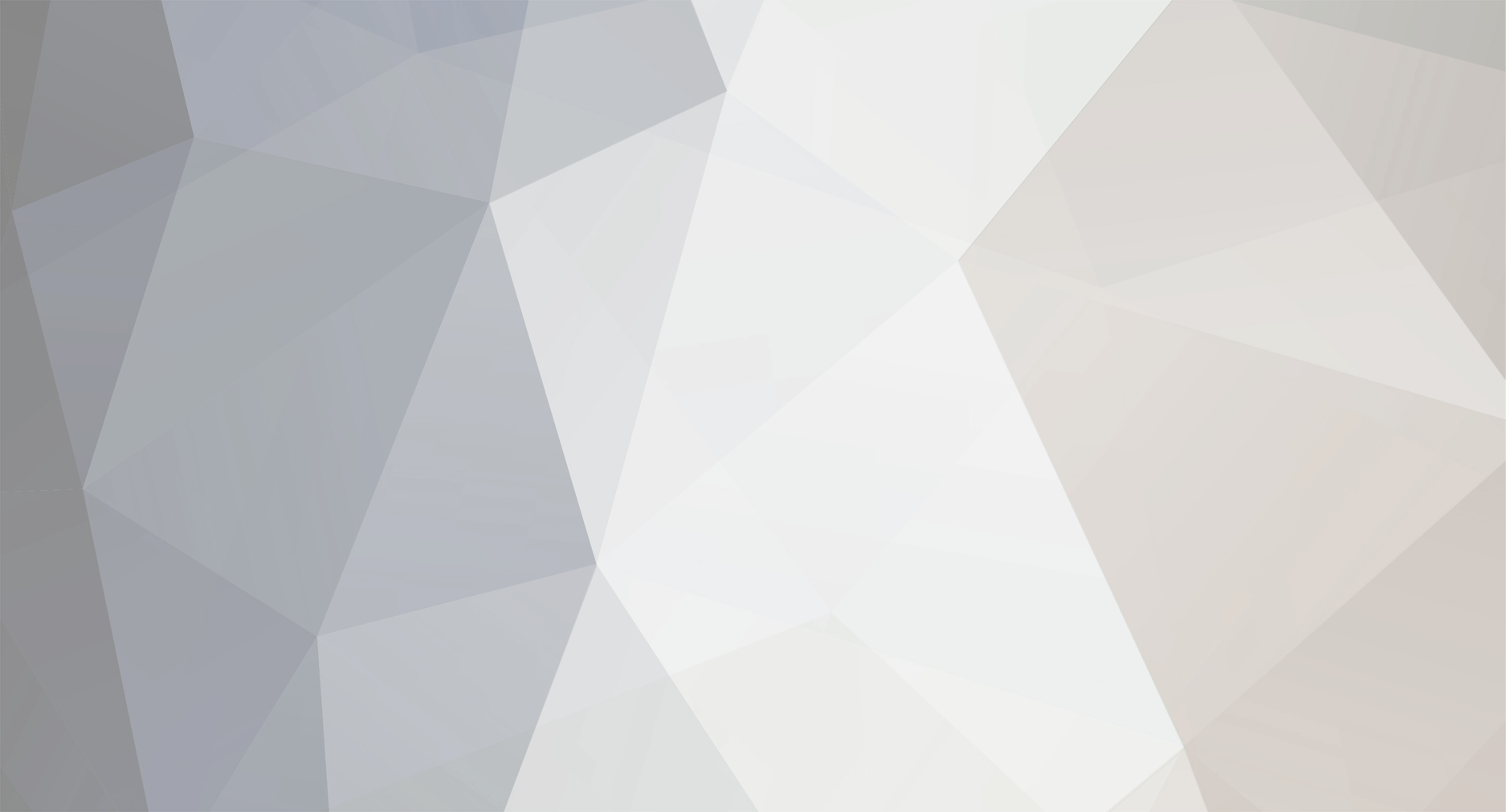
dadagoboi
Member-
Posts
44 -
Joined
-
Last visited
Content Type
Profiles
Forums
Events
Shop
Articles
Everything posted by dadagoboi
-
Metal Work 101, prototype to production. Steve Soar of ThunderBucker Ranch who makes most of the pickups I use is also collaborates on my bridges and tail pieces. Clockwise from bottom left: Prototo tailpiece from aluminium stock, ThunderBucker supplied nickel silver blank, drilled and polished, NS bridge channel with .020 AL insert. Assembly begins.
