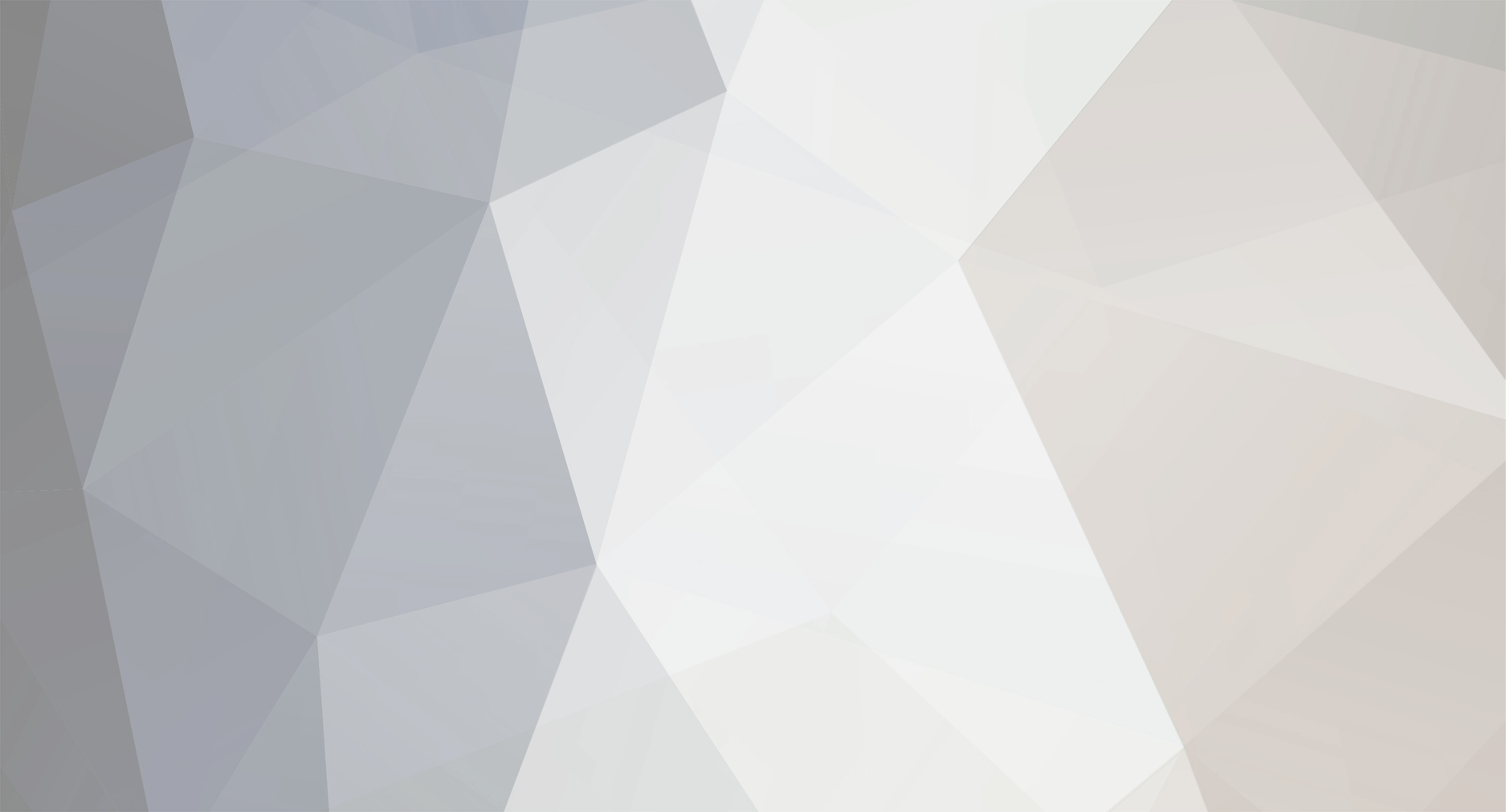
rmorris
-
Posts
1,302 -
Joined
-
Last visited
Content Type
Profiles
Forums
Events
Shop
Articles
Posts posted by rmorris
-
-
2 hours ago, shoulderpet said:
Ok thanks, I assume also that soldering a capacitor to the copper tape should also be fine?
