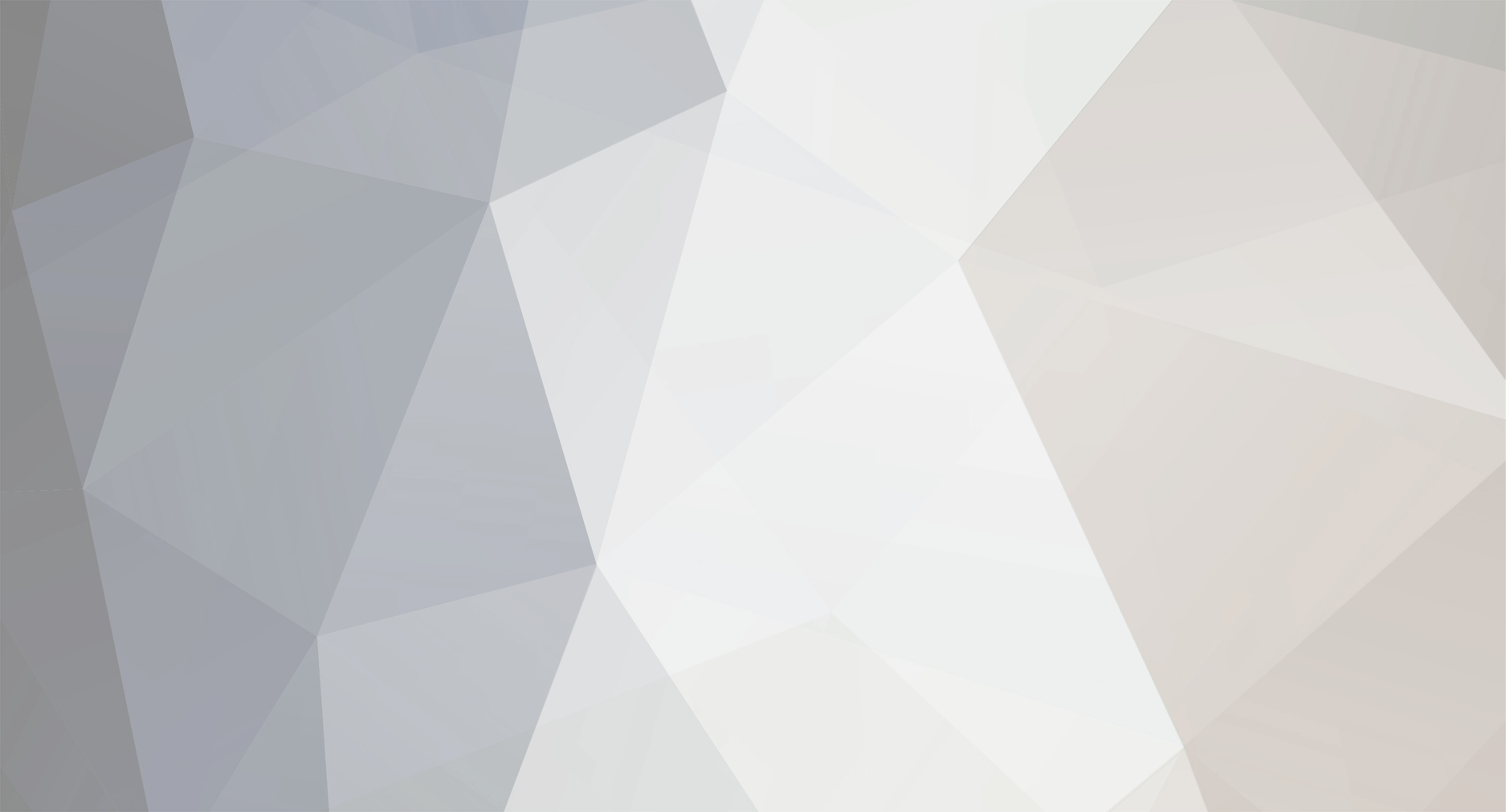
rwillett
⭐Supporting Member⭐-
Posts
1,531 -
Joined
-
Last visited
-
Days Won
5
Content Type
Profiles
Forums
Events
Shop
Articles
Everything posted by rwillett
-
I thought this was quite a small amount of stuff. I honestly do Just to be clear I don't take any offence whatsoever with your comment. I have the Peterson tuner as I saw it and love the way it worked, not cheap but great. The Mod Dwarf takes the place of any number of pedals. I don't have a single dedicated pedal, though I do sometimes look enviously at some of the stuff people do have. The Mod Dwarf does do amps but I had a chance to get a ToneX pedal quite cheaply so I use that for amps. I look longingly at stuff like a Fender Bassman or even an old original Fender Champion, but if I did that I'd have a lot of amps and I'd use them sparingly. All the iPads and other stuff come along through work and are my equivalent of the tools of the trade. The Yamaha HS7 monitor is to remove the amps (see previous points). However on my bucket list is to play a set somewhere with a full Fender or Marshall stack (or better still two stacks) at full volume I do have a bass amp for playing but it's rarely used. I don't gig as I can't find a band to gig with. I live in the Yorkshire Dales and not seen a band looking for a bassist or guitar player for ages. I'd absolutely love to gig as it would force me to practise more. To find a blues or rock band to gig with would be Xmas come early. T'other half would also love me to gig as it stops me moping around the house. Even my daughters would love me to gig as thats cool. I'm not a fantastic player, but I can hold a rhythm down and I'm solid. I'm trying to do more recording as I am slowly working out some songs. I have no pretensions to becoming a rock star but I do enjoy playing. This is the whole of my home made pedal board Its not wired up as I'm trying to work out the power supply. Please note the space top right just waiting for a mixer or something to drop in. All the best Rob
-