-
Polaris White, '60s Gibson custom color: pure white nitro lacquer plus yellow and burnt sienna pigment. One coat Polaris White and two double coats Mohawk Piano Lacquer clear. Polaris White '64 Thunderbird, refinned about 8 years ago in the background.
-
Whatever works! Yesterday's Technology Tomorrow is my creed. "Ebonised' Jatoba. Thoroughly clean fretboard with denatured alcohol. Carefully apply three coats of alcohol based leather dye (USA brand I use is Fiebings) about 5 minutes apart. Let dry overnight and rub with a rough cloth to remove any excess pigment on the surface. Darken dots with Sharpie. 3mm 'Geezer Dots' (1/8" plastruct.rod) My spraygun setup, LVLP using $20 USD siphon guns and 1 pint screw top mason jars. Allows for quick cleaning and no wastage of leftover lacquer. As well as no surprises in the middle of a coat. I use about 25 PSI at the gun maximum for most lacquer base, mid, and top coats . Light 320 grit dry scuff sanding between paint steps only when necessary. Two coats of pure white nitro, about 15 minutes apart. 'Flash Off' flow out solvent, 'No Blush'' additive, and slow thinner makes nitro behave when temp and humidity are this high in the swamp. Better Living Through Chemistry!
-
Thanks!. Every bass I build gets assembled at least once before it's time for finishing, even then there are surprises. It's like I get a new bass about every six weeks or so for a tryout, then it flies away. Quite a few flaws need to be addressed and body has to be recontoured slightly in the heel and lower horn area. jack mounting hole is damaged, three point bridge and scratchplate holes have to be filled, etc. Plastruct rod, superglue, chisel for cutoff take care of small holes. Durham's RocK Hard Water Putty does the 3 point and original neck screw holes. Sheet balsa is glued into the deep part of the neck pocket and planed flat. Neck pocket taped, poly finish block sanded to 240, spot primed, and final sanded with 320. Standard Cataldo six bolt neck pattern drilled and counterbored for ferrules. Neck is moved into the body quite a bit more than the standard Epi neck location. Those small fills are the BACK neck screws on the stock body. Next, NIitro.
-
This bass is a prototype and a chance to do some minor house cleaning. My TBird style designs are based on Peter Cook's work with John Entwistle. The ONLY FenderBird (JAE's spelling). The Gibson original body shape was slightly modded to make it compact enough to fit in a Precision sized case when mated with a Fender neck. This is my workhorse, a 35 year old overarm pin router, bought used in 2010 for $700 and a 900 mile round trip to North Carolina. Pedal actuates the hydraulics that lower the pin while simultaneously raising the cutter. Safe as milk. With it and shop made mdf templates plus some other bench and hand tools I can make consistent pickup, neck pocket, and control cavity routes with the aged 15 amp Bosch router (110 volt). This bass doesn't get one of my scratch built bodies. Instead I'm using a Korean made bolt on Epi body from a bass I bought mainly to get a TBird case for one of my Gibsons. Prototypes for me are basically proof of concept before doing production templates. I'll just give this one a respray. Wider, shallower neck pocket routed, masking tape to draw critical measurements for bridge and tailpiece. Then, semi-instant gratification before the real work begins.
-
Thanks for the warm welcome, guys!
-
I did a quick search and could only come up with 22 for their bass necks. Warmoth has an optional 24 fret overhang board on Fender heel necks that can be cut back to 22.. I was going to do that for a customer who then decided to keep the full 24. It's a $25 option on a minimum $200 USD custom neck, though.
-
Most Ibanez basses, even the GIO series have 22 fret necks. They're well made, although the headstocks are ugly IMO. Cheap enough second hand to buy one just for the neck, tuners, and odd bits.
-
Hi Andy, Cataldo is my first name and I use it for bass builds. Glad you like my work, thanks!
-
Thanks, no clips. I will say that the original is almost a clone of my '55 Precision in neck specs (baseball bat profile and 1-3/4" at the nut) unlike the Crucianellis, and the pickups more muscular as well. I used a pair of chopped Duncan quarter pounder 51SCs with scratch built covers on the clone. They're close in sound except the clone switch is a blend pot allowing both pickups to be used together Both basses weigh the same, around 8 lbs and don't neck dive, also unlike the Italian versions. I do know the current Triumph story but I've moved on to Ducatis...actually I've quit riding though I still have the bikes and licence. Currently driving a twin turbo 350z but looking to downsize to a restored Series 4 Alfa Spider and take it on a west coast road trip. I first did that in '76 in a '60 'frogeye' Sprite built with parts from four donor cars. New fangled machinery doesn't leave much the owner can DIY.