Another thing that I have just thought of is that most of the time there is a ground wire soldered from the back of the tone pot to the underneath of the bridge, could I instead have the ground wire that would usually go to the back of the pot to the bridge wired from the output jack to the bridge?
Yes (to the 0V connection (screen) of course.
Be careful not to connect to the Ring Connection by mistake.
-
For the Copper Tape solution you first need to be certain that the adhesive is conductive. Some types are and some aren't.
Soldering the wire to the tape should be fine. The possible problem you may have is a secure adhesive connection.
Do key the pot casing to remove any coating / grease etc. But you'll still have a relatively small flat surface to fix the tape.
Really 'squeegee' it down.
I'd advise soldering the connection myself. Use a good sized. preferably temperature controlled iron.
If it's a configuration where you are attaching one of the pot lugs to the casing to ground it - then bend the lug over to solder that. Then the wire can be more easily soldered to the lug using the hole in it to keep the wire in place.
-
12 minutes ago, Chienmortbb said:
I have made hundreds (maybe thousands) of cables over the years and in most situations, the standard quality cables from Sommer* and Klotz** are my choice. There are a number of reasons but the main ones are:
- Better bend radius. The cables...
Thanks for posting sensible advice on this topic.
And to be clear about the conductivity (or resistance) of copper vs silver:
It's not an issue. It doesn't matter. (because it's insignificant in the context of your output and input impedances).
Mechanical integrity is key - basically your connector joints and cable relief. And cable capacitance makes a difference.
Minimise unbalanced / Hi-Z cable runs.
-
2
-
On 28/02/2022 at 06:02, Marvin said:
The Sire preamp has a 'baked in' sound, I'd like something that's maybe a bit flatter or neutral.
Is that compared to running the bass passive ?
-
10 hours ago, Boodang said:
As these cables are low capacitance and as my main gigs are more jazz orientated where I'm sitting down, I'm going to use them live as well as the studio as it's not exactly a harsh environment (although I'll use my normal cables for the Sex Pistols tribute band gigs I think!). The biggest damage will probably be to the braiding from the coiling/uncoiling but I'm sure they are not that delicate.
After all the only way to really preserve them would be to not use them.
Wrt braiding / shielding. The 'delicacy' really depends on the construction. There are all sorts of tradeoffs with construction vs frequency vs flexing.
But basically braided if static. Spiral (preferably Double Reussen) if flexed.
Apart from that. Best thoughts to anyone reading this in these worrying times.
-
4 hours ago, Dan Dare said:
Not necessarily. Cable made from many finer strands will be more flexible and less likely to fatigue from constant flexing than that made from fewer strands of a thicker gauge. That's why solid core cable is intended for fixed/static use.
True. I was assuming a signal conductor made from multiple fine strands. Although the most critical point of failure is where it is terminated to the connector and there should be minimal flexing at that point.
-
43 minutes ago, Dan Dare said:
Silver is a marginally better conductor than copper, although I can't hear the difference. It may be noticeable in a quiet studio environment, but not in a live situation. Silver isn't nearly as good at coping with flexing/bending and general abuse, however. That makes it a bit fragile for use as a stage cable, being trodden on, coiled and uncoiled constantly, etc.
There is no real advantage in having a signal conductor that has slightly better conductivity than copper. The electrical characteristics that matter are capacitance and screening. Mechanical integrity is also key. The advantage of having a decent sized conductor guage is to avoid it breaking.
-
On 25/02/2022 at 13:03, Jean-Luc Pickguard said:
I used copper slug tape from amazon.co.uk to shield my squier jaguar shortscale and can confirm that no slugs have been found in or near the bass since.
Seems I got it wrong then. I used it to tape slugs to my bass. It's s bit slimy now 😳
-
31 minutes ago, Rayman said:
Slug tape ordered. It’s just odd that 4 other basses don’t make a sound, and I’m pretty sure two of them are also unsheilded.