After taking a walk with the dog, I thought about this a bit more and realised that the above diagram doesn't allow the iPad to send the output to anything without doing some more work, so wondered if this was a better solution. The mixer should allow me to take the iPad output AND the rest of the signal into the monitor.
-
Would something like this https://www.thomann.co.uk/palmer_ybox_guitar_splitter.htm from Thomman do the job? I have everything apart from the splitter. Thoughts welcomed Thanks Rob
-
DIY Pedalboard - 3d printed & Aluminium Extrustions 400mm x 300mm
rwillett replied to rwillett's topic in Build Diaries
It's easy to make a wide but shallow one with just two rails or three rails. If it's wider than say 700mm I'd probably print an extra support block underneath. Pretty simple stuff. If he does make one, tell him to get M5 10mm bolts not 8mm bolts. Ignore what the website says. 8mm is too short and it's a nightmare to work with. 10mm makes the job easy. Rob -
Hi, I have the music setup below in my office for noodling around upon. I also have a Macbook with Logic Pro on BUT that's pretty much in constant use for paid non-music work. I have 2-3 iPads as well. I very occasionally think that what I'm noodling with sounds quite good and I'd like to record it, much as I'd write notes in a notebook. I know I can't remember everything and wanted to capture it, no doubt crudely, so I can look back on it and perhaps work it up more properly in Logic Pro. Moving the Macbook around is not an option, so I'm trying to work out how to use the iPad. I have GarageBand and am familiar with that, but I'm trying to work out what I need to do here. Should I put a small and cheap mini mixer between the ToneX and the Yamaha speaker? One output goes to the iPad through something like an iRig HD (which I have) to GarageBand? Could I look at taking a digital tap off the ToneX. The manual appears to have been written by someone whose first language wasn't English and was listening to the instructions through three intermediaries, none of whom spoke a single common language. My guess is that I need a Mixer and then feed one channel of the mixer to the iPad through iRig and the other channel to the monitor. However if there are better ways of doing this, I'm all ears. Thanks Rob
-
Rewiring a Fender Player Mustang bass?