-
Stratobasster! Daphne Blue, Squier Strat hardtail body, SX modded reverse headstock 32" neck. Stock pickups/electronics, scratch plate graft. .010 aluminium pole piece covers. Sound s better than it should.
-
I'm Carlo, currently living in a Florida swamp by way of NYC and more recently China. I've been playing bass since 1962 and started building basses in earnest in 2010 after exiting furniture design and returning from Asia. I had quit playing in the early 80s, keeping only a 1960 EBO and a '77 StingRay. Picked it up again around 2002 and have since acquired too many basses. Here's my 1965 UK Vox Phantom and one of the clones I built a few years back. I owned a Crucianelli Vox version in the early '70s. Sad to say, it didn't hold a candle to the original. I've also owned a number of British sports cars and Triumph motorcycles which definitely were instrumental in forming a DIY attitude!
-
Started with a Schaller 471-8 Functionally great, but a little overdesigned, e.g. the gronky coarse adjustment is aesthetically challenged compared to a TOM solution. Unnecessary if the saddle carriers are properly located. Four saddle (12 string ) prototype using pieces from my standard 4 string bridge/tailpiece and some .020 aluminium in situ with prototo (misdrilled) tailpiece. Then it got ugly... more Al, more butchered bridge parts and Francis, the Talking Mule. Essential for developing my 5s, 8s, 12s, and now, 10-15s. Only way to find out what pickup sounds how where. In this case ThunderBucker Fiver pups. Also helps in finding balance points and strap button locations. Now with TrembleNO™, the aspirational whanger system. Amazing what odd bits you can find in a drawer to screw into an untapped hole in .020 Next: Bring up the Body.
-
Belle du Jour Allparts second swamp ash body, Fneder CIJ P neck, DiMarzios, BadAss. Iced Blonde wash, satin nitro top coat.
-
Extensions attached and planed flat Waiting for the clampdown. 1/32" 3 ply veneer each side fully baked 10 and 12 string headstocks rough cut, drilled, and filled.. Tenner fretboard is Jatoba, 12er, genuine ebony
-
Comin' right up! I've been a BassChat member for a while but haven't posted much. I'm not aware of the rules for 'commercial users'. But here's a link if it's OK with the mods. CURRENT CATALDO It covers a lot of builds. Please Remove If Inappropriate.
-
I've built a number of 8 and 12 string basses, building a Tenner was always intriguing. The stumbling blocks have been the neck and bridge. Neck: I stumbled across 34" six string dual trussrod Ibanez and that got the juices flowing. Donor: Doweled the original headstock holes and commenced the headstocectomy.
-
[quote name='FlatEric' timestamp='1384622581' post='2278884'] Hi. Your first post on here - I know you through the Peter Cook thing I did. Welcome. I know it's a bit off topic (the connection) but the bass looks great in these shots. Nice. Cheers. [/quote] Thanks, Eric, your PC article was a big inspiration for me! I caught the Status bug while refurbing the Buzzard, it plays and sounds incredible. Here's my Jonas Hellborg Signature. [URL=http://s976.photobucket.com/user/cata1d0/media/Buzzard/P1050032_zpsc6d1bfb8.jpg.html][IMG]http://i976.photobucket.com/albums/ae241/cata1d0/Buzzard/P1050032_zpsc6d1bfb8.jpg[/IMG][/URL]
-
Here's a refurb I did on a '97 Buzzard. Dakota Red, gold, Switchcraft output jack with repaired/reinforced area where original jack had broken thru body. Before: [URL=http://s976.photobucket.com/user/cata1d0/media/Buzzard/P1040791_zps9af797c2.jpg.html][IMG]http://i976.photobucket.com/albums/ae241/cata1d0/Buzzard/P1040791_zps9af797c2.jpg[/IMG][/URL] After: [URL=http://s976.photobucket.com/user/cata1d0/media/Buzzard/P1040970_zpsb2db89f1.jpg.html][IMG]http://i976.photobucket.com/albums/ae241/cata1d0/Buzzard/P1040970_zpsb2db89f1.jpg[/IMG][/URL] [URL=http://s976.photobucket.com/user/cata1d0/media/Buzzard/P1040968_zps0fb5c1be.jpg.html][IMG]http://i976.photobucket.com/albums/ae241/cata1d0/Buzzard/P1040968_zps0fb5c1be.jpg[/IMG][/URL]