Different electronics can easily have differing susceptibility to interference.
wrt the pickups - yes they can make a big difference - type / construction / resistance / inductance all relevant.
And pot / cap values and the wiring. Larger pot values will be more easily affected.
It's still advisable to shield the other basses. Even though you may not hear interference through whatever setup you are using it may show up in a different system (typically one with more high frequency response eg cab with tweeters or in a studio environment.
Also, they may be shielded with conductive paint ? - It usually black. imo not as good as metal but can be effective if properly applied.
Hope you get it sorted.
-
1
-
-
2 hours ago, NancyJohnson said:
The idea of the shielding is to stop/reduce interference from outside sources (dimmer switches/electronic anomalies); the slug tape alternative was suggested to me by John East. I'm not certain that it's necessary to connect the strips together; any adhesive overlap should have sufficient conductive properties to create a sealed enclosure, plus the pots will also be in contact with it as well.
This is the first time I've ever seen the words conductive and glue in the same sentence!
Conductive adhesive on the tape is definitely needed unless seams are made by solder or pressure. If the "slug tape" adhesive is reasonably conductive then fine but if it's not it will not shield effectively. And there is definitely adhesive copper tape that has non-conductive adhesive. It's a source of frustration / amusement in the world of EMC testing when a "non-technical" customer doesn't understand why they are having problems despite wrapping stuff with copper tape.
Test with DMM shows it's not electrically connected as it has non-conductive adhesive.
And put good pressure on the adhesive join to get a good connection.
(You generally need to rely on pressure for screening 'detatchable' bits eg control cavity covers / scratchplates.
Connecting scratchplates / pickguards to the screen will also help avoid 'static' noises caused by rubbing the scratchplate / screws.
-
Have you considered half round / ground wound / pressure wound string options ?
-
23 hours ago, SH73 said:
If anyone reads this thread, where are the places to get spare electronic parts, capacitors, PCB etc. E bay takes a long time...thanks
CPC (part of Farnell but prices often cheaper with free delivery over £17 I think atm).
Ebay sellers can be quick if UK stock.
-
1
-
-
are the cavities screened ?
-
1
-
-
On 16/02/2022 at 22:43, benebass said:
Hopefully won't be an expensive fix, but still a bit miffed the seller washed their hands on this one - not the most disastrous deal I've ever had, but not great & thankfully not typical of people on here...
Cheers! 😁👍
tbf U don't think anyone checks for corroded screws before selling a bass ? Use stainless steel screws for replacement.
-
1
-
-
On 14/02/2022 at 12:06, BassAdder27 said:
I’m seriously thinking if I really need to use an outboard compressor pedal and my Boss TU3
I am liking the fact it keeps my signal in check on my ABM600 but perhaps if I turn down the input slightly I can ignore the use of a compressor ( acting more as a limiter ) and as I tune up typically twice per session with the band ditch the tuner and use a clip on when not playing ( start of set )
I would still use my Line 6 G30 wireless which I really.
Just a thought do I really need the compressor at all ?
I never slap and play finger style for mostly rock
Anything else in the signal path ?
-
Start with the original pickup. You can always change it later.
-
Questions not Judgements - but is it really worth the time/expense/risk to DIY fretwork if it's just going to be a one or two off ?
You're going to need serious tools - straight edges / clamps / files etc and patience.
I'd suggest that, if serious, a hands on in person tutored course is the preferred route.
-
15 minutes ago, verb said:
I emailed Clive a few years ago, he was very helpful, he even gave me the part number for the Series 6 EQ slider pots from memory. He also told me that he had binned all his TE drawings when he retired.
thanks for the info'. And I won't hold breath on getting a schematic from Mr Button then !
Still - he has quite a legacy with Trace, Ashdown and more...
Maybe 'we' (not that I'm an admin here) should grant him some sort of honorary Basschat title ?