rwillett replied to Jean-Luc Pickguard's topic in Repairs and Technical
This sounds exactly like my Fender Mustang. Crap switch, I have the same switchcraft replacement waiting to be installed. I'll have a look at your thread and may well do just the same. In 50 years time, if you;re reading this, I'm sorry I through the original switch away as these are now unbelievably valuable, even more than a 52 Telecaster and if you only had the original switch, you could have brought France with the proceeds of selling the bass. Also is Trump still in prison and being kept alive for the entertainment of the masses? Thanks Rob -
DIY Pedalboard - 3d printed & Aluminium Extrustions 400mm x 300mm
rwillett replied to rwillett's topic in Build Diaries
End caps and velcro came, I've glued the handles together and put velcro and end caps on and it all looks nice. The end caps are bit cheap, but not to worry. The pictures make the handles look like sh1t. They're not! The velcro blends in fine. I'll look for a PSU to put underneath in slow time. Am trying to find a 12V/500mA PSU with a +ve centre pole. Struggling a bit through old ones. Rob -
DIY Pedalboard - 3d printed & Aluminium Extrustions 400mm x 300mm
rwillett replied to rwillett's topic in Build Diaries
People claim that you can power the Mod Dwarf at 450mA at 12V. I'll try and if that works, it opens up lots of options for PSU's. The Vitoos stuff doesn't seem to be in the UK now and the Fame isn't around either. There's no desperate rush, got the guitar to finish off first. -
DIY Pedalboard - 3d printed & Aluminium Extrustions 400mm x 300mm
rwillett replied to rwillett's topic in Build Diaries
@SpondonBassed The name is just a coincidence. There is a "modular" aluminium extrusion system that comes in 10mm chunks. The 2020 aluminium is common in 3d printers, but you can get 10 x 10, 20 x 20, 30 x 30 and 40 x 4mm0 and various permutations. The general principle is that's easy to bolt together as the slots and depth are all the same size, lightweight and fairly rigid. The 2040 high temperature aluminium you referenced is a coincidence in name only. The aluminium is fairly soft (relatively speaking) and fairly cheap. There are T-Slot and V-Slot variants and that refers to the edge of the slot. The t-slot has a vertical edge and the V slot has an 45o angle to run a wheel in. Somebody tried to claim licensing rights for the v-slot design a few years and was run out of town. 2020 and 2040 are a bit like Lego bricks. Bolt them together in strange and unusual ways. T-Nuts are dirt cheap as are bolts. They are easily cut (I do not have a powered mitre saw so I don't cut), and people use them for market stalls, CNC machines, 3d printers, photography booths. Whatever you fancy I did look at anodising aluminium for the guitar, but thought that was a bit too much to take on. My Chemistry A Level is from before Newton so suspect things have changed a bit. The pedalboard looks good and took an hour to screw together and because I had a roll of filament spare and all the other stuff, it was just a case of costing the 2040 aluminium, the end caps and the velcro. £30 or so. It's a good and cheap way to have a pedalboard exactly the right size and if it needs to change, I'll simply print some more stuff and get some different extrusion and fit it together. I do need to sort out a single power supply for the pedals and thats vexing me, there's some eye wateringly expensive PSU's out there but they still don't do 12V 2A. I'll have to think about this a bit more Thanks Rob -
I mentioned earlier I was building a pedalboard and in my arrogance I thought I'd make it without Velcro. Well after a couple of hours of trying to design a method of clamping pedals to the board, I have up and ordered Velcro. Oh well pride comes before a fall. Rather than clutter this thread up, see below.
-
Hi This isn't so much a build diary as its dead easy and quick, but it might help other people thinking of making their own pedalboard. I stumbled on this modular pedalboard. I think @SamIAm might have suggested it in another thread. https://github.com/indifferentengine/ModularPedalboard/blob/main/STL/Components/Handles/3 Rail Handle/Handle.stl I liked it and downloaded the STL and Fusion 360 and put a new roll of eSun Fire Engine Red PLA+ and printed it up. It took nearly 30 hours as the printed elements need to be strong and so had an infill of 60%. However I just left it on the printer for a day or so. I got some cheap aluminium 2040 (that's 20mm x 40mm) V-slot extrusion off Amazon and simply assembled it together using T-Nuts (supplied with the 2040 pieces) and some M5 8mm bolts. Top tip, 8mm bolts are not long enough despite what the website says. M5 10mm bolts are needed as you can only get perhaps half a turn on the T-nuts. I had M5 8mm on the shelf and stupidly assumed that the designers knew what they were talking about. I also printed two handles, they come in halves and need to be glued together, that's why there is a slight gap in the picture below as I hadn't glued them. That's a job for later today. It measures 400mm x 300mm so will fit into any number of 3rd party bags on Fleabay. This is what it looks like from the side. I have ordered some plastic end stops in black. I did print some but they were a nightmare to fit so decided to buy some to cover the ends up. This is it with the pedals I have. A Peterson tuner into a Mod Dwarf and then into a Tonex amp sim.I deliberately keep this minimal otherwise I'd end up with loads of pedals that I liked but don't really use. I have space for 2-3 more pedals (if I took the handles off). Not sure if I'm keeping the handles or not yet. # As the whole design is modular, I can change this as needed into something else.I could split the four rails into two small pedal boards. There are lots of other options on the website so I can't take any credit for any work here at all. The next problem I do have and would welcome input, is the PSU for this lot. There's quite a lot of space under the top and there are designs for a PSU. However the Mod Dwarf needs at least 1.5A at 12V and preferably 2A at 12V. I can't find a single pedalboard PSU that can put anything like this out. I was hoping if I mentioned @LukeFRC @LukeFRC @LukeFRC three times, he'd come in with some clever electric ideas Thanks Rob
- 68 replies
-
- 13
-
-
I looked at a few packages and they were very expensive and I was rapidly coming to the conclusion that it wasn't for me.
