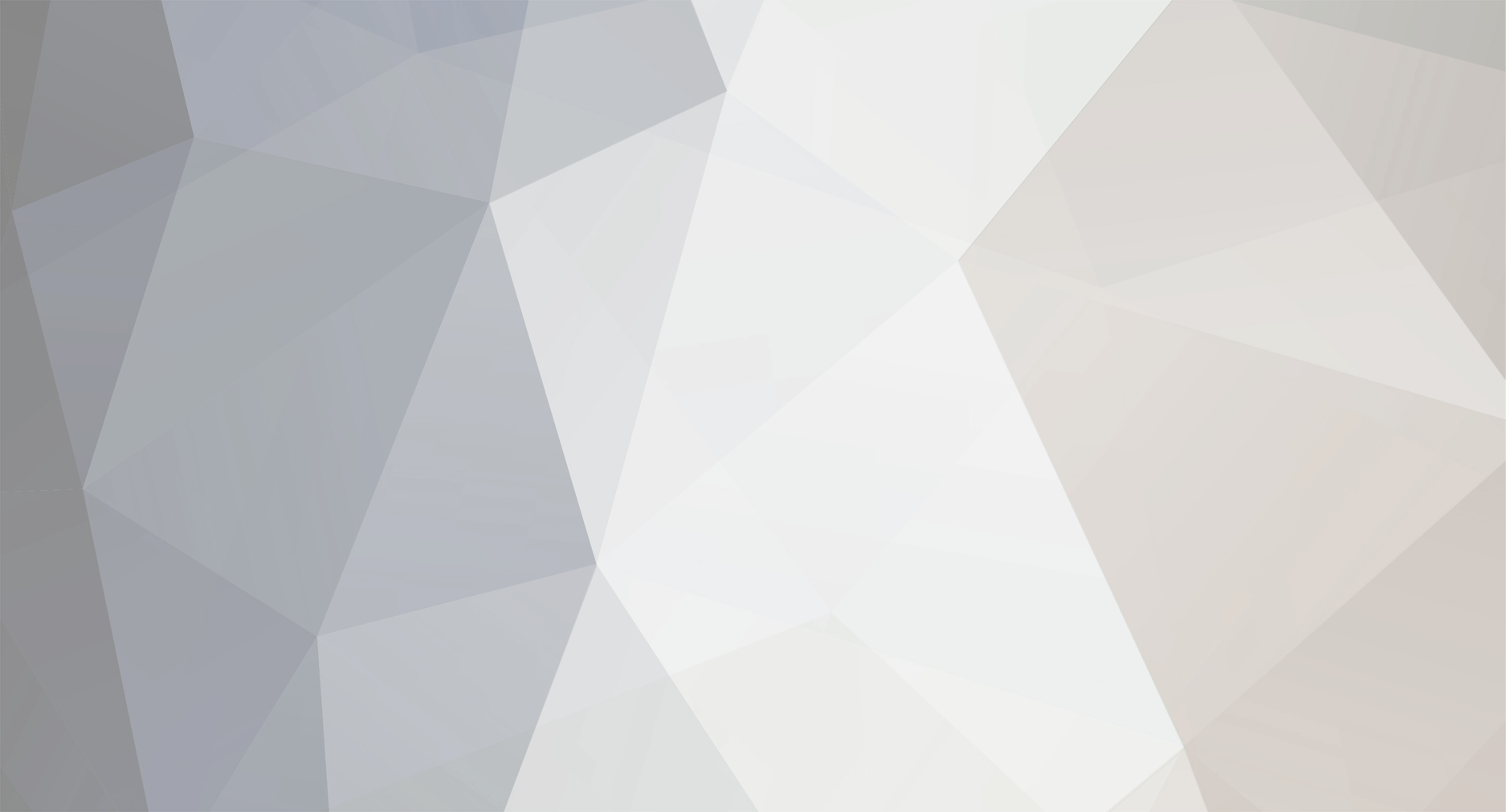
PlungerModerno
-
Posts
1,449 -
Joined
-
Last visited
Content Type
Profiles
Forums
Events
Shop
Articles
Posts posted by PlungerModerno
-
-
[quote name='Grangur' timestamp='1470926902' post='3109389']
Sorry I have to disagree there. Jabba of this Parish can make a superb 5er out of an old door and a shelf!