-
1
-
-
18 hours ago, fleabag said:
You could do worse than try emailing Clive Button who was the sole designer, from Series 6 on, TE bass amps/ combos and acoustic combos plus a host of other TE gear for the next 12 years from 1985
Bass - Series 6 range, SMX range, SMC range, 7 Band range, 12 Band range, GP7 Pre-Amp, GP12 Pre-Amp, AH150, AH200, AH300, AH350, AH500, AH1000-12, Valve Series, VA350, VA400, VR400, Twin, Quatra, Hexa, Commando range, Boxer range, PPA power amplifiers, Powered Sub 15, Bass effects pedal range, MP11 etc:
Acoustic - TA100R, TA50R, TA200R, TA Concert range, TA60, TA35, TA30, Acoustic Cube, TAB100 (Acoustic Bass), Acoustic PA 16 channel powered mixer system, Acoustic PA 12 channel powered mixer system, TAP1 acoustic pre-amp pedal, in fact everything that came out of Trace Elliot all the way through to 1997
I dont know whether he's still active, but i had an email chat with him some 8 or 9 years ago about my series 5 4x10 combo, but as he told me, he didnt design the series 5, but was helpful nonetheless
Thanks. Yes - I'm aware of Clive and his TE history and more.
I emailed him just after I posted here.
And, fantastically, someone on here posted me a partial schematic scan shortly after I posted.
-
1
-
-
Bit of a long shot - but does anyone have a schematic of a very early (1987 I think) Trace Elliot GP7 MK2 Amp Head.
The later GP7 SMX circuit is easy to find. But I've had mine apart earlier today trying to diagnose a longstanding cut out / fade out issue and the signal path is clearly significantly different.
Sounds great when plugged into a Marshall Jubilee 4x10 so would like to fix the issue.
Thanks.
-
9 hours ago, Supernaut said:
I think I know the answer but wanted to check...
My nut is cut for 45-105 gauge strings.
Would changing gauge to 40-100 mean I would have to recut the nut?
Thanks.
Good question. It doesn't seem to register as a problem generally.
I reckon that going lighter the difference in possible movement is minimal.
Going heavier might be an issue if the string becomes too tight in the slot and doesn't sit correctly.
Would be interesting to hear the views of the more expert here.
-
From the OP's post he mentions Australia so not very near Somerset !
I'd suggest find out what's (not) going on with the DI first before getting into power amp territory.
As you say, that should be independent of the power stage (but never say never...)
-
10 hours ago, Waddycall said:
I really dislike colour matched headstocks and my highly customised Ray34 has one (black). How feasible is it to strip the paint and refinish clear with a new set of decals ? I’m pretty good with sandpaper but wonder how deep into the grain the black paint might go?
tbh I'd likely 'work on' overcoming a dislike of colour matched headstocks.
After all, you can't really see it when you're playing 😀
of course YMMV.
It should work out fine to strip I think.
I'd normally caution that it will affect resale value potential - but since you state that it's highly customised that may not be relevant.
-
2 hours ago, paul_5 said:
500k volume pots will give you a brighter sound, but won’t make your bass any louder.
what I’ve seen done to supercharge passive pickups is to place s bar magnet underneath the pickup, so that it increases the magnetic field.
Higher Value pots' will actually increase the signal level (it's simply electronics/maths) - but yeah, not the sort of difference that I take the OP to be talking about - more significant to tonal balance and sustain. That's why I suggest bypassing all the vol/tone stuff to hear what the pickup alone is doing. In case the problem - if there is one - is related to the pots' / cap / wiring.
Alternative methods to solder to back of pot can these work?
in Repairs and Technical
Posted
Well I was being rather brief so no problem.
This really applies only to active basses that use a 'stereo' jack for the output and the screen connection of a mono jack plug is used to join the 'Ring' conductor to 'Screen' to complete the power circuit - hence the usual advice to unplug when not used inn order to avoid running batteries down quickly. So I'm just advising to wire to the 'Screen' connection on the output jack and not the 'Ring' connection.
For clarity - 'Stereo' or 'Balanced' jack connections are referred to as "TRS" jacks.
T = Tip (Signal +ve)
R = Ring (next 'band' on the plug - Signal -ve for balanced audio; other channel for stereo)
S = Screen
To add to the fun also often used as combined Send/Return connector for unbalanced Insert points on mixers.