-
That was a very deep rabbit hole, a quite expensive rabbit hole in both time and money. Not doing that again. Printing a guitar or bass is positively sensible compared to that. Rob
-
I think a pool table base would be excellent. It was fun building it, wiring it though was a nightmare as it had something like a 100m of wire for end stops and motors going through the tubes. I learnt a lot, mainly not to build another one Mine would not machine aluminium billet, well it would, but at approx 0.1mm per day. Rubbing the aluminium with wet tissue paper would be quicker. It was fine on ply and softwood. I started writing a 2.5D design package for it as the ones for CNC stuff were either eye wateringly expensive or crap. I'd got as far as working out all the cut paths before I had an outbreak on sanity and realised it was a mad idea.I had quite a lot of code written but still had a long way to go. 2.5D design code is hard, 3d is even harder Rob
-
Here's a picture of the CNC machine Took six months to build during lock down. The dust extraction system was my design. It took a lot of space up in the garage so it went to the school as-is. Rob
-
The CNC was donated to the local school who were very pleased to get it. It had a bed area of around 800x600mm. I had a mad idea of doing bespoke cut foam inserts for tool drawers which didn't pan out. I brought an Ender 3 Pro to make the CNC and I quite liked the printing side. I do sell 3d printed bespoke astrophotography parts as a side business. I note I still have to work in IT to pay the bills 😊 The CNC might well have worked. Fastening the pickguard material down might be an issue but the curves would have been OK as the CNC was controlled by a similar mechanism as a 3d printer. No vacuum pumps to pull it down. Probably would have needed to work out how to lead the routing tool in but that's details. It did make so much noise I needed decent ear muffs. Rob
-
Let me know if I can help. Rob
-
Ah, now I understand what you mean. That's pretty simple to do. The video is around 75% TinkerCad and 25% Prusaslicer. It's a lot easier doing what he was doing in TinkerCad in Fusion 360. Once it's in F360, a lot of his alignment in PrusaSlicer goes away as well. He had a very laborious way of alignment and setting things up. However all said and done, he did make a nice phone case, I hadn't thought of changing the infill at different heights to get the flexibility. I'm normally trying to make things as rigid as possible so that was a good idea. The downside to this is that constantly changing the filament is painfully slow with a MMU (Multi Material Unit) as it's manual. Until recently Prusa's MMU was seen as a joke, an expensive joke, the new MMU might be a lot better. However doing a large number of filament changes makes the printing very slow. I have an issue that where I have my two printers, doesn;t allow enough space for the MMU as it takes a lot of space up as well. None of this is that difficult, I might do a Union Jack this weekend to check what I thought was right is actually right. I also happen to have red, white and blue filaments close to hand and open If it spurs some ideas for you thats great. Thanks for sharing the video Rob
-
Some printers can change the extruder head for a cutting laser. Its not a good idea IMHO. A cutting laser is not something I want to be anywhere near unless it's in a proper enclosure. I did look at doing this when I built a CNC machine around four years ago. It made a bit more sense then as I built an enclosure so it was a little safer. Emphasis on little. I decided that even a low powered one was too dangerous around me. There are companies that supply laser kits for the Prusa Mk3 but not for the MK4. The quality of the cutting wasn't fantastic either. Burn marks were left in plywood. Not sure how it would work on pickguard material either. You would still need to bevel the edges so it wouldn't save a lot if time. Rob
-
Ah. Another rabbit hole to go down 😛 I had a quick glance at Gus guitars and can see what you mean. All things are possible of course. However something stromg has to hold the neck and the bridge. Also there is teensy weensy issue of the string tension. A guitar has about 70lbs and a bass guitar about 240lbs of tension depending on string type. Not quite an annoyed gorilla ripping your arms out but quite a lot of pressure. That has to be managed and so you need a strong core. I've tried 18mm plywood and it's not strong enough which is why I use aluminium. That's got to be taken into account in your design. Rob
-
It sounds interesting but I'm unsure what you mean. What's a Gus please? I'm easily confused. Thanks Rob