Wow that man has talent!
Sorry, I digress.
[/quote]
I think if he were charging a living wage for the hours he puts into each build (from what I've seen, haven't had the pleasure of trying one in person) - and a modest fee for the experience he brings to the bench - those wouldn't be cheap instruments. They'd still be as awesome, but not cheap! -
After looking at those images. . .
I'm all shook up (a haw haw). -
Realllllly looking promising. Definately will have to work on strap button placement, definately will have to try and keep the neck and headstock weight down (resolites or ultralites?). But you knew that already. I just hope Pete (the comissoner of this bass) isn't after a baseball bat neck!
FWIW I think the first position of the cap is nicer - but that's just me. Let the person who'll be playing it make the final call! -
I like it - except I think it would have been a lot nicer in a transparent green all over, or a greenburst like this one:
I think the maple would have worked great as a stained green finish too. -
If you can afford it - and it's pretty original, and not battered . . . you can probably sell it on for at least 900.
I'd say go for it. -
Wow . . . quite nasty. Shame as the unscarred paint seems like a passable matt/satin black.
Let's not mention the headstock. -
Coming along very nicely. Would look amazing with a clearcoat finish with that woodgrain.
-
I think they already do this - pretty sure it's called a piezo or lightwave system!
Or just go with the ramp look:
Borrowed from [url="http://basschat.co.uk/topic/284848-shuker-no-2-the-same-but-different/"]this thread[/url].
You could of course get the pickups closer to the strings by lowering the bridge and neck or raising the front of the body. could be done fairly cheaply - as long as you weren't after "Exhibition Grade" figured wood for the cap or having a custom low profile bridge engineered up! -
So would thinning the neck down (depth and width) - as well as making the headstock as thin and small as possible.
-
Try putting a smaller shim in the neck pocket - that will lessen the amount of height adjustment screw showing for the same string height.
If you make a custom shim that fits the entire neck pocket and tapers the desired amount you can get a stable joint with quite a few degrees neck angle change and /or a few mm of spacing to better set it up (e.g. with a different bridge than it was designed for). The only rule is that you increase screw length as needed - or risk a weaker joint. -
What are the pickups & where are they?
The second part will play an important role to the solo sound e.g. neck vs. bridge. How far they are apart will combine with their position relative to the basses scale to produce a range of sounds (depending on the gain of each pickup). When their both on full you'll probably notice what I think of as the "Jazz" effect - take a full sounding neck pickup output, combine with a mid rich (less bassy than neck) bridge pickup and you get a naturally scooped sound - Far less present than the mid rich solo pickup sound. With humbuckers I find they have a lot less sparkle than single coils so they sound better solo'd than when blended together. -
If you already have a Fender P - and are looking at a SS Jag (Jazz like pickups) . . . What about a used Japanese one?
[url="http://www.ebay.com/sch/items/?_nkw=fender+jaguar+bass+japan&_sacat=&_ex_kw=&_mPrRngCbx=1&_udlo=&_udhi=&_sop=12&_fpos=&_fspt=1&_sadis=&LH_CAds=&rmvSB=true"]http://www.ebay.com/...Ads=&rmvSB=true[/url]
Maybe you could go with a Fender or a Licenced neck and go with a custom build... e.g. Warmoth. That'd give you more options with regards to finish and custom routing (e.g. LEDs, extra pickups like a Stu Hamm Urge or the like).
Personally I'd like to see the Jaguar body shape with a Tele headstock shape, like the below.
Edit - I know that's a P bodyshape . . . Here's more what I mean:
[attachment=225082:Alder-3UPFront-withPick_Combined.png] -
Nice - Just when you say "Trimmed it down to fit" I assume you mean the case & not the pickup!
-
A combo like that is almost never economically repairable - bench costs at a repair place will be more than the replacement cost before it's opened up!
It could be a nice project for an amateur or ethusiast - just be aware it may be a hazard once altered (e.g. damage to other equipment or catching on fire), always a risk with electrical goods, but far more likely with one that the last person inside it wasn't a competent service / repair person. Not saying an amateur or enthusiast can't be competent - just that it's more likely they'll mess up than somebody that does it all the time & gets payed for it. Just make sure you unplug it after use and Put the right fuse in it! (A good idea generally.). -
Sweeeeeeeeeet!
-
[quote name='JJW' timestamp='1470264133' post='3104690']
Originally I lacquered the neck with a spray, it was quite thick, then I wet sanded it down to smooth it out but I wasn't happy with the size of the neck so I sanded it all down and reshaped it. To refinish the neck this time I applied Danish oil with a 1200 grit sand paper, which worked well to grain fill.
The body is mahogany and thicker than a normal p bass, so it is quite heavy.
[/quote]
Good looking, but time effective finish - Oils really do wonders for the grain. -
Very nice - knowing it was built in just a few weeks - including finishing, is quite impressive.
I can see the neck is some very pretty ash - how did you handle the grain before finishing? Did you fill it or go with a spray on sanding sealer?
Also is it a heavy body? the wood looks like a mahogany or similar "exotic" wood. -
BT7 ?
[url="http://www.bestbassgear.com/hipshot-bt7-bass-xtender.htm"]http://www.bestbassg...ass-xtender.htm[/url]
I know it fitted mine! -
My reaction when seeing the pictures:
[url="http://youtu.be/M_eYSuPKP3Y?t=64"]http://youtu.be/M_eYSuPKP3Y?t=64[/url] -
-
WOW. That's a beaut!
You say "£300 delivered (in the UK)" - Does that mean you're willing to box this beast up & ship it?
Of course it'd be a little more expensive to ship across the Irish Sea!
Lovely bass you have there! -
[quote name='BassBus' timestamp='1469461277' post='3098488']
There's something very satisfying looking at newly polished frets (specially when someone else has done the job). All nice and shiney. This is looking fantastic.
[/quote]
+1
My thoughts exactly. The maple looks a lot nicer than the plastic, even if the grain isn't identical. -
Wow - I just saw the title and thought it was interesting - as it had no replies I assumed it was a new thread!
Still better late than never. Glad you've got good results, those pickup covers look great with the matching fingerboard! Certainly an improvement over matt black covers!
FWIW pickup height & biasing (in the case of an active blend circuit) is always a compromise on a two pickup bass. The bridge may need to come up - but the neck may need to come down- if the pickups are to play nice together.
Of course if you go down the Billy Sheehan or "Rick-O-Sound" route, with a seperate output for each pickup, it's another story! -
Looks like a Maple cap on an Ash body. While the brass inserts would have probably held in the maple - ash has a much coarser grain and they should have probably used something more like this:
For a much more secure hold in the wood grain. Especially with less dense grain ash is unpredictable. Not suitable for press fit fittings, unless it's your only option.
I'd reuse the fitting to keep the bass stock, sticking it in with Gel superglue, or epoxy Would not recommend thin/watery superglue as it may not bond the wood and fitting together as well as desired, instead mostly soaking into the exposed end grain.
If you want to use thin CA/superglue (if that's all you have) you can put a couple of drops in, let it dry, put in another couple of drops, see if it pools in the bottom of the hole or gets soaked in - if it pools you can add another couple of drops and drive in your fitting. If it gets soaked up, let it dry and try again. Sometimes the wood can soak up a fair amount - it's like putting on an oil finish!.
Budget "P" bass?
in Bass Guitars
Posted
Try out as many as you can (within & within sight of your budget) and see what takes your fancy. Keep in mind dead spots and overall feel is hard to tweak whereas sound (e.g. low output, dead sounding strings) are easily changed to suit your liking!