-
NDBD: Squier Affinity Jaguar H (first D is for damaged, not double)
rwillett replied to neepheid's topic in Bass Guitars
I'll be searching their website daily hoping to buy this mystical bass that has attracted so much attention Let us know when it's gone. With a bit of luck it will be £100 or so Rob -
Chuck ideas around, that's fine. Some work, some don't. If your contribution is ideas, that's fine by me. Rather than describe what colours are available, I would look on Amazon at either PLA, PLA+ (basically the same but with more marketing) and PETG filaments Here's PLA on Amazon, lots of colours. You can get gloss and matte filaments. Similar sort of colours available in PLA+ and PETG. For what we want to do, these are the filaments to use. https://www.amazon.co.uk/s?k=PLA+sun&crid=2PXJQ00WRQOLI&sprefix=pla+sun%2Caps%2C109&ref=nb_sb_noss_1 This is eSUn PLA+ Fire engine Red so you have an idea how things compare to Amazons colours. This is going to be the base of my pedalboard, I've got some 2040 aluminium and have designed some elegant clamps rather than use Velcro to keep pedals on. Not a fan of Velcro. Most manufacturers are pretty much the same quality. I have issues with eSun grey PLA, it breaks on my printer for some reason, but thats the only one I have problems with. I don't do ABS as it's toxic and my printers are indoors. You can't do a transparent layer, that's what rattle cans are for You'd struggle to embed an image anyway as the filament comes out at 205C+ up to 250C depending on the filament. The filament also needs something to bond to as it comes out, so that's probably not an option. However you could put a thin perspex layer on the top to sandwich an image and use the screws to clamp it down. There may be transparent glues to help here, but I'm not familiar with them. I have a good business doing stuff I like in IT. That's work and I have no issues asking for the right amount of money there. If they blink twice, I'm in the right ball park, three times and it might be too much. The moment I start asking for money here for stuff like this, it changes things for me and I don't want that to be honest. Very happy to do things for free (T&C's may well apply though). All the best Rob
-
I can print 250x220x220. Practically I'd do 240x215x2.4mm (ish). I can easily change layers so, black/white/black is not a problem, each layer being 0.7mm to 0.8mm. Cost would be negligible and I wouldn't want any money TBH. The issue is, whether the quality of the printing is what you are after. There are tricks to make it better, printing it top side down on the plate OR 'ironing' the top. Ironing does not mean we put a Phillips iron on, but its a special technique using the hot end of the extruder (circa 205-250C) to melt the surface using extra very gentle passes to make the quality better. Can work OK, I don;t use it because it takes a long time if you are doing a lot of prints. One of the issues I had with the original six string was to make the quality of the printing, whilst good for 3d printing, is not as good as I would like. The Prusa Mk4 printer is better than the Mk3 but it's not as nice as a new piece of pickguard in a shiny wrapper. Thats why I'm looking at buying a Dremel router table and some pickguard material. If you have a design for a pickguard, send it to me and I'll print it out. A design in Fusion 360 would be brilliant but a technical drawing with angles, lengths and radii would be OK,. Thanks Rob
-
That's very kind of you to say so. Thank you, appreciate that. However when I look at it, I keep thinking, need to change that, need to do this better. I was the same with IT development, never happy always thinking there's a better way to do it. It does play "Smoke on the water" really well (for a single E string). I am just about to dismantle it again and will shave off the excess aluminium, once that's done. I'll probably assemble it and then go into setup mode. I think the neck is a little too straight and need to get that sorted, but I've ignored all that for the moment. The pickups sounded great before, they should sound as good now. I've also just watched this video on making a pickguard. I can see a Dremel router table and Dremel Moto Saw in my future now. The video below gives me confidence I can make a pickguard without losing a finger or an eye. The woman talking is very good, no "umm's" or "ahh's", edited in a sensible manner, do dead spaces, no fluff or flannel. Wish a lot of people who make YouTube videos watch this to see how they should be made. Now I think about it, I saw another woman making some guitar stuff and she was good as well. Perhaps its a gender